Your Trusted Wholesale And Custom Cotton Fabric Manufacturer
As a specialized neoprene fabric manufacturer, Szoneier Fabric empowers industries with high-performance, customizable materials built for resilience. Leveraging neoprene’s unique properties—waterproof insulation, thermal retention, shock absorption, and stretch durability—we craft fabrics that excel in demanding environments.
Your vision defines our process. From vibrant prints and embossed logos to precision-cut patterns, we integrate designs seamlessly into neoprene through advanced dyeing, laser cutting, or sublimation techniques—without sacrificing its structural integrity.
Choose thickness (1mm to 7mm+), surface textures, or specialty coatings (anti-slip, UV-resistant). We transform raw neoprene into branded, purpose-driven solutions.
Your Design. Neoprene’s Potential. Perfected by Szoneier.
Just Try Us!
You just choose wholesale any neoprene fabric types for your customization, and we will take care of the rest.
Selecting the perfect fabric for your product line has never been easier! As a top rated fabric manufacturer, we offer a wide variety of wholesale Cotton fabrics that can be customized to suit your exact needs. Whether you’re looking for lightweight cotton for clothing, durable options for bags, or specialized fabrics with water-resistant or UV-protective coatings, we’ve got you covered. With endless options in colors, textures, and finishes, our fabrics are perfect for fashion, home textiles, outdoor gear, and more. Partner with us to bring your ideas to life with high-quality materials, competitive prices, and flexible customization options.
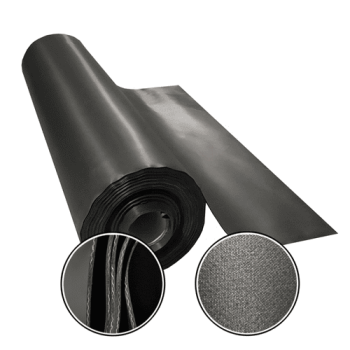
1.5mm neoprene
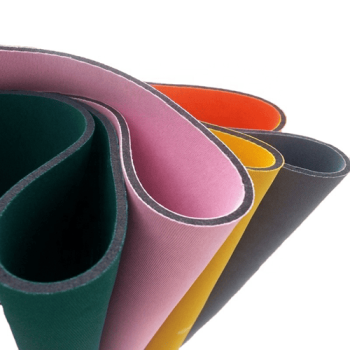
1mm neoprene
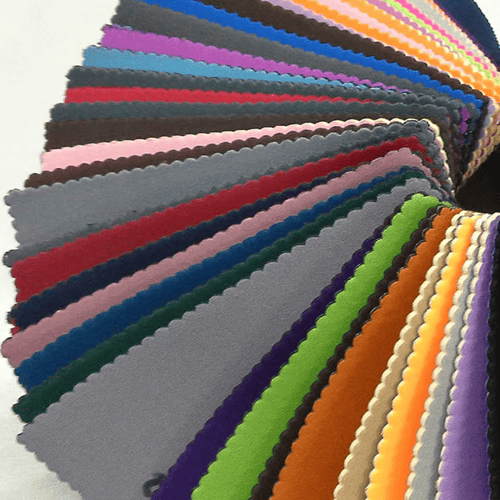
2mm neoprene
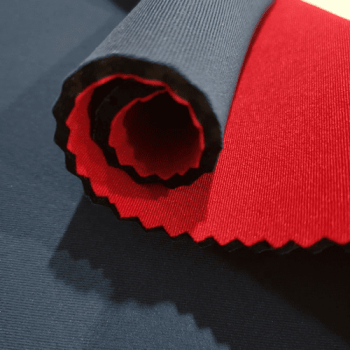
3mm neoprene

4mm neoprene
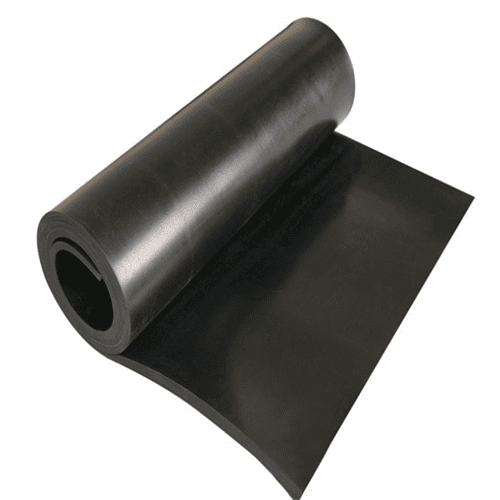
5mm neoprene
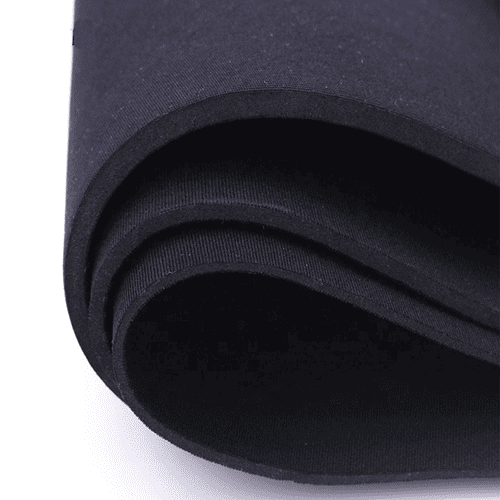
6mm neoprene
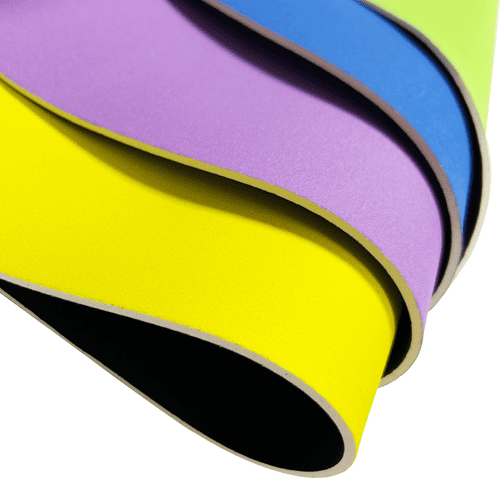
8mm neoprene
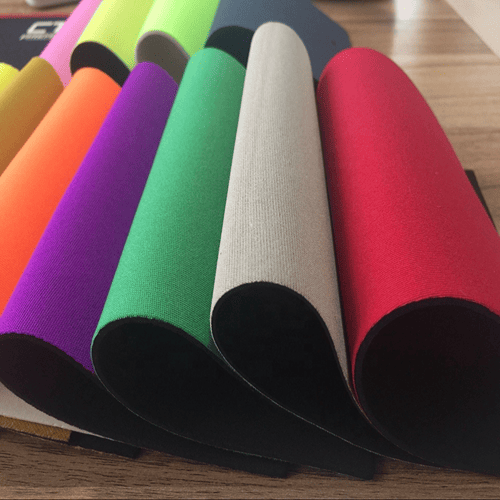
10mm neoprene
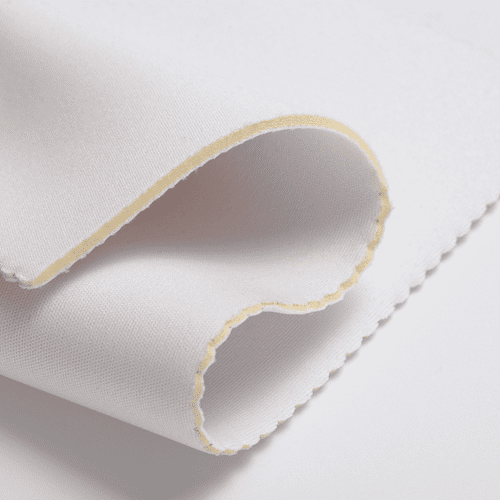
beige neoprene
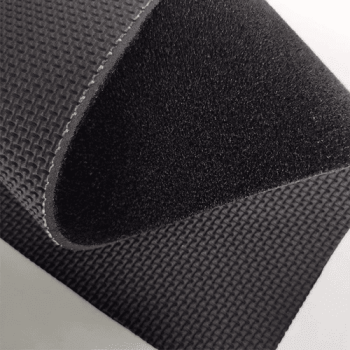
black neoprene
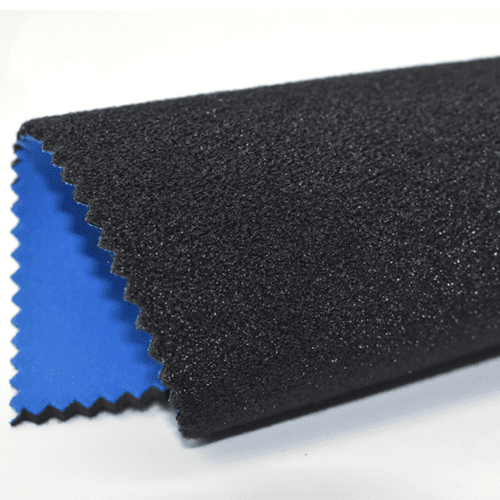
blue neoprene
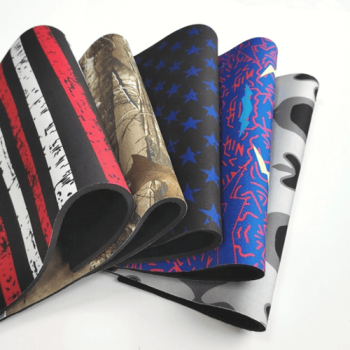
camo neoprene
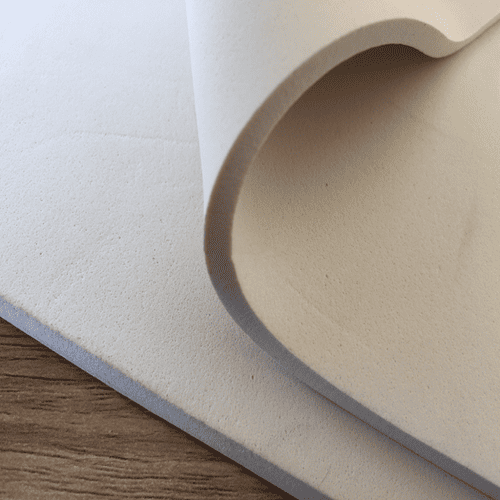
closed cell neoprene
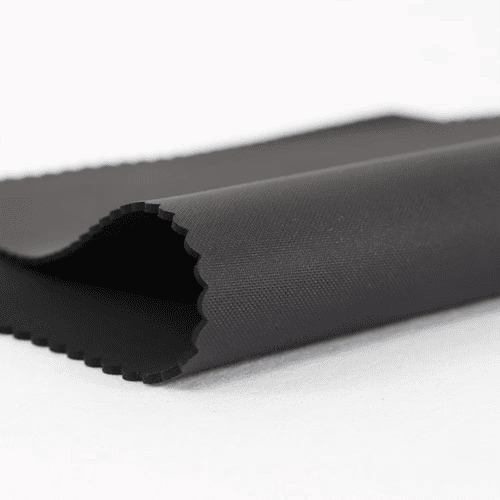
cr neoprene
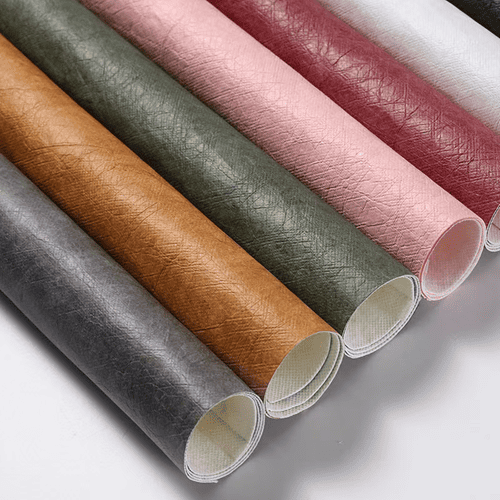
dupont neoprene
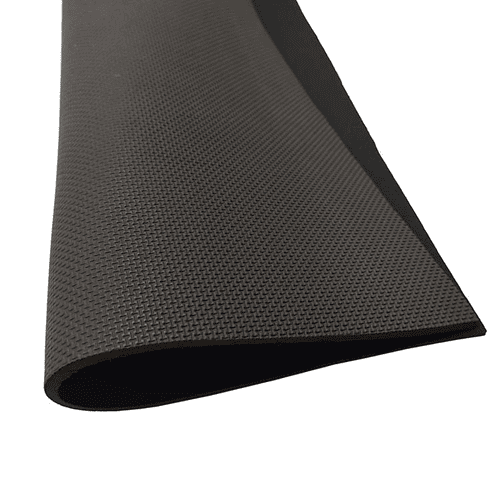
embossed neoprene
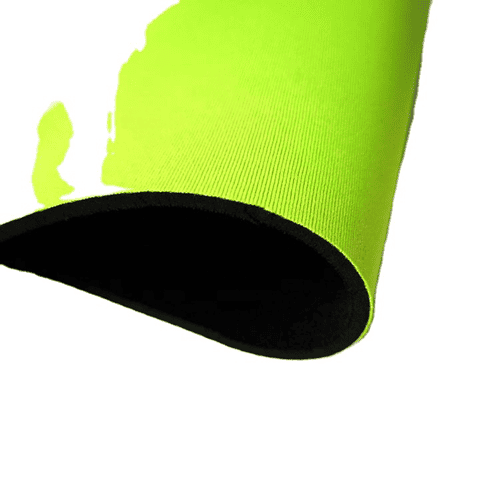
green neoprene
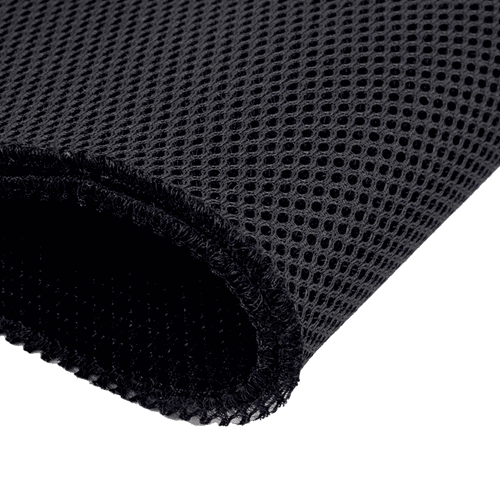
mesh neoprene
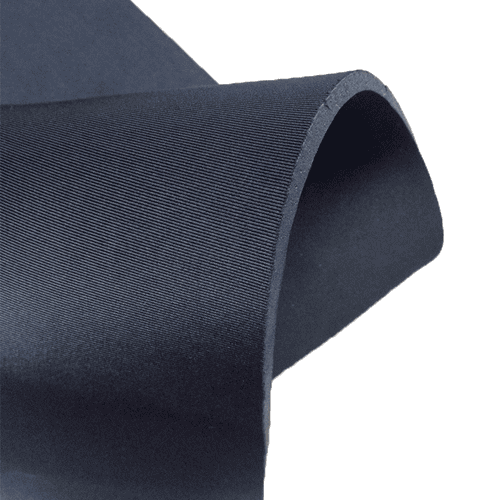
neoprene coated nylon
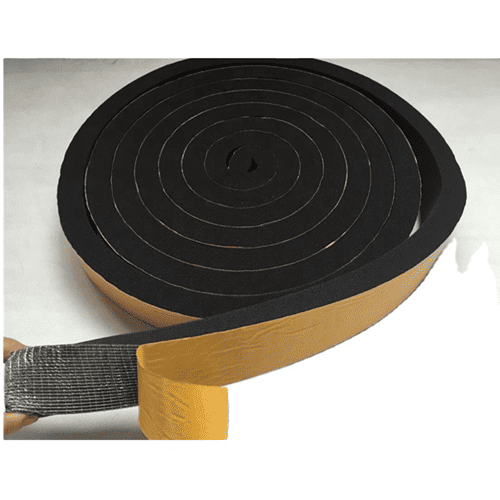
neoprene epdm
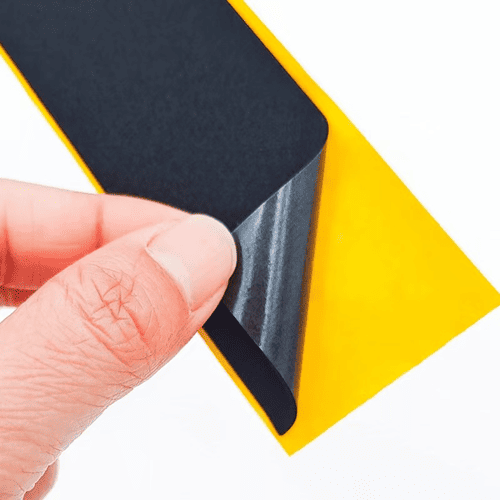
neoprene tape
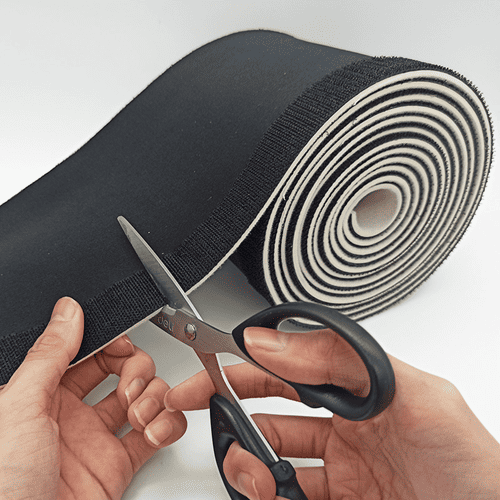
neoprene velcro
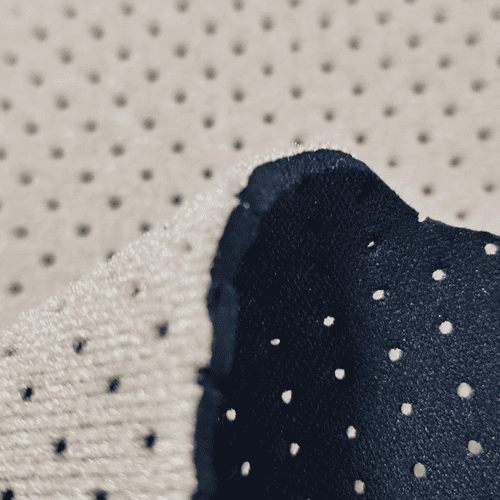
neoprene coated nylon
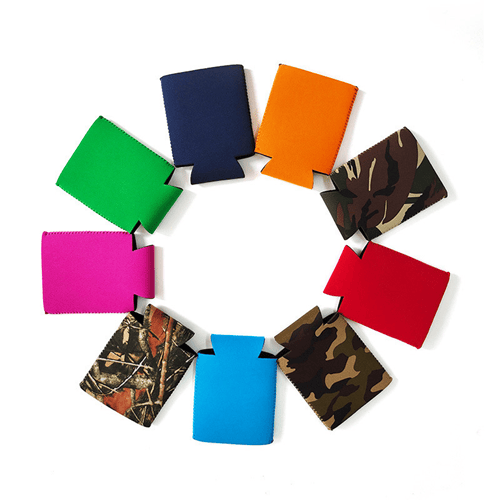
printed neoprene
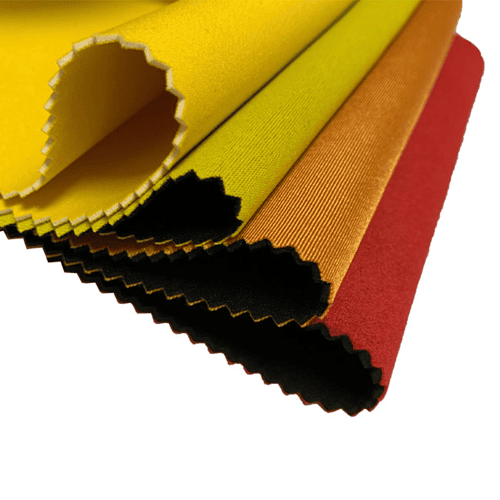
recycled neoprene
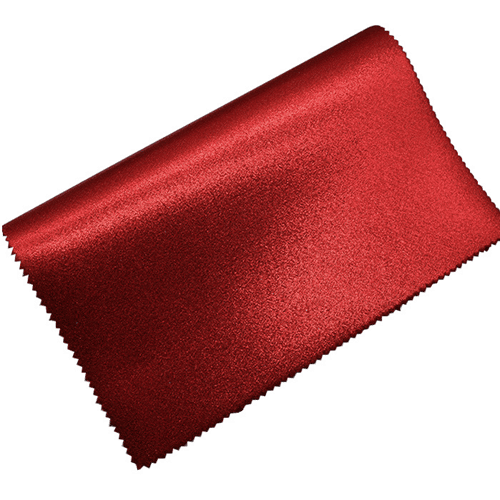
red neoprene
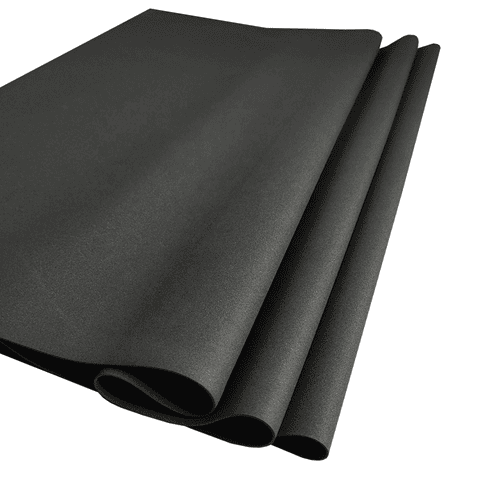
scr neoprene
Wholesale and Custom Fabric Categories
Renowned for its waterproof insulation, flexibility, and durability, neoprene fabric is a go-to material for performance-driven solutions.

Potential applications of neoprene fabric
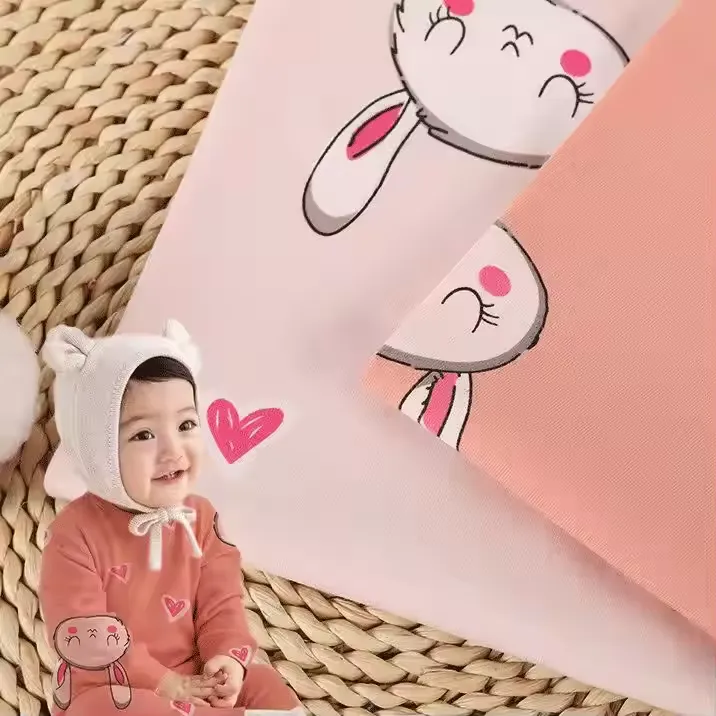
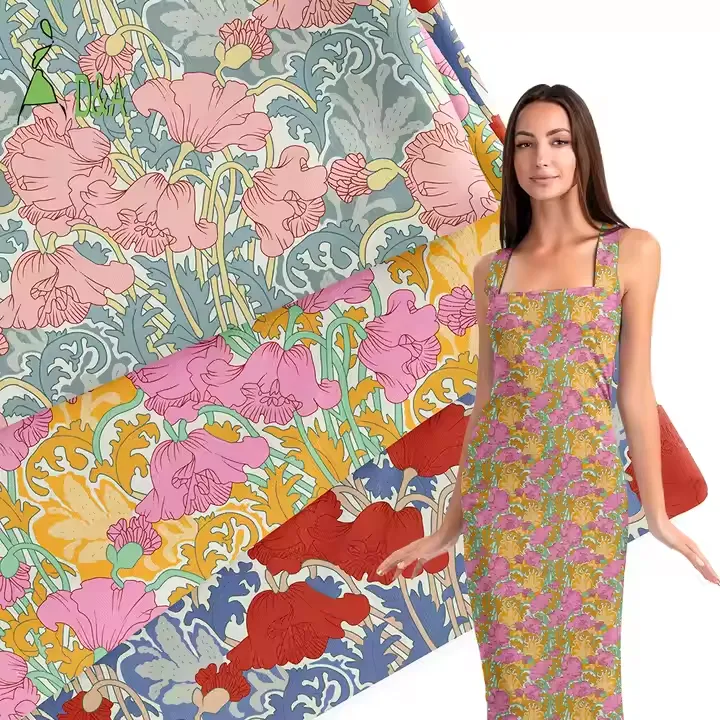
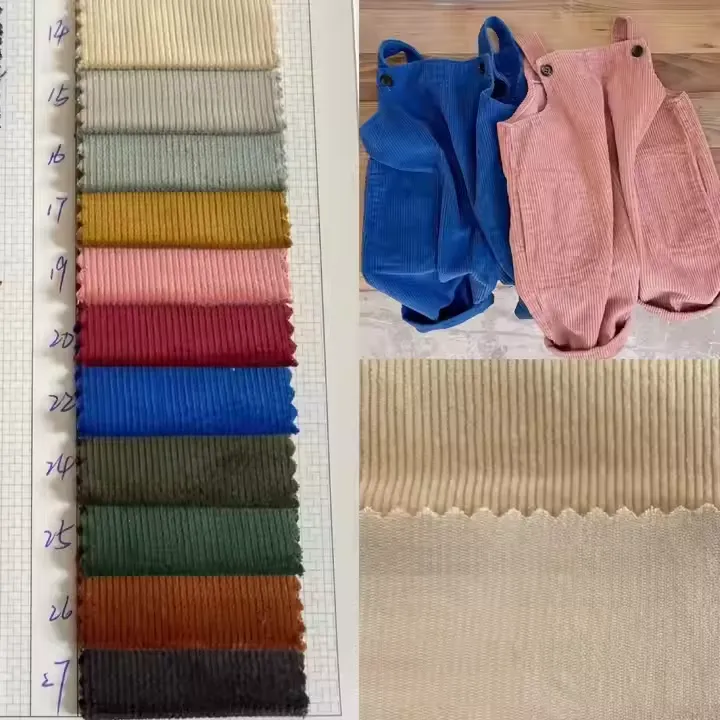

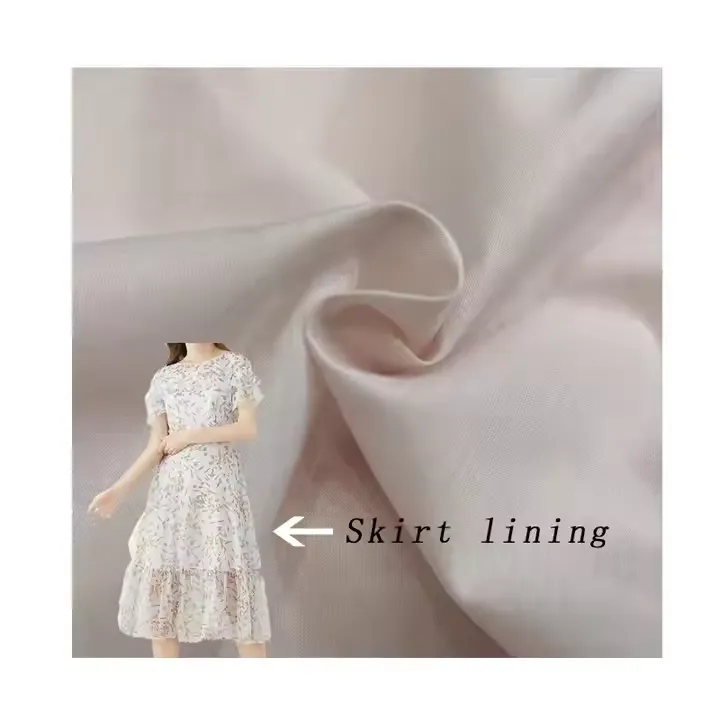
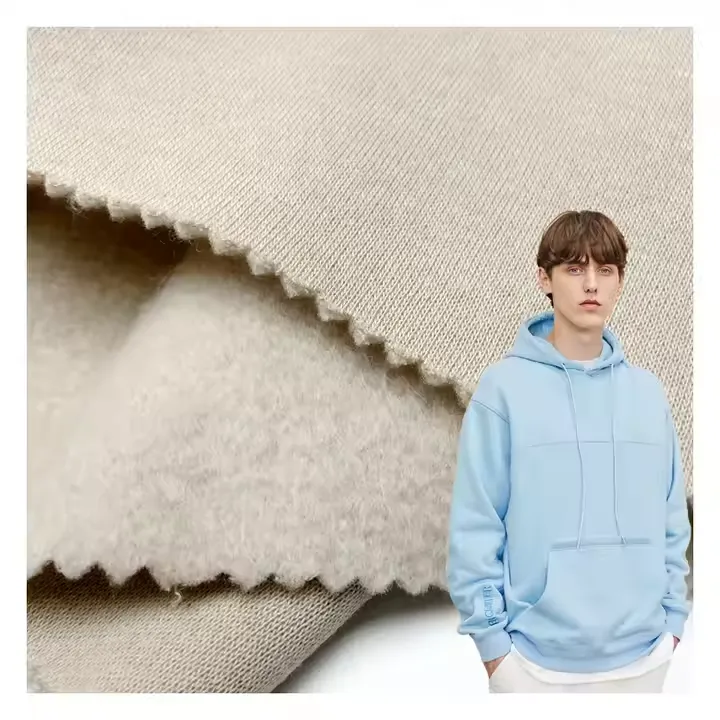
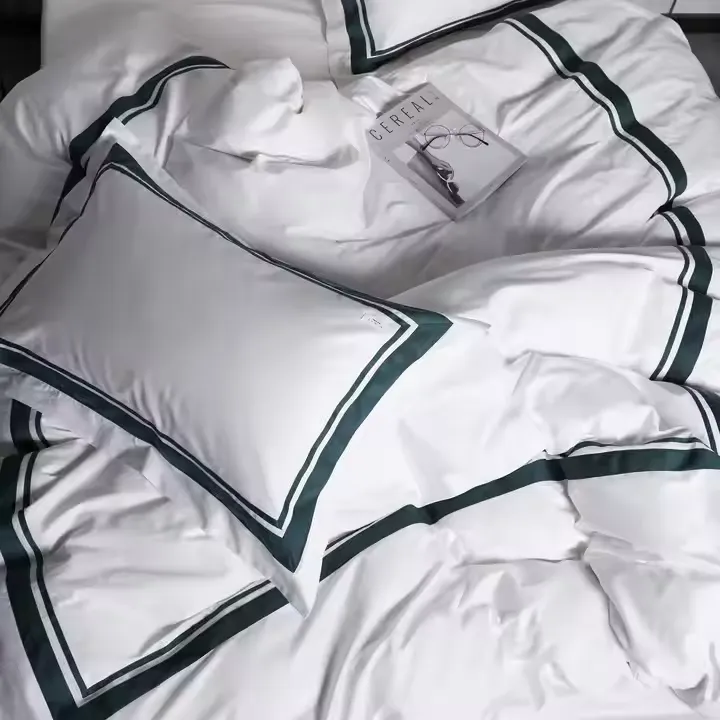
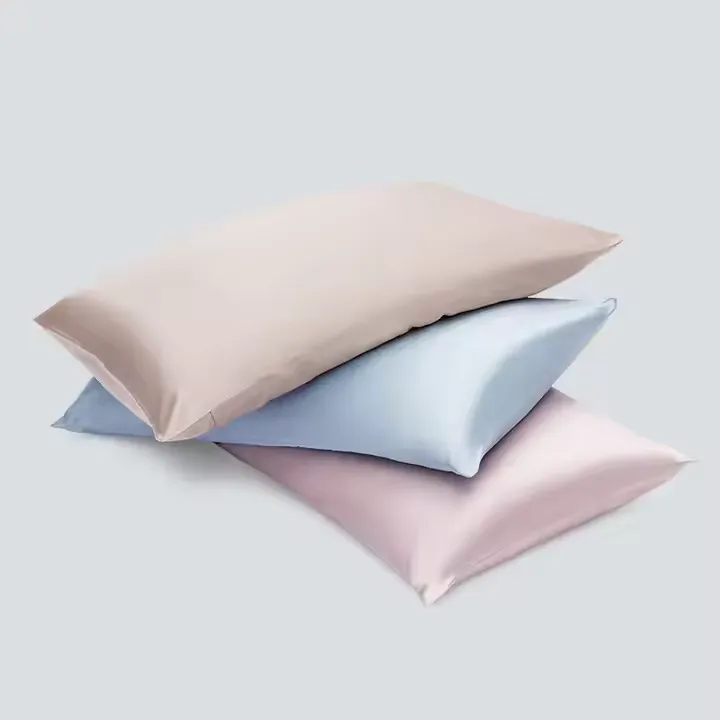
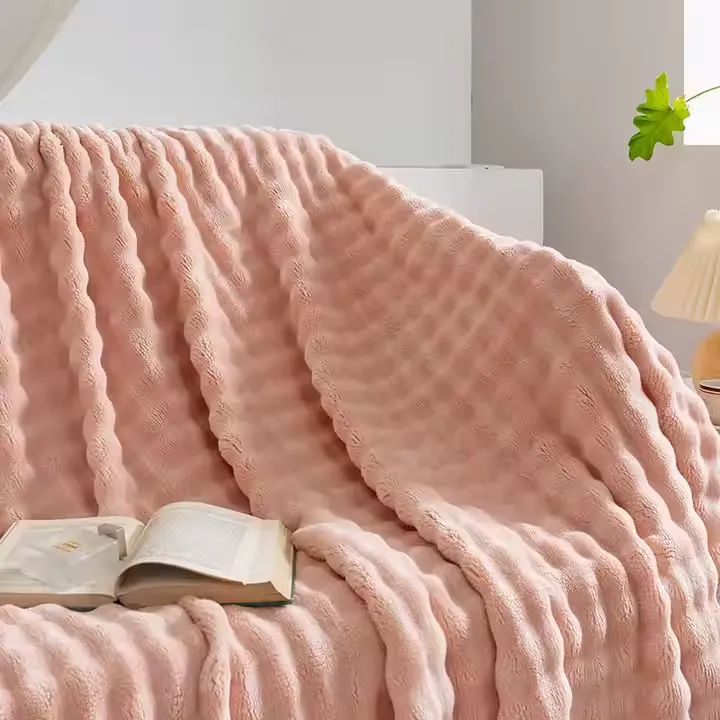
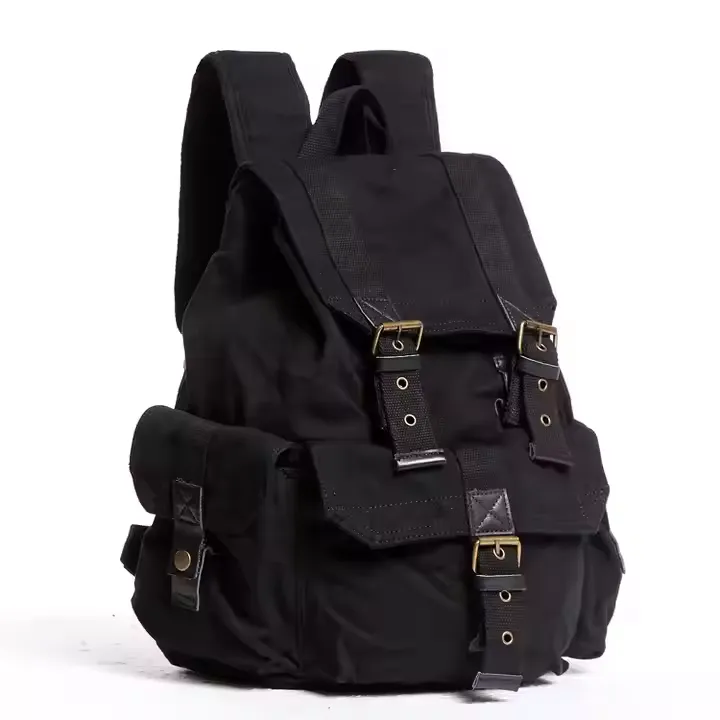
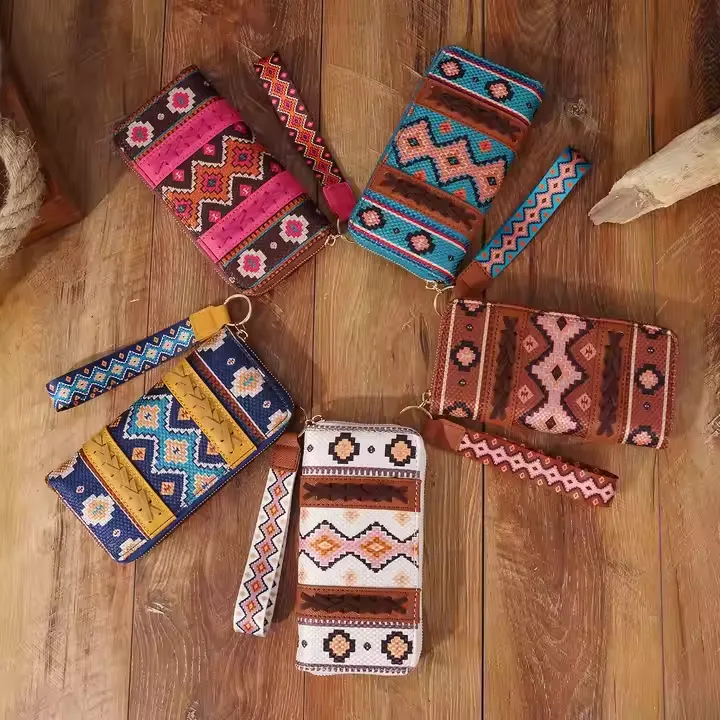
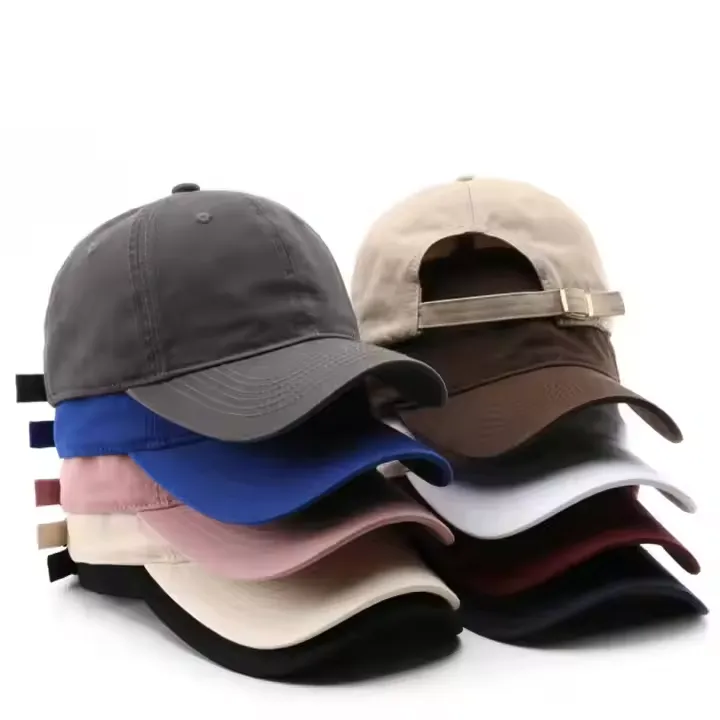
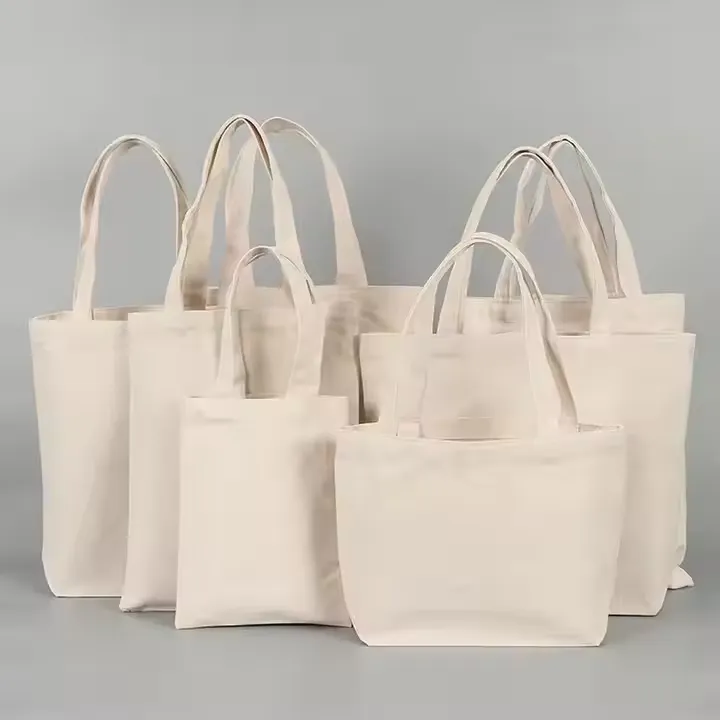
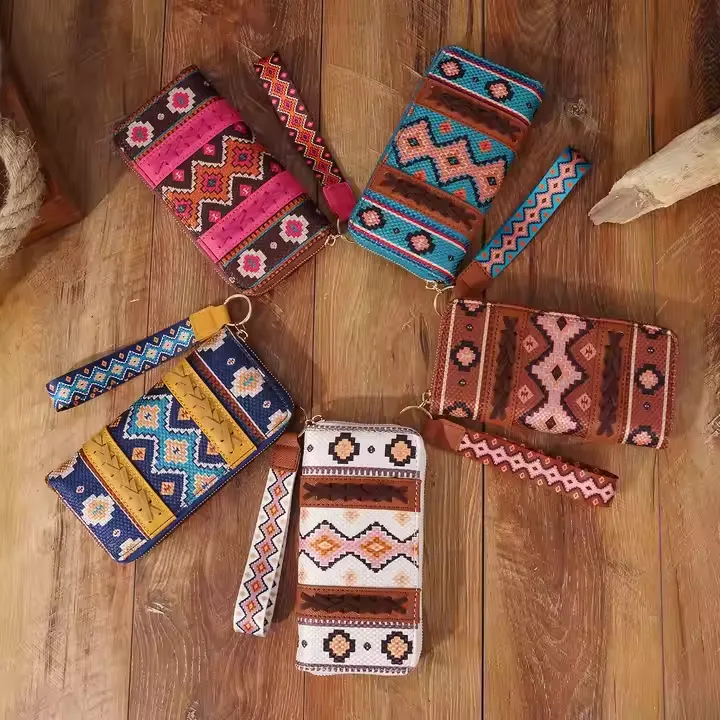
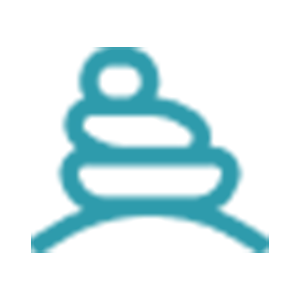
Sports & Outdoor Gear
Wetsuits/Dive Gear: Thermal insulation for surfing, diving, and water sports. Athletic Supports: Knee/elbow braces, yoga mats, and gym accessories with shock absorption. Backpacks/Cases: Water-resistant laptop sleeves, camera cases, and outdoor equipment covers.
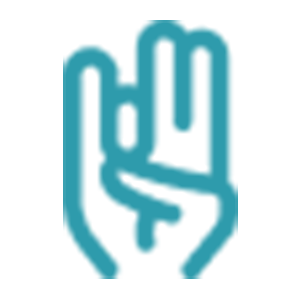
Fashion & Lifestyle
Tech-Enhanced Apparel: Sleek neoprene jackets, avant-garde dresses, and statement accessories. Footwear: Shoe liners, insoles, and waterproof boot accents. Luxury Goods: Designer handbags, phone cases, and branded merchandise with custom prints.
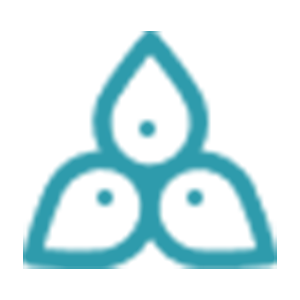
Industrial & Technical Use
Vibration Dampening: Machinery padding, automotive gaskets, and HVAC insulation. Protective Gear: Work gloves, safety equipment liners, and anti-slip surfaces. Marine/Automotive: Boat hatch seals, car seat covers, and vibration-resistant components.

Medical & Rehabilitation
Orthopedic Supports: Custom-fit braces, compression sleeves, and posture-correcting wear. Therapeutic Products: Heat-retention pads and ergonomic cushions.
Why Partner With Your Trusted Nylon Fabric Manufacturer For Your Bespoke Products Needs?
When it comes to creating durable, versatile, and stylish products, nylon fabric remains a top choice. As a manufacturer with years of expertise in nylon fabric production, we offer both wholesale options and fully customizable solutions tailored to meet your unique requirements. Szoneier factory is equipped with state of the art machinery, allowing us to produce nylon fabrics in a wide range of textures, weights, and colors to suit various applications,from apparel to accessories and home textiles.
Partnering with us ensures that you benefit from high-quality materials, competitive pricing, and flexible production capabilities. We pride ourselves on strict quality control measures, ensuring each batch meets industry standards and your expectations. Whether you’re looking for eco-friendly recycled nylon or specialized finishes such as water resistance or UV protection, we’ve got you covered. Let us bring your vision to life, offering custom dyeing, printing, and finishing options to create the perfect fabric for your products.
Choose us as your trusted nylon fabric manufacturer and enjoy a seamless, reliable partnership for all your bespoke fabric needs!
Fabric Dyeing And Finishing Process
The fabric dyeing and finishing process is a crucial phase in textile manufacturing, transforming raw materials into vibrant, functional textiles. This process not only enhances the aesthetic appeal of the fabric but also improves its durability and usability
Dyeing
Dyeing is the process of adding color to fabric. Different dyeing techniques can be used depending on the type of fabric and the desired outcome: Fiber Dyeing: Color is applied directly to the fibers before they are spun into yarn. This method is often used for wool and silk and allows for rich, deep colors. Yarn Dyeing: The yarn is dyed before weaving into fabric. This technique is ideal for patterns like stripes or plaids and is commonly used for cotton fabrics. Piece Dyeing: In this method, the fabric is dyed after it has been woven. It is the most common method used for bulk production of colored fabrics. Batch Dyeing: Fabric is dyed in large batches, ensuring consistency in color across large quantities.
Printing
Printing adds intricate designs to fabric using various methods. The most common printing techniques include: Screen Printing: A stencil is created for each color, and dye is pushed through a mesh screen onto the fabric. This method is ideal for bold, vivid designs and is widely used for T-shirts and home textiles. Digital Printing: This modern technique uses inkjet technology to print designs directly onto fabric. It allows for high detail and quick turnaround times, making it perfect for custom designs. Rotary Screen Printing: Similar to screen printing but uses a cylindrical screen for continuous printing, making it efficient for large runs.
Coating
Coating involves applying a layer of material to the fabric to enhance its properties. This can include: Waterproofing: Fabrics are coated with a water-repellent finish to protect against moisture. This is commonly used for outdoor gear and clothing. Flame Resistance: Fabrics can be coated with fire-retardant chemicals to meet safety standards for specific applications, such as upholstery and workwear. Stain Resistance: A coating can be applied to fabrics to prevent stains from setting in, making them easier to clean and maintain.
Color Weaving
Color weaving involves incorporating colored yarns into the fabric during the weaving process. This method allows for intricate patterns and designs, such as:Jacquard Weaving: Developed in the 19th century, this advanced technique employs computerized looms to independently control thousands of warp threads, enabling photorealistic imagery and elaborate motifs. Modern applications range from luxury tapestries to technical textiles with embedded smart patterns, particularly valued in high-end upholstery and narrative-driven fabric art. Twill Weave: Characterized by its signature diagonal ribbing, this method interlaces colored weft threads in staggered sequences that enhance structural integrity. The angled texture not only camouflages stains but also improves abrasion resistance, making it ideal for durable workwear, designer denim, and performance-oriented home textiles like decorative pillow covers.
Fabric Structure Types
If you need help choosing the right fabric structure for your project, feel free to reach out to our expert team for guidance!
The plain neoprene structure is the most basic and widely used form of neoprene, where the material is typically formed without any distinct texture or pattern. This simple design offers excellent flexibility, insulation, and durability. Plain neoprene is often used in wetsuits, dive suits, and protective gear due to its ability to provide thermal insulation and flexibility. The smooth surface allows for easy movement and a comfortable fit, making it suitable for water sports and outdoor activities.
1. Plain Neoprene
Open-cell neoprene features a structure where the cells within the material are interconnected, allowing air and water to pass through. This makes the fabric more breathable and flexible but less insulated compared to closed-cell options. Open-cell neoprene is commonly used in dive gear, thermal insulation for clothing, and sports braces where breathability is important. It is also often used in impact-resistant padding because of its cushioning properties.
2. Open-Cell Neoprene
In closed-cell neoprene, the material consists of cells that are not interconnected, providing a better barrier to air and water. This structure enhances insulation and buoyancy, making it ideal for wetsuits, diving suits, fishing waders, and thermal clothing used in cold-water conditions. The closed-cell structure helps keep the body warm by trapping air within the material and preventing water absorption, making it suitable for cold-water environments.
3. Closed-Cell Neoprene
Foam-filled neoprene is a variation where a layer of foam is inserted between the neoprene layers. This provides enhanced insulation and cushioning properties. Foam-filled neoprene is often used in protective gear, sports pads, and insulated clothing, offering additional shock absorption and comfort. The foam layer also improves the flexibility of the material, making it ideal for activities like kayaking, surfing, or any sport requiring impact protection.
4. Foam-Filled Neoprene
Textured neoprene features a surface with added patterns or embossing, giving it a more aesthetic and functional design. The texture can enhance grip, durability, and comfort, making it useful in sports gloves, protective knee pads, and equipment covers. The added texture also allows for better aeration, making it more comfortable for extended wear, especially in protective gear or sports apparel.
5. Textured Neoprene
Fabric Weaving Process
01
Single-Sided Fabrics
Single-sided fabrics are produced using a straight forward weaving technique where the design and texture are visible on only one side of the fabric. The reverse side often has a plain, untextured appearance. This type of fabric is commonly used in garments, linings, and home textiles, where only one side is intended to be seen. The benefits of single-sided fabrics include simplicity in design and cost-effectiveness in production. Examples include satin, which features a glossy surface on one side, and muslin, known for its lightweight and breathable qualities.
02
Knitted Fabrics
Knitted fabrics are created by interlocking loops of yarn, resulting in a flexible and stretchy material. This process allows for a variety of textures and patterns, making knitted fabrics popular in apparel, activewear, and home textiles. Knitting can be performed using different techniques, such as warp knitting and weft knitting. Warp knitting involves yarns running parallel to the fabric’s length, providing greater stability, while weft knitting has yarns woven horizontally, offering more stretch. The unique properties of knitted fabrics, such as breathability and comfort, make them ideal for casual wear and sportswear.
03
Double-Sided Fabrics
Double-sided fabrics, also known as reversible fabrics, are woven to have distinct designs or textures on both sides. This type of fabric is produced by interlacing two layers of yarn, creating a thicker and more substantial textile. Double-sided fabrics are highly versatile and can be used in a variety of applications, from fashion to upholstery. The ability to use either side of the fabric adds value and functionality, allowing designers to create reversible garments and accessories. Common examples include double-faced wool, often used in coats, and plush velvet, popular in home furnishings.
04
Weft Knitting
Weft knitting is a specific type of knitting technique where the yarn is fed horizontally across the fabric. This process creates a series of interlocking loops, resulting in a stretchy and comfortable fabric. Weft knitted fabrics are widely used in garments such as T-shirts, sweaters, and leggings due to their excellent elasticity and ability to conform to the body. Additionally, weft knitting allows for a wide range of stitch patterns, offering designers creative flexibility in their projects. The softness and drape of weft knitted fabrics make them a favorite choice in casual and activewear.
Fabric thickness
Neoprene (chloroprene rubber) is a versatile material used across various industries, with its thickness significantly influencing its properties and applications. Below is an overview of common neoprene thicknesses and their typical uses:
1.5 mm Neoprene
- Applications: Ideal for lightweight wetsuits, dive skins, and protective clothing in warm water environments.
- Properties: Offers flexibility and comfort, suitable for activities like surfing and snorkeling.
2 mm Neoprene
- Applications: Used in wetsuit vests, tops, and shorts for warm water sports.
- Properties: Provides moderate insulation while maintaining high flexibility.
3 mm Neoprene
- Applications: Commonly found in full wetsuits, gloves, and booties for water temperatures above 59°F (15°C).
- Properties: Balances insulation and flexibility, suitable for various water activities.
5 mm Neoprene
- Applications: Suitable for semi-dry suits, diving gloves, and boots in cooler water conditions.
- Properties: Offers enhanced thermal protection with reduced flexibility.
7 mm Neoprene
- Applications: Used in full-body wetsuits and dry suits for cold water diving.
- Properties: Provides substantial insulation but may limit mobility.
10 mm Neoprene
- Applications: Employed in specialized suits for extreme cold-water diving and industrial applications.
- Properties: Offers maximum thermal protection with significant reduction in flexibility.
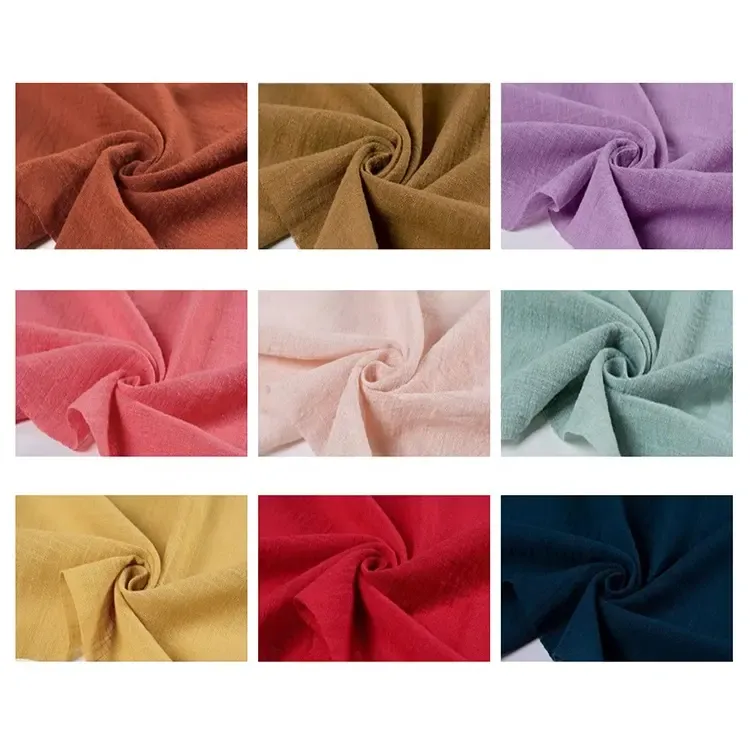
Fabric Printing Styles
Fabric printing is an essential aspect of textile design, allowing for the creation of unique patterns and vibrant colors that enhance the aesthetic appeal of fabrics. Various printing styles cater to different tastes and applications, providing endless possibilities for customization. Let’s explore some of the most popular fabric printing styles:
1. Intricate Printing
2. Black and White Printing
3. Botanical Prints
4. Geometric Prints
5. Knitted Jacquard
6. Abstract Prints
Fabric hardness
Neoprene (chloroprene rubber) is a versatile elastomer available in various hardness levels, measured on the Shore A durometer scale. The hardness of neoprene influences its flexibility, durability, and suitability for specific applications. Below is an overview of common neoprene hardness ranges and their typical uses:
Soft Neoprene (Shore A 20–40)
Medium Soft Neoprene (Shore A 40–50)
- Applications: Suitable for weather stripping, insulation, and marine seals.
- Properties: Provides a balance between flexibility and durability, with good resistance to oils and weathering.
Medium Hard Neoprene (Shore A 50–60)
- Applications: Commonly used in automotive seals, hoses, and vibration mounts.
- Properties: Offers enhanced durability and resistance to abrasion, oils, and ozone.
Hard Neoprene (Shore A 60–70)
- Applications: Ideal for industrial gaskets, rollers, and conveyor belts.
- Properties: Provides high tensile strength and excellent resistance to oils, fuels, and weathering.
Very Hard Neoprene (Shore A 70–80)
- Applications: Used in heavy-duty industrial applications, including gaskets for high-pressure environments and protective covers.
- Properties: Offers superior abrasion resistance and structural integrity under stress.

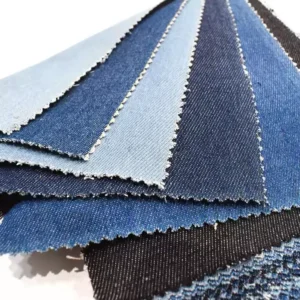
Fabric Surface Treatments
Neoprene’s versatility is amplified through specialized surface treatments that tailor its properties for specific applications. Here’s how we modify and optimize neoprene fabric at Szoneier:
1. Functional Coatings
Waterproofing (PU/PVC Coatings):Adds a seamless waterproof layer for marine gear, wetsuits, or outdoor accessories.
Anti-Slip Textures:Silicone or rubberized patterns improve grip for yoga mats, footwear, or industrial safety gear.
UV-Resistant Finishes:Protects against sun degradation for outdoor equipment and apparel.
Flame-Retardant Treatments:Critical for automotive, aerospace, or industrial applications requiring fire resistance.
2. Aesthetic & Branding Enhancements
Sublimation Printing:Vibrant, fade-resistant colors for custom designs, logos, or patterns on sportswear and fashion items.
Embossing/Debossing:Creates 3D textures or branded logos (e.g., luxury bags, tech accessories).
Laser Cutting/Etching:Precision detailing for intricate patterns or breathability in performance wear.
Fabric Lamination:Bonds neoprene with nylon, polyester, or knit layers for a softer feel (ideal for apparel linings).
3. Technical Modifications
Abrasion-Resistant Layers:Reinforces high-wear areas in industrial covers or motorcycle gear.
Thermal Reflective Coatings:Enhances heat retention for cold-weather gear or medical supports.
Antimicrobial Treatments:Ideal for medical braces, footwear, or reusable products requiring hygiene.
4. Structural Adaptations
Perforation:Adds breathability to wetsuits, athletic gear, or laptop sleeves.
Adhesive Backing:Enables easy bonding for DIY projects or industrial padding.
Weight Grading:Custom thickness (1mm–7mm+) paired with surface treatments for targeted flexibility or rigidity.
Factory Direct Wholesale Stock Cotton Fabric Styles
High-quality source manufacturers, providing bulk orders, spot and customized solutions for global retailers. Guaranteed fast delivery.
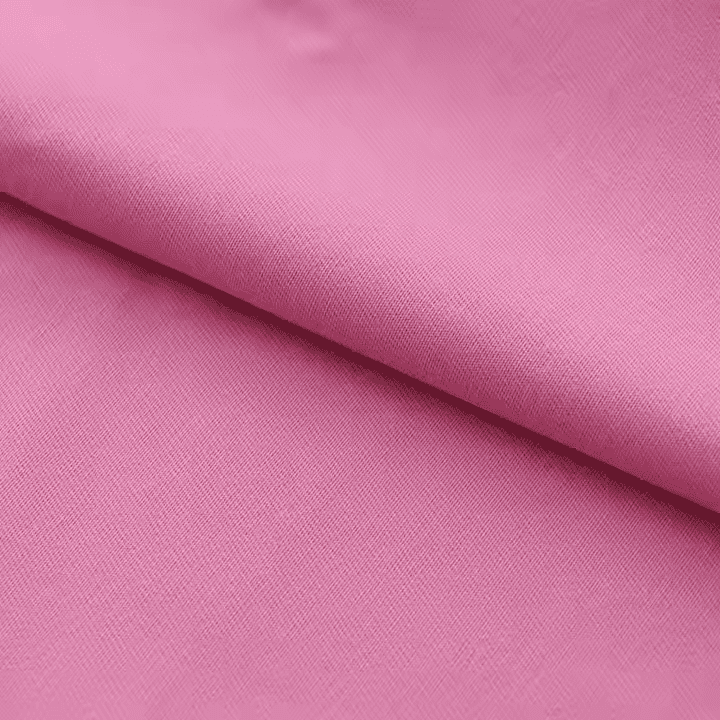
240 Gsm Twill Cotton Fabric
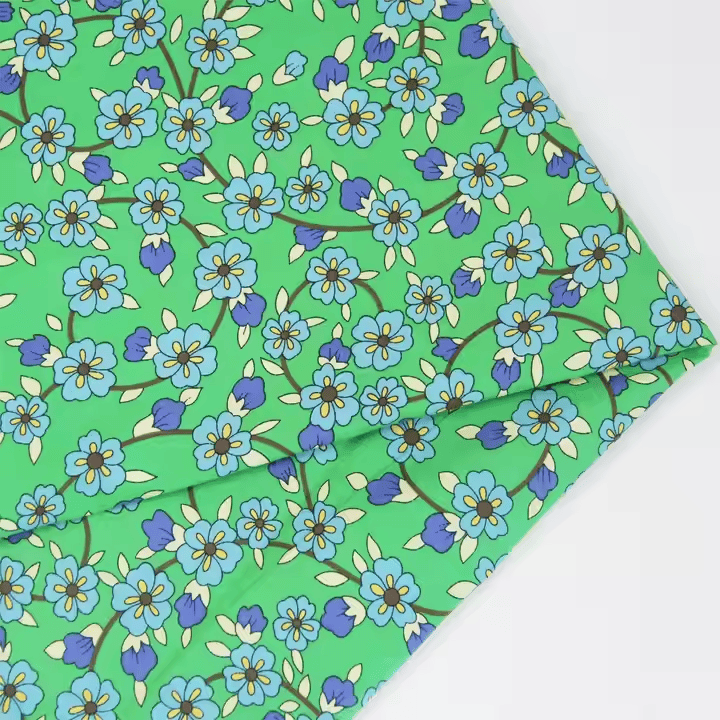
100 Cotton Fabric 40s Poplin
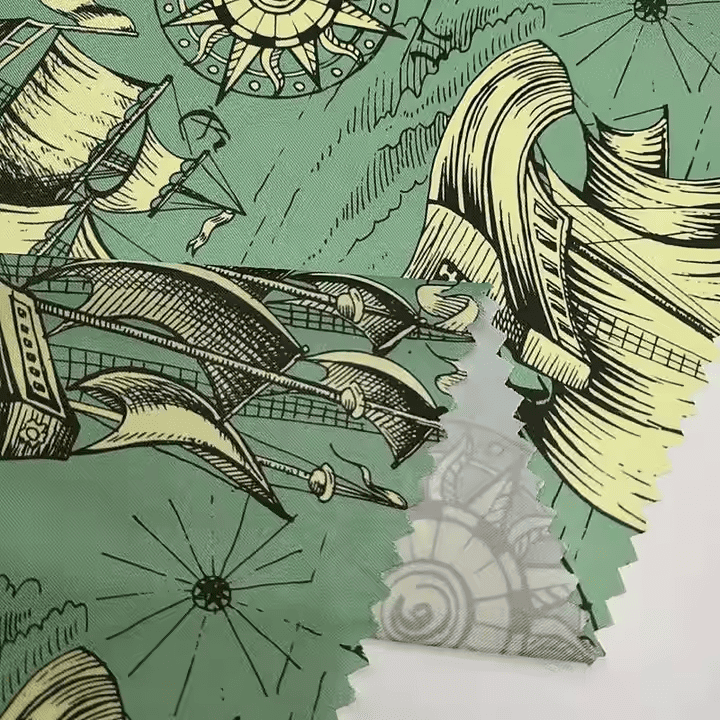
100 Cotton Printed Baby Girl Fabric Printing
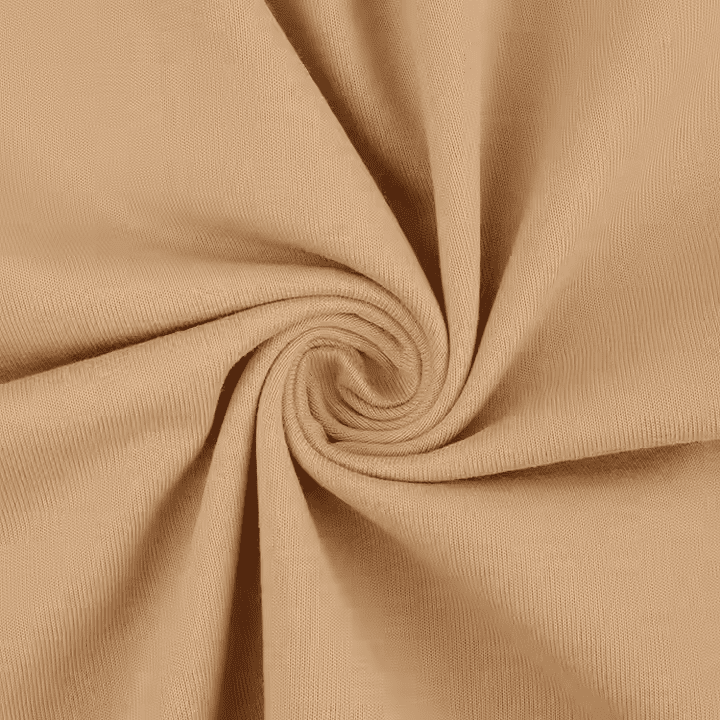
100 Pure Cotton Fabric
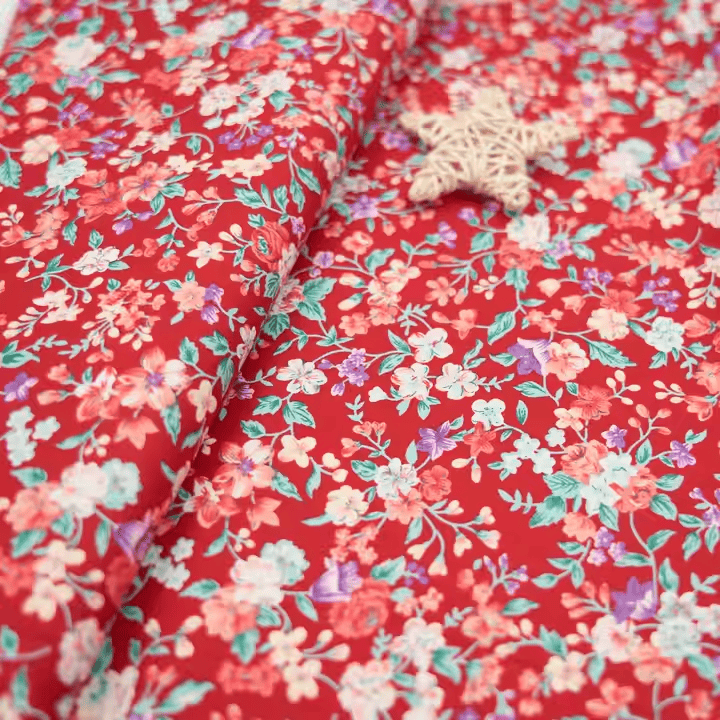
Liberty Cotton London Fabric
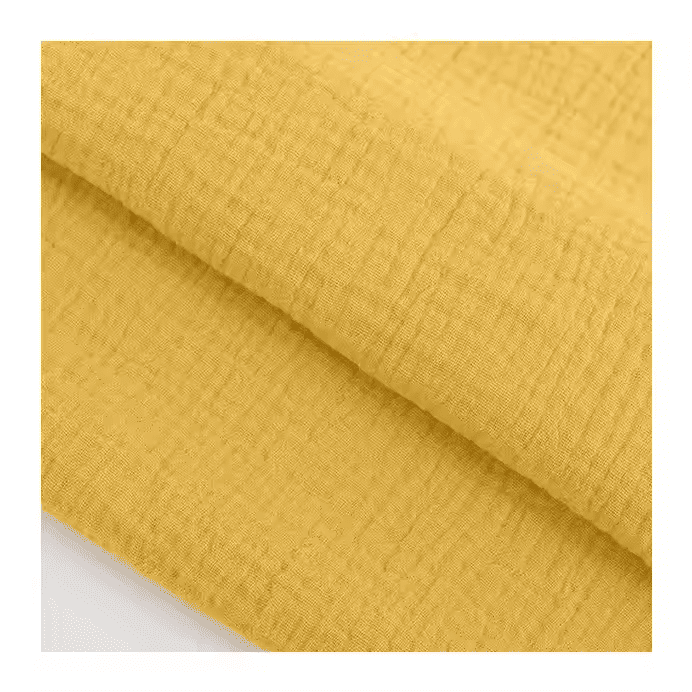
Crepe Double Gauze Layer Organic Cotton
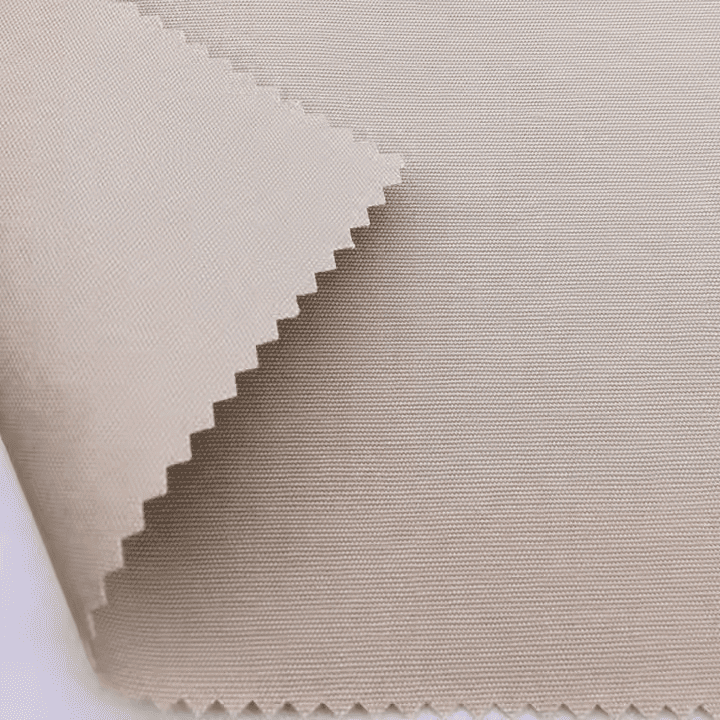
Eco Friendly Organic Moon Light Plain Canvas 100 Cotton Fabric

Inspired Fabric Cotton Fabric
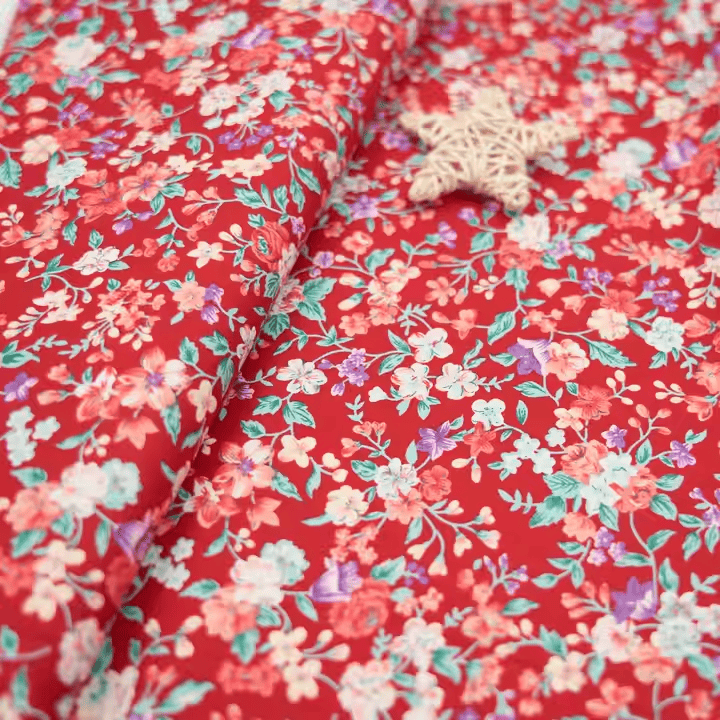
Liberty Cotton London Fabric
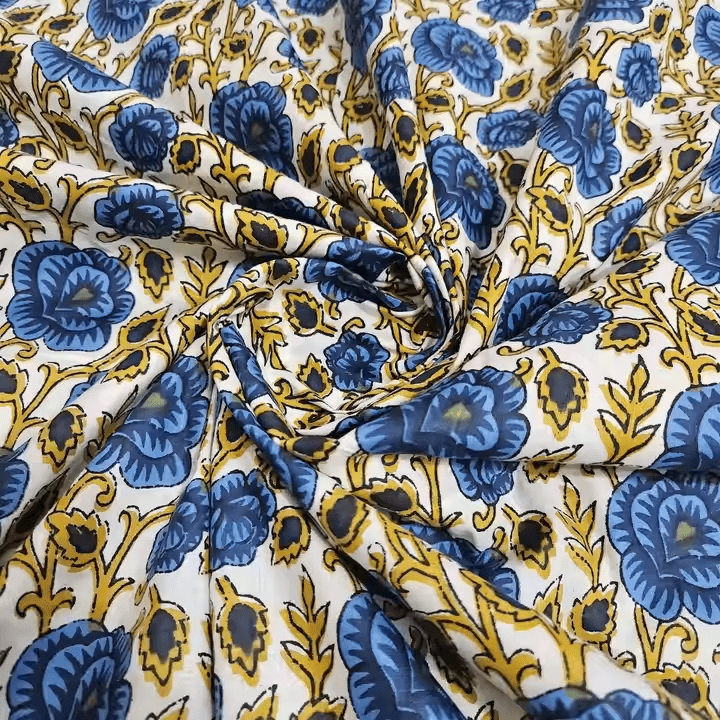
Options Printed Cotton Fabric
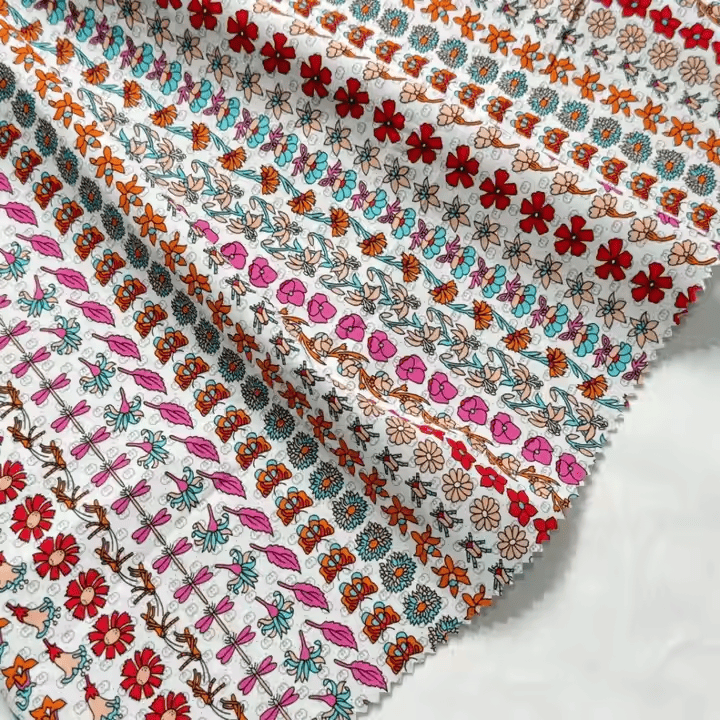
Poplin 100 Cotton Fabric
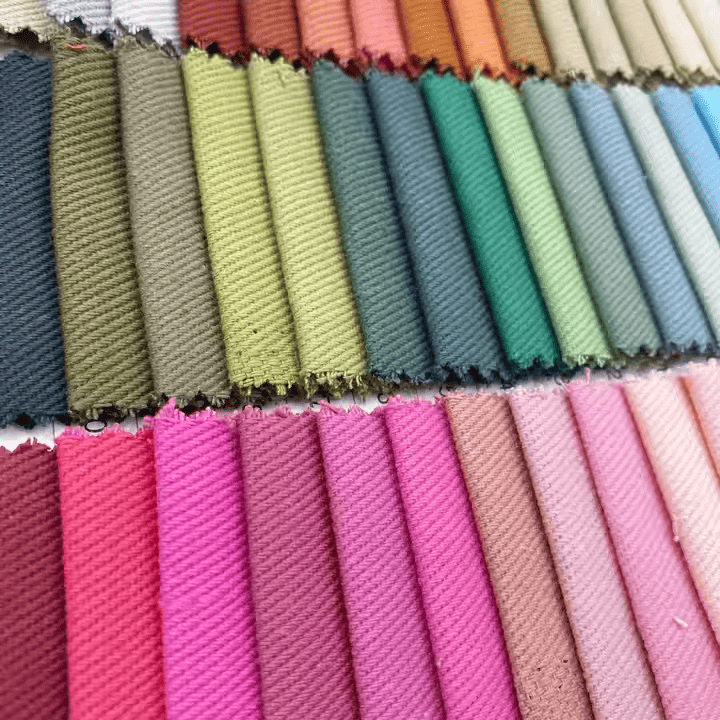
Pure Cotton Fabric 355Gsm 100 Cotton Fabric
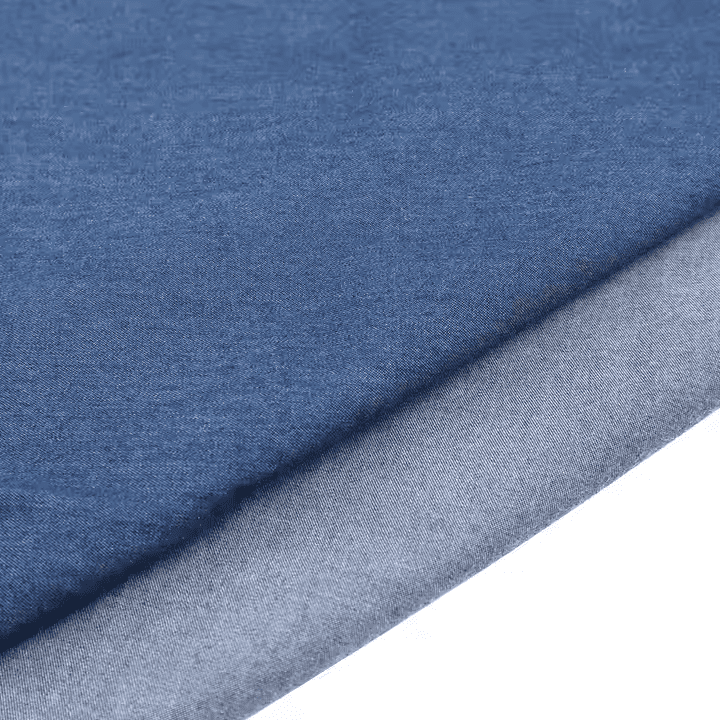
Rayon Twill Stretch DIY Plain Soft Washed Denim Quilting Cotton Poplin Fabric
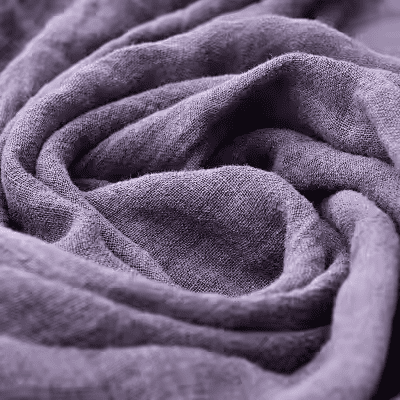
Single 100 Cotton Jersey Fabric 115GSM
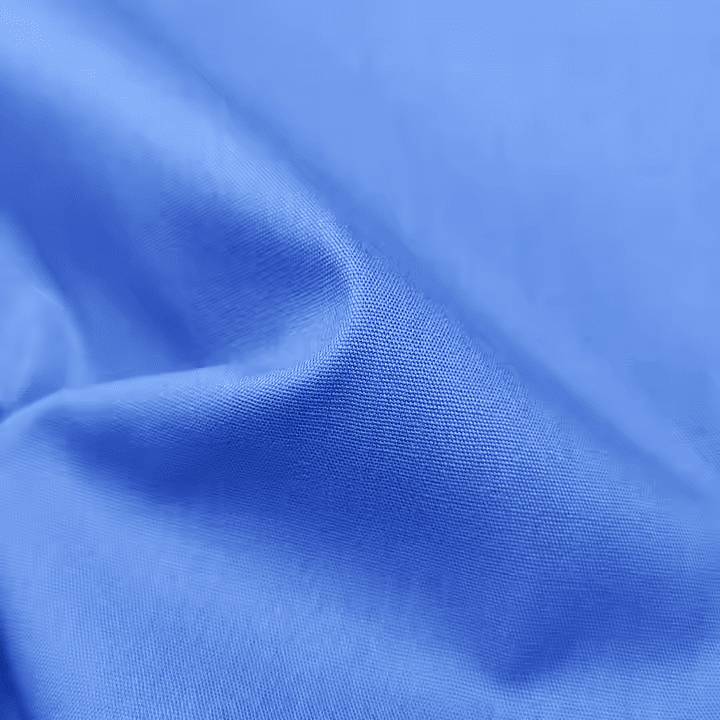
Solids Poplin 100 Cotton Fabric
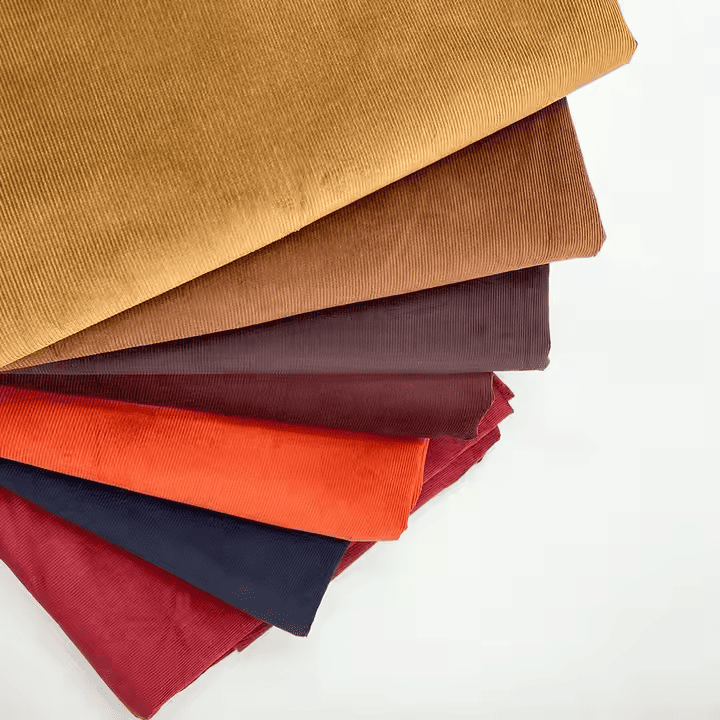
Textile Clothing Stretch Cotton Baby Wale Corduroy Fabric
Fabric Post Treatment Processes
Fabric finishing processes play a vital role in enhancing the quality and performance of our polyester fabrics. At the Szoneier mill, we use advanced technologies to ensure that each fabric meets the highest standards of durability, softness and functionality. Our finishing processes include dyeing, finishing and coating methods that not only enhance color vividness and fade resistance, but also enhance properties such as water and stain resistance. Through the careful application of these processes, we ensure that our polyester fabrics are not only beautiful, but also meet the needs of a variety of applications. We have listed 50 processes to make them the perfect choice for your needs.
What is Pre-shrinking ?
Pre-shrinking is a process that uses physical methods to reduce the shrinkage of fabric after water immersion, thereby lowering the shrinkage rate. Mechanical pre-shrinking involves wetting the fabric with steam or mist, followed by mechanical squeezing in the warp direction, which increases the amplitude of buckling waves, and then subjecting it to relaxed drying.
What is Stretching ?
Stretching is a finishing process that utilizes the plasticity of fibers like cellulose, silk, and wool in humid conditions. By gradually expanding the fabric to a specified width, this method stabilizes its shape during drying. Known as dimensional finishing, it helps the fabric maintain its intended dimensions and improves its overall structure, reducing distortion during use.
What is Sizing ?
Sizing is a technique that involves applying a sizing solution to the fabric and subsequently drying it to enhance its stiffness and body. This process improves the fabric’s strength, making it easier to handle during manufacturing and providing a more substantial feel. Sizing also helps reduce fraying and ensures better dye absorption, resulting in improved color depth and uniformity.
What is Heat Setting ?
Heat setting is a finishing process that stabilizes thermoplastic fibers in synthetic materials like nylon and polyester, preventing shrinkage or deformation. By applying controlled heat and pressure, it maintains the fabric’s dimensions and enhances stability, improving durability and providing a firmer hand feel for better quality and performance in various applications.
What is Whitening ?
Whitening enhances the brightness and whiteness of textiles using complementary colors. Techniques include blue tinting, which adds a subtle blue hue to reduce yellowing, and fluorescent whitening, which uses optical brighteners to reflect more light. These methods improve the fabric’s appearance, making it look cleaner and more vibrant.
What is Calendering, Electric Calendering, and Embossing ?
Calendering is a process that flattens fabric surfaces and creates patterns using heat and humidity to enhance luster. Flat calendering employs hard and soft rollers for a smooth finish, while soft calendering uses two soft rollers for a gentler gloss. Electric calendering utilizes heated rollers, and embossing adds patterns with engraved steel rollers, resulting in a lustrous look.
What is Napping ?
Napping is a finishing process that employs abrasive rollers or belts to raise a layer of short, dense fibers on the fabric’s surface. This brushing technique produces a plush nap, enhancing both the warp and weft yarns. The result is a soft, textured fabric that feels warm and inviting, making it ideal for clothing, blankets, and upholstery while improving its aesthetic appeal.
What is Raising ?
Raising is the process of lifting fibers from the surface of the fabric using dense needles or pricking, creating a layer of pile, also known as pile raising. This technique is primarily applied to coarse wool fabrics, acrylic fabrics, and cotton fabrics. The resulting pile layer enhances the fabric’s warmth, improves appearance, and provides a soft hand feel.
What is Shearing ?
Shearing is a process that removes unwanted fuzz from the fabric surface using a shearing machine. Its purpose is to clarify the fabric weave, achieve a smooth surface, or ensure an even finish on raised or fuzzy fabrics. Common products requiring shearing include wool fabrics, velvet, faux fur, and carpets.
What is Softening ?
Softening can be achieved through mechanical or chemical means. Mechanical softening involves multiple rubbing and bending actions on the fabric, but the resulting softness may not be ideal. Chemical softening involves applying softening agents to the fabric, reducing the friction coefficient between fibers and yarns, resulting in a noticeably soft and smooth hand feel.
What is Stiffening ?
Stiffening is a process that involves coating the fabric with a sizing solution and drying it to achieve a thick and firm hand feel. This finishing method aims to improve the fabric’s hand feel by applying a solution made from natural or synthetic polymers with certain viscosity, forming a thin film on the fabric that imparts smoothness, firmness, thickness, and fullness, while also enhancing the fabric’s strength and abrasion resistance.
What is Liquid Ammonia Treatment ?
Liquid ammonia treatment involves processing cotton fabrics with liquid ammonia to eliminate internal stress within the fibers, improving their luster and wear performance, reducing shrinkage, and increasing resilience, tensile strength, and moisture absorption. The resulting hand feel is soft, elastic, and resistant to wrinkles, with stable dimensions.
What is Weighting ?
Weighting is a process primarily aimed at compensating for the weight loss of silk fabrics after degumming, using chemical methods to increase the weight of silk textiles. Common methods include tin weighting, tannin weighting (not suitable for white or light-colored silk fabrics), and resin weighting.
What is Lightening ?
Lightening is a finishing process that utilizes the hydrolysis of polyester in high-temperature and specific concentrations of sodium hydroxide solution to gradually dissolve the fibers, reducing the fabric’s weight (typically controlled at 20%-25%) and creating depressions on the surface that lead to diffuse light reflection, resulting in a soft sheen. At the same time, the gaps between fibers in the yarn are enlarged, creating a silk-like effect.
What is Boiling Wool ?
Boiling wool is a process that treats wool fabrics in a hot water bath under tension to flatten and stabilize them, reducing deformation during later wet processing. Primarily used for finishing worsted wool fabrics, it enhances dimensional stability and improves hand feel, preventing future wrinkling or deformation.
What is Steaming Wool ?
Steaming wool is a process that stabilizes wool fabrics through steaming under humid heat conditions, improving hand feel and luster. This technique is primarily used for wool fabrics and their blends, but can also be applied to silk and viscose fabrics. The resulting fabric is dimensionally stable, with a smooth surface and a natural sheen, as well as a soft and elastic hand feel.
What is Pressing Wool ?
Pressing wool uses mechanical pressure and humid heat to flatten the fabric, enhancing its luster and texture. Key techniques include rotary pressing, which employs steam and heated cylinders for a smooth finish (though the shine is temporary), and electric board pressing, which offers a soft sheen and crisp feel but requires bulky equipment, mainly for worsted wool fabrics.
What is Felted Wool ?
Felted wool is a process that uses the felting property of wool to create dense, thick wool fabrics and form a pile on the surface, also known as fulling. Felting improves the hand feel and appearance of the fabric while enhancing its thermal insulation. This process is especially suitable for coarse wool fabrics.
What is Anti-felting ?
Anti-felting is a finishing process aimed at preventing or reducing the shrinkage and deformation of wool fabrics during washing and wear, thereby ensuring dimensional stability in garments. This principle involves chemically treating the scales to alter their surface state or covering the surface with a polymer layer to bond fiber interlace points, effectively removing the basis for felting.
What is Wrinkle Resistance ?
Wrinkle resistance is a finishing process that modifies the original composition and structure of fibers, enhancing their resilience and making the fabric less prone to wrinkling during wear. This method is primarily used for pure or blended cellulose fibers and can also be applied to silk fabrics.
What is Crinkle Finish ?
Crinkle finish is a process that creates various irregular wrinkles on fabric. Techniques include mechanical pressing for an embossed appearance, such as hand crinkling and rope crinkling, as well as rubbing methods like liquid flow dyeing and tumbler drying. This finish is mainly applied to pure cotton, polyester/cotton blends, and polyester filament fabrics.
What is Water Repellent Finish ?
Water repellent finishing involves treating fibers with chemical water repellents to lower the surface tension, causing water droplets to not wet the surface. This process is also known as breathable waterproof finishing and is suitable for materials used in raincoats and travel bags. Based on the durability of the water repellent effect, it can be categorized as semi-durable or durable.
What is Oil Repellent Finish ?
Oil repellent finishing involves treating fabrics with oil-repellent agents to create a surface that repels oil. Fabrics that undergo oil repellent finishing are also water-repellent and possess good breathability. This technique is mainly applied to high-quality raincoats and specialized wear materials.
What is Antistatic Finish ?
Synthetic fiber fabrics can accumulate static electricity due to low moisture and high crystallinity. Antistatic finishing applies chemical agents to enhance hydrophilicity and reduce static by creating a conductive layer on hydrophobic surfaces for ionization. However, this method is generally less effective and durable than blending or interlacing conductive fibers during weaving.
What is Easy-Clean Finish ?
Easy-clean finishing simplifies dirt removal from fabric during standard washing while preventing re-accumulation. It enhances the fibers’ surface hydrophilicity, reducing surface tension between the fibers and water. When wet, the hydrophilic layer expands, creating mechanical forces that help detach dirt by applying a hydrophilic polymer layer to the fabric’s surface.
What is Mold and Mildew Resistant Finish ?
Mold and mildew resistant finishing typically involves applying chemical anti-mold agents to cellulose fiber fabrics to kill or inhibit microbial growth. To prevent textiles from molding during wet processing or in humid environments, common anti-mold agents include formaldehyde and 2-phenylphenol.
What is Flame Retardant Finish ?
Flame retardant finishing involves treating fabric surfaces with flame retardant agents to improve the fabric’s fire resistance. Common flame retardant agents include phosphoramide, ammonium phosphate, and polyvinyl chloride, all of which can reduce combustion rate and slow down flame spread.
What is Waterproof Finish ?
Waterproof finishing treats fabric surfaces with agents like fluorocarbon compounds, polyurethane, and silicone to block moisture while maintaining breathability. This finishing is applied to products such as rain gear, tents, and outdoor sportswear. Fluoropolymer coatings are commonly used, forming a barrier against water without compromising airflow.
What is Durable Press Finish ?
Durable press finishing involves applying resin finishing to cellulosic fiber fabrics to improve their crease resistance. The finishing is primarily applied to fabrics that require high durability, such as workwear and casual wear. The primary agent used in durable press finishing is DMDHEU (dimethylol
dihydroxyethyleneurea).
What is Stain-Resistant Finish ?
Stain-resistant finishing involves applying agents to the surface of fabrics to reduce dirt adhesion and enhance stain resistance. This can be achieved through methods such as chemical treatment or applying a special surface coating. Common stain-resistant agents include fluoropolymer-based finishes, which repel water and oil-based stains.
What is Antimicrobial Finish ?
Antimicrobial finishing involves applying antimicrobial agents to the surface of textiles to inhibit microbial growth, odors, and degradation caused by bacteria and fungi. Common antimicrobial agents include silver ions, quaternary ammonium compounds, and organic biocides. This finishing technique is widely used in medical textiles, activewear, and home textiles.
What is Coating ?
Coating is a finishing process where a layer of polymer material is applied to the surface of the fabric, forming a barrier against water and other external factors. This process can also provide additional properties such as breathability and UV protection. Coatings can be applied using methods such as knife-over-roll or rotary screen printing.
What is Gluing ?
Gluing is a finishing process that utilizes adhesive materials to bond fabric layers or attach various components, such as linings and interlinings. This technique is commonly used in the production of garments and upholstery, providing structural integrity and durability to the final product.
What is Laminating ?
Laminating involves bonding two or more layers of fabric together using heat, pressure, or adhesives to create a composite material with enhanced properties. This process can improve the fabric’s strength, durability, and weather resistance, making it suitable for a variety of applications such as outdoor gear, footwear, and protective clothing.
What is Compounding ?
Compounding is a finishing process that combines different materials, such as rubber, plastic, or textile fibers, to create a composite material with specific performance characteristics. This technique is often used in the production of high-performance textiles, such as those used in automotive or industrial applications.
What is Composite ?
Composite finishing involves combining different textile materials or layers to enhance the overall performance of the fabric. This technique is commonly used in technical textiles, where multiple layers are bonded to achieve specific properties such as strength, breathability, and insulation.
What is Sanding ?
Sanding is a finishing process that involves abrading the surface of the fabric to create a soft, velvety texture. This technique is often applied to cotton and polyester fabrics, resulting in a luxurious hand feel and enhancing the fabric’s aesthetic appeal.
What is Brushing ?
Brushing is a finishing process that lifts and opens the surface fibers of the fabric, creating a soft and fuzzy texture. This technique is commonly used on fabrics like fleece and flannel, providing a cozy hand feel and enhancing warmth.
What is Crimping ?
Crimping is a process that imparts a wave or crinkle effect to fibers or fabrics, enhancing their texture and appearance. This technique is often used in synthetic fibers to improve their elasticity and resilience.
What is Thickening ?
Thickening is a finishing process that involves adding a thickening agent to the fabric, enhancing its texture and weight. This technique is commonly used in heavy-duty textiles, such as canvas and denim, to improve durability and performance.
What is Pilling Resistance ?
Pilling resistance is a finishing process that enhances the fabric’s ability to resist the formation of pills or small balls of fibers on the surface. This technique is especially important for fabrics that are subject to frequent abrasion, such as knitwear and upholstery.
What is Color Fastness ?
Color fastness finishing involves treatments that enhance the fabric’s ability to retain its color and resist fading during washing and exposure to sunlight. This technique is essential for ensuring the longevity of dyed textiles and is commonly applied to garments and home textiles.
What is Lightfastness ?
Lightfastness finishing involves applying treatments that protect the fabric from fading or discoloration due to exposure to light. This process is particularly important for outdoor textiles and fabrics used in window treatments, ensuring that they maintain their original appearance over time.
What is Thermal Insulation ?
Thermal insulation finishing involves treatments that enhance the fabric’s ability to retain heat, providing warmth and comfort in cold conditions. This technique is commonly used in outerwear and bedding, utilizing materials such as down or synthetic insulation.
What is UV Protection ?
UV protection finishing involves treatments that enhance the fabric’s ability to block harmful ultraviolet (UV) radiation from the sun. This process is essential for outdoor textiles, such as swimwear and sun protective clothing, ensuring that they provide adequate protection against sun damage.
What is Antibacterial Finish ?
Antibacterial finishing involves applying treatments to the fabric that inhibit the growth of bacteria, preventing odors and degradation. This technique is commonly used in activewear and medical textiles, providing added hygiene and freshness.
What is Odor Control ?
Odor control finishing involves treatments that reduce or eliminate odors in fabrics, enhancing their freshness and wearability. This process is often applied to activewear and home textiles, utilizing antimicrobial agents and odor-absorbing materials.
What is Flame Resistant Finish ?
Flame resistant finishing involves applying treatments to fabrics that enhance their ability to resist ignition and slow down the spread of flames. This process is crucial for protective clothing and upholstery in environments where fire hazards are present.
What is Reinforcement ?
Reinforcement finishing involves adding extra layers or materials to enhance the strength and durability of fabrics. This technique is commonly used in workwear, outdoor gear, and upholstery, ensuring that textiles can withstand wear and tear.
What is Environmental Finishing ?
Environmental finishing involves applying treatments and processes that minimize the environmental impact of textiles, such as using eco-friendly dyes and finishes, reducing water and energy consumption, and implementing recycling practices.
Free Pantone Color Choice
For all your polyester fabric customization needs, we offer a free Pantone color selection to ensure your products reflect your exact vision. Our extensive color chart includes a wide array of Pantone options, allowing you to select the perfect shade to match your project requirements—whether it’s for apparel, bags, outdoor gear, or home textiles. Each color category is carefully curated to include vibrant tones, soft neutrals, and everything in between, providing a diverse palette to inspire creativity.
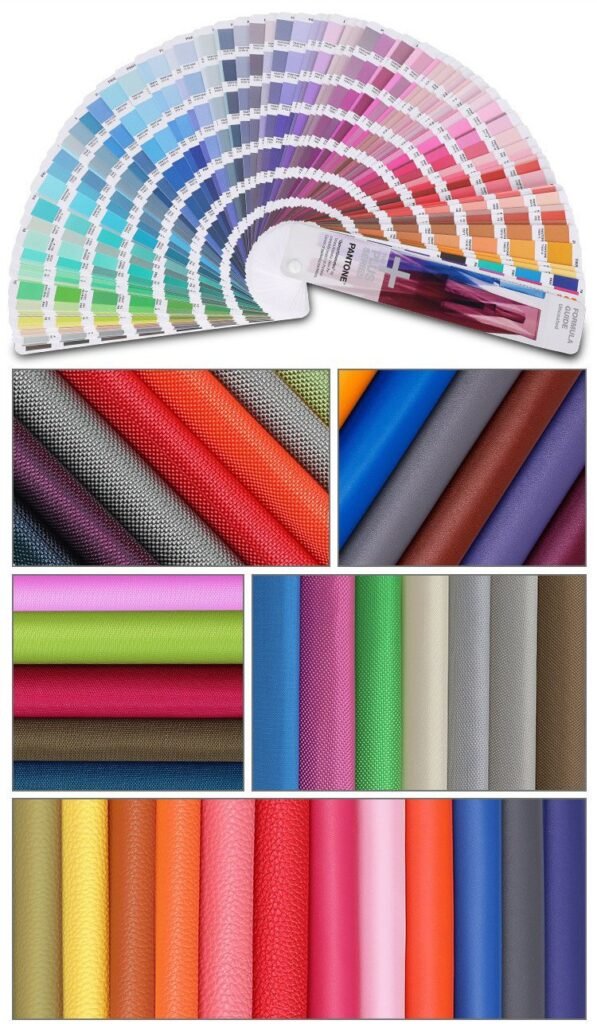
Color Categories:Our fabric color chart is divided into clear categories, making it easy for you to navigate and find your desired hues. Whether you’re searching for bold colors that stand out or subtle tones for a minimalist design, our organized color chart ensures quick selection. These categories cover a full spectrum of options, from bright and eye-catching shades to more muted and elegant tones, perfect for any polyester fabric project.
Color Swatches and Codes:Each category contains multiple swatches that display the available shades within that color family. Next to each swatch, you’ll find the Pantone color code, which ensures consistency and accuracy when placing your order. These Pantone codes serve as an industry standard, guaranteeing that the color you see on our chart is exactly what will be delivered in the fabric. This attention to detail ensures that your products maintain their visual appeal and stay true to your original design.
Custom Color Options:If our extensive standard chart doesn’t perfectly match your needs, we also offer fully customizable fabric colors. Simply provide us with your desired Pantone code or specific color samples, and our team will work with you to develop a fabric color that fits your exact vision. This option is ideal for companies looking for exclusive branding opportunities or designers aiming to create a unique and personal touch.
Digital Rendering Services:To help you visualize how your chosen fabric color will appear on your finished product, we provide digital rendering services. This allows you to preview how the selected color looks in context, whether it’s on a garment, bag, or other textile product. With this tool, you can fine-tune the color choice or make adjustments to other design elements before production begins, ensuring that your custom polyester fabric meets your expectations.
Production Process Of Fabric
At Szoneier factory, the production process of polyester fabric is a blend of advanced technology and meticulous craftsmanship. We begin with the polymerization of raw materials to create polyester fibers, which are then spun into yarn. These yarns undergo weaving or knitting to form the base fabric. To ensure top-tier quality, each stage of production is carefully monitored, from dyeing and finishing to applying special treatments like water resistance or UV protection. Our cutting-edge machinery allows us to produce fabrics in a wide range of textures and finishes, customized to meet the specific needs of your project. With our commitment to precision and excellence, you can count on durable, vibrant, and versatile polyester fabrics ready for any application.
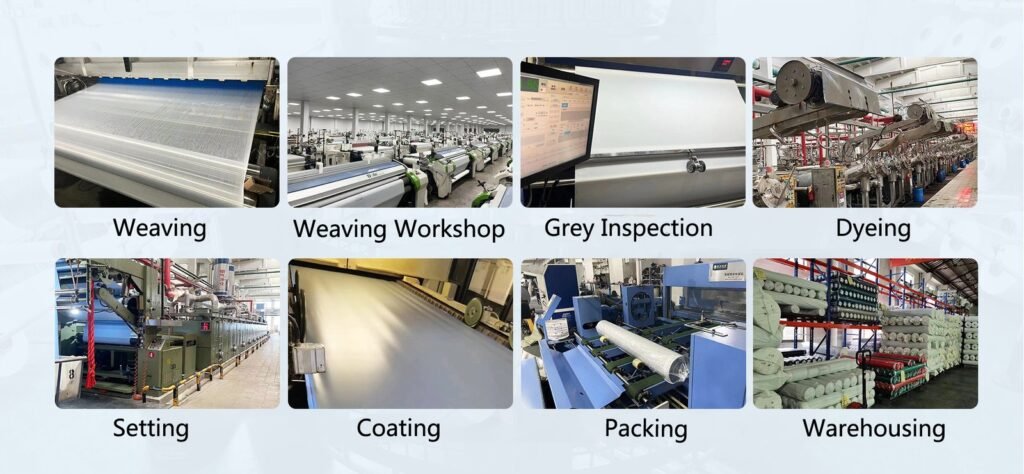

Testing Equipment Of Fabric Production
At Szoneier fabric production factory, we utilize state of the art testing equipment to ensure the highest standards of quality and durability. Our advanced machinery includes tensile strength testers, colorfastness testing equipment, abrasion resistance testers, and moisture control systems. Each piece of fabric undergoes rigorous testing for consistency, performance, and longevity, allowing us to guarantee top-quality products that meet both industry standards and customer expectations. This commitment to quality ensures fabric excellence from production to final delivery.
Make A Sample First?
Got a specific artwork, logo, or design concept in mind? We’re all ears! Share every detail—your preferred fabric type, Pantone colors, and any custom features you want. Our team will partner with you to nail your vision with precision. We’ll start by creating a fabric sample so you can touch, feel, and inspect the quality, texture, and color firsthand before committing to full production. This way, we tweak things until it’s exactly what you imagined. Let’s turn your ideas into a fabric that’s uniquely yours !
Video Of Product And Production
Get a behind the scenes look at our fabric production process with our exclusive factory video. where you can witness the fascinating journey of our polyester fabrics from raw materials to finished products. Our informative videos provide a behind-the-scenes look at the advanced techniques and skilled craftsmanship that define our manufacturing process. Whether you’re interested in the production methods or the innovative designs we offer, these videos reflect our dedication to quality and creativity in fabric development. Join us and explore the artistry of our fabric production!
Cooperating Brands Trusted
Your product is produced in reliable factory like our already cooperating international brand partners below:
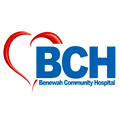
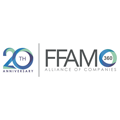
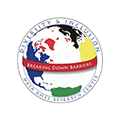
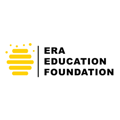
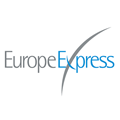
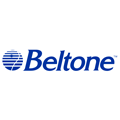
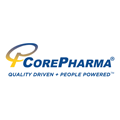

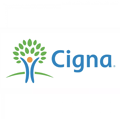
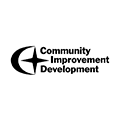

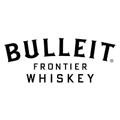
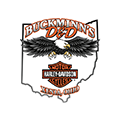
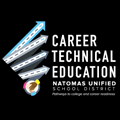
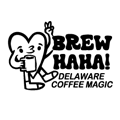
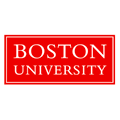
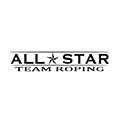
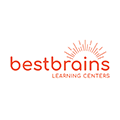
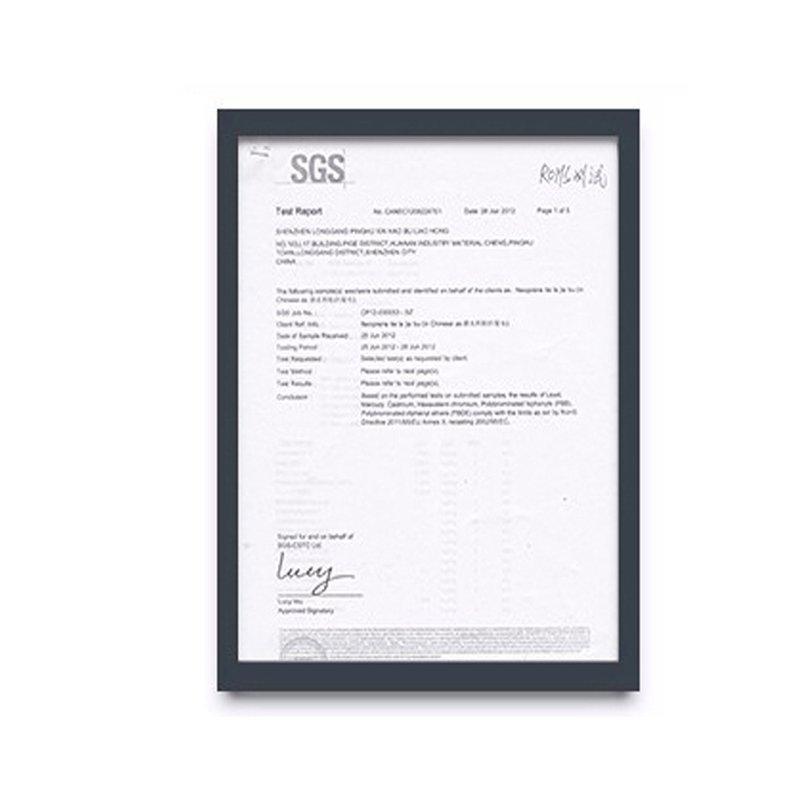
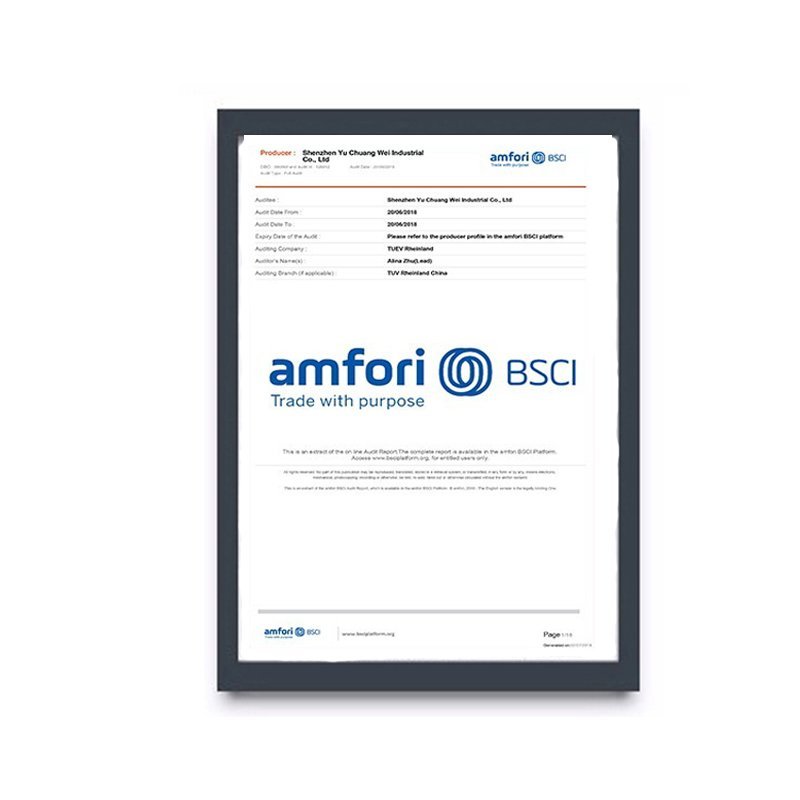
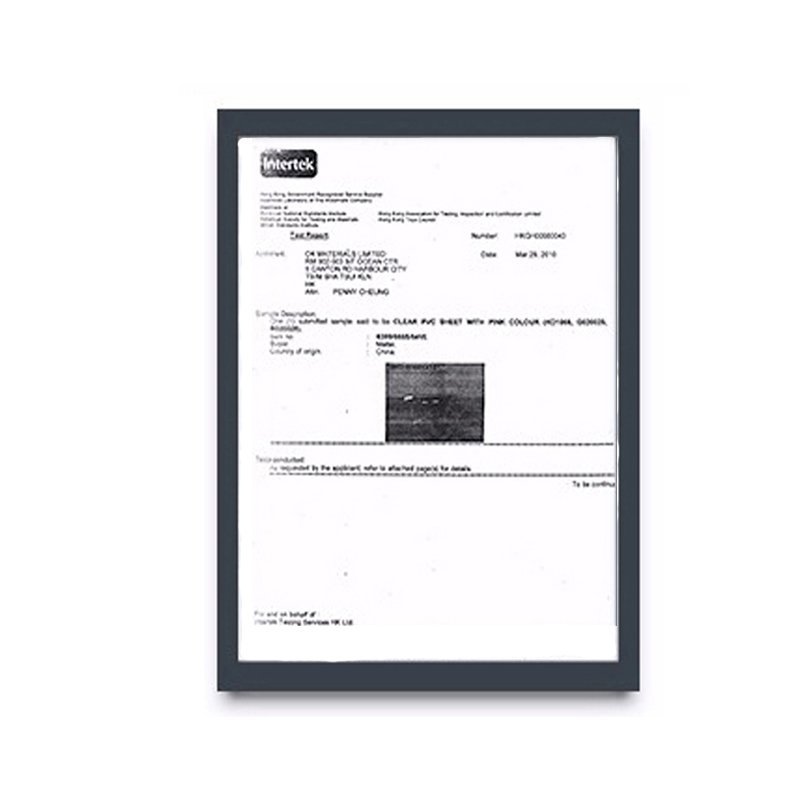
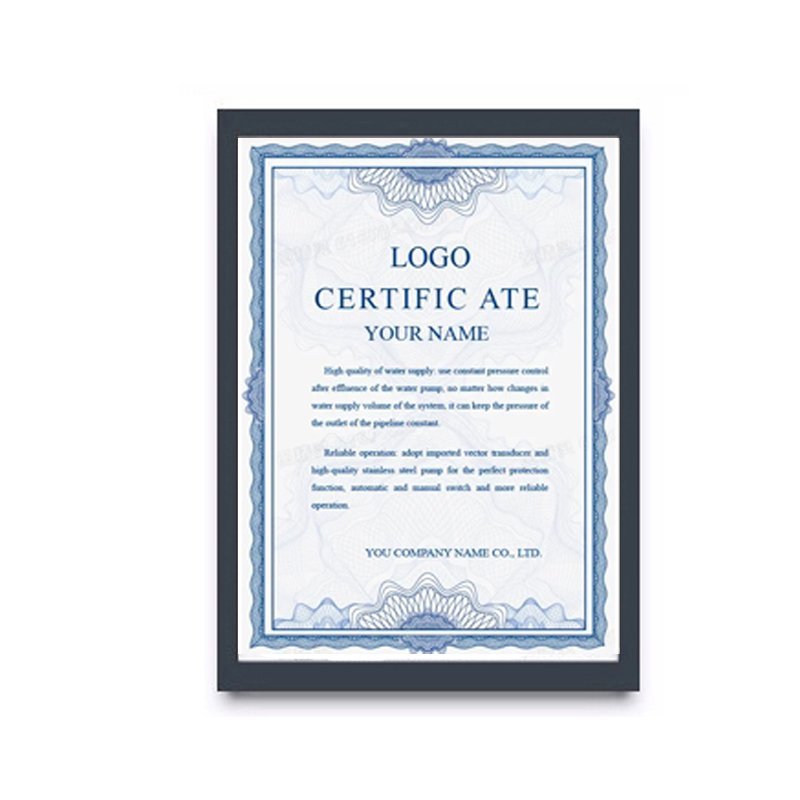
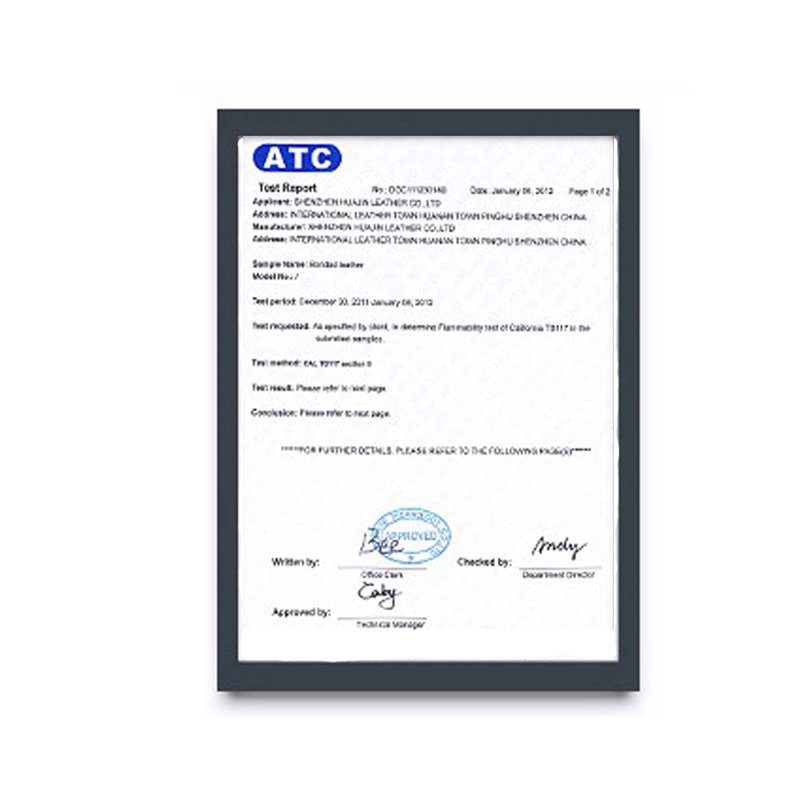
International Certification
You can totally trust us with all certifications shown below.
Yes, cotton is naturally breathable. Its fibers allow air to flow through, keeping the body cool and comfortable, making it an ideal choice for warm-weather clothing and bedding.
Cotton is easy to care for and can typically be machine washed and dried. However, to maintain its softness and prevent shrinking, it’s best to follow the care instructions, such as washing in cold water and air drying or using low heat settings.
Yes, cotton is a natural, biodegradable fiber. Organic cotton is even more eco-friendly, as it is grown without synthetic pesticides or fertilizers. It’s a great choice for sustainable fashion and textiles.
Yes, cotton fabrics are versatile and can be used for a variety of outdoor gear, such as jackets, bags, and camping gear. For outdoor applications, thicker and more durable cotton fabrics like canvas or twill are often preferred.
When selecting cotton fabric, consider factors like weight, texture, and durability. For clothing, lightweight cotton is ideal, while heavier fabrics like denim or canvas are great for bags and outerwear. Feel free to contact us for guidance on choosing the perfect fabric for your needs.
Frequently Asked Questions
Welcome to our FAQ section on customized nylon fabrics, where we answer your most common questions and provide insights into fabric types, customization options, features, and order-related details. Whether you’re looking to learn more about the various nylon fabric styles, specialized finishes, or the ordering process, we’re here to help. Our goal is to ensure that you have all the information needed to make informed decisions about selecting the perfect nylon fabric for your unique project.
