In large-scale textile manufacturing, even the smallest mishap—like a splash of acrylic paint—can snowball into massive rework costs, quality control rejections, and production delays. Unlike common stains, acrylic paint chemically bonds to fibers as it dries, turning from water-soluble to water-resistant in a matter of minutes. This transformation is a nightmare for fabric processors managing hundreds of rolls per day. For factories dealing with natural and synthetic blends, removing acrylic paint isn’t just about stain removal—it’s about preserving fabric integrity, maintaining throughput, and avoiding profit loss. To remove acrylic paint from fabric in large-scale textile operations, factories typically use controlled applications of alkaline-based removers or glycol ethers before the paint fully cures. Timing, fabric type, and machine compatibility play critical roles in determining the best removal strategy.
Let’s break it down: imagine your QA team flags 80 yards of cotton-blend canvas with dried acrylic ink from a silkscreen misfire. Do you toss the batch and lose the day’s production value? Or do you deploy a specialized paint remover that can restore the fabric at 90% efficiency with no fiber damage? Understanding that decision point is what separates average textile factories from top-tier operations.
Let’s explore what really happens behind the scenes when paint meets production—and how to take back control.
What Makes Acrylic Paint Difficult to Remove from Fabric in Bulk Production?
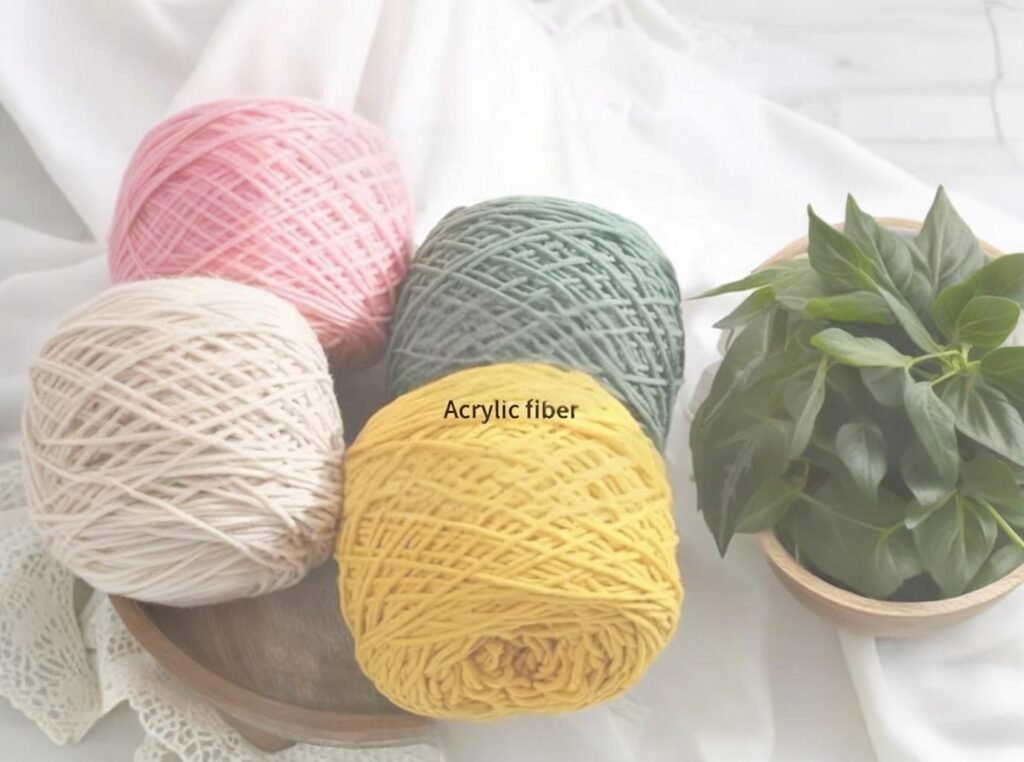
Acrylic paint becomes hard to remove in bulk fabric production because it forms a plastic-like film once dried, binding to textile fibers. In high-volume settings, this adhesion disrupts flow processes and increases labor, solvent use, and risk of fabric damage if not treated early.
1.1. The Chemistry of Acrylic Paint on Fabric
- Acrylic paint is composed of pigment, water, and acrylic polymer emulsions.
- As it dries, water evaporates and polymers cross-link, creating a permanent bond.
- Once cured, it’s no longer water-soluble—solvents like isopropyl alcohol, glycol ethers, or DMSO may be required to dissolve it.
Component | Behavior on Fabric | Removal Difficulty |
---|---|---|
Wet Acrylic Paint | Water-soluble | Easy (detergent, rinse) |
Semi-dried Paint | Partial polymerization | Medium (requires solvents) |
Fully Dried Paint | Cross-linked plastic film | High (specialized removers only) |
1.2. Why It’s Worse in High-Volume Operations
- Fabric rolls can exceed 1,000 meters per batch.
- Paint often transfers across folds, increasing affected surface area.
- Detection may be delayed until post-processing QC—when it’s already too late for easy removal.
1.3. Process Bottlenecks Introduced by Paint Contamination
- Manual inspection slows line efficiency.
- Solvent application introduces safety and ventilation challenges.
- Increased risk of dye migration or fiber breakdown during removal.
1.4. Industrial Case Study: Screen Printing Error in Vietnam (2023) A large factory producing promotional polyester t-shirts for export had a 7% paint contamination rate due to nozzle clogging in an automatic screen printer. With each shirt valued at $4 and a daily run of 10,000 units, the potential loss was $2,800/day. By implementing timed removal within the first 90 minutes using monoethanolamine-based cleaners, the plant reduced rejection rates to 1.2%.
1.5. Critical Thinking Angle: Should factories even attempt to remove dried paint at scale, or is it more cost-effective to repurpose the fabric for downgraded use (e.g., interlinings, insulation)? The answer depends on fabric cost, client expectations, and factory capabilities.
Which Types of Fabrics Are Most Affected by Acrylic Paint Stains?
Natural fibers like cotton and linen absorb acrylic paint deeply, making removal harder, while synthetic fibers like polyester resist absorption but allow surface bonding, which may be easier to strip with solvents in industrial cleaning setups.
2.1. Natural vs Synthetic Fiber Behavior
Fabric Type | Absorption Rate | Paint Removal Difficulty | Remarks |
---|---|---|---|
Cotton | High | High | Paint penetrates deeply |
Linen | High | High | Similar to cotton, stiff fiber |
Rayon | Medium | Medium | Semi-synthetic, variable behavior |
Polyester | Low | Medium–Low | Paint stays on surface |
Nylon | Low | Medium | Surface bonding + static attraction |
Acrylic Fabric | Moderate | Medium–High | Similar chemistry = high bonding |
2.2. Factors That Affect Paint Adhesion Beyond Fiber Type
- Fabric weave (tight vs loose)
- Surface treatments (pre-coating or water repellency)
- Moisture content at the time of contamination
2.3. Why Cotton-Blend Fabrics Are a Major Concern Cotton-poly blends are very common in textile production (especially in t-shirts, hoodies, and tote bags). But they pose a unique problem: the cotton portion absorbs paint, while the polyester may reject solvents. This duality makes uniform cleaning challenging.
2.4. Practical Test Data: Paint Penetration Depth by Fabric Type
Fabric Sample | Paint Penetration (μm) | Ease of Removal (1–5) |
---|---|---|
100% Cotton | 120 μm | 2 |
65/35 Cotton-Poly | 95 μm | 3 |
100% Polyester | 45 μm | 4 |
100% Nylon | 50 μm | 3 |
2.5. Alternative View: Could Hydrophobic Fabrics Prevent the Issue Entirely? While polyester and nylon repel water to some extent, many still get contaminated due to static buildup or low-viscosity paints. Surface modifications or post-treatment hydrophobic sprays may reduce paint retention.
2.6. Human-Centered Insight: Workers often rely on tactile detection rather than machine vision for paint flaws on textured or dyed fabric. This can delay response time by hours in large facilities, further complicating stain removal.
How Do Industrial-Scale Textile Factories Typically Remove Acrylic Paint?
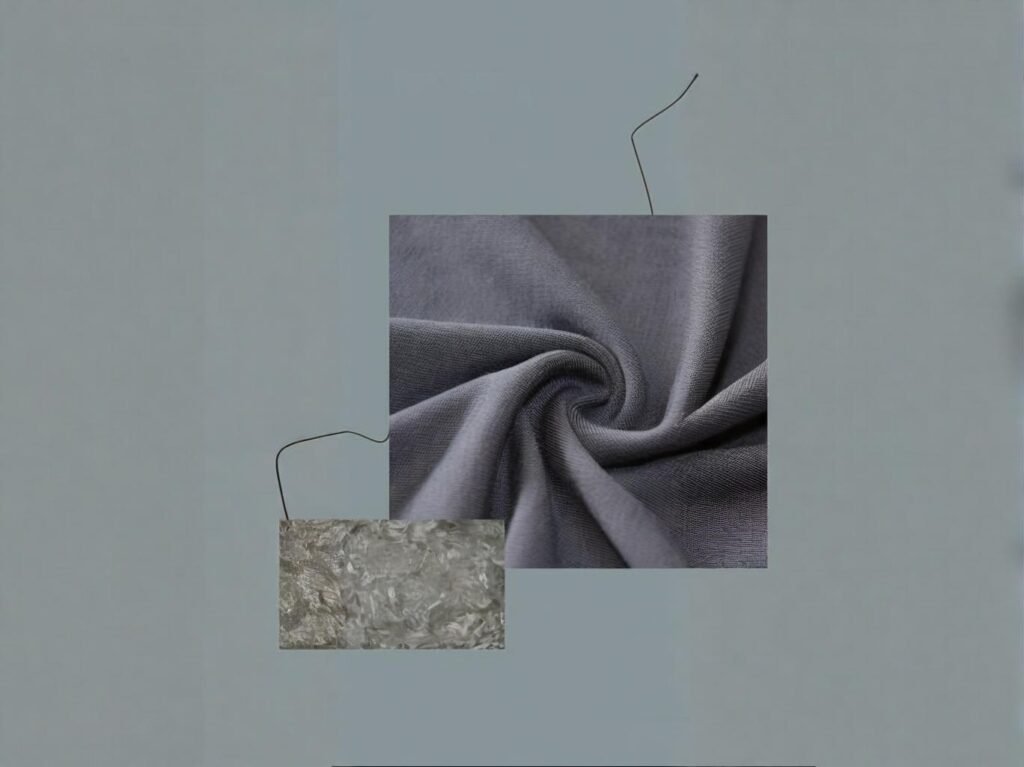
Large textile factories remove acrylic paint using automated solvent treatment lines, spot-cleaning stations, or enzyme-based softening agents depending on stain severity, fabric type, and stage of production. The goal is to minimize damage while preserving output speed.
3.1. Three Common Paint Removal Approaches in Large Textile Operations
- Inline Solvent Spray Systems: Used in continuous processing lines; employ solvents like glycol ethers or MEK with roller-assisted scrubbing to treat linear stains.
- Batch Soaking or Tumble-Wash Removal: Particularly for cut garments or smaller roll batches. Uses enzyme-boosted surfactants and warm water (50–60°C) for softening semi-dry paint.
- Manual Spot Cleaning Stations (With Ventilation Systems): Used for quality control corrections or small-volume stains on premium fabric. Operators use cotton swabs with acetone, isopropyl alcohol, or citrus terpenes.
3.2. Time Sensitivity of Removal Process
Stage of Paint | Suggested Removal Window | Preferred Method |
---|---|---|
Wet | 0–30 minutes | Water + detergent rinse |
Semi-dry | 30 min – 2 hours | Glycol ether application |
Dried | >2 hours | Solvent + mechanical assist |
3.3. Equipment Used in Large-Scale Paint Removal
Equipment Type | Function | Common in Industries |
---|---|---|
High-Pressure Rinse Units | Removes paint from flat fabric | Denim, canvas, bags |
Heated Soaking Tanks | Softens acrylic polymers | Fashion garments |
Roller-Scrub Stations | Applies solvents and agitation | Upholstery textiles |
UV Inspection Tables | Detects invisible dried paint | High-end production |
3.4. Real Factory Insight: India Cotton Processing Facility (2022) A woven fabric mill in Coimbatore installed a mid-line detection and treatment unit using ethylene glycol monoethyl ether sprayers. The result: 92% stain resolution on semi-dry paint at a cost of only $0.03 per meter vs. $0.28/meter reprint cost.
3.5. Multi-Angle Evaluation: Removal or Reweave?
- Removal: Low cost, risk of partial success, can alter finish.
- Reweave: High cost, labor-intensive, ensures consistent texture.
- Overlay/Print Over: Medium cost, design-dependent, saves production timeline.
What Chemicals and Solvents Are Safe for Large-Scale Fabric Cleaning?
Safe chemicals for removing acrylic paint from fabric at scale include glycol ethers, isopropyl alcohol, and low-VOC citrus-based solvents. The ideal choice balances paint softening power with fiber safety and ventilation requirements.
4.1. Chemical Solvent Classes Commonly Used
Solvent Type | Examples | Strength | VOC Level | Fiber Compatibility |
---|---|---|---|---|
Glycol Ethers | EGBE, DPM, PGME | Strong | Medium | Cotton, polyester |
Alcohol-Based | Isopropyl alcohol, ethanol | Medium | Low | Most fibers |
Citrus-Based Terpenes | D-limonene | Mild | Low | Delicate fabrics |
Ketones | Acetone, MEK | Very Strong | High | Nylon, acrylic, but not delicate fibers |
Amines/Alkalines | Monoethanolamine (MEA) | Strong | Medium | Heavy-duty only |
4.2. Safety and Compliance Factors for B2B Buyers
- Ventilation & PPE Needs: Solvents like MEK require fume hoods and gloves.
- Environmental Regulations: Many regions (e.g., EU, California) limit high-VOC removers.
- Certification Requirements: For OEKO-TEX® or GOTS compliance, only certain solvents are allowed during stain remediation.
4.3. Eco-Friendly or Low-VOC Alternatives
Solvent | Source | VOC Compliance | Reusability | Notes |
---|---|---|---|---|
d-Limonene | Citrus peels | Yes | Limited | Biodegradable, pleasant odor |
Bio-Alcohol Blends | Corn-based | Yes | Yes | Lower flash point |
Enzyme-Based Softeners | Plant-derived | Yes | Yes | Slower but gentler process |
4.4. Cost Comparison Table
Chemical Type | Approx. Cost per Liter | Removal Efficiency (%) | Handling Cost (Est.) |
---|---|---|---|
Glycol Ether Blend | $3.20 | 85–92 | Medium |
Isopropyl Alcohol | $1.80 | 65–75 | Low |
MEK (Ketone) | $4.50 | 95+ | High |
d-Limonene | $5.00 | 60–70 | Low–Medium |
4.5. Industry Case: Polyester Curtains Factory in Turkey After switching from MEK to PGME for environmental compliance, a Turkish home textile plant reduced regulatory fines and improved indoor air quality without losing stain removal performance (88% retention rate).
4.6. Human Angle: Line workers prefer low-odor and low-skin-irritation solvents—even if removal takes longer—because daily exposure compounds over time. Some factories rotate chemicals by shift to reduce exposure fatigue.
How Can Heat and Drying Processes Affect Paint Removal in Production Lines?
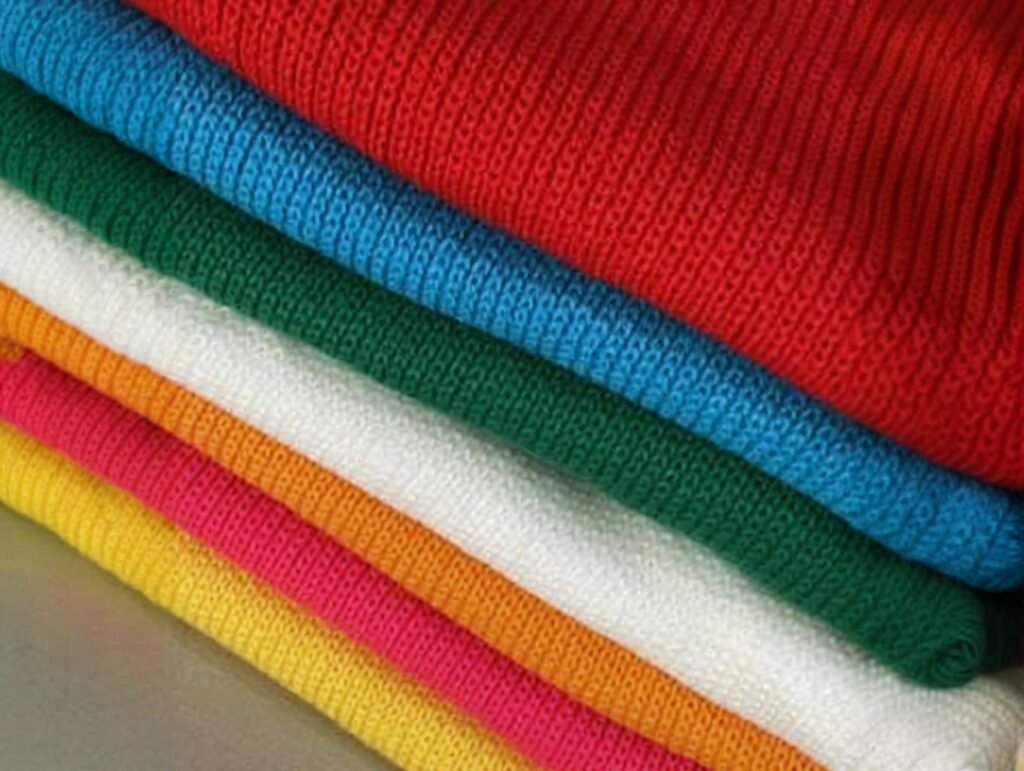
Heat accelerates the curing of acrylic paint, making removal significantly harder. In textile production, exposure to drying ovens or IR heat sets the paint into a plastic-like layer that requires stronger solvents and more aggressive mechanical treatment.
5.1. What Happens When Acrylic Paint Is Heated on Fabric?
- The acrylic polymers undergo thermosetting, locking in their structure.
- Once set, the paint resists not only water but also many industrial detergents.
- The bond becomes mechanical (within fibers) and chemical (cross-linked).
5.2. Key Production Stages Where Heat Exposure Occurs
- Infrared Dryers: Used in screen or roller printing processes.
- Hot Air Ovens: Common in calendaring and heat-setting.
- Steaming Chambers: Though mostly for dye fixation, can affect paint.
Process Type | Typical Temp (°C) | Time (min) | Paint Curing Risk |
---|---|---|---|
IR Flash Drying | 150–170 | 1–3 | Very High |
Hot Air Tumble Dry | 120–140 | 5–20 | High |
Conveyor Oven | 160–180 | 1–2 | Extreme |
5.3. Real-Life Example: Denim Factory in Mexico (2021) A denim mill with inline pigment printing mistakenly dried 20,000 meters of fabric before inspection. Post-drying stain removal dropped to <20% efficiency—even with methyl ethyl ketone—leading to $18,000 in scrap material loss. They later added a pre-dry inspection light tunnel to catch stains earlier.
5.4. Is Heat Always the Enemy? Situational Perspective
- If paint is still wet, heat should be avoided.
- If paint is fully dry and removal isn’t viable, heat re-softening + scraping can help, but only under precise conditions using heat guns and layered removal stations.
5.5. Predictive Maintenance Tip for Factories Install thermal cameras before drying stages to detect abnormal paint hotspots. Combined with AI object recognition, this can alert QC teams before it’s too late.
Is It Better to Treat Acrylic Paint Stains Before or After Curing?
It is far more effective to treat acrylic paint stains before they fully cure. Early-stage intervention using water or mild solvents within 30–90 minutes of staining increases removal success by up to 90%, versus below 40% after full curing.
6.1. Fabric Response Based on Paint Curing Stage
Paint Condition | Treatment Window | Ideal Approach | Success Rate |
---|---|---|---|
Wet (0–30 min) | Immediate | Rinse with water + detergent | 95%+ |
Semi-dry (30–90 min) | Short-term | Solvent + gentle brushing | 70–85% |
Fully dry (>2 hrs) | Late-stage | Strong solvent + abrasion | <40% |
6.2. Operational Flowchart: Paint Removal Decision Tree
↓ Paint Detected on Fabric
→ Is the Paint Wet?
→ Yes → Rinse + Wash → Done
→ No → Is it Semi-dry?
→ Yes → Solvent + Spot Scrub
→ No → Heat Re-soften or Scrap Evaluation
6.3. Why Factories Delay Treatment (And Why It Hurts)
- Production prioritization: Focus is often on output, not inspection.
- Late-stage QC: Paint often goes unnoticed until packing or shipment checks.
- Workforce training gaps: Operators may not be empowered to stop lines.
6.4. Factory SOP Insight: Pakistan Knitwear Manufacturer By establishing a 3-zone inspection system (entry, mid, final), this knitwear exporter reduced post-curing paint stain rejections by 78%. They also included real-time WhatsApp alerts for any detected stains before drying.
6.5. Strategic Recommendation: SOP Integration
- Zone 1 (Greige Inspection): Pre-processing visual screening.
- Zone 2 (Post-Print, Pre-Heat): Use UV-enhanced tables to check for residue.
- Zone 3 (Post-Drying): Only final confirmation—not primary detection.
6.6. Empathy Insight: Worker Hesitation Operators may fear halting production over a stain. Giving them authority to flag issues and offering incentives for early detection can significantly improve outcomes.
Are There Eco-Friendly Solutions for Removing Acrylic Paint at Scale?
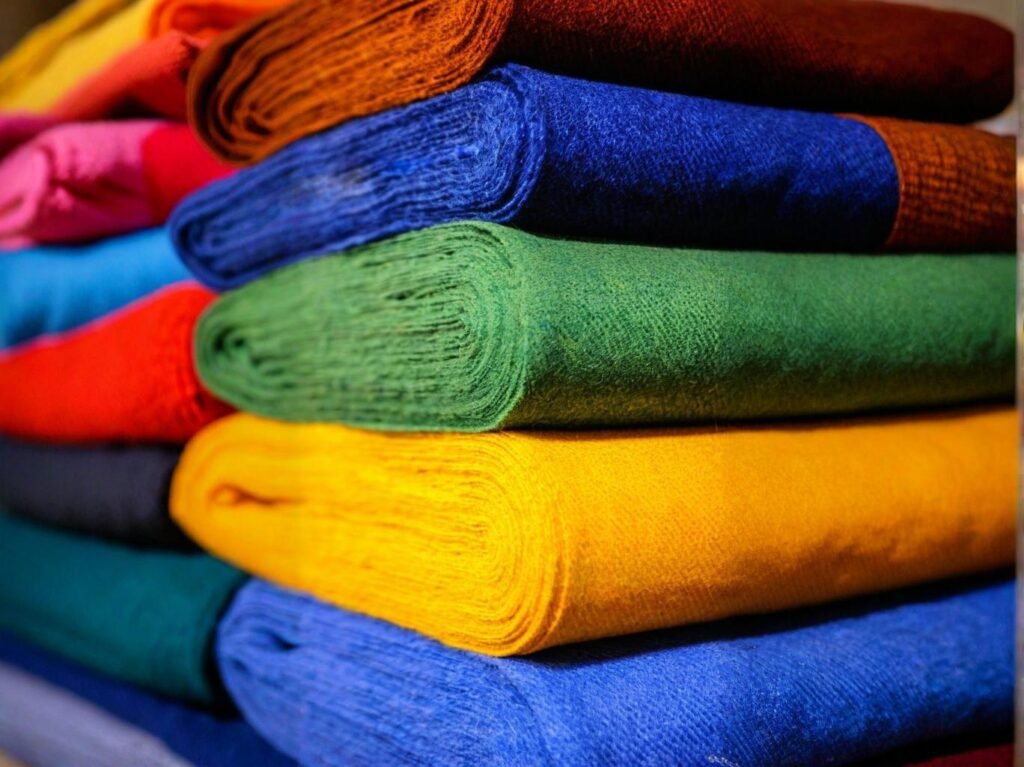
Yes, eco-friendly solutions such as citrus-based solvents, enzyme cleaners, and biodegradable alcohol blends can remove acrylic paint while meeting sustainability standards. These alternatives reduce VOC emissions, protect worker health, and comply with certifications like OEKO-TEX® and GOTS.
7.1. What Defines an “Eco-Friendly” Paint Removal Solution?
- Biodegradability: Breaks down naturally without harming ecosystems.
- Low VOC Emissions: Compliant with regional air quality laws.
- Safe Handling: Reduced skin and respiratory hazards.
- Certifiability: Meets textile eco-label requirements.
7.2. Top Sustainable Solvent Alternatives
Eco-Solvent Name | Source | Effective On | Certifications | VOC Emission |
---|---|---|---|---|
d-Limonene | Citrus peels | Light–medium stains | USDA Biobased, REACH | Low |
Bio-Alcohol Blends | Corn/sugarcane | Surface stains | OEKO-TEX®, GOTS | Very Low |
Enzyme-based Softeners | Plant proteins | Delicate fabrics | Bluesign®, GRS | None |
Sodium Citrate & Vinegar Mix | Natural acids | Pre-cured stains | None (DIY use) | None |
7.3. Factory Case Study: German Organic Bedding Manufacturer A GOTS-certified factory in Hamburg switched from petroleum-based stain removers to a proprietary d-limonene solution. While stain removal efficiency dropped from 92% to 76%, it allowed them to retain their certification and opened new European retail partnerships.
7.4. Trade-Offs and Limitations
- Cost: Bio-solvents are often 1.5–2x more expensive than traditional chemicals.
- Time: Reaction time is slower; some need 30–60 minutes to activate.
- Stain Severity: May not work well on deeply cured or thickly layered paint.
7.5. Sustainability Scorecard Example
Removal Method | Eco Impact | Cost | Effectiveness | Scalability |
---|---|---|---|---|
Glycol Ether Solvent | ✗ | $$ | ★★★★★ | ★★★★☆ |
d-Limonene Solution | ✓✓ | $$$ | ★★★☆☆ | ★★★☆☆ |
Enzyme Cleaner | ✓✓✓ | $$$$ | ★★☆☆☆ | ★★☆☆☆ |
Manual Vinegar/Water | ✓✓ | $ | ★☆☆☆☆ | ★☆☆☆☆ |
7.6. Future Outlook: Green Chemistry Partnerships Startups are emerging that blend green chemistry and nanotech to create hybrid cleaning agents for textiles. B2B buyers may soon see private-label bio-removers with high efficacy and low toxicity as standard offerings.
How to Set Up a Standard Operating Procedure (SOP) for Paint Removal in Fabric Manufacturing?
To build a textile factory SOP for acrylic paint removal, define inspection checkpoints, chemical usage guidelines, staff responsibilities, and safety protocols. Ensure documentation aligns with production stages and includes pre-cure and post-cure decision-making trees.
8.1. Key Components of an Effective SOP
- Inspection Workflow: When and how fabric should be checked.
- Stain Categorization: Wet, semi-dry, and cured classification.
- Removal Methodology: Match stain type with safe, effective cleaning method.
- Chemical Handling Rules: Safety, dilution ratios, storage.
- Escalation Protocols: When to involve supervisors or QC heads.
8.2. SOP Template Example
Step | Action | Responsible Dept | Timeframe |
---|---|---|---|
1 | Visual inspection post-printing | Line Operator | <10 minutes |
2 | Identify paint condition | QA | Immediate |
3 | Apply correct remover from SOP chart | Stain Tech | <30 minutes |
4 | Re-inspect & log results | QA | Post-treatment |
5 | Flag unresolved fabric for rework/scrap | Supervisor | Same shift |
8.3. Role-Specific Responsibilities
Role | Core SOP Responsibilities |
---|---|
Line Operators | First point of visual detection and reporting |
QC Inspectors | Classify paint type, approve remediation plan |
Safety Officer | Verify chemical use complies with MSDS and PPE protocols |
Floor Managers | Authorize rework, scrap, or return-to-process decisions |
8.4. Training and SOP Reinforcement
- Hold quarterly workshops with stain testing simulations.
- Display SOP flowcharts at strategic locations on factory floors.
- Use incentive systems for early detection and successful removal logging.
8.5. Digital SOP Integration with ERP Systems Factories using ERP software like SAP, Odoo, or Netsuite can link SOP checkpoints to barcode scans. When paint is detected, the system pulls the correct SOP module and tracks chemical usage in real time—supporting traceability and compliance.
8.6. Global Benchmarking: China vs. Italy vs. Bangladesh
Country | SOP Digitalization | Common Removal Method | SOP Compliance Rate |
---|---|---|---|
China | Medium | Solvent + rinse | 82% |
Italy | High | Spot-clean + enzyme-based | 91% |
Bangladesh | Low | Manual cleaning | 67% |
8.7. Critical Thinking: Customize or Standardize? One-size SOPs often fail in multi-fiber environments. Hybrid SOPs based on customer orders, fabric type, and machine capability can maximize flexibility while maintaining compliance.
Removing acrylic paint from fabric in large-scale textile operations is a complex, multi-variable challenge. Timing, fabric composition, chemistry, equipment, and human judgment all play vital roles. Whether you’re running an industrial garment facility or a specialized home textile plant, the cost of ignoring proper paint removal SOPs can be staggering—from lost inventory to missed shipment deadlines and reputation risk.
At SzoneierFabrics, we specialize in developing custom fabric solutions and production processes that account for every detail—from pre-treatment to post-processing stain control. We help you build SOPs that work in your factory environment with your specific fabrics.
Get in touch with SzoneierFabrics today
for free samples, low MOQ customization, expert R&D support, and fast global delivery. Let us help you produce fabrics that are not only premium but protected at every step. Contact us now to request a custom quotation!