In industries where materials are pushed to their limits—blistering UV exposure, sub-zero temperatures, harsh chemicals—selecting the right plastic can make or break a product’s success. Whether it’s used in outdoor signage, marine windows, factory light covers, or protective panels, acrylic is often the go-to material for manufacturers who need clarity and strength under pressure.
So, how durable is acrylic material in harsh environments? Acrylic (PMMA) is highly durable in UV, rain, and cold exposure, with excellent optical clarity and color retention over years of outdoor use. While it’s not as impact-resistant as polycarbonate, its resistance to yellowing, warping, and chemical corrosion makes it ideal for long-term deployment in extreme industrial or environmental conditions.
Take, for instance, the 2022 case of a Middle Eastern oil refinery that replaced its steel-framed polycarbonate covers with UV-stabilized acrylic shields. After just 18 months, the polycarbonate had yellowed and cracked, while the acrylic panels remained intact, clear, and functional—despite daily exposure to 45°C heat, sand, and oil mist.
Let’s explore exactly what makes acrylic a smart choice for harsh environments—and where it may (or may not) hold up under pressure.
What Factors Affect the Durability of Acrylic in Harsh Conditions?
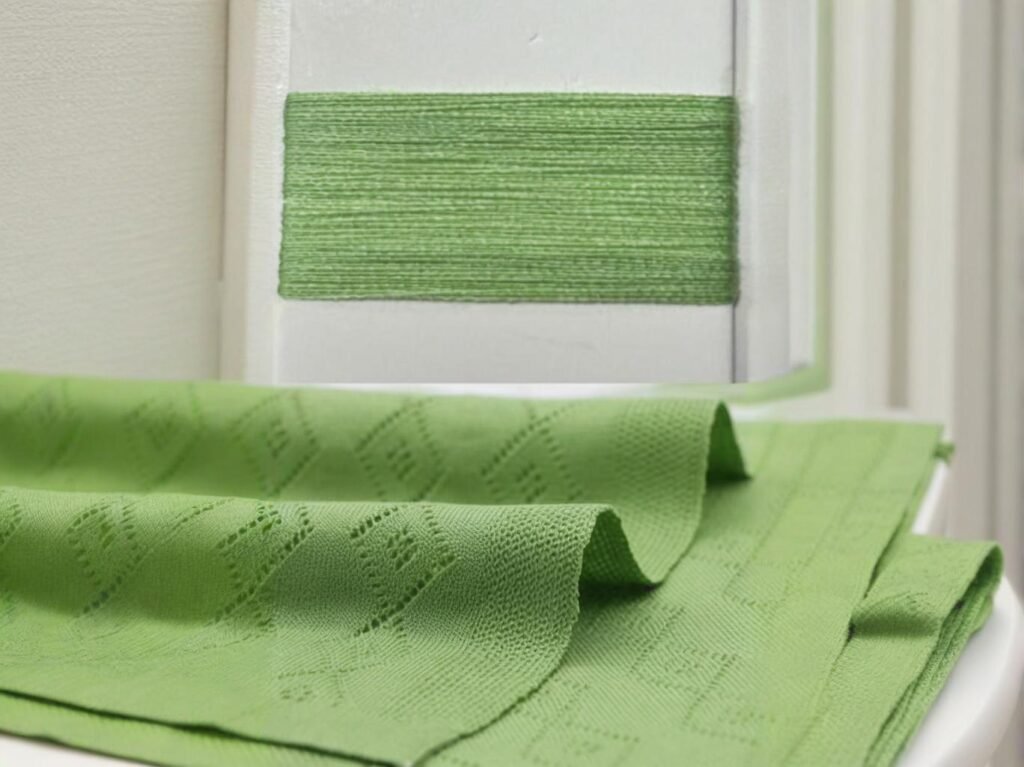
The durability of acrylic material depends on exposure to UV radiation, temperature fluctuations, mechanical load, chemical interaction, and the specific grade or additives used during manufacturing. Its longevity improves significantly when UV inhibitors, impact modifiers, and surface coatings are applied.
a) Primary Stress Factors and Their Effects
Environmental Factor | Potential Impact on Acrylic | Notes |
---|---|---|
UV Radiation | Yellowing, brittleness over time | Can be mitigated with UV stabilizers |
High Temperature | Softening or warping above 85–100°C | Thermal limit depends on formulation |
Cold Temperature | Maintains rigidity but may become brittle | Can handle down to –40°C in outdoor applications |
Moisture/Humidity | No swelling or hydrolysis | Good dimensional stability |
Abrasion/Impact | Surface scratches, risk of cracking | Surface coatings and thicker gauges help |
Chemical Exposure | Cracking or stress whitening with solvents | Resistant to weak acids and cleaning agents |
b) Formulation Matters
- Impact-modified acrylic increases resistance to physical force.
- Weatherable acrylic includes UV and heat stabilizers.
- Co-extruded acrylic layers combine clarity with strength (used in outdoor signs).
c) Real-World Use: Telecom Antennas in Canada
A telecom provider installed PMMA enclosures for rural 5G antennas. These enclosures:
- Withstood –35°C winters and 38°C summers without cracking.
- Maintained transparency for signal reception.
- Required no replacement after 3+ years, reducing maintenance costs by 28%.
d) Critical Insight
Durability is not just about the base resin—it’s about using the right grade for the environment. A signage-grade extruded sheet used on an offshore rig will fail. A marine-grade cast acrylic panel will thrive.
How Does Acrylic Perform Under UV, Heat, and Cold Stress?
Acrylic exhibits excellent UV resistance, retains its properties at sub-zero temperatures, and performs reliably up to 85–100°C. Unlike many plastics, it resists discoloration and distortion when exposed to prolonged sunlight, making it a top choice for outdoor and climate-variable installations.
a) Thermal and UV Performance Table
Stress Condition | Performance Summary | Recommended Grade |
---|---|---|
Prolonged Sunlight | No yellowing for 5–10 years with UV additives | Cast or UV-stabilized PMMA |
Continuous Heat (85°C) | Holds shape and clarity | Weather-resistant PMMA |
Short-Term Heat (up to 100°C) | Some softening may occur | Use thicker or coated grades |
Cold Temperatures (–40°C) | Remains clear, no cracking | All industrial grades |
b) Case Example: Dubai Outdoor Kiosks
A commercial display vendor replaced tempered glass with UV-resistant acrylic for touchscreen kiosks in Dubai malls and outdoor walkways. After 24 months of extreme heat exposure:
- The acrylic panels retained 96% optical clarity.
- Glass counterparts had cracked or shattered in several units.
- Acrylic panels also weighed 42% less, making installation easier.
c) How Acrylic Beats Polycarbonate in UV Performance
Property | Acrylic (PMMA) | Polycarbonate (PC) |
---|---|---|
UV Resistance | Excellent | Poor (yellows without coating) |
Optical Retention | Long-term (5–10 yrs) | Requires UV coating |
Heat Resistance | Slightly lower | Slightly higher |
d) Best Practices for Harsh Environments
- Use cast acrylic for extreme clarity and thermal expansion control.
- For sunny + cold mixed zones (e.g., Alpine), opt for UV + cold impact-modified PMMA.
- Avoid using uncoated extruded acrylic in high-temperature outdoor settings.
Is Acrylic Material Resistant to Chemicals and Abrasion?
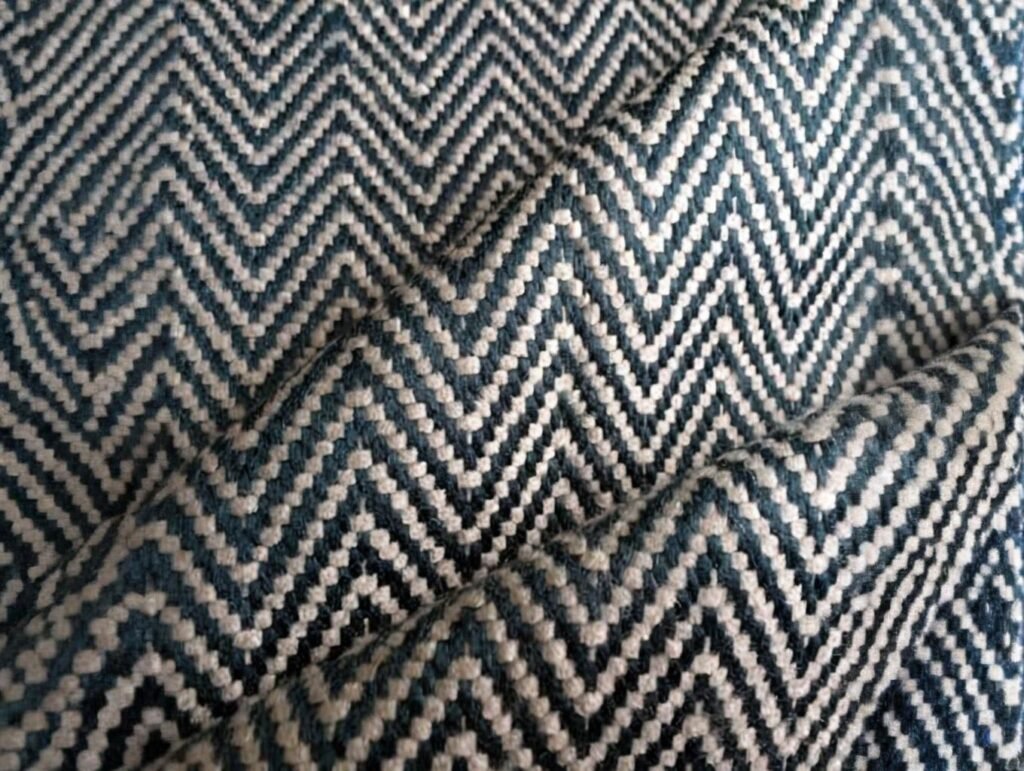
Acrylic has good resistance to diluted acids, oils, and cleaning agents, but it is vulnerable to strong solvents like acetone and alcohols. Abrasion resistance is high for a thermoplastic, but surface scratches can occur without protective coatings.
a) Chemical Resistance Overview
Chemical Type | Acrylic Resistance | Notes |
---|---|---|
Dilute Acids (e.g., HCl, H₂SO₄) | Good | No degradation under normal concentrations |
Alkalines (e.g., NaOH) | Moderate | Stress whitening may occur with exposure |
Organic Solvents (e.g., acetone, MEK) | Poor | Causes cracking, crazing, or melting |
Alcohols (e.g., ethanol) | Weak | Surface damage and internal stress possible |
Oils & Grease (e.g., motor oil) | Excellent | No swelling, discoloration, or breakdown |
Cleaning Detergents | Good | Withstands standard industrial cleaners |
b) Abrasion Resistance Analysis
Metric | Acrylic | Polycarbonate | Glass |
---|---|---|---|
Scratch Resistance | High | Low (requires coating) | Very High |
Surface Hardness (Rockwell M) | 90–100 | \~70–80 | >100 |
Buffability | Yes | Limited | Not buffable |
Coating Compatibility | Excellent (anti-scratch, anti-fog) | Limited | Not applicable |
c) Case Study: Medical Lab Enclosures
A lab equipment company replaced polycarbonate control panel windows with cast acrylic due to alcohol-based cleaning compatibility issues. While PC clouded after repeated sanitation, acrylic stayed clear for over 300 cleaning cycles using hospital-grade detergents—demonstrating superior resistance to mild chemicals and better lifecycle value.
d) Best Practices for Chemical Durability
- For food or medical use, always request FDA-grade acrylic with surface treatments.
- Avoid using acrylic near solvents or heavy degreasers.
- For improved abrasion resistance, apply hard coatings or UV-cured overlays.
How Does Acrylic Compare to Polycarbonate and Glass in Extreme Environments?
In harsh conditions, acrylic excels in optical clarity and UV resistance, while polycarbonate offers superior impact resistance and glass provides unmatched scratch protection. The best choice depends on whether your priority is clarity, strength, or surface hardness.
a) Material Performance Comparison in Harsh Environments
Property / Stress Test | Acrylic (PMMA) | Polycarbonate (PC) | Glass |
---|---|---|---|
Optical Clarity | 92% light transmission | 88–90% | 91–92% |
UV Resistance | Excellent | Poor (needs coating) | Good |
Impact Resistance (Izod) | Moderate | Very High | Very Low (shatters) |
Scratch Resistance | High | Low | Very High |
Thermal Stability (°C) | –40 to 85–100°C | –40 to 115–130°C | –50 to 250°C |
Chemical Resistance | Moderate | Good | Excellent |
Weight (g/cm³) | 1.19 | 1.20 | 2.5 |
b) Application Suitability Matrix
Application | Best Material | Reason |
---|---|---|
Protective machine covers (indoor) | Polycarbonate | Impact resistance and toughness |
Outdoor signage or lightboxes | Acrylic | UV clarity, surface polish, easy fabrication |
Touchscreen kiosks in malls | Acrylic (coated) | Optical quality + weight advantage |
Chemical labs or pharma | Glass or PC | Scratch and solvent resistance |
Bulletproof shields | Laminated polycarbonate | Extreme impact requirements |
c) Field Report: Greenhouse Paneling Project
In a European botanical center:
- Acrylic panels lasted 10+ years with minimal discoloration.
- Polycarbonate panels yellowed after 3 years, leading to reinstallation.
- Glass was deemed too heavy and risky for the tall dome installation.
d) Critical View: Which Is Best?
- Acrylic is the sweet spot for clarity, cost, and UV endurance.
- Polycarbonate wins when strength is critical but must be coated.
- Glass is ideal where weight isn’t an issue and long-term surface protection matters.
Which Types of Acrylic Are Best for Outdoor and Industrial Use?
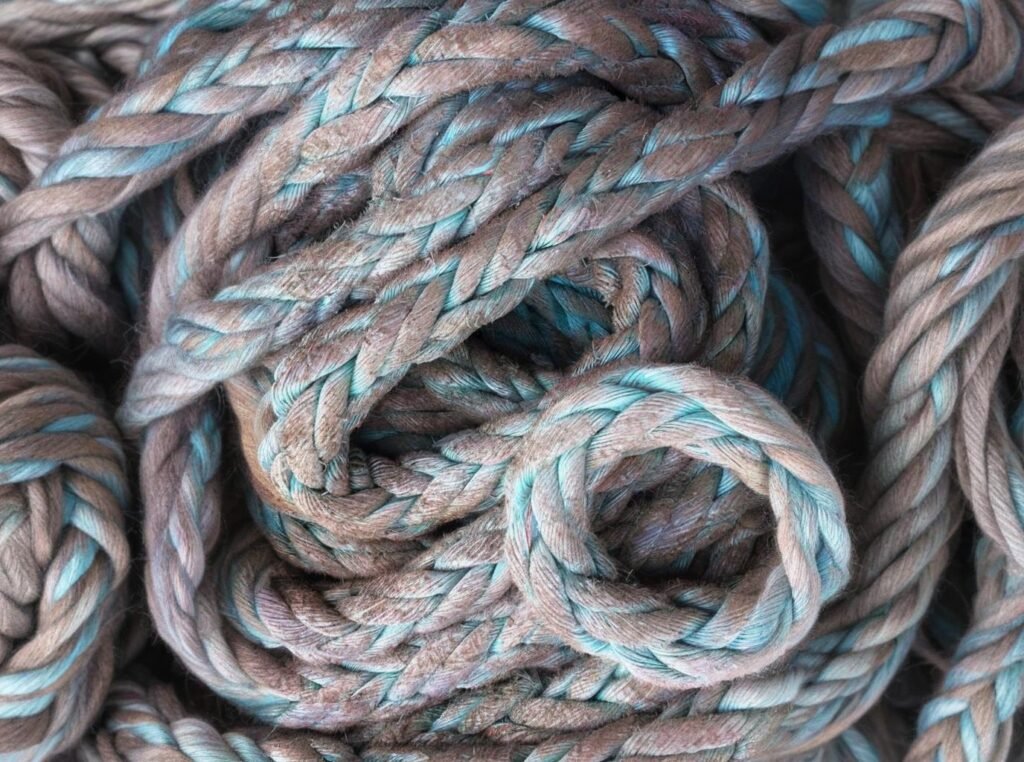
Cast acrylic and UV-stabilized extruded acrylic are the most suitable types for outdoor and industrial use due to their superior weatherability, optical retention, and mechanical resilience. Impact-modified grades and co-extruded blends also offer targeted durability for specific environments.
a) Acrylic Types Overview for Harsh Applications
Acrylic Type | Key Features | Ideal Use Case |
---|---|---|
Cast Acrylic (Cell/Continuous) | Best UV resistance, optical clarity | Outdoor signage, skylights, industrial panels |
UV-Stabilized Extruded Acrylic | Consistent thickness, weatherable additives | Kiosks, protective enclosures |
Impact-Modified Acrylic | Rubber modifiers improve impact performance | Factory windows, tool machine covers |
Co-Extruded Acrylic (ASA or PMMA blends) | Dual-layer for strength + durability | Automotive trims, architectural cladding |
Textured or Frosted Acrylic | Scratch-hiding surface for high-traffic areas | Retail, outdoor displays, bus shelters |
b) Performance Comparison Table
Property | Cast Acrylic | Extruded Acrylic | Impact-Modified Acrylic | ASA/PMMA Co-extrusion |
---|---|---|---|---|
UV Resistance | Excellent | Good | Moderate | Excellent |
Impact Strength | Moderate | Low | High | Very High |
Weathering Stability | 10+ years | 3–5 years | 5–7 years | 10+ years |
Surface Gloss | High | Medium | Medium | High |
Moldability | Moderate | Excellent | Excellent | Good |
c) Case Study: Outdoor LED Lightboxes in Coastal India
A signage manufacturer tested cast acrylic vs. extruded acrylic for outdoor LED boxes:
- Cast acrylic outperformed in UV retention, with 98% clarity after 18 months.
- Extruded acrylic panels showed visible yellowing and brittleness by month 12.
- The decision to switch saved an estimated \$22,000 in annual maintenance.
d) Selection Tips for B2B Buyers
- For climate with extreme sun, always choose UV-resistant cast PMMA.
- For impact zones, use impact-modified or ASA-acrylic sheets.
- Ask for weathering test reports (ASTM D4329, ISO 4892) before bulk ordering.
What Are the Long-Term Performance Test Results for Acrylic Products?
Acrylic performs exceptionally well in long-term UV, weather, and aging tests, with minimal yellowing, cracking, or loss of strength when high-grade material is used. Real-world and lab results show acrylic can last 7–15 years depending on application and exposure conditions.
a) Accelerated Weathering Test Data
Test Standard | Result Summary (Cast Acrylic) | Duration Simulated |
---|---|---|
ASTM G154 (UV-A) | No yellowing, <5% gloss loss | \~5 years outdoor exposure |
ISO 4892-2 | Maintained >90% transparency | 1000 hours |
DIN 75220 | Dimensional stability retained | Thermal cycling validated |
ASTM D638 (Tensile) | Strength retained within 92% of initial | After humidity + UV test |
b) Real-World Field Results: Rooftop Glazing (Germany)
A cast acrylic skylight dome installed in Munich in 2014 was tested in 2023:
- No stress cracks, surface gloss still over 80%.
- Tensile strength drop: only 6% from original value.
- Weather seal around the panel failed before the material itself—highlighting its longevity.
c) Factors That Affect Long-Term Durability
Factor | Impact on Lifespan | Mitigation Strategy |
---|---|---|
UV Intensity (Geographic) | High UV zones degrade unprotected sheets | Use UV-absorbing grades |
Thickness | Thin sheets warp/fail sooner | Choose thicker gauge for long exposure |
Air Pollution | Sulfur compounds can stain or corrode | Use coated or specialty formulations |
Installation Quality | Poor mounting causes stress cracks | Follow supplier installation instructions |
d) What Buyers Should Demand
- Request accelerated aging test certificates from suppliers.
- Prefer brands or manufacturers with ISO/ASTM-compliant lab reports.
- If sourcing from China, ask about QUV test machine availability and test duration logs.
How Do Environmental Certifications Impact Acrylic’s Durability Claims?
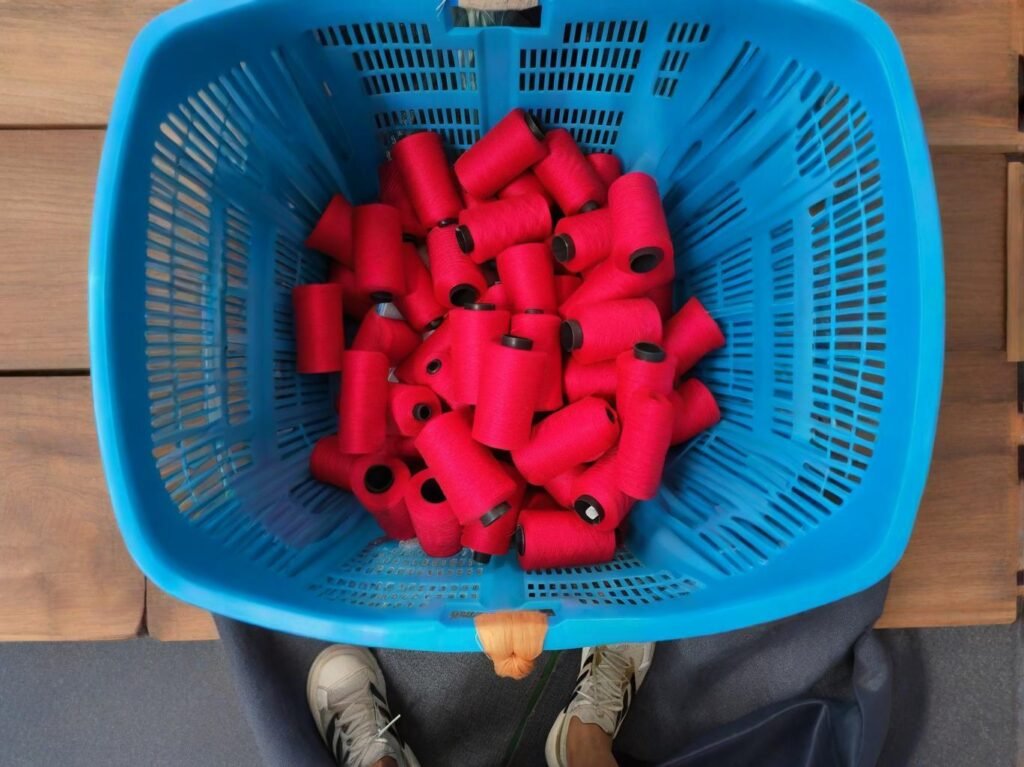
Certifications such as ISO 4892, ASTM G154, ROHS, REACH, and UL94 serve as third-party validations of an acrylic material’s resistance to UV aging, chemical exposure, and fire—providing credibility and assurance to industrial buyers and engineers. These certifications are especially critical when the material is used in regulated or extreme environments.
a) Key Certifications and What They Mean
Certification / Test | Focus Area | What It Confirms |
---|---|---|
ISO 4892 | Accelerated weathering (UV, temp) | Durability under sunlight and humidity |
ASTM G154 | UV resistance (fluorescent light) | Long-term aging resistance |
ROHS (EU Directive) | Hazardous substances restriction | No lead, cadmium, mercury, or other toxins |
REACH | Chemical safety compliance | Ensures safe material lifecycle |
UL94 | Flammability standard | V-0 or V-2 rating denotes flame resistance |
ISO 9001 / ISO 14001 | Manufacturing and environmental systems | Proven quality and sustainability practices |
b) Case Example: Transit Shelters in Sweden
A Swedish government contract for heated bus shelters required certified UV and flame-retardant acrylic panels. The winning supplier provided:
- ISO 4892-2 weathering test results showing less than 7% gloss reduction after simulated 7-year exposure
- ROHS & REACH documents for EU import compliance
- UL94-V2 rating, fulfilling fire safety mandates for public spaces
c) Why Certifications Matter for B2B
- Mitigate liability: Especially in public infrastructure or transportation
- Win contracts: Many tenders require ISO/ASTM documentation
- Ensure durability: Certified materials are more predictable in performance
When sourcing from overseas factories (especially in Asia), request certification copies in advance, and verify lab accreditation (e.g., SGS, TUV, Intertek) to ensure authenticity.
What Should B2B Buyers Consider When Sourcing Durable Acrylic for Tough Environments?
Buyers must consider application conditions, material formulation, compliance requirements, and supplier capability when sourcing durable acrylic. Long-term reliability, rather than just upfront price, should drive procurement decisions.
a) Sourcing Evaluation Checklist
Consideration | What to Evaluate |
---|---|
Application Environment | Is it outdoor, marine, desert, cold, or chemical-heavy? |
Acrylic Grade/Type | Cast vs extruded? UV-stabilized? Impact-modified? |
Certifications Required | UL, ISO, REACH, ROHS depending on country or sector |
Supplier Capabilities | Can they customize size, color, or blend? |
MOQ and Sampling Policy | Do they provide test sheets or prototypes? |
Logistics and Lead Time | Especially critical for replacement cycles and seasonal use |
b) Global Sourcing Hotspots and Insights
Region | Pros | Cons |
---|---|---|
China | Competitive pricing, full customization, rapid scaling | Must verify certifications |
Germany | Engineering precision, material purity | Higher cost, longer lead time |
USA | Fast fulfillment, strong compliance | Expensive for large volumes |
India | Emerging supplier base, good value | Inconsistent optical quality |
c) Red Flags to Avoid
- Suppliers offering no samples or lab data.
- Generic PMMA being marketed as “UV stable” without actual test results.
- No mention of test standards or international compliance on the data sheet.
d) Best Practices for Industrial Buyers
- Conduct pilot testing with sample sheets before full production.
- Choose suppliers who offer custom formulation for environment-specific use.
- Build long-term partnerships with certified manufacturers for consistent quality.
Source Certified Durable Acrylic from SzoneierFabrics
At SzoneierFabrics, we specialize in customized, industrial-grade acrylic solutions tailored for the most demanding environments. Whether you’re sourcing for construction, signage, automotive, or marine use—we offer:
- ✅ Cast and extruded acrylic with UV and impact modifiers
- ✅ ROHS, REACH, and ISO-certified production lines
- ✅ Free samples and custom formulations
- ✅ Short lead times and low MOQs for B2B buyers
- ✅ Engineering support for performance-critical applications
Ready to upgrade your product line with long-lasting, high-performance acrylic? Contact SzoneierFabrics now for a free sample or quote.