Tired of sorting through buzzwords to choose the right synthetic fiber for your next collection or product line? Polyester and polyamide (commonly known as nylon) dominate the performance-fabric market, yet they differ in surprisingly meaningful ways—from molecular makeup to wearer comfort and environmental impact. In this guide, we’ll cut through the noise to answer the single most important question:
Polyester and polyamide are both versatile synthetic fibers, but polyester excels in colorfastness and moisture resistance while polyamide offers superior elasticity, abrasion strength, and next-to-skin comfort. Use polyester when you need rugged, low-cost goods with easy care; choose polyamide for stretch activewear, high-performance hosiery, and lightweight technical gear.
Imagine your favorite rain jacket: is it a stiff, guard-against-downpour shell or a soft, packable windbreaker you barely notice? The answer often lies in the choice between these two synthetics. Ready to dive in? Let’s unravel the science, the care, the sustainability—and how SzoneierFabrics can custom-engineer your perfect blend.
What Are Polyester and Polyamide?
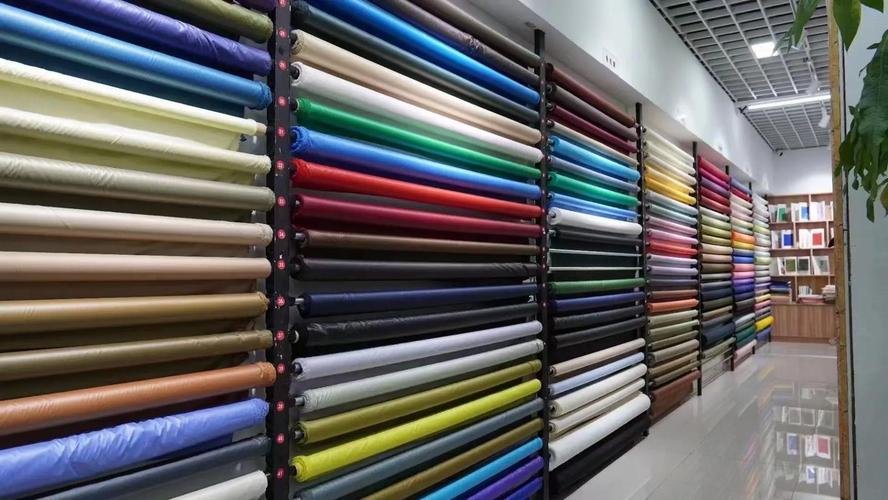
Polyester originated in the 1940s as an affordable, resilient fiber made by linking ethylene glycol and terephthalic acid. Polyamide, invented a decade earlier, forms from hexamethylenediamine and adipic acid to yield nylon—a breakthrough in elasticity and abrasion resistance.
Polyester is a stiff, hydrophobic fiber prized for color retention and low-moisture uptake; polyamide is a slippery, elastic fiber celebrated for its strength, stretch recovery, and next-to-skin softness.
Origins and Chemistry
- Basic Monomers Polyester: Ethylene glycol + terephthalic acid → PET Polyamide: Hexamethylenediamine + adipic acid → Nylon-6,6
- Polymerization Process Step Polyester (PET) Polyamide (Nylon-6,6) Catalyst None or antimony oxide Phosphoric acid derivative Temperature 260–280 °C 260–275 °C By-products Water, ethylene by-products Water
- Critical Thought How do residual catalysts affect dye uptake and FDA-approved food-contact applications? Could emerging bio-based feedstocks yield “green” versions of each without sacrificing performance?
How Do Their Molecular Structures Influence Performance?
Polyester’s ester linkages confer a very low moisture regain (\~0.4%), making it quick-drying but prone to static build-up. Polyamide’s amide bonds allow higher moisture regain (\~4–5%), giving nylon fabrics a softer hand but slower drying.
The stronger hydrogen bonding in polyamide yields better elasticity and moisture wicking, while polyester’s non-polar ester groups deliver superior hydrophobicity and shape retention.
Ester vs. Amide Linkages
- Hydrogen Bonding Polyester: minimal → lower moisture but static Polyamide: significant → better comfort, dye affinity
- Thermal Behavior Property Polyester Polyamide Melting Point 250–260 °C 260–265 °C Glass Transition 70–80 °C 50–60 °C
- Critical Thought In stretch blends, how does differential thermal behavior impact garment stability under heat? Could nano-composite additives tune each polymer’s moisture and thermal responses for specialized sportswear?
Which Mechanical Properties Set Polyester and Polyamide Apart?
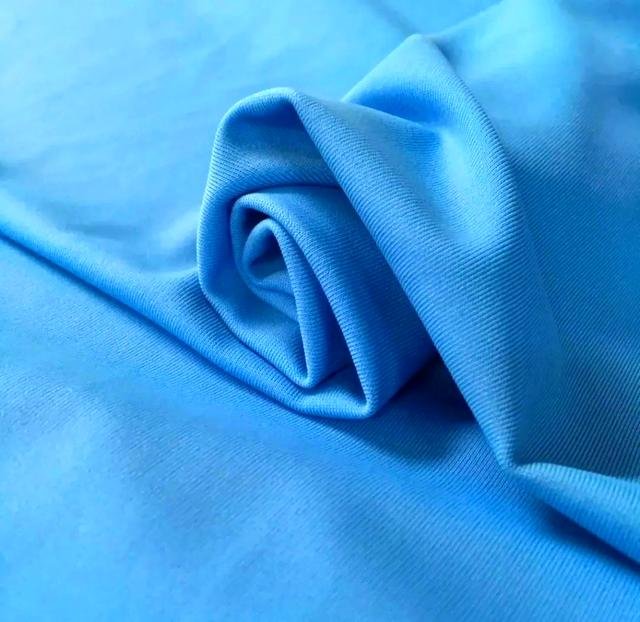
Polyamide boasts higher tensile strength (typically 800–1200 MPa) and abrasion resistance, while polyester excels in UV stability and resilience against repetitive laundering.
Summary Answer: Nylon outperforms polyester in toughness and elasticity, making it ideal for hosiery, climbing ropes, and stretch‐denim; polyester offers better UV resistance and colorfastness for outdoor gear and home textiles.
Strength, Abrasion & Stretch
- Tensile & Tear Metric Polyester Polyamide Tensile Strength (MPa) 600–900 800–1200 Elongation at Break (%) 15–30 20–50
- Abrasion Resistance Polyester: good, but can fuzz Nylon: excellent, resists pilling
- Critical Thought For hybrid backpacks, does the polyamide front panel truly extend lifespan—or would a heavy-denier polyester suffice at lower cost? In technical fabrics, is there a point of diminishing returns when maximizing both strength and stretch?
How Do Polyester and Polyamide Compare in Moisture Management and Comfort?
Polyamide’s higher hydrophilicity gives it superior wicking; polyester’s hydrophobicity promotes quick-drying but can leave a clammy feel if not engineered with mesh or perforations.
Summary Answer: Nylon wicks and transports moisture more efficiently, while polyester dries faster—so blending the two often yields the best compromise for activewear.
Wicking vs. Drying
- Moisture Regain & Wicking Rate Fiber Regain (%) Wicking Speed (cm/hr) Polyester 0.4 20 Polyamide 4.5 35
- Hand & Feel Polyester: crisp, can feel stiffer Nylon: soft, silky smooth
- Critical Thought Could cross-section modifications (e.g., trilobal nylon) enhance drying without sacrificing wicking? Are consumer perceptions of “clammy” fabrics rooted more in weave density than polymer choice?
Are There Significant Differences in Durability and Abrasion Resistance?
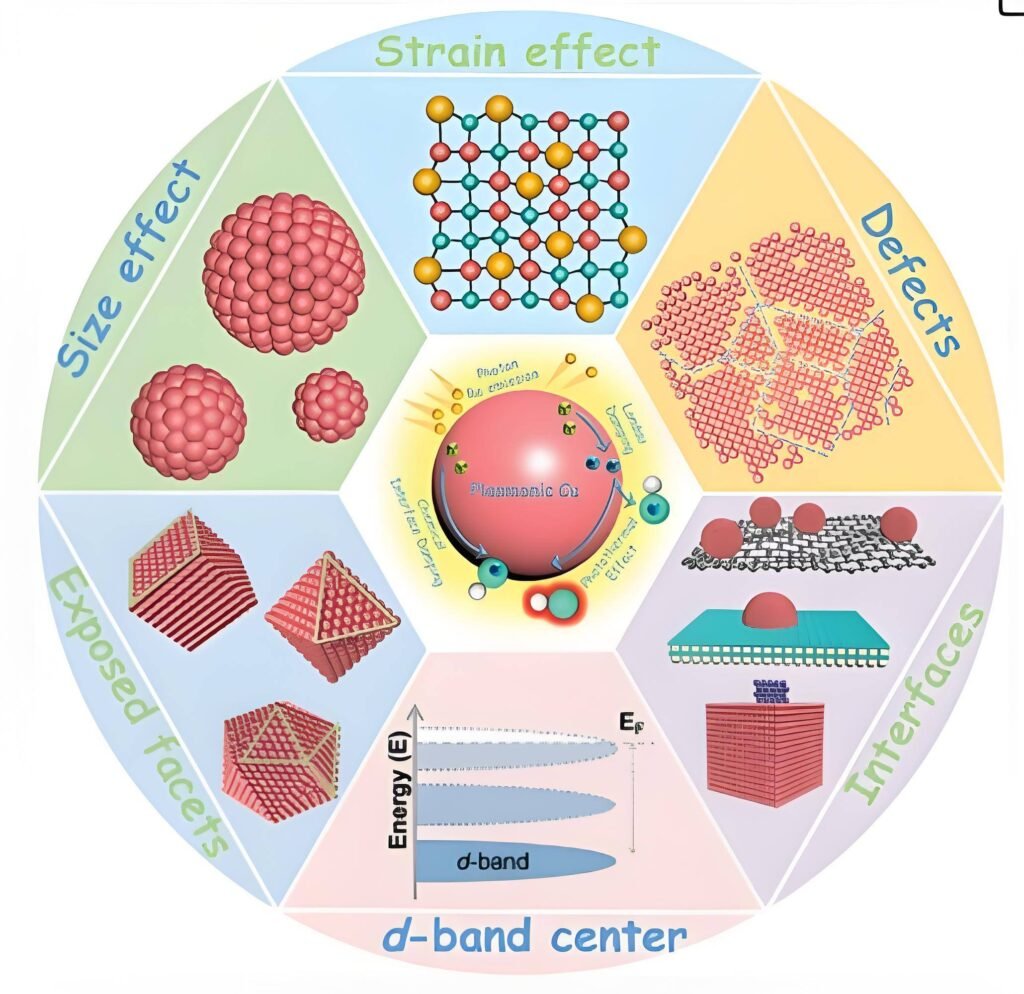
Yes. Nylon typically withstands 20–30% more abrasion cycles in Martindale tests than polyester of equivalent denier. However, polyester resists UV-induced degradation far better.
Choose polyamide for high-abrasion uses like luggage webbings and hosiery; choose polyester for outdoor awnings, flags, and UV-exposed upholstery.
Martindale & UV Resistance
- Abrasion Cycles Fiber Martindale Rating (cycles) Polyester 25,000 Polyamide 32,000
- UV Stability Polyester: 80% tensile retention after 500 hours Nylon: 50% after 500 hours unless UV-stabilized
- Critical Thought In marine applications, does nylon’s abrasion win offset the need for UV-coatings? Can novel stabilizers bring nylon’s UV resistance on par with polyester?
Which Environmental Impacts and Recycling Options Apply to Each Fiber?
Polyester has a massive existing recycling infrastructure (PET bottles → fiber), while nylon recycling is emerging (e.g., carpet reclamation) but less widespread.
Recycled polyester (rPET) offers a closed-loop path from bottles to garments; recycled nylon (e.g., ECONYL®) repurposes waste fishing nets but is costlier and less scalable.
Lifecycle & Microplastics
- Carbon Footprint (kg CO₂/kg fiber) Source Polyester Polyamide Virgin 5.5 8.5 Recycled (rPET/ECONYL) 3.0 4.5
- Microplastic Release Polyester: \~350 mg per 6 kg wash Nylon: \~250 mg per 6 kg wash
- Critical Thought Should brands favor nylon’s lower microfiber release despite higher virgin footprint? Could advanced wash-bag tech withdraw microplastics at scale, reducing polymer-choice trade-offs?
Do Polyester and Polyamide Require Distinct Finishing and Care Processes?
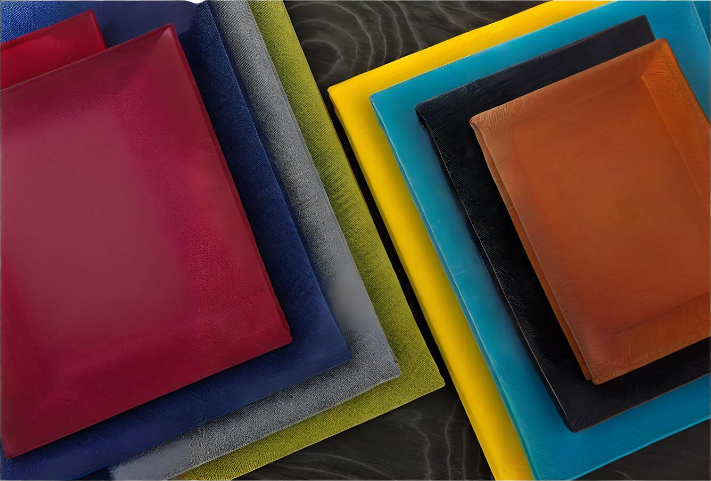
Each fiber benefits from tailored finishes: polyester often gets C6 fluorocarbon DWR and anti-static; nylon is treated for stain resistance and UV stabilization.
While both fibers can share stain-resistant and antimicrobial finishes, nylon often needs extra UV and heat-setting, whereas polyester benefits more from anti-static and softening treatments.
Finish Types & Care
- Common Finishes Finish Polyester Polyamide DWR Coating Standard C6/C0 Specialized low-temp cures Anti-Static Yes Less common Softening Silicone or PU emulsions Enzyme washes
- Care Guidelines Polyester: machine wash cold, low-heat tumble Nylon: hand wash/delicate, line dry to avoid heat damage
- Critical Thought As PFC-free DWRs evolve, can nylon finishes match polyester’s repellency? Will enzyme-based softeners replace silicones for eco-friendly “hand” in both fibers?
How Can Blending Polyester and Polyamide Optimize Fabric Performance?
By blending, you can engineer a fabric that wicks like nylon, dries like polyester, resists UV, and stretches comfortably—all in one. Common ratios range from 65/35 to 50/50 blends.
Strategic poly-blend fabrics leverage polyester’s hydrophobicity and UV stability alongside nylon’s elasticity and moisture transport, creating versatile performance textiles.
Dive Deeper: Blend Strategies
- Blend Ratios & Effects Blend (PES/PA) Wicking Drying Speed Stretch Recovery 65/35 30 80 20 50/50 35 70 30
- Weave & Knit Considerations Warp-knit tricot vs. woven plain weave Impact on mechanical stretch and dimensional stability
- Critical Thought For sustainable activewear, does a tri-component yarn (PES/PA/TENCEL™) add enough benefit to offset processing complexity? How will emerging circular-economy platforms handle multi-polymer blends at end-of-life?
Ready to Customize Your Perfect Blend?
Navigating the polyester vs. polyamide decision is all about matching fiber chemistry to end-use demands—whether it’s lightning-fast drying, marathon-worthy stretch, or low-impact recyclability. At SzoneierFabrics, we bring years of R\&D expertise, 100% quality assurance, low MOQ flexibility, and rapid sampling to help you dial in the exact PES/PA ratio, yarn count, and finish that your brand—and your customers—need.
Contact us today for a free design consultation and sample pack. Let’s co-create the next generation of high-performance textiles!