When we think of industrial textiles, materials like polyester, nylon, and aramid often take the spotlight. Yet acrylic fiber quietly powers a significant share of industrial applications, from filtration systems and thermal insulation to outdoor signage and UV-resistant canopies. While originally developed as a wool substitute for fashion, acrylic’s performance profile makes it a strong player in technical manufacturing environments.
Acrylic fiber is a synthetic polymer made from polyacrylonitrile. It is lightweight, thermally insulating, resistant to sunlight, chemicals, and weathering—making it an ideal material for industrial textiles used in harsh, high-demand environments.
Its soft feel is just one of its features. Acrylic can also withstand exposure to acids, alkalis, and UV radiation, and when properly engineered, it delivers flame retardancy and dimensional stability. In one notable example, an automotive air filter company transitioned from polyester to acrylic for its pleated filtration fabrics due to better chemical resistance and lower fiber distortion over time.
In this article, we’ll unpack acrylic fiber’s molecular makeup, explore its role in heavy-duty applications, and help B2B buyers and product engineers evaluate where it fits into modern industrial textile production.
What Is Acrylic Fiber and How Is It Produced for Industrial Use?
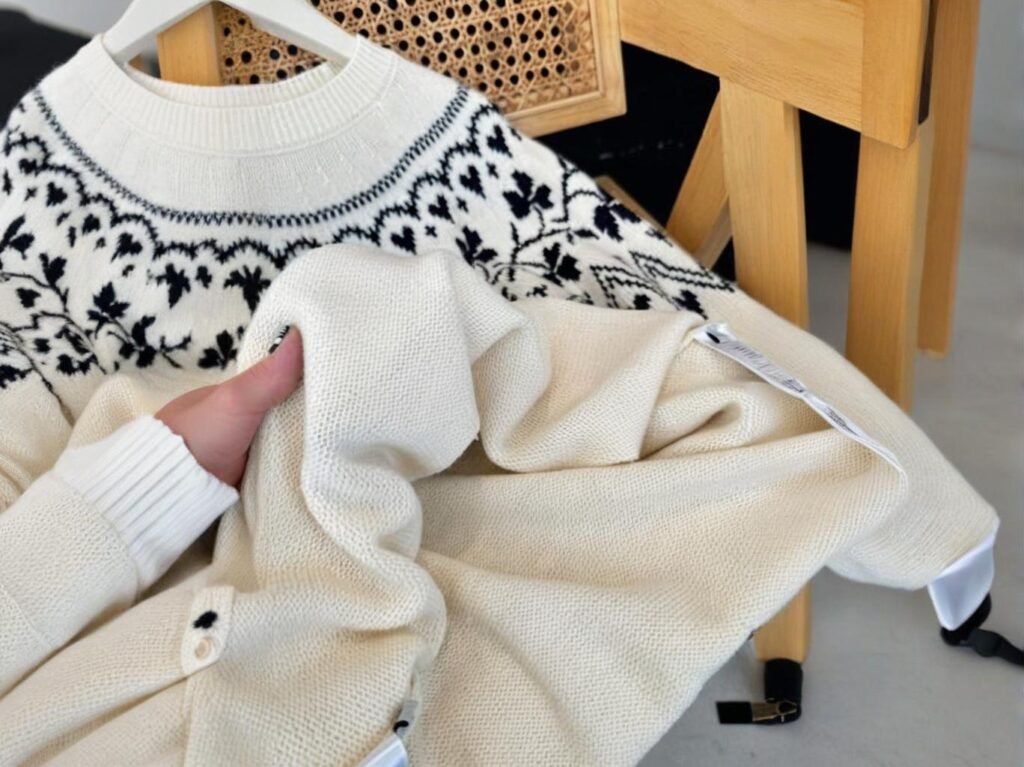
Acrylic fiber is a synthetic polymer composed primarily of acrylonitrile, derived from petrochemical feedstocks. It’s produced through wet or dry spinning methods and tailored through additives or blending to serve industrial performance needs, such as UV resistance or flame retardancy.
From Monomer to Fiber—How Acrylic Is Engineered for Industry
Production Overview
- Polymerization Acrylonitrile undergoes free-radical polymerization to form polyacrylonitrile (PAN). Often, comonomers like vinyl acetate or methyl acrylate are added to improve flexibility and dyeability.
- Spinning Methods
- Wet Spinning: The polymer solution is extruded into a coagulation bath (used for high-tenacity fibers).
- Dry Spinning: Solvent evaporates as the fiber solidifies in hot air (faster and more scalable).
Process Step | Technical Notes |
---|---|
Polymer Content | ≥85% acrylonitrile for “acrylic” labeling |
Spinneret Type | Round or trilobal for surface customization |
Fiber Form | Staple or tow for nonwovens & blends |
- Post-Processing
- Stretching: Aligns molecular chains for higher strength
- Crimping: Adds bulk, important for insulation applications
- Cutting: Tailored to specific industrial formats (3–15 cm fiber lengths)
Types of Acrylic Used in Industry
- Regular Acrylic: Strong, warm, colorfast—suitable for filtration or insulation
- Modacrylic: Modified with halogen-based comonomers for flame resistance
- High-Bulking Acrylic: Crimped for high-loft textiles like thermal linings
Real-World Note: A European nonwoven fabric producer uses trilobal-dry-spun acrylic fibers for acoustic panels in commercial buildings due to their sound-dampening structure and dimensional recovery after compression.
What Are the Key Physical and Chemical Properties of Acrylic Fiber?
Acrylic fiber boasts a unique combination of light weight, chemical stability, UV resistance, and thermal insulation, making it suitable for technical textiles exposed to extreme environments or continuous mechanical stress.
Acrylic Fiber Property Matrix with Performance Ratings
Property | Acrylic Fiber | Industrial Benefit |
---|---|---|
Density | \~1.17 g/cm³ | Lightweight for transportable textiles |
Moisture Regain | 1.5%–2.5% | Quick-drying, mold-resistant |
Thermal Conductivity | Low (\~0.04 W/m·K) | Excellent insulation |
UV Resistance | High (especially when solution dyed) | Suitable for outdoor exposure |
Flame Resistance (Modacrylic) | Self-extinguishing | Protective textiles, workwear |
Acid/Alkali Resistance | Very good | Industrial chemical environments |
Tensile Strength | Moderate to High (\~2.0–4.5 g/denier) | Withstands mechanical use in filters/fabrics |
Elastic Recovery | Moderate | Acceptable for flat industrial layers |
Key Advantages
- UV Resistance: Maintains integrity in signage, marine, and outdoor applications
- Chemical Stability: Resists breakdown from acidic fumes or alkaline wash cycles
- Thermal Performance: Competes with wool or polyester in insulation applications
- Colorfastness: Excellent when solution-dyed or cationic-dyed for industrial use
Limitations
- Melts at \~230°C (lower than aramids)
- Not biodegradable—requires waste management consideration
Performance Comparison
Fiber Type | UV Resistance | Flame Resistance | Acid Resistance | Cost (\$/kg) |
---|---|---|---|---|
Acrylic | ★★★★☆ | ★★★☆☆ (modacrylic: ★★★★★) | ★★★★☆ | \$2.0–3.5 |
Polyester | ★★★☆☆ | ★☆☆☆☆ | ★★★☆☆ | \$1.8–2.8 |
Nylon | ★★☆☆☆ | ★★☆☆☆ | ★★☆☆☆ | \$2.5–3.0 |
Aramid (e.g. Nomex) | ★★★★★ | ★★★★★ | ★★★★☆ | \$25–30+ |
Example: A Southeast Asian tent manufacturer replaced polyester backing fabric with solution-dyed acrylic for better UV stability. The result? Product lifespan increased from 2.5 years to over 5 years in direct sunlight without fading or brittleness.
How Does Acrylic Compare to Other Synthetic Fibers in Industrial Applications?
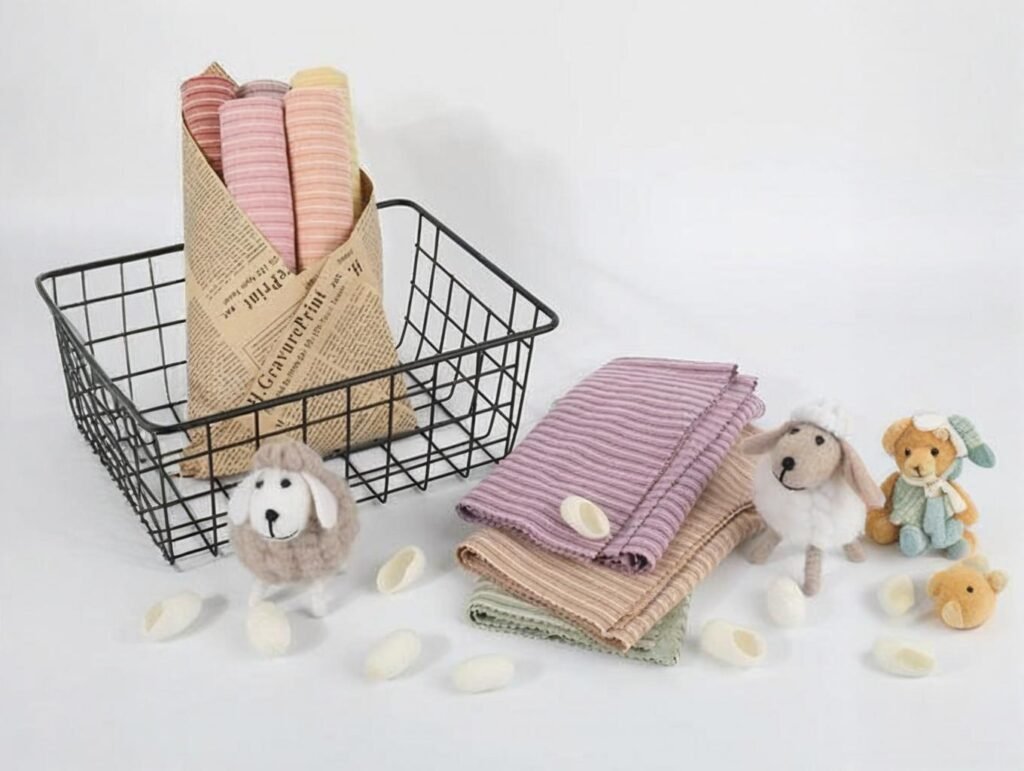
In the realm of industrial textiles, acrylic competes directly with polyester, nylon, polypropylene, and aramid fibers. While each material has its own strengths, acrylic stands out for its balance of thermal insulation, chemical resistance, and cost-efficiency in mid-demand environments.
Comparative Performance of Acrylic vs. Other Industrial Fibers
1. Acrylic vs. Polyester
- Acrylic offers better insulation and UV resistance, making it more suitable for outdoor, marine, and cold-weather industrial uses.
- Polyester excels in tensile strength and abrasion resistance, ideal for geotextiles and industrial straps.
Property | Acrylic Fiber | Polyester Fiber |
---|---|---|
UV Resistance | ★★★★☆ | ★★★☆☆ |
Insulation | ★★★★☆ | ★★☆☆☆ |
Tensile Strength | Moderate | High |
Colorfastness | Excellent (solution-dyed) | Good |
Typical Use | Awning, filter, insulation | Bags, webbing, apparel |
2. Acrylic vs. Nylon
- Nylon has higher strength and stretch recovery but poor UV resistance, which limits its outdoor life.
- Acrylic resists UV degradation and maintains shape and color better under sunlight.
Property | Acrylic | Nylon |
---|---|---|
Stretch Recovery | Moderate | Excellent |
UV Stability | High | Low |
Moisture Absorption | Low | Moderate |
Heat Resistance | Moderate | Higher |
3. Acrylic vs. Aramid (e.g., Nomex, Kevlar)
- Aramid is a high-performance fiber for extreme heat and flame resistance (used in fire suits, aerospace).
- Acrylic, particularly modacrylic, offers good flame resistance at a fraction of the cost, making it suitable for budget-sensitive protective gear or flame-retardant linings.
Property | Acrylic (Modacrylic) | Aramid |
---|---|---|
Flame Resistance | ★★★★☆ | ★★★★★ |
Price (USD/kg) | \$3–5 | \$25+ |
Processability | Easy | Complex |
Washing Durability | Good | Excellent |
Industry Insight: An Eastern European manufacturer of FR blankets uses modacrylic acrylic for thermal liners because it balances fire safety with affordability and bulk production needs—especially compared to aramids.
Which Industrial Sectors Commonly Use Acrylic Fiber-Based Textiles?
Acrylic fiber’s versatility enables its use in a wide range of industrial sectors—especially those requiring UV protection, thermal insulation, chemical resistance, or flame retardancy.
Industry Applications of Acrylic-Based Textiles
1. Outdoor & Marine Textiles
- Used in: Awnings, marine covers, tents, sunshades
- Requirements: UV resistance, water resistance, low shrinkage
Feature | Acrylic Performance |
---|---|
Lightfastness (ISO 105-B02) | Grade 6–7 |
Water Absorption | <2% |
Salt Spray Resistance | High |
Case Example: A Mediterranean yacht company uses solution-dyed acrylic canopies for sun protection. After 5 years of sea exposure, over 90% of the material retained its original color, outperforming polyester equivalents by 2x.
2. Filtration & HVAC
- Used in: Air filters, dust collection bags, industrial filtration systems
- Requirements: Dimensional stability, chemical resistance, thermal tolerance
Property | Acrylic Nonwoven Performance |
---|---|
Heat Resistance | Up to 130°C continuous |
Acid Resistance | Excellent |
Filtration Efficiency | High (for fine particulates) |
Application Note: Acrylic fibers are often needle-punched into felt for air filtration in cement and chemical plants.
3. Protective Textiles
- Used in: FR blankets, fire-retardant curtains, electrical insulation layers
- Requirements: Flame retardancy, low toxicity, thermal stability
- Modacrylics (with halogenated comonomers) are commonly used for:
- Fire barriers in bedding
- FR clothing linings
- Fire-resistant upholstery
4. Construction & Architecture
- Used in: Acoustic panels, thermal insulation pads, exterior cladding fabrics
- Requirements: Bulk, sound absorption, resistance to moisture and decay
Project Insight: A commercial builder in Germany chose trilobal acrylic for ceiling acoustic panels. The material provided both sound-dampening and decorative appeal, with minimal maintenance requirements.
5. Industrial Upholstery & Technical Fabrics
- Used in: Workstation furniture, wall coverings, abrasion-resistant linings
- Requirements: Wear resistance, fire rating compliance, colorfastness
How Does Acrylic Perform in Harsh Environmental Conditions?
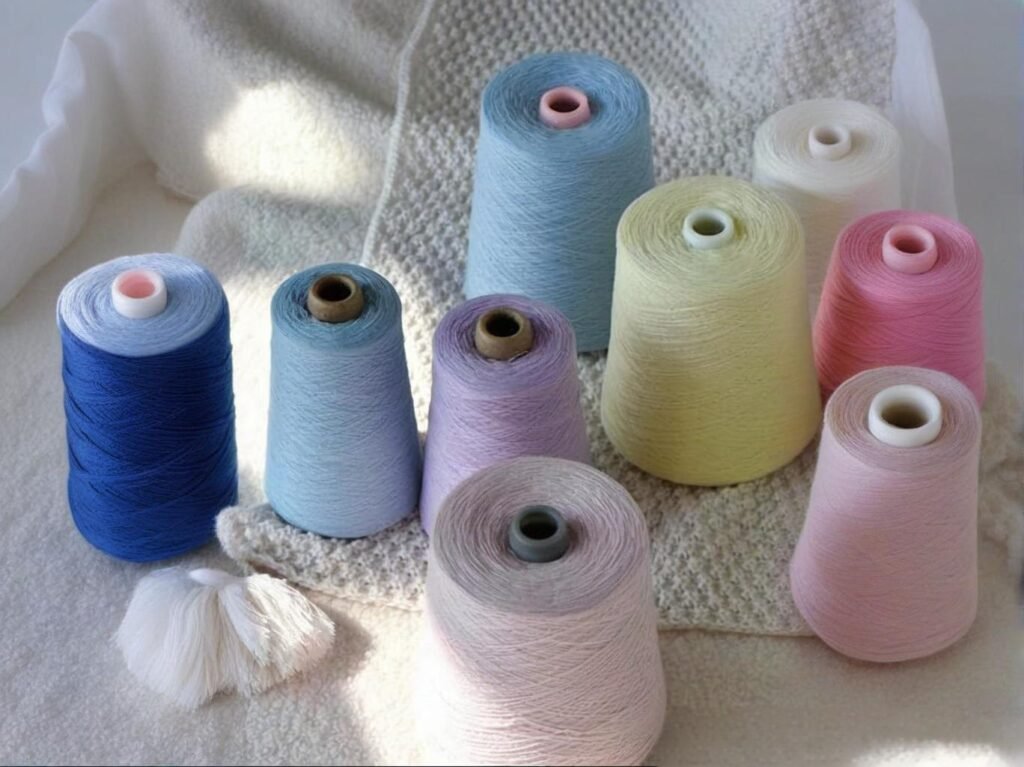
Acrylic fiber is well-known for its resilience in extreme environments, including prolonged exposure to sunlight, salt spray, acid fumes, fluctuating temperatures, and mechanical stress. This makes it an ideal candidate for demanding outdoor, industrial, and chemical applications.
Environmental Tolerance of Acrylic in Industrial Use
UV and Sunlight Exposure
- Acrylic, especially solution-dyed, has superior UV stability compared to polyester and nylon.
- Maintains color and strength over long periods in outdoor use.
- Does not yellow or degrade quickly under sunlight.
Fiber Type | UV Resistance Grade (ISO 105-B02) | Fading After 1 Year Exposure |
---|---|---|
Acrylic (solution dyed) | Grade 6–7 | <10% color fade |
Polyester | Grade 3–4 | 30–50% color fade |
Nylon | Grade 2–3 | 50–70% color fade |
Example: An outdoor signage company in California tested three awning materials under direct sun. Acrylic fabric outperformed polyester and PVC blends, retaining over 90% of its original hue after 12 months.
Salt, Humidity, and Mildew
- Acrylic is hydrophobic, absorbing only \~2% of its weight in water.
- Its structure resists mildew, mold, and rot, making it ideal for marine, coastal, and high-humidity environments.
- Salt spray resistance makes it a staple in boat covers and marine cushions.
Chemical Exposure
- Acrylic performs well under acidic and alkaline environments, often used in filtration systems at chemical plants and dyeing facilities.
- Resistant to:
- Nitric acid
- Sulfur dioxide
- Ammonia-based cleaning solutions
Thermal Resistance
- While not a high-heat fiber like aramid, acrylic can tolerate continuous use up to 130°C.
- Modacrylics go further, offering self-extinguishing properties for fire safety textiles.
Environmental Condition | Acrylic Performance Rating |
---|---|
UV Radiation | ★★★★★ |
Salt Spray / Humidity | ★★★★☆ |
Acidic Fumes | ★★★★☆ |
Mild Alkali | ★★★★☆ |
Heat Exposure (non-FR) | ★★★☆☆ (max \~130°C) |
Flame Retardant (modacrylic) | ★★★★☆ |
Use Case: A Southeast Asian power utility company replaced fiberglass-based insulation in substations with modacrylic felt linings due to higher resistance to thermal cycling and better fire ratings.
What Types of Industrial Fabrics Are Made with Acrylic Fiber?
Acrylic fiber’s form versatility allows it to be woven, knitted, needle-punched, or laminated into a range of industrial textile formats. These include both performance-driven and structural fabrics used across multiple sectors.
Fabric Structures and Acrylic Fiber Integration
1. Needle-Punched Nonwoven Acrylic Fabrics
- Used in: Filter media, insulation panels, FR barriers
- Produced by layering and interlocking staple acrylic fibers without weaving.
Benefit | Application Examples |
---|---|
High loft & breathability | HVAC filters, sound panels |
Dimensional stability | Automotive heat shields |
2. Woven and Twill Acrylic Technical Fabrics
- Used in: Marine awnings, industrial upholstery, sunshades
- Offers durable structure and dimensional consistency, especially when solution-dyed.
Weave Type | Application |
---|---|
Plain Weave | Marine fabrics, advertising tents |
Twill Weave | Outdoor upholstery, deck chairs |
Example: An Italian marine brand uses woven solution-dyed acrylic fabric with a PU coating for its sailboat covers—achieving both waterproofing and 5+ year outdoor durability.
3. Laminated Acrylic Fabrics
- Used in: Protective apparel, roofing membranes
- Acrylic fabric can be bonded to PVC, PU, or other films for:
- Waterproofing
- Fire retardancy
- Chemical resistance
4. Thermal Bonded Acrylic Liners
- Used in: Cold storage gear, industrial jackets, gloves
- Acrylic’s insulative properties are leveraged as inner linings, often brushed for warmth and softness.
5. Acrylic-Coated Technical Textiles
- Surface coated to improve:
- UV protection
- Flame resistance
- Water and oil repellency
Fabric Type | Typical End Use |
---|---|
Needle-punched felt | Air filters, protective mats |
Laminated woven acrylic | Roofing, event tents |
Coated acrylic textiles | High-end umbrellas, exhibition signage |
Twill weave + PU backing | Industrial canopies, transit shelters |
Case Insight: A bus stop manufacturer in Dubai needed fade-resistant, durable canopy fabric. They chose twill-woven acrylic with PU lamination, resulting in zero fading or fraying over 3 years under high desert UV exposure.
Is Acrylic Fiber Suitable for Flame-Retardant or UV-Stable Applications?
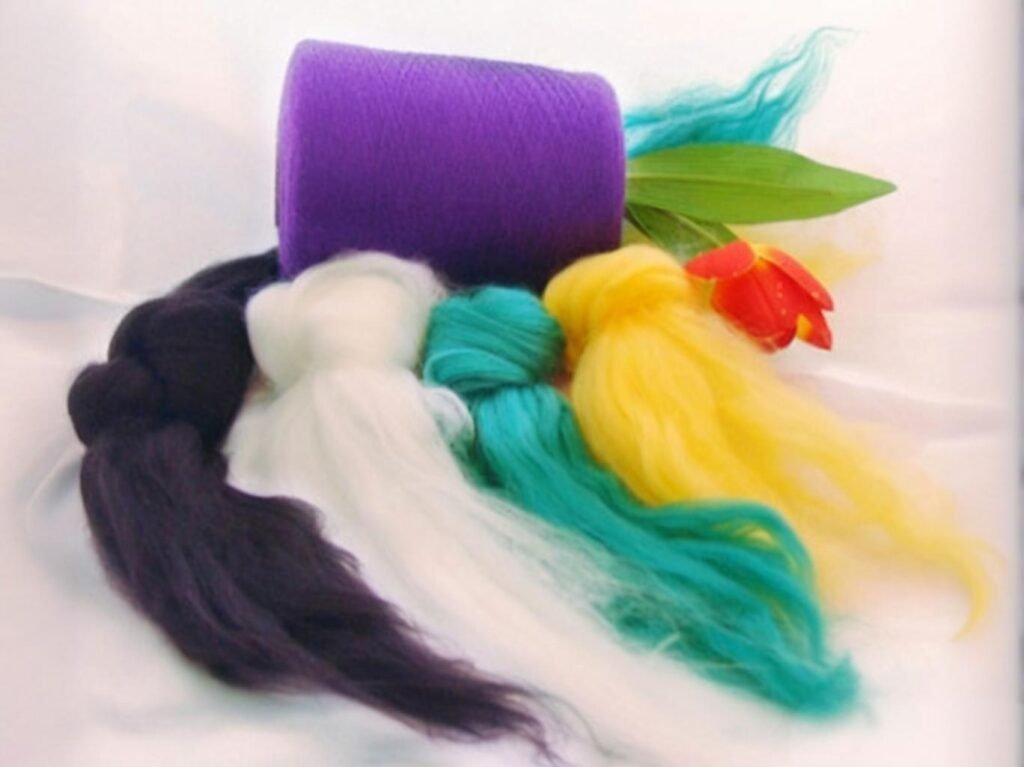
Yes—acrylic fiber, especially when modified or properly finished, performs exceptionally well in UV-exposed and flame-retardant textile applications. This dual capability makes it a preferred material for both outdoor industrial use and protective environments like transportation, construction, or utilities.
How Acrylic Is Engineered for UV and FR Needs
UV Stability in Acrylic
- Solution-dyed acrylic has UV-stabilizers blended into the polymer itself during fiber formation.
- Unlike surface-dyed fabrics, solution-dyed acrylics resist:
- Fading from sunlight (ISO 105-B02 Grade 6–7)
- Cracking and brittleness due to prolonged UV exposure
- Degradation under outdoor pollutants (ozone, NOx)
Real-World Example: In Florida’s humid coastal climate, a hospitality brand used solution-dyed acrylic awnings that retained over 90% color after 4 years in direct sunlight and salt air—outperforming standard polyester by a wide margin.
Flame Retardancy in Modacrylics
- Modacrylic fibers are made by copolymerizing acrylonitrile with halogen-containing monomers, giving them inherent flame resistance.
- Key characteristics:
- Self-extinguishing
- Low smoke toxicity
- Stable under arc or thermal exposure
Property | Modacrylic Performance |
---|---|
Limiting Oxygen Index (LOI) | >28% (self-extinguishing) |
Melting Point | None (chars instead) |
After-flame time (ISO 15025) | ≤2 seconds |
Typical Modacrylic Applications
- Flame-retardant protective clothing linings
- Thermal and fire-resistant upholstery
- Arc-flash rated garment layers
- Curtains and drapes in public buildings
Add-on Treatments for Standard Acrylic
- Acrylic can be top-treated with:
- FR coatings (silicone, phosphate-based)
- UV-protective coatings for extended outdoor exposure
- Anti-drip or self-extinguishing finishes
Industrial Note: An Asian railway system selected modacrylic-blend seat fabrics for subway cars due to the combination of fire resistance, low smoke output, and easy cleaning performance.
How Can Buyers Source High-Performance Acrylic Fiber for Industrial Manufacturing?
Buyers should prioritize technically capable, responsive suppliers that offer not only raw material production but also fabric development, performance testing, and customization services based on the end-use environment.
Sourcing Strategy for Industrial Acrylic Fiber Buyers
Key Sourcing Factors to Define
- Application type: Filtration, canopy, upholstery, insulation, FR
- Required certifications: OEKO-TEX®, REACH, UL94, ISO 105, ISO 15025
- Preferred dyeing method: Solution dyed, cationic dyed, raw white
- Format: Staple fiber, yarn, nonwoven, laminated fabric
- MOQ and lead time expectations
Certifications to Look For
Certification | Relevance |
---|---|
OEKO-TEX® Standard 100 | Skin safety, especially for interior use |
REACH Compliance | Chemical safety for EU-regulated markets |
ISO 105-B02 / C06 | UV and wash fastness |
ISO 15025 | Flame resistance (surface ignition test) |
ASTM E84 | Surface burn classification (building codes) |
Questions to Ask Potential Suppliers
- Do you offer batch-specific test reports?
- Can you provide lab dips or physical samples?
- What’s your MOQ for solution-dyed industrial acrylic?
- Can you custom-blend or laminate fabrics?
- What finishing options do you support (FR, UV, anti-static)?
Why Choose SzoneierFabrics
Capability | SzoneierFabrics Offering |
---|---|
Fiber customization | ✅ Modacrylic & regular acrylic blends |
Industrial fabric development | ✅ Woven, nonwoven, coated options |
Technical support | ✅ Application-based engineering |
Low MOQ + fast sampling | ✅ For small to mid-sized B2B buyers |
Certification coverage | ✅ OEKO-TEX®, ISO, REACH |
Client Story: A Canadian HVAC component brand partnered with SzoneierFabrics to replace their polyester filter backing with needle-punched acrylic nonwovens. The result: improved thermal and chemical resistance, higher retention efficiency, and 28% fewer warranty claims related to material breakdown.
Acrylic Fiber’s Industrial Role Goes Far Beyond Fashion
In today’s performance-driven textile landscape, acrylic fiber delivers exceptional versatility and technical benefits—especially for industrial sectors that demand durability, environmental stability, and custom fabric engineering.
Whether it’s creating a long-lasting awning, insulating a filtration system, or producing flame-resistant materials for infrastructure, acrylic remains one of the most underutilized yet highly capable fibers on the industrial stage.
For sourcing managers, engineers, and product developers, acrylic’s potential lies not just in cost-efficiency but in the ability to tailor it for very specific mechanical and environmental needs—when partnered with the right supplier.
Looking for a Trusted Acrylic Fiber Manufacturer for Industrial Use?
At SzoneierFabrics, we specialize in custom acrylic textile solutions for filtration, protective gear, outdoor fabrics, marine covers, architectural shading, and more.
Why Work with Us:
- ✅ 100% quality-tested acrylic fiber fabrics
- ✅ Custom R\&D support for flame-retardant and UV-stable textiles
- ✅ Solution-dyed, modacrylic, and blended options
- ✅ Fast sampling, low MOQs, and global shipping
- ✅ ISO, REACH, OEKO-TEX® compliance