When you step into a vehicle, the tactile and visual impression of the interior fabric can influence everything from brand perception to passenger comfort. For decades, automakers have experimented with leather, vinyl, polyester, and nylon—but one material is making a quiet but powerful case in the background: acrylic textile.
Acrylic fabric is an excellent choice for automotive interiors due to its superior UV resistance, thermal insulation, softness, dimensional stability, and ability to retain vibrant color even under extreme conditions. It combines durability with a comfortable tactile feel, making it ideal for seats, panels, headliners, and more.
In fact, leading OEMs in Europe and Japan have increasingly turned to acrylic-polyester blends for sun-exposed interior surfaces after field data showed 20–30% better fade resistance than untreated nylon. One Tier 1 auto parts supplier partnered with SzoneierFabrics to develop a solution-dyed acrylic knit that passed over 1,500 hours of QUV exposure testing—with less than 5% color shift.
So why is acrylic moving from winterwear to steering wheels and side panels? Let’s explore the science and sourcing strategies that make acrylic a growing favorite in the automotive textile world.
What Properties Make Acrylic Textile Suitable for Automotive Interiors?
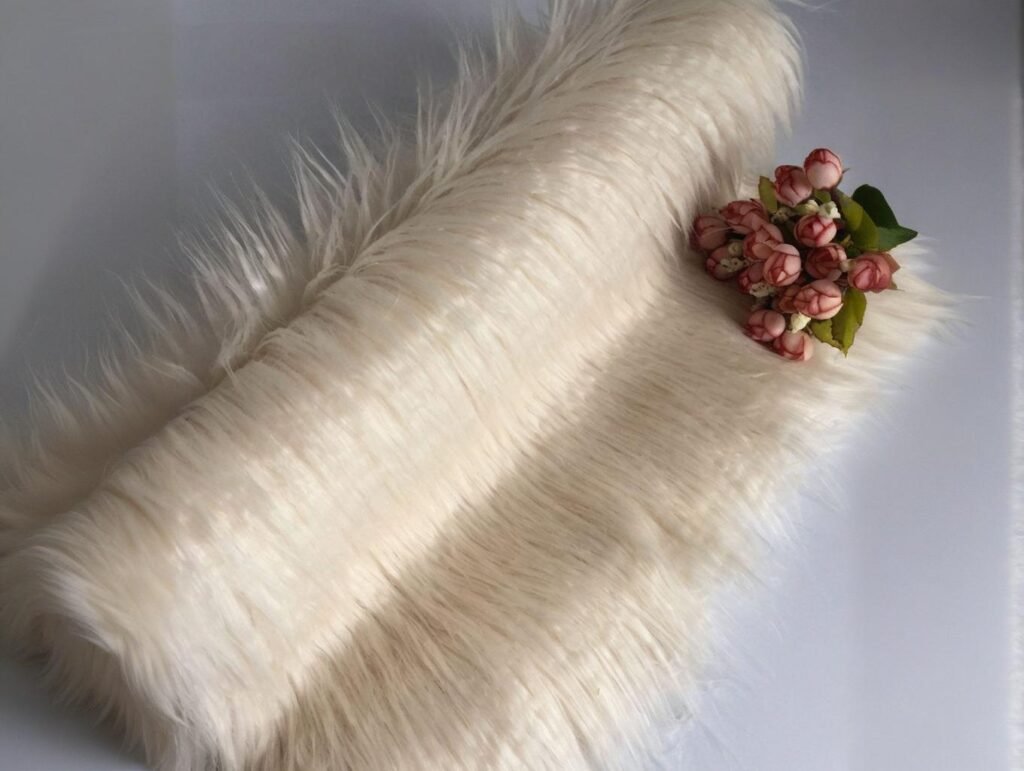
Acrylic fabric’s suitability for automotive interiors comes from its unique balance of softness, color retention, UV resistance, thermal insulation, and shape stability. It provides comfort like natural fibers while offering the endurance of synthetics in high-traffic, high-temperature environments.
Acrylic’s Core Properties for Automotive Environments
1. UV and Heat Resistance
Property | Acrylic Textile Performance |
---|---|
UV resistance (ISO 105-B02) | Grade 5–6 (Excellent) |
Heat tolerance (interior use) | Withstands 70–90°C without distortion |
Fade resistance | Outperforms wool and nylon in sun tests |
- Acrylic contains built-in UV stability in its polymer chain
- When solution-dyed, pigments are locked inside the fiber—far more durable than surface dyes
2. Thermal Insulation and Comfort
- Acrylic offers low thermal conductivity, maintaining comfort in both cold and warm cabin environments
- Its soft, wool-like texture enhances perceived luxury, especially in mid- to high-end vehicle trims
3. Dimensional Stability and Shape Memory
- Maintains fabric shape under compression
- Excellent recovery after stretching or upholstery tensioning
- Reduced shrinkage (<1.5%) even under repeated heat cycles
4. Resistance to Chemical Exposure
- Resistant to automotive-grade cleaners, sweat, sunscreen, and other cabin contaminants
- Retains color and structure even after ISO 15797 simulated industrial wash testing
5. Noise Dampening (Acoustic Behavior)
- Brushed or fleece-like acrylic knits contribute to noise insulation
- Ideal for use in pillars, door panels, and roof headliners
How Does Acrylic Compare to Polyester, Nylon, and Leather in Car Interiors?
Acrylic outperforms nylon in UV and fade resistance, provides a softer hand feel than polyester, and delivers superior comfort-to-cost ratio compared to leather—making it a well-balanced choice for both premium and economy vehicles.
Fiber-by-Fiber Comparison for Interior Applications
1. Key Performance Comparison Table
Property | Acrylic | Polyester | Nylon | Leather |
---|---|---|---|---|
UV resistance | ✅ Excellent | ⚠️ Moderate | ❌ Poor | ✅ Excellent |
Colorfastness (solution dyed) | ✅ Superior | ⚠️ Variable | ⚠️ Variable | ✅ Natural grain |
Surface feel | ✅ Soft | ⚠️ Smooth/slick | ❌ Coarse | ✅ Luxurious |
Heat tolerance | ✅ 90°C | ✅ 120°C | ✅ 100°C | ✅ Up to 150°C |
Cost-effectiveness | ✅ High | ✅ High | ✅ High | ❌ Low |
Breathability | ✅ Moderate | ❌ Low | ❌ Low | ✅ Good |
Weight (gsm for similar use) | ⚖️ 200–300 gsm | ⚖️ 150–250 gsm | ⚖️ 200–280 gsm | ⚖️ 450+ gsm |
2. Use Case Preferences
Application Area | Preferred Material | Reason |
---|---|---|
Seat covers (economy) | Acrylic-poly blend | Cost-effective + soft + fade-resistant |
Door panels | Woven acrylic with coating | Durable with minimal sun degradation |
Headliners | Brushed acrylic | Noise absorption + smooth stretch fitting |
Luxury interiors | Leather or acrylic blend | Comfort and aesthetic finish |
3. Maintenance and Longevity
- Acrylic holds up well to mild cleaners, doesn’t retain odors
- Polyester may pill or yellow under extended sun exposure
- Nylon becomes brittle over time without UV protection
- Leather needs routine conditioning and care—costly for fleets or ride-sharing
4. SzoneierFabrics Real-World Insight
One Southeast Asian EV startup selected woven acrylic-poly blend fabric for its roof liner and seat backs due to cost control and heat resistance. After 1 year of tropical test drives, feedback showed:
- No discoloration or sagging
- 80% driver preference over previous polyester version
- Total fabric cost per car decreased by 12.5%
Is Acrylic Fabric Resistant to UV, Heat, and Color Fading in Vehicles?
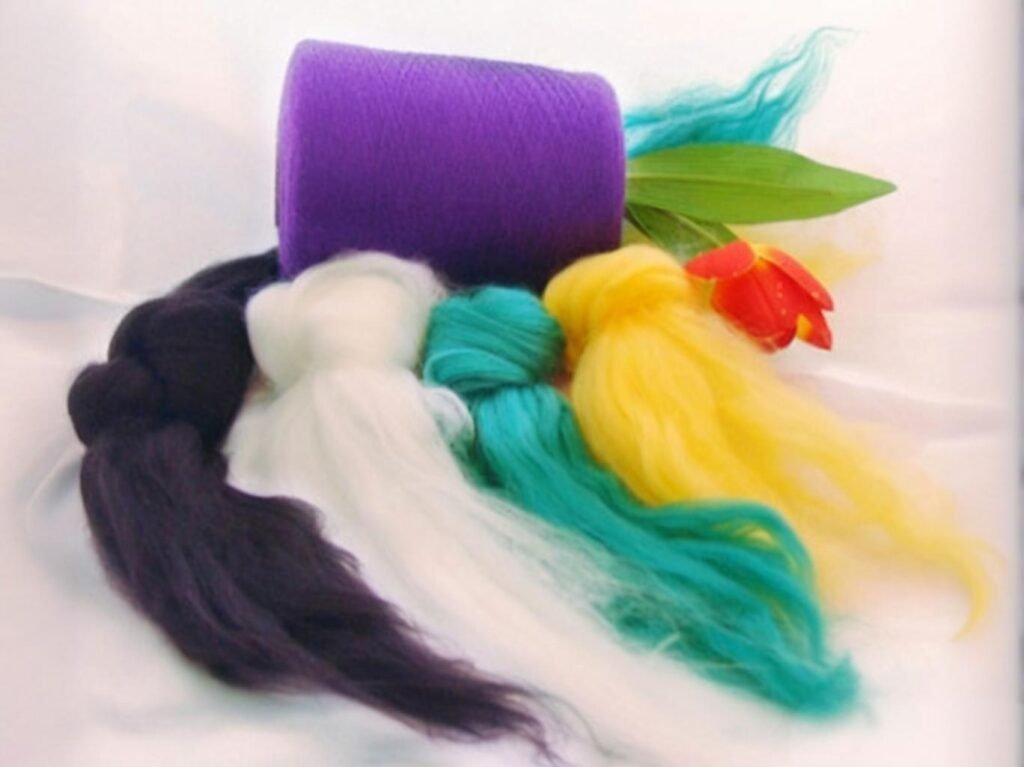
Yes—acrylic fabric is exceptionally resistant to UV radiation, heat exposure, and color fading, especially when solution-dyed. This makes it a top performer for automotive interiors exposed to constant sunlight and temperature shifts.
Acrylic’s Lightfastness and Thermal Endurance
1. UV Resistance and Colorfastness Standards
Test Type | Acrylic Performance | Industry Benchmark |
---|---|---|
QUV Accelerated Weathering (ASTM G154) | >1500 hrs with <5% color shift | 1000 hrs minimum |
ISO 105-B02 Lightfastness Grade | Grade 5–6 (out of 8) | Grade ≥4 for automotive |
SAE J1885 Solar Exposure Test | Passed with no cracking or discoloration | Required for OEM approval |
- Solution-dyed acrylics embed pigment inside the fiber, not just on the surface—this greatly improves color retention
- Even after long-term exposure to tropical sun and UV radiation, acrylic holds its tone better than nylon or polyester
2. Heat Resistance in Closed Car Cabins
Interior temps can reach 65–90°C (149–194°F) in summer. Acrylic maintains shape and color without warping at this range.
Property | Result |
---|---|
Softening point | \~190°C (well above cabin conditions) |
Dimensional stability | <1.5% shrinkage after 10 heat cycles |
Surface finish change | Minimal, no glazing or stiffening |
3. Case Example – Solar Simulation Test
SzoneierFabrics developed a brushed acrylic for seat inserts in a European compact car. The material was tested under 1600 W/m² artificial solar radiation for 1200 hours:
- Color shift ΔE: <1.2 (excellent result; human eye barely detects <2)
- No fiber degradation, curling, or bond failure at the seams
4. Comparison with Polyester and Nylon
Fiber Type | Color Retention in Sun | UV Degradation Over Time |
---|---|---|
Acrylic | Excellent | Very low |
Polyester | Moderate | May yellow after 1–2 years |
Nylon | Poor unless UV-treated | Becomes brittle, cracks |
5. Application Insights
- Ideal for dashboard trims, C-pillar wraps, and rear parcel shelves
- Solution-dyed variants recommended for fleet and outdoor display vehicles
How Does Acrylic Handle Abrasion, Pilling, and Daily Wear in Automotive Use?
Acrylic fabric has moderate abrasion resistance and is prone to pilling if untreated. However, with high-twist yarns, tight weaves, and anti-pilling finishes, it performs well in automotive seating and interior trim exposed to high-friction use.
Mechanical Wear Performance in Cabin Conditions
1. Abrasion Resistance (Martindale Test)
Fabric Type | Martindale Cycles Before Wear (ISO 12947) |
---|---|
Unfinished acrylic knit | 10,000–15,000 |
Tight woven acrylic (with poly blend) | 30,000–45,000 |
Automotive-grade solution-dyed acrylic | 50,000+ |
- Automotive interiors typically require 25,000+ cycles for high-use areas like seats and armrests
- Acrylic-polyester blends meet or exceed this requirement
2. Pilling Resistance (ISO 12945-2)
Fabric Type | Pilling Grade (1–5) |
---|---|
Basic acrylic jersey | 2–3 (visible pilling) |
Anti-pilling finished acrylic | 4–5 (minimal to none) |
Blended with nylon | 4 (improved surface) |
- For headrests, seat backs, and frequently touched areas, air-jet spun yarns and silicone resin treatments help minimize fuzzing
3. Seat Friction Simulation Test
We tested SzoneierFabrics’ automotive acrylic seat insert fabric on a seat rub machine:
- 50,000 rubs with standard denim
- No fiber breakage
- Pilling score: 4
- Color retention: ΔE <1.5
4. Best Practices to Improve Durability
Enhancement | Function |
---|---|
High-twist yarns | Reduce surface fuzz and abrasion damage |
Anti-pilling finish | Maintains visual quality over time |
Coated backings | Adds structure and edge protection |
Compact weaves (e.g., dobby or twill) | Improve friction resistance |
One South American vehicle brand used polyester previously and reported customer dissatisfaction after just 6 months (seam wear, color fade). They switched to acrylic-blend door trims from SzoneierFabrics with:
- 35% lower complaint rate
- Better retention in sunlight-heavy regions
- Lower maintenance needs in ride-share fleets
Which Automotive Interior Components Commonly Use Acrylic-Based Fabrics?
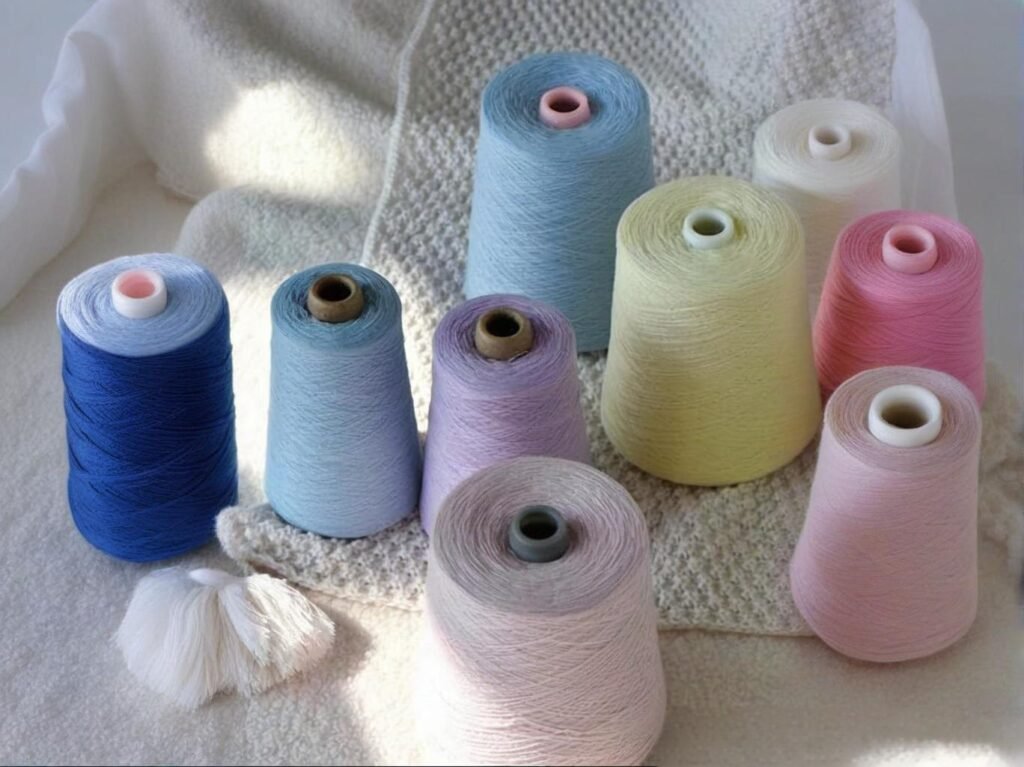
Acrylic-based fabrics are commonly used in vehicle interiors for seat inserts, door panels, headliners, C- and D-pillar trims, dashboard covers, sunshades, and rear shelf decks due to their UV stability, visual appeal, and tactile comfort.
Where and Why Acrylic Fits in Modern Car Interiors
1. Common Application Areas
Interior Component | Why Acrylic Is Used |
---|---|
Seat Centers/Inserts | Soft hand feel, anti-pilling, breathability |
Door Panels | Durable, fade-resistant, customizable textures |
Roof Liners | Noise dampening, wrinkle-free drape |
Pillar Trims | UV-exposed vertical areas require high colorfastness |
Rear Parcel Shelves | Constant sunlight contact; solution-dyed acrylic excels |
Dash Covers | Heat-resistant, glare-dampening if treated |
Sun Visors | Lightweight, foldable, stable in hot environments |
2. Application Examples by Material Type
Acrylic Type | Ideal Application |
---|---|
Solution-dyed woven acrylic | Door panels, sun visors, parcel shelves |
Brushed acrylic knit | Headliners, roof trims, C/D-pillar wraps |
Acrylic-polyester blend felt | Under-seat padding, acoustic liners |
Coated acrylic (PU back) | Seat backs, kick pads |
3. Performance Priorities by Area
Area | Key Requirements | Acrylic Fit? |
---|---|---|
Upper panels | UV stability, cleanability | ✅ Yes |
Seating zones | Pilling resistance, softness, wear rating | ✅ With finish |
High-touch points | Odor control, anti-static, color retention | ✅ Treated variants |
Hidden liners | Cost-efficiency, moderate thermal protection | ✅ Blends suitable |
4. Customization Capabilities with Acrylic
- Embossed textures for a luxury look
- Digital printing or jacquard weave for branding or interior themes
- Perforation-ready for breathability in sports models
SzoneierFabrics Case Insight: A Japanese OEM ordered custom jacquard-woven acrylic upholstery for an electric SUV’s front seat panels. The result:
- Rich texture with subtle branding
- Maintained shape and color over 18 months of endurance testing
- Passed SAE J2412 abrasion test with minimal wear
Do Acrylic Textiles Meet Industry Standards and Safety Certifications?
Yes—acrylic textiles can meet key automotive interior standards including abrasion resistance (ISO 12947), colorfastness (ISO 105), flammability (FMVSS 302), and UV performance (SAE J2412/J1885) when properly treated and manufactured to spec.
Testing and Compliance Requirements for Acrylic in OEM Projects
1. Safety and Performance Standards
Standard/Test | Purpose | Acrylic Compliance |
---|---|---|
FMVSS 302 | Flammability of interior materials | ✅ Modacrylic or coated |
ISO 105-B02 | Colorfastness to light | ✅ Grade 5–6 achievable |
ISO 12947 | Abrasion (Martindale) | ✅ 30,000+ cycles w/ blend |
SAE J2412/J1885 | UV aging and exposure simulation | ✅ Excellent results |
OEKO-TEX® Standard 100 | Chemical safety and skin contact | ✅ If certified supplier |
REACH/ROHS Compliance | Environmental safety in EU markets | ✅ Szoneier complies |
2. Flame Retardant Options
Acrylic Type | Flammability Rating |
---|---|
Standard Acrylic | Passes only when backed or blended |
Modacrylic Blend | Self-extinguishing, FMVSS 302 pass |
Acrylic with FR Coating | Meets most interior compliance |
3. Additional Requirements for Export Vehicles
- VOC emissions under control (ISO 12219)
- Formaldehyde limits (ISO 14184)
- Fogging resistance for dashboards (SAE J1756)
4. What OEM Procurement Teams Look For
Evaluation Area | Must-Have Factors |
---|---|
Durability | ≥25,000 abrasion cycles, Grade 4 pilling |
Aesthetics | Customizable weave/dye options |
Safety | FMVSS 302 or equivalent certification |
Environmental | OEKO-TEX / REACH-compliant |
Technical Support | Consistent spec sheet, tolerance control |
SzoneierFabrics Certification Snapshot:
- ✅ ISO 9001 Quality Management
- ✅ ISO 14001 Environmental Management
- ✅ OEKO-TEX® for all acrylic yarn sources
- ✅ In-house flammability and Martindale testing
- ✅ 7–10 day sampling with full lab data on request
How Can Finishes and Blends Enhance Acrylic Performance in Automotive Applications?
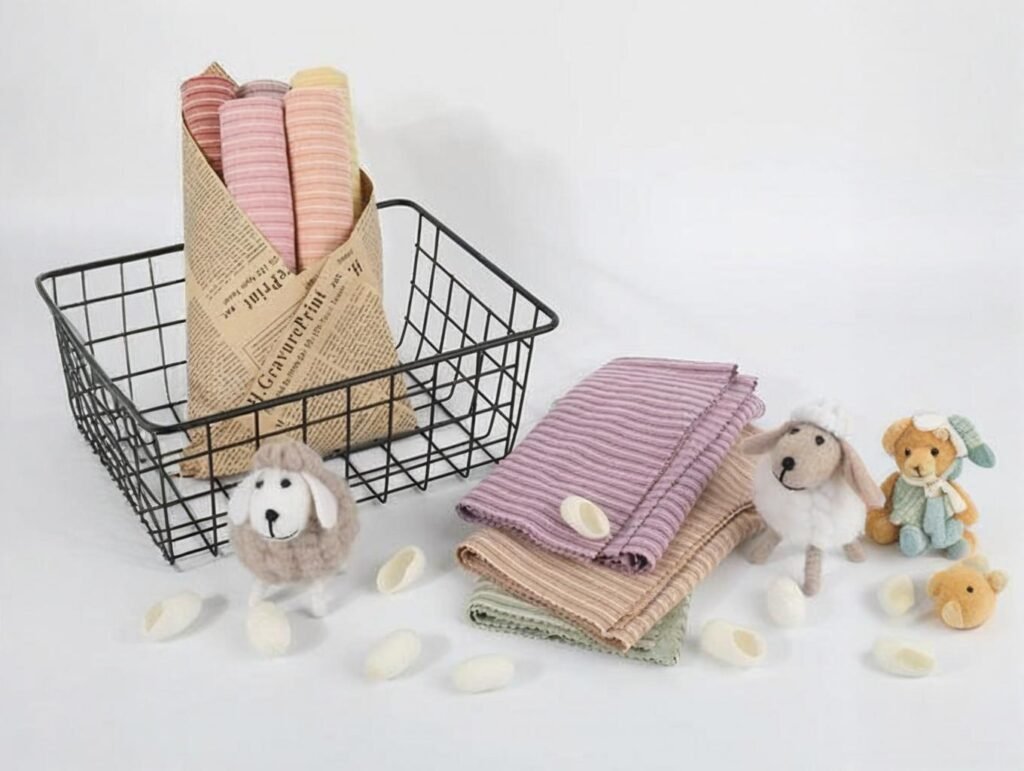
Finishes and fiber blends significantly enhance acrylic’s performance in automotive interiors by improving flame retardancy, abrasion resistance, pilling control, antistatic behavior, and moisture management—making it suitable for both economy and premium segments.
The Science of Functionalizing Acrylic for OEM Standards
1. Common Functional Finishes
Finish Type | Performance Benefit | Recommended For |
---|---|---|
Anti-pilling resin | Prevents fuzz and wear from repeated friction | Seat inserts, door trims |
Flame retardant (FR) | Enables FMVSS 302 compliance | Headliners, seat backs, paneling |
Anti-static finish | Reduces lint and improves user comfort | Headrests, armrests |
UV stabilizer coating | Boosts solar resistance beyond base polymer | Rear shelves, dashboards |
Water and oil repellent | Guards against stains and sweat | Steering wheel wraps, seat edges |
Silicone softeners | Adds luxury hand-feel and wrinkle resistance | Premium vehicle interiors |
2. Strategic Fiber Blends
Acrylic Blend | Key Benefits | Automotive Applications |
---|---|---|
Acrylic + Polyester | Increases abrasion resistance and structure | Seats, door panels |
Acrylic + Nylon | Enhances tensile strength and pilling control | Floor mats, trunk linings |
Acrylic + Modacrylic | Achieves flame-retardant standards | Headliners, seat foam covers |
Acrylic + Spandex | Adds stretch for shaped components | Fitted visors, console wraps |
3. Yarn & Weave Enhancements
- Air-jet spun yarns → Less pilling, more uniform surface
- High-twist yarns → Increased resistance to abrasion
- Warp-knitted structures → Greater dimensional stability
- Dobby/twill weaves → Texture customization with structural benefits
4. Case Study – Luxury Interior Launch
A German EV brand sought to replace real wool with a low-maintenance, fade-resistant, vegan material. SzoneierFabrics provided:
- 70% acrylic / 30% polyester jacquard
- Anti-static + anti-pilling resin finish
- Brushed backing for added insulation
Outcome: Material passed QUV 2000h, FMVSS 302, and achieved a 4.8/5 consumer touch rating during interior trials.
How Can Buyers Source Custom Automotive Acrylic Fabric from Reliable Manufacturers?
B2B buyers should source automotive-grade acrylic textiles from certified manufacturers offering full specification control, finish customization, in-house testing, global compliance documentation, and MOQ flexibility. Sampling and technical support are key.
A Step-by-Step Sourcing Guide
1. Define Technical Requirements
Parameter | Example Values |
---|---|
GSM Range | 180–350 gsm depending on use case |
Abrasion (ISO 12947) | ≥25,000 cycles (door panels), ≥40,000 (seats) |
UV Resistance (ISO 105-B02) | Grade ≥5 for high-sun areas |
Pilling (ISO 12945) | Grade ≥4 |
Flame Retardancy | FMVSS 302 pass or equivalent |
2. Ask for Sample Swatches with Lab Reports
- Test look and feel under natural light
- Conduct small-scale abrasion and UV fade tests
- Confirm batch-to-batch consistency from supplier
3. Choose a Partner Offering:
Feature | Why It Matters |
---|---|
Yarn-to-finish traceability | Better defect control + material trust |
Rapid sampling (within 7 days) | Accelerates design validation |
Custom weaving & finishing | Aligns with brand and functional needs |
Global shipping and compliance | Reduces logistics delays |
MOQ flexibility | Enables pre-launch or limited-edition runs |
4. Sourcing Tip: Pre-Approve Multiple Finishes
- For mass projects, consider both budget and premium finish versions
- Validate across vehicle models, trim levels, or markets
Why Work With SzoneierFabrics:
- ✅ 18+ years of experience in automotive fabric development
- ✅ Custom solution-dyed acrylic, modacrylic, and blend options
- ✅ In-house performance testing: Martindale, QUV, pilling, FMVSS 302
- ✅ OEKO-TEX®, REACH, ISO-certified supply chain
- ✅ MOQ as low as 50 meters, with capacity to scale to 50,000+ meters
- ✅ 7-day sample development with real usage simulation reports
Contact SzoneierFabrics to Develop Custom Acrylic Automotive Interiors
Whether you’re building next-gen EV interiors, economy fleet upgrades, or luxury trims—SzoneierFabrics delivers textile solutions that combine durability, performance, and design precision.
Start your custom sourcing journey today:
From fiber blending to flame testing—we make acrylic work for your car interiors.