How Much Does It Cost to Manufacture Denim Jeans?
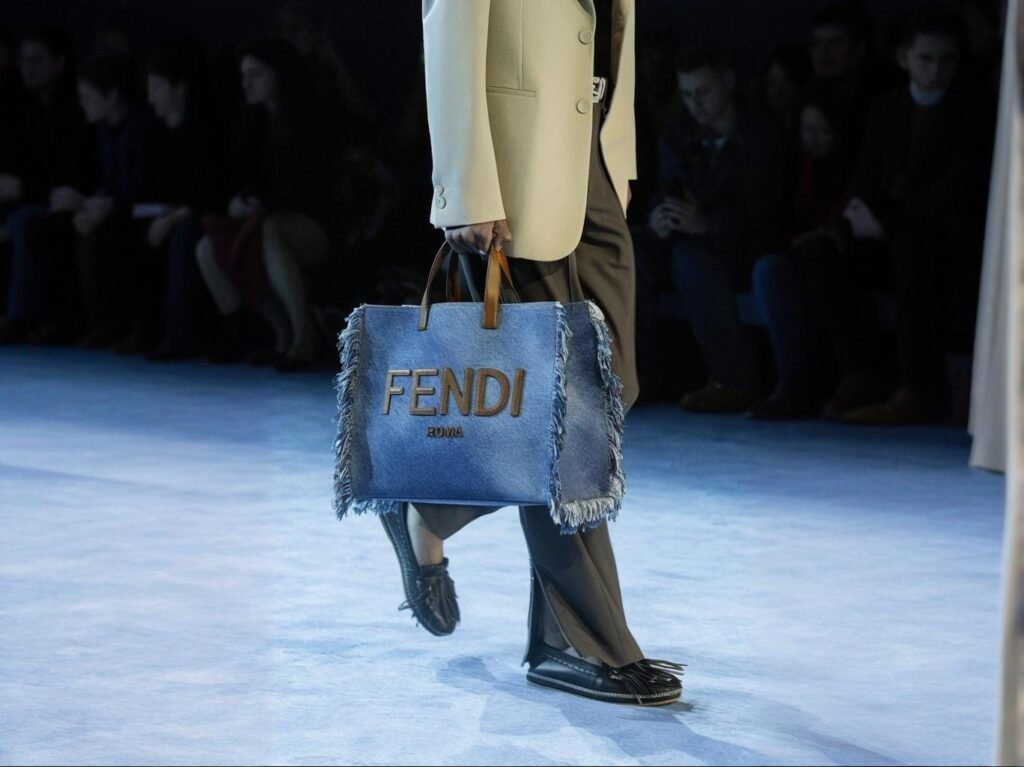
In the world of fashion manufacturing, few products are as universally worn — yet variably priced — as denim jeans. For B2B buyers, sourcing managers, and private label startup founders, understanding the true cost of producing denim jeans isn’t just about fabric or stitching; it’s about balancing quality, branding, volume, sustainability, and global logistics. The average manufacturing cost of denim jeans ranges from $6 to $30 per unit depending on fabric quality, country of origin, labor costs, order volume, and branding specifications. Key cost components include denim fabric, trims, labor, finishing, washing, and freight.
But here’s the catch: Two pairs of jeans can look identical to the untrained eye — yet one might cost 3x more to manufacture due to ethical sourcing, sustainable washing processes, or advanced finishing techniques. That’s why knowing the why behind the numbers is critical.
Let’s unpack the denim cost structure through a real story: A startup in California sourced $9 jeans from Bangladesh for their entry-level product line. They later launched a $22 pair using Turkish selvedge denim, targeting conscious consumers — and doubled their profit margin due to brand value. This contrast reveals how pricing reflects more than production; it reflects positioning.
So, what exactly goes into manufacturing denim jeans — and how do the numbers play out? Let’s dive in.
1. What Are the Main Cost Components in Denim Jeans Manufacturing?
The total cost of manufacturing denim jeans is made up of several key components: denim fabric, labor, trims (buttons, zippers), washing/finishing, overhead, and logistics. Fabric and labor typically account for 60–70% of the total unit cost.
Key Denim Production Cost Breakdown
1.1 Fabric Cost: The Biggest Slice of the Pie
- Basic denim (non-stretch): $1.5–$2.5 per yard
- Premium denim (selvedge/stretch/sustainable): $3.5–$8.5 per yard
- Average consumption per jeans: 1.3 to 1.6 yards
- Fabric cost per unit: $2–$12+
Fabric Type | Price per Yard (USD) | Avg. Usage (Yards) | Cost per Jeans |
---|---|---|---|
Basic cotton denim | $1.80 | 1.4 | $2.52 |
Turkish stretch denim | $5.50 | 1.6 | $8.80 |
Japanese selvedge denim | $7.80 | 1.5 | $11.70 |
1.2 Labor Cost: Varies by Region
- Bangladesh/Pakistan: $0.80–$1.50 per jeans
- China/Vietnam: $1.50–$3.00
- Mexico/Turkey: $2.50–$4.00
- Italy/USA: $5.00–$8.00
1.3 Trims and Hardware
- Includes rivets, waistband button, zipper, brand patch, thread, labels
- Total trim cost: $0.60–$2.50 per unit depending on customization
1.4 Washing and Finishing
- Basic enzyme wash: $0.50
- Heavy stone wash or laser finishing: $1.00–$3.00
1.5 Overhead and Packaging
- Cutting room, factory overheads, admin, packaging: $0.70–$2.00
1.6 Logistics and Duties
- Freight and customs (for export buyers): $0.50–$4.00 per unit depending on destination
Case Study: A U.S. wholesaler orders 5,000 jeans/month from India. Using mid-range fabric and semi-automated production, their unit cost breakdown is:
- Fabric: $4.20
- Labor: $2.10
- Trims: $1.20
- Washing: $1.00
- Packaging + Overhead: $1.00
- Freight + Duties: $1.50
- Total landed cost: $11.00
2. How Does Fabric Quality Affect the Cost of Producing Denim Jeans?
Higher-quality denim significantly increases manufacturing costs due to the use of premium cotton, specialty weaves like selvedge, and sustainable practices such as organic farming or low-impact dyeing.
The Fabric Factor in Denim Pricing
2.1 Fabric Composition: Cotton vs Blends
- 100% cotton denim is cheaper but may lack stretch.
- Cotton-spandex blends add 10–20% to the cost.
- Organic cotton increases fabric price by 15–30%.
Fabric Type | Price/Yard | Stretch | Sustainability Label | Common Use Cases |
---|---|---|---|---|
Regular cotton denim | $2.00 | No | None | Budget jeans |
Cotton-elastane blend | $3.50 | Yes | No | Skinny jeans |
Organic stretch denim | $5.20 | Yes | GOTS Certified | Eco-conscious |
Recycled cotton denim | $4.80 | Slight | GRS Certified | Sustainable line |
2.2 Selvedge vs Non-Selvedge Denim
- Selvedge denim requires old shuttle looms and slower production (adds $3–$7 per pair).
- Preferred for premium and Japanese-style jeans.
2.3 Dyeing and Finish Techniques
- Traditional indigo dye: cheaper, less eco-friendly.
- Natural or rope-dye methods: costlier but valued in slow fashion.
Expert Insight: A European private label jeans brand switched to GOTS-certified Turkish denim, increasing fabric cost by 38% — but their retail price jumped from €49 to €89, appealing to eco-conscious Gen Z consumers. Profit margins still grew.
2.4 Market Positioning
- Budget jeans (e.g., Walmart, Primark): lower fabric cost to maintain sub-$10 production cost.
- Mid-range brands (e.g., Levi’s, Lee): mix of quality and cost (~$10–$18/unit).
- Premium niche brands (e.g., Naked & Famous): $20–$35 per unit fabric+labor cost, selling at $120+.
3. Which Countries Offer the Lowest Manufacturing Costs for Denim Jeans?
Countries like Bangladesh, Pakistan, and India consistently offer the lowest denim jeans manufacturing costs due to low labor rates, government subsidies, and well-established denim production ecosystems.
Global Cost Comparison by Country
3.1 Labor Cost Benchmarks by Country Labor is a critical driver of cost. Here’s a snapshot of average labor rates for denim production:
Country | Avg. Labor Cost per Jeans | Avg. Monthly Wage in Apparel Sector |
---|---|---|
Bangladesh | $0.90–$1.30 | $95–$110 |
Pakistan | $1.00–$1.50 | $120–$140 |
India | $1.50–$2.10 | $140–$160 |
Vietnam | $1.80–$2.50 | $180–$220 |
China | $2.50–$3.50 | $250–$350 |
Turkey | $3.50–$5.00 | $400–$500 |
Mexico | $4.00–$5.50 | $450–$550 |
USA | $6.00–$9.00 | $1,500–$2,000 |
Italy | $8.00–$12.00 | $2,000–$2,500 |
3.2 Infrastructure and Industry Maturity
- Bangladesh: Over 400 denim mills and global B2B buyers like H&M, C&A, and Primark.
- Pakistan: Strong in spinning and weaving; best for high-volume, low-cost jeans.
- Turkey: Fast-fashion-friendly; nearshoring advantage for EU.
- China: Still dominant in tech-driven and mid-high range denim manufacturing.
- Mexico: Ideal for U.S. buyers due to USMCA agreement and short lead times.
3.3 Trade Agreements and Tariffs
- USMCA, GSP+, and RCEP lower import duties.
- For U.S. buyers, Mexico offers duty-free access.
- For EU buyers, Turkey benefits from the EU–Turkey Customs Union.
Case Example: A U.K. brand shifted its production from China to Pakistan, cutting per-unit costs from $14 to $9 while keeping fabric quality constant. However, lead time increased by 8 days — a trade-off that needed inventory strategy adjustment.
4. What Is the Average Cost to Produce One Pair of Denim Jeans by Region?
Average denim manufacturing costs range from $6–$10 in South Asia, $10–$15 in East Asia, and $15–$25 in Western countries. Costs vary based on wage levels, material sourcing, washing complexity, and order size.
Regional Denim Cost Insights
4.1 South Asia (Bangladesh, Pakistan, India)
- Avg. Unit Cost: $6–$10
- Fabric Source: Often local
- Best For: Bulk low- to mid-tier denim orders
Component | Bangladesh (USD) | Pakistan (USD) | India (USD) |
---|---|---|---|
Fabric | $2.00 | $2.10 | $2.50 |
Labor | $1.00 | $1.20 | $1.80 |
Trims | $0.80 | $0.90 | $1.00 |
Washing | $0.80 | $0.70 | $1.00 |
Total Cost | $4.60–$6.60 | $4.90–$7.00 | $6.30–$8.50 |
4.2 East and Southeast Asia (China, Vietnam, Cambodia)
- Avg. Unit Cost: $10–$15
- Fabric Sourcing: Often higher-grade Chinese or imported
- Best For: Private label brands with higher customization
4.3 Europe and North America
- Avg. Unit Cost: $15–$30
- Labor Cost Impact: High — but mitigated by smaller batch quality control and faster delivery
- Best For: Premium & sustainable niche brands
Region | Avg. Cost | Strengths |
---|---|---|
Turkey | $11–$16 | Fast shipping to EU, skilled labor |
Mexico | $13–$18 | Nearshoring for U.S., high efficiency |
USA | $18–$25 | Ethical labor, “Made in USA” branding |
Italy | $22–$30 | Artisan denim, high-end fashion |
4.4 What Impacts Regional Cost Beyond Labor?
- Currency fluctuations
- Energy and water costs
- Environmental compliance fees
- Factory automation (especially in China and Turkey)
Buyer’s Insight: One Scandinavian buyer shared that producing 3,000 jeans in Turkey cost €13 per unit (delivered), compared to €9 in Pakistan. However, Turkish production cut their lead time by 50% — a critical edge during fashion season drops.
5. How Do MOQ and Order Volume Influence Per-Unit Denim Production Costs?
The higher the order volume, the lower the per-unit cost due to economies of scale, bulk purchasing discounts, reduced machine downtime, and more efficient resource allocation. MOQs also determine access to certain factories or price tiers.
MOQ & Volume Cost Dynamics in Denim Production
5.1 Understanding MOQ in the Denim Industry
- Typical factory MOQs: 500–3,000 pcs per style
- For fully custom jeans: MOQs can start at 1,000 pcs per wash/style
- Low MOQ production (below 300 pcs): Often higher cost per unit due to setup and waste
MOQ Tier | Avg. Cost/Unit | Notes |
---|---|---|
< 300 units | $18–$25 | High due to inefficiencies |
500–1,000 units | $10–$15 | Moderate discount, still flexible |
3,000–10,000 | $7–$10 | Economies of scale start to apply |
10,000+ units | $6–$8 | Best pricing, factory priority given |
5.2 Fixed Costs vs. Variable Costs Factories often charge for:
- Pattern making and grading
- Sample making (deducted from order cost)
- Machine setup (cutting tables, wash cycles, etc.)
These are spread over the quantity ordered — thus, with higher volumes, the fixed cost per piece is lower.
5.3 Real Buyer Comparison
- A Canadian startup ordered 200 units from China with custom branding and acid wash; their cost was $19/unit.
- When they reordered 1,500 pcs of the same style, cost dropped to $11.30/unit — a 41% reduction.
5.4 Negotiation Tip for B2B Buyers Many manufacturers will reduce MOQ if:
- You use in-stock denim fabrics
- You accept standard trims
- You consolidate styles (same wash, cut, or sizing)
5.5 How Volume Affects Trims and Freight
- Trims: Buying 10,000 zippers = 30% cheaper than 500 zippers
- Freight: FCL (Full Container Load) shipping is cheaper per unit than LCL (Less than Container Load)
6. What Role Does Labor Cost Play in the Denim Manufacturing Price?
Labor cost has a direct impact on the final unit cost of denim jeans — particularly for hand-intensive processes like stitching, embroidery, and washing. In low-wage countries, labor costs can be as low as 10–20% of total cost, while in high-wage nations it can exceed 40%.
Dissecting Labor Cost Realities
6.1 Labor-Intensive Tasks in Jeans Production
- Cutting
- Sewing (15–18 operations per jeans)
- Riveting & button setting
- Quality control
- Washing, distressing, laser, ozone
Operation | Avg. Time (mins) | Labor Cost in Bangladesh | Labor Cost in Italy |
---|---|---|---|
Sewing | 25 | $0.60 | $4.50 |
Washing | 10 | $0.25 | $1.50 |
Finishing | 15 | $0.40 | $2.00 |
Total Labor | ~50 mins | $1.25–$1.50 | $7.00–$8.00 |
6.2 Automation’s Impact on Labor Efficiency
- In China and Turkey, semi-automated stitching and laser finishing reduce manual labor time by 30–50%.
- Labor cost is still present, but output per worker increases.
6.3 Wage Trends in Key Manufacturing Countries
Country | 2015 Avg. Monthly Wage | 2023 Avg. Monthly Wage | % Increase |
---|---|---|---|
Bangladesh | $68 | $110 | +61% |
India | $110 | $160 | +45% |
Vietnam | $150 | $220 | +47% |
China | $320 | $450 | +40% |
6.4 Ethical Labor and Buyer Expectations Brands targeting eco-conscious consumers are expected to support fair labor practices. Some key certifications:
- SA8000
- WRAP
- Fair Trade Certified
Case Study: A U.S. luxury denim label working with a Los Angeles factory pays $9 per unit in labor. They market their jeans as “locally handmade by skilled workers” and sell at $200+. While unit cost is 4x higher than overseas options, their margin and brand story are significantly stronger.
6.5 Sourcing Strategy Tip Smart brands balance labor costs and ethics by:
- Producing basics in low-cost regions
- Outsourcing limited-edition or branded lines to higher-wage countries
7. Is It Cheaper to Produce Denim Jeans Domestically or Overseas?
It is generally cheaper to manufacture denim jeans overseas due to lower labor and operational costs, especially in South Asia. However, domestic production may offer advantages in shipping time, quality control, and ethical sourcing — which can offset higher unit costs.
Comparing Domestic vs. Offshore Denim Manufacturing
7.1 Total Cost Comparison: A Quick View
Factor | Overseas (e.g. Bangladesh) | Domestic (e.g. USA) |
---|---|---|
Labor | $1.00–$2.00 | $7.00–$10.00 |
Fabric | $2.00–$5.00 | $3.00–$6.00 |
Trims & Finishing | $1.00–$2.00 | $2.00–$3.00 |
Freight & Import Duty | $1.00–$3.00 | $0.00 |
Lead Time | 30–45 days | 7–15 days |
Avg. Total Cost/Unit | $6.00–$12.00 | $15.00–$25.00 |
7.2 Advantages of Overseas Production
- Mass production at lower costs
- More factory options and sourcing flexibility
- Larger labor force, higher capacity
7.3 Advantages of Domestic Manufacturing
- Faster response time to market demand
- Easier communication and design iteration
- Ethical labor transparency
- “Made in USA/Italy” label adds brand value
7.4 Risk Assessment
- Offshore: Quality control issues, shipping delays, tariffs
- Domestic: Higher cost, limited supplier base
Buyer Insight: A U.S. DTC jeans brand tested both models. Offshore production cost them $9.50 per pair, while domestic cost $21. However, with faster domestic restocking, they reduced warehousing needs and increased conversion rates for limited drops. Total ROI improved, despite higher unit cost.
7.5 Hybrid Strategy
- Basic SKUs: Offshore
- Premium/special edition SKUs: Domestic
- In-season fast response: Local factory
- Core line mass stock: Overseas partner
8. How Can B2B Buyers Reduce Denim Jeans Production Costs Without Sacrificing Quality?
B2B buyers can lower denim manufacturing costs by optimizing fabric selection, consolidating orders, simplifying design elements, leveraging existing supply chains, and negotiating bulk pricing — all without compromising product quality.
Smart Cost-Cutting Without Compromising Value
8.1 Optimize Fabric Sourcing
- Choose in-stock fabrics from suppliers to skip custom weaving lead times and added cost.
- Use cotton blends with low elastane content for stretch jeans — saves 10–15% on fabric cost.
8.2 Simplify Construction
- Reduce pocket stitch complexity
- Use bar-tack instead of rivets where possible
- Replace expensive embroidery with printed branding
Feature | Cost Impact | Alternative |
---|---|---|
Custom rivets | +$0.60 | Plain branded buttons |
Laser distressing | +$1.00–$2.00 | Basic enzyme washing |
Back leather patch | +$0.80 | Printed logo on fabric label |
8.3 Streamline Washing Processes
- Avoid multiple-stage washes
- Choose eco-washes that consume less energy and water
8.4 Leverage Supplier Relationships
- Build long-term partnerships with 1–2 core factories
- Repeat orders = reduced development and QC cost
8.5 Combine SKUs Across Styles Instead of ordering 1,000 pcs each of 3 SKUs, combine to 3,000 pcs of the same base pattern but change color or trim — most factories will quote better pricing for combined bulk.
8.6 Case Study: A Brand That Did It Right A mid-size UK label worked with a Turkish factory to:
- Use ready stock denim
- Switch from heavy stone wash to medium enzyme
- Cut back pocket embroidery
They reduced cost per unit from €14.80 to €11.20 — and used that savings to upgrade packaging and include recycled hangtags, increasing brand appeal and repeat orders.
In the competitive landscape of fashion manufacturing, cost control is just one piece of the puzzle. Understanding where your denim is made, how it’s made, and what decisions drive cost vs. value can make or break a private label strategy or B2B partnership.
At SzoneierFabrics, we help international buyers — from e-commerce entrepreneurs to fashion brands — manufacture high-quality denim jeans that fit their exact budget, branding, and sustainability goals.
We offer:
- Fabric customization with low MOQ
- Quick sampling and responsive communication
- Support for both small and large volume orders
- Transparent pricing with no hidden charges
Ready to start your denim production project? Contact us now to request a free quote, sample evaluation, or technical consultation tailored to your needs.
Let’s create denim that fits your vision — and your bottom line.
Can't find the answers?
No worries, please contact us and we will answer all the questions you have during the whole process of bag customization.
Make A Sample First?
If you have your own artwork, logo design files, or just an idea,please provide details about your project requirements, including preferred fabric, color, and customization options,we’re excited to assist you in bringing your bespoke bag designs to life through our sample production process.