In the ever-evolving automotive landscape, materials matter more than ever. From dashboards to tail lights, the choice of polymer can affect not only aesthetics but performance, safety, and long-term cost. Among these materials, acrylic has carved out a unique niche for itself. Thanks to its transparency, UV resistance, and rigidity, it’s used in everything from lighting lenses to trim panels and display casings.
So, what is acrylic used for in the automotive industry? Acrylic is used to manufacture a wide range of components in modern vehicles—including headlamp covers, interior display panels, instrument clusters, rear lighting assemblies, and trim parts—thanks to its high optical clarity, thermal resistance, scratch resistance, and design flexibility. It is especially favored in premium vehicle models where aesthetics and long-term performance are critical.
One compelling example comes from the electric vehicle (EV) space. A leading German EV maker switched from glass to acrylic PMMA panels in their HMI display screens. The result? A 22% reduction in dashboard weight and a 15% increase in impact resistance without compromising clarity or capacitive touch functionality. This single shift helped the automaker increase range and improve safety.
Let’s break down exactly how—and why—acrylic is revolutionizing automotive components.
What Types of Acrylic Materials Are Commonly Used in Automotive Manufacturing?
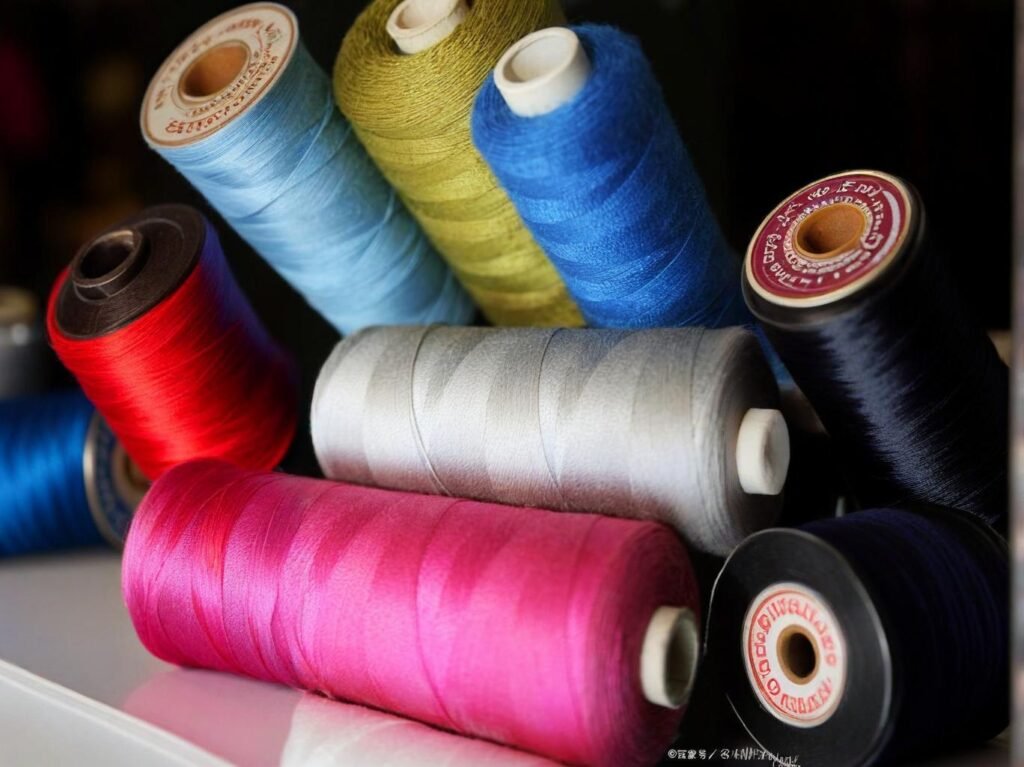
Automotive manufacturing primarily uses polymethyl methacrylate (PMMA), cast acrylic sheets, and impact-modified acrylic blends to create lightweight, transparent, and durable parts for both interior and exterior use. These formulations vary in optical performance, impact resistance, and thermal stability.
a) Overview Table: Acrylic Types Used in Automotive Manufacturing
Acrylic Type | Key Features | Common Automotive Uses |
---|---|---|
PMMA (Polymethyl Methacrylate) | High transparency, UV-resistant | Lighting lenses, windows, HUD display covers |
Impact-Modified Acrylic | Enhanced toughness with rubber modifiers | Bumper trim, bezels, interior protective covers |
Cast Acrylic | Superior optical clarity, easy to fabricate | Infotainment panels, instrument cluster lenses |
Acrylic Copolymers | Better flow and heat resistance | Injection-molded interior components |
b) Industry Example: Japan’s Automotive Plastics Market
A 2023 industry study by Fuji Keizai showed that PMMA demand in Japanese automotive production grew by 12.5% year-over-year, especially in EV dashboard casings and transparent body components. Toyota and Honda are actively sourcing enhanced acrylic blends to meet both safety and aesthetic goals.
c) Performance and Processing Advantages
- Low shrinkage rate during molding—ideal for complex interior parts
- Excellent UV and chemical resistance—important for exposed surfaces
- Compatible with laser engraving and edge lighting—used in ambient lighting systems
d) Critical Perspective: Why Not Polycarbonate Instead?
- While polycarbonate is more impact-resistant, it requires hard coating to match acrylic’s scratch resistance.
- Acrylic retains optical clarity longer under sunlight, making it better for headlamp and rear-light applications.
How Is Acrylic Applied in Automotive Interior Components?
In automotive interiors, acrylic is used for display covers, instrument panels, ambient lighting components, and decorative trim due to its clarity, touch sensitivity compatibility, and premium feel. It offers OEMs a balance between aesthetics and performance, especially in digitally integrated cabins.
a) Interior Applications Table
Component | Function | Why Acrylic Is Used |
---|---|---|
Infotainment Display Covers | Protection & touchscreen clarity | Optical-grade PMMA resists scratches and glare |
Instrument Cluster Lenses | Protect gauge visuals | Maintains clarity and resists fogging |
Ambient Light Panels | Distribute soft LED lighting in doors and dashboards | Acrylic enables even light diffusion with minimal weight |
Trim Inserts & Logo Backlights | Design accents | Easily laser cut and edge-lit |
Control Panel Covers | Decorative functional components | Durable under frequent use |
b) Real-World Case: Volkswagen’s Digital Cockpit
VW’s next-gen Golf lineup integrates cast acrylic display panels with capacitive touch sensors. The acrylic not only supports fine haptic feedback but reduces panel thickness by 30% compared to glass, allowing for sleeker dashboard integration.
c) Acrylic vs. Glass in HMI Screens
- Acrylic is less brittle, reducing risk of cracking in impact events.
- Allows edge polishing for seamless integration into trim.
- Supports IR touch technology, increasingly used in modern infotainment systems.
d) Critical Thinking: Is Acrylic Too “Plastic” for Luxury Brands?
Not necessarily. Premium brands like BMW and Mercedes-Benz now use UV-cured acrylic sheets with anti-smudge coating, giving them a glass-like surface without the fragility. When done right, acrylic can actually enhance a luxury cabin’s futuristic look.
What Are the Advantages of Using Acrylic in Vehicle Exterior Parts?
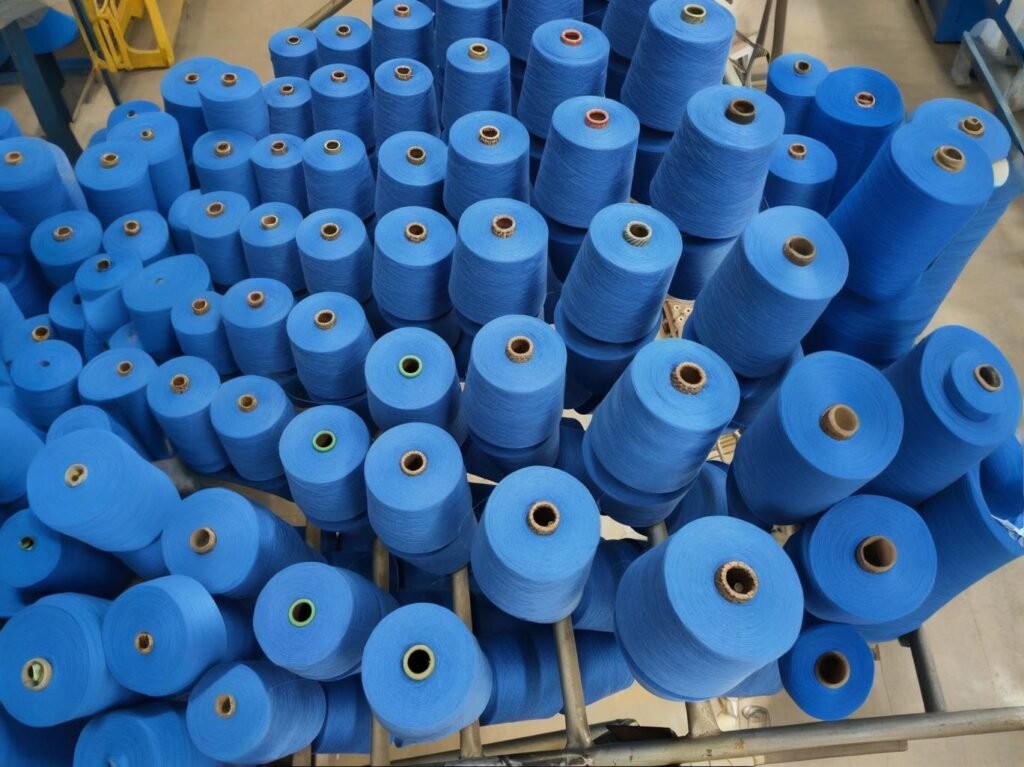
Acrylic offers significant advantages for exterior automotive parts due to its UV resistance, weatherability, lightweight structure, and visual clarity. This makes it ideal for components like rearview mirror housings, decorative trims, and window visors where aesthetics and durability intersect.
a) Benefits of Acrylic in Exterior Parts
Feature | Advantage for Automotive Use |
---|---|
UV Stability | Resists yellowing and degradation under sunlight |
Lightweight | Reduces vehicle weight, improves fuel efficiency |
Moldability | Enables complex designs with tight tolerances |
Surface Finish Flexibility | Supports gloss, matte, frosted, and colored finishes |
Weather Resistance | Withstands rain, snow, heat, and road debris over time |
b) Real-World Example: Hyundai Decorative Trims
Hyundai Motor Company has adopted impact-modified acrylics for door mirror caps and pillar trims in several SUV models. This resulted in a 9% part weight reduction and a longer gloss retention under desert UV testing conditions compared to previously used ABS plastic.
c) Exterior Components Commonly Using Acrylic
Exterior Component | Acrylic Role |
---|---|
Rearview Mirror Housings | Provides lightweight gloss or color-matched finish |
Door Pillar Garnishes | Adds contrast and durability to design lines |
Side Visors | Clarity and curvature for aerodynamics and visibility |
Emblems & Badging | Molded 3D lettering with transparent acrylic overlays |
Roof Spoiler Light Covers | Lightweight and UV-stable lens material |
d) Critical Insight: Acrylic vs. ABS or Polypropylene
- ABS offers toughness but can discolor in UV over time.
- Polypropylene is cheaper but lacks clarity or fine surface detail.
- Acrylic strikes a balance—especially when co-extruded with ASA for impact/weather resistance and gloss retention.
Which Automotive Lighting Components Are Made from Acrylic?
Acrylic is a preferred material for automotive lighting due to its exceptional light transmittance (up to 92%), formability, and UV aging resistance, making it ideal for headlamps, tail lamps, turn indicators, and ambient light guides.
a) Lighting Components That Use Acrylic
Lighting Component | Why Acrylic Is Ideal |
---|---|
Headlamp Outer Lens | High clarity, UV resistance, and lightweight |
Tail Lamp Lenses | Formable into bold shapes, available in tinted variants |
Turn Signals | Easy to mold with amber color and directional focus |
DRL (Daytime Running Lights) | Allows even diffusion of LED lighting |
Ambient Light Guides | Edge-lit acrylic panels distribute soft interior lighting |
b) Case Study: Tesla Model Y Headlamps
Tesla uses optical-grade cast PMMA for its headlamp lenses in the Model Y. Compared to polycarbonate (used in earlier models), PMMA provided better clarity with a 30% improvement in light diffusion accuracy and reduced lens fogging under thermal cycling tests.
c) Performance Characteristics of Acrylic in Lighting
Performance Metric | Acrylic Score | Polycarbonate Comparison |
---|---|---|
Light Transmittance | 92% | 88–90% |
UV Resistance | Excellent (does not yellow) | Requires coating to match |
Scratch Resistance | High | Lower without hard coating |
Dimensional Stability | Good | Better under high impact |
d) Emerging Trends in Automotive Lighting
- 3D LED signatures are molded into acrylic light pipes.
- Laser-etched acrylic panels now enhance rear lighting branding.
- Some OEMs use multi-layer acrylic lenses with texture gradients for futuristic designs.
How Does Acrylic Compare to Polycarbonate and Glass in Automotive Applications?
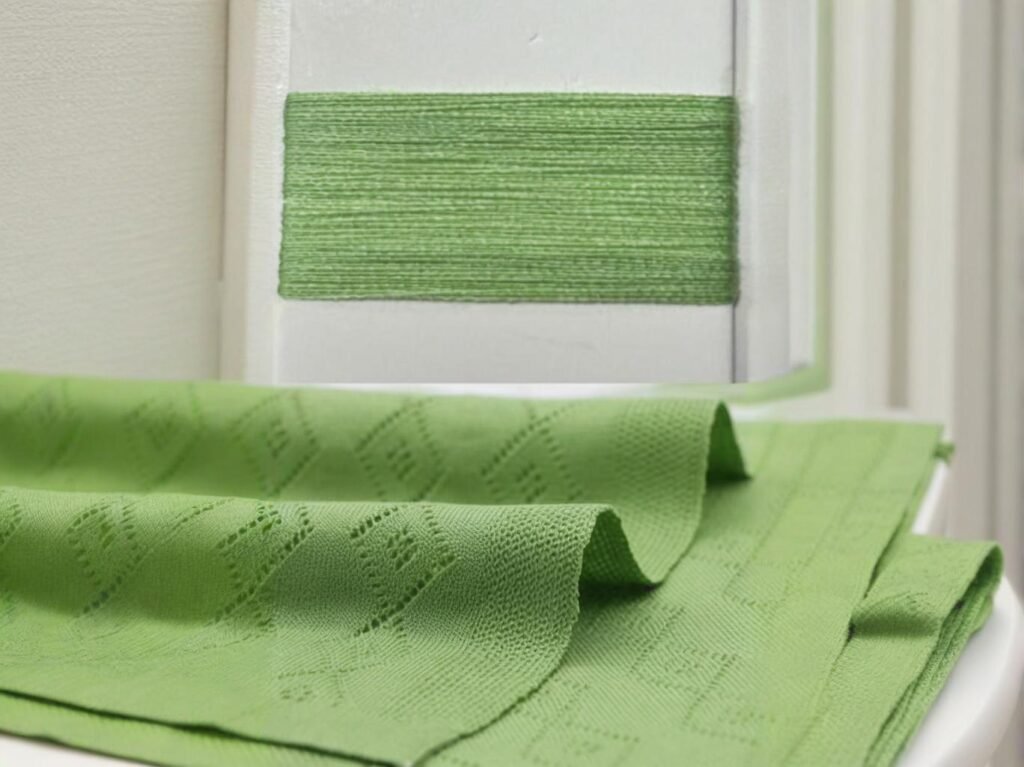
Acrylic offers superior optical clarity and UV resistance compared to polycarbonate and is significantly lighter and safer than glass, making it ideal for aesthetic and functional vehicle components. However, it trails polycarbonate in terms of impact resistance.
a) Material Comparison Table: Acrylic vs. Polycarbonate vs. Glass
Property | Acrylic (PMMA) | Polycarbonate (PC) | Glass |
---|---|---|---|
Optical Clarity | Excellent (92%) | Good (88–90%) | Excellent (91–92%) |
UV Resistance | Excellent | Poor (needs coating) | Good |
Impact Resistance | Moderate | Very High (up to 250x glass) | Low |
Scratch Resistance | High | Low (without coating) | Very High |
Weight | Light (1.19 g/cm³) | Light (1.20 g/cm³) | Heavy (2.5 g/cm³) |
Moldability | Excellent | Excellent | Poor |
Cost | Moderate | High | Variable |
b) When to Choose Acrylic:
- Display panels, ambient lighting, and trim parts where clarity and surface finish matter.
- Tail lamps and DRLs, where diffused LED light needs to pass through precisely.
- Weight-sensitive EV applications, where reducing panel mass is a priority.
c) When to Choose Polycarbonate:
- Impact zones, like fog lamp protectors and rugged bumpers.
- Safety shields in motorsports or high-speed environments.
d) When to Choose Glass:
- Windshields (mandated by law), due to scratch resistance and rigidity.
- Areas requiring superior sound insulation or anti-fog laminated properties.
e) Case Comparison: BMW Headlamp Evolution
- Pre-2010: BMW used glass lenses (heavy and brittle).
- 2010–2018: Switched to polycarbonate with anti-fog coating.
- 2019 onward: Premium models adopted cast acrylic with nano-coatings, improving aesthetics, reducing scratches, and optimizing LED visibility.
Is Acrylic Durable Enough for High-Temperature and UV-Exposed Automotive Environments?
Yes, automotive-grade acrylic is highly durable under UV exposure and moderately resistant to high temperatures, especially when stabilized with additives or used in blended copolymers. However, its temperature ceiling (\~85–100°C) limits its use in under-the-hood applications.
a) Environmental Durability Summary Table
Stress Condition | Acrylic Performance | Notes |
---|---|---|
UV Exposure | Excellent (5–10 years with no yellowing) | Solution-dyed and UV-stabilized variants available |
Temperature Resistance | Up to 85–100°C | Suitable for interiors and lighting applications |
Humidity & Rain | Very good (non-hygroscopic) | Won’t swell or absorb moisture |
Thermal Cycling | Good (low expansion coefficient) | Avoids panel cracking in dashboard assemblies |
Chemical Resistance | Moderate | Resists many automotive cleaners but not solvents |
b) Test Case: Outdoor Mirror Acrylic Covers in Arizona
An OEM conducted a 12-month UV exposure test in the Arizona desert:
- Acrylic panels retained 93% gloss level and showed zero discoloration.
- Polycarbonate versions exhibited yellowing after 6 months despite coating.
c) How to Improve Heat Tolerance
- Use impact-modified acrylic blends with better thermal properties.
- Apply IR-reflective surface coatings to reduce direct solar heat load.
- Opt for thicker sections in exposed components to slow thermal distortion.
d) Critical Limitations
- Not suitable for engine bay components or exhaust covers.
- Deformation risk at continuous temperatures above 90°C.
What Are the Regulatory and Safety Standards for Acrylic Use in Automotive Design?
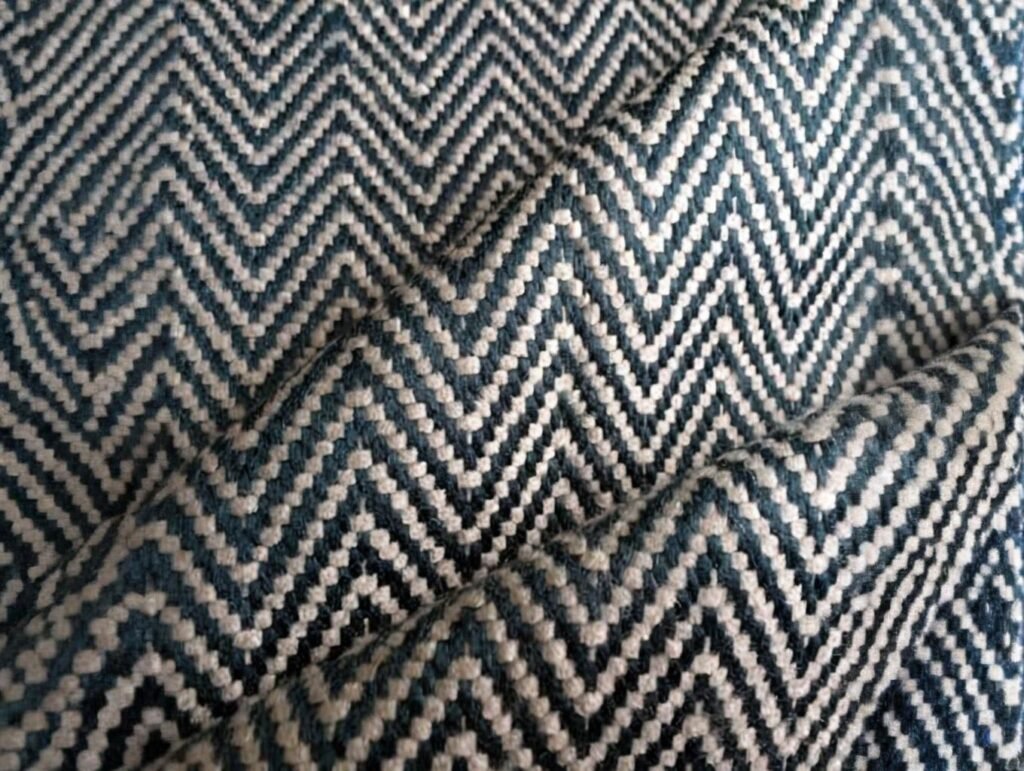
Automotive-grade acrylic must comply with global safety and environmental standards, including FMVSS, ECE regulations, ISO/ASTM mechanical benchmarks, and increasingly, REACH and RoHS directives for material safety. These standards ensure that acrylic parts meet performance, durability, and toxicity thresholds.
a) Major Regulatory Standards for Acrylic in Automotive Use
Standard/Directive | Jurisdiction | What It Covers |
---|---|---|
FMVSS 108 | United States | Specifies photometric and mechanical standards for lighting |
ECE R48, R112 | Europe | Covers lighting materials and optical clarity |
ISO 178 / ISO 527 | Global | Acrylic mechanical strength and elongation properties |
ASTM D4802 / D638 | USA | Defines acrylic sheet specifications and tensile properties |
RoHS (EU Directive 2011/65) | Europe | Restricts hazardous substances in polymer components |
REACH | Europe | Ensures acrylic chemical content is safe for human contact |
b) Certification Examples
- REACH-certified acrylic sheets ensure absence of SVHC (Substances of Very High Concern).
- RoHS compliance is often mandatory for electrical system displays and LED covers.
c) Safety Considerations for Lighting Components
- Acrylic must maintain photometric performance under UV exposure and thermal stress.
- Diffusion panels in DRLs are tested for glare, impact resistance, and heat deformation.
d) OEM Case Study: Volvo’s Material Compliance Strategy
Volvo requires third-party lab validation for all plastics used in its interiors, including:
- Flammability (FMVSS 302)
- UV stability (ASTM G154)
- Fogging resistance (DIN 75201)
They switched to a UV-stabilized acrylic blend in 2022 for trim panels to meet stricter sustainability and optical standards.
How Can OEMs and Tier 1 Suppliers Source High-Quality Automotive Grade Acrylic?
Sourcing high-grade acrylic for automotive applications requires evaluating resin purity, fabrication technique (cast vs extruded), supplier certifications, and the ability to customize formulations for impact, UV, or optical needs.
a) Sourcing Checklist for B2B Buyers
Criteria | Why It Matters |
---|---|
Resin Purity (Virgin PMMA) | Ensures consistency and performance in production |
Cast vs. Extruded Acrylic | Cast provides higher clarity, extruded suits budget parts |
UV/IR Stabilization Additives | Protects against sunlight and thermal damage |
RoHS / REACH / ISO Certifications | Required for export and OEM compliance |
Customization Services | Blending, color matching, surface treatments available |
MOQ & Sampling Capabilities | Important for development or limited-edition model testing |
Automotive-Grade Documentation | MSDS, COA, tensile, optical, and fogging reports |
b) Global Sourcing Hotspots
Country | Known For |
---|---|
China | Large-scale OEM supply, affordable pricing |
Germany | Precision optical acrylic and R\&D coatings |
Japan | High-quality impact-modified PMMA blends |
USA | Certified lighting-grade acrylic producers |
c) Case Study: EV Startup Scaling with Acrylic
A U.S.-based EV startup used SzoneierFabrics’ automotive acrylic for rear light guides and interior ambient lighting panels. The factory:
- Delivered custom-blended PMMA with built-in UV resistance.
- Provided free samples and rapid prototyping within 10 days.
- Met ISO 9001 and RoHS certification for global export readiness.
Work with a Trusted Acrylic Supplier
At SzoneierFabrics, we specialize in manufacturing and customizing acrylic materials tailored for automotive needs. Whether you’re sourcing light guide panels, display-grade covers, or UV-resistant trims, we offer:
- ✅ 100% Quality Guarantee
- ✅ Free Design Services and Samples
- ✅ Low MOQ Custom Orders
- ✅ Short Lead Time and Global Shipping
- ✅ ISO, RoHS, REACH Certified Options
Looking to upgrade your automotive parts with high-performance acrylic? Contact our team today for a free sample or custom quote.