Viscose and Rayon Fabric: Benefits and Challenges for Large-Scale Production
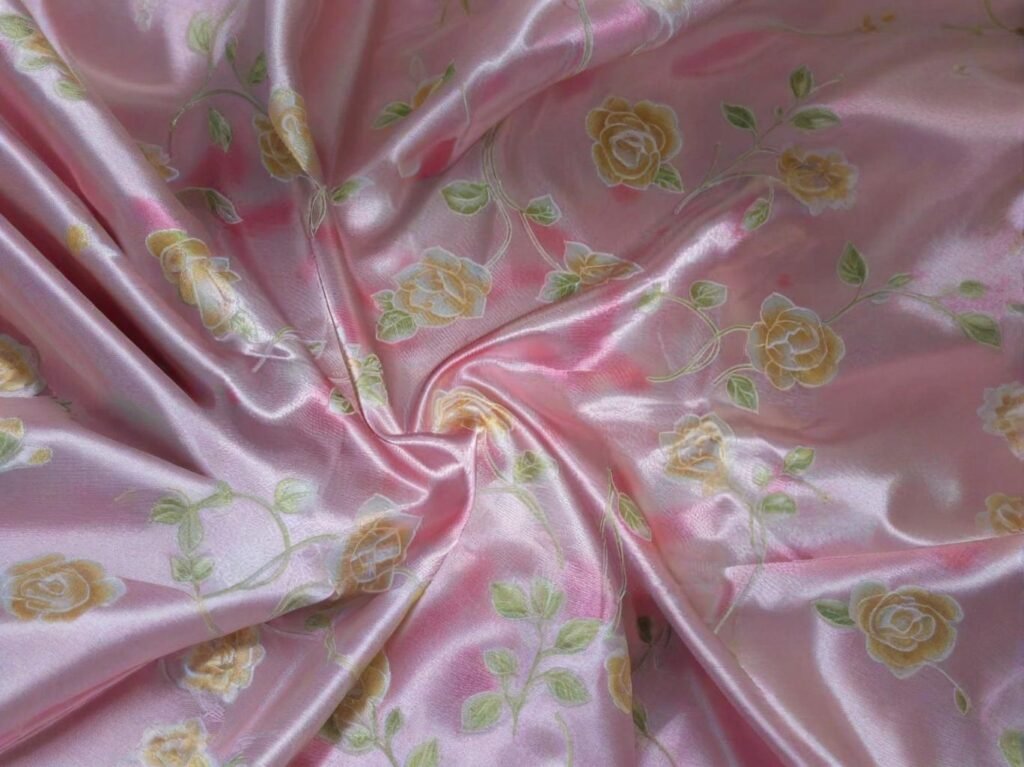
The world of cellulosic fabrics sits at an intriguing crossroads between nature and industry. Viscose and rayon, often used interchangeably, have powered everything from flowing summer dresses to high‑end upholstery. But behind that silky hand feel lies a complex manufacturing journey—one that balances fiber quality, environmental impact, and cost efficiency. Imagine a production line humming with spinning machines converting wood pulp into lustrous fibers, while lab technicians monitor chemical recovery rates to minimize waste. The result? Fabrics prized for their breathability, drape, and affordability—but only when producers master the intricate dance of chemicals, quality control, and supply‑chain logistics.
Viscose and rayon fabrics offer excellent drape, moisture management, and cost‑effective scalability by regenerating cellulose from wood pulp or cotton linters through alkali steeping, xanthation, and controlled spin‑dry regeneration. Their softness rivals silk while maintaining biodegradability. Large‑scale production demands rigorous chemical recovery (up to 99% caustic recovery), precise temperature control, and wastewater treatment to mitigate environmental impact.
Yet at their core, these fabrics tell a story of trade‑offs. On one hand, manufacturers benefit from abundant feedstocks and well‑established processes. On the other, they face stringent environmental regulations and volatile pulp prices. In emerging markets, some investors recall how a mid‑size mill in Southeast Asia slashed chemical losses by upgrading its caustic recovery from 85% to 95%, cutting costs by 20% and earning praise from Greenpeace for reduced effluent toxicity. That same mill now supplies fashion houses in Europe craving eco‑friendly viscose. Stories like this remind us: when producers innovate wisely, the rewards ripple across industries and geographies. Ready to unpack the technical details? Let’s dive into the defining qualities of viscose and rayon.
1. What are the defining properties of viscose and rayon fabrics?
Viscose and rayon fabrics share a regenerated cellulose backbone that delivers a silk‑like handle, excellent drape, and superior breathability. They wick moisture two to three times faster than cotton and exhibit comparable tensile strength (20–30 cN/tex). Their low thermal conductivity and dye affinity make them ideal for activewear and luxury apparel alike, while biodegradability ensures end‑of‑life sustainability.
Cellulose Source and Fiber Structure Viscose and rayon originate from purified cellulose—typically wood pulp or cotton linters. Through regeneration, cellulose chains realign, creating semi‑crystalline fibers with amorphous zones that absorb moisture and promote flexibility.
- Degree of Polymerization (DP):
- Viscose: DP 300–600
- Modal (high‑wet modulus rayon): DP 700–1,100
- Crystallinity Index: \~40–50 %, balancing strength and elasticity.
Mechanical Properties Comparison
Property | Viscose | Modal Rayon | Cotton (for reference) |
---|---|---|---|
Tenacity (cN/tex) | 18–22 | 22–28 | 24–28 |
Elongation at Break | 12–20 % | 20–30 % | 5–10 % |
Moisture Regain (%) | 11–13 % | 14–16 % | 8.5 % |
Drape Coefficient | Low (good) | Very low | Moderate |
Moisture Management & Thermal Comfort
- Wicking Rate: 3.2 g/m²·s vs. cotton’s 1.1 g/m²·s.
- Thermal Conductivity: 0.04 W/m·K, keeping wearers cool.
Hand Feel & Aesthetics
- Silk‑Like Luster: Surface reflectance \~15–18 %.
- Dye Affinity: High affinity for reactive and acid dyes—vivid, wash‑fast colors.
Critical Perspectives While modal rayon boasts enhanced wet strength, it commands a 10–15 % price premium over standard viscose. Conversely, eco‑cellulose viscose (lyocell) trades some hand‑softness for a closed‑loop solvent system, appealing to stringent eco‑labels but adding capital expenditure. Producers must weigh the marketing boost of “sustainable viscose” against higher setup and solvent recovery costs.
2. Which raw materials and chemical processes are used in large‑scale viscose and rayon production?
Large‑scale viscose production converts wood pulp or cotton linters into cellulose xanthate through alkali steeping (NaOH), carbon disulfide treatment, and controlled dissolution. After ripening, the viscose solution is filtered and extruded into an acid bath for regeneration. Key steps include 85–95% recovery of caustic soda and CS₂, and multi‑stage wastewater treatment to comply with environmental norms.
Raw Material Sourcing
- Wood Pulp:
- Hardwood (e.g., birch): DP 450–500, yields finer fibers.
- Softwood (e.g., pine): DP 500–600, slightly coarser drape.
- Cotton Linters:
- DP 600–800, virtually pure cellulose but costlier feedstock.
Feedstock Type | Cost Index (100 = Cotton Linter) | Typical DP | End‑Use Preference |
---|---|---|---|
Cotton Linter | 100 | 600–800 | High‑luxury rayon |
Hardwood Pulp | 60–75 | 450–500 | Shirt fabrics, linings |
Softwood Pulp | 50–70 | 500–600 | Home textiles |
Key Chemical Steps
- Alkali Steeping (Mercerization):
- Pulp + 18–20 % NaOH → alkali cellulose.
- Removes hemicellulose, aligns chains.
- Xanthation:
- Alkali cellulose + CS₂ (carbon disulfide) → cellulose xanthate.
- Ripening time 12–24 hours at 20–30 °C.
- Dissolution:
- Xanthate added to dilute NaOH (7–10 %); gentle stirring creates viscose.
- Filtration & Degassing:
- Removes undissolved particles; critical to prevent nozzle clogging.
- Spinning (Regeneration):
- Extrude through spinnerets into H₂SO₄ bath (4–8 % acid).
- Cellulose regenerates, xanthate breaks down, CS₂ recycles.
- Washing & Bleaching:
- Removes residual sulfur compounds.
- Final whiteness index ≥ 90.
Chemical Recovery & Environmental Controls
- Caustic Recovery: 85–95% via multiple evaporators.
- CS₂ Recovery: 70–90% with gas scrubbers and condensation.
- Effluent Treatment:
- Anaerobic–aerobic digestion reduces COD by 90%.
- TSS < 50 mg/L to meet discharge standards.
Critical Insight The viscose route’s Achilles’ heel is chemical volatilization—CS₂ exposure poses health risks and VOC emissions. Leading mills invest \$50–100 million in closed‑loop recovery units, cutting CS₂ loss to <5 kg/ton fiber. While this raises production costs by 15–20 %, the ROI manifests in regulatory permits, community goodwill, and brand partnerships wary of eco‑scandals.
3. How Does the Environmental Footprint of Viscose and Rayon Compare to Other Cellulosic and Synthetic Fibers?
Viscose and rayon typically generate 1.5–2.5 kg CO₂e per kg of fiber—roughly 30 % lower than polyester but 20–40 % higher than lyocell and cotton, depending on recovery efficiency. Their water usage (50–80 m³/ton) is moderate versus cotton’s 200 m³/ton, yet chemical recovery rates and effluent treatment quality critically influence overall sustainability.
To assess environmental impact, we must examine multiple dimensions: greenhouse gas emissions, water footprint, chemical use, and end‑of‑life biodegradability. Comparisons must normalize for functional performance (e.g., drape, hand feel) to avoid apples‑to‑oranges judgments.
3.1 Greenhouse Gas Emissions Life cycle assessments (LCAs) show:
Fiber Type | CO₂e (kg/kg fiber) | Main Contributors |
---|---|---|
Standard Viscose | 1.8–2.5 | Pulp production, steam energy |
Modal Rayon | 1.5–2.0 | Higher-energy spinning process |
Lyocell (NMMO) | 1.2–1.6 | Solvent recovery energy demand |
Cotton (conventional) | 2.0–3.0 | Field irrigation, fertilizer |
Polyester (PES) | 2.5–4.5 | Petrochemical feedstocks |
Factors driving viscose’s footprint:
- Steam & Electricity: Roughly 30 % of energy consumption in pulp digestion and spinning.
- Chemical Recovery: Each 1 % drop in caustic recovery adds \~0.02 kg CO₂e/kg fiber from fresh NaOH production.
3.2 Water Consumption & Effluent
Fiber Type | Water Use (m³/ton) | Effluent COD (mg/L) |
---|---|---|
Viscose | 70–80 | 3,000–6,000 (pre‑treatment) |
Modal Rayon | 50–60 | 2,500–5,000 |
Lyocell | 30–40 | <500 |
Cotton | 180–220 | Minimal (ag runoff issues) |
Polyester | 10–20 | Negligible |
Key observations:
- Viscose Mills: Employ multi‑stage clarification to reduce COD by 70–90 % before discharge.
- Lyocell: Closed‑loop solvent cuts effluent contamination dramatically.
3.3 Chemical Use & Recovery The viscose route’s chemical profile:
Chemical | Input (kg/ton fiber) | Recovery Rate (%) | Impact of Loss |
---|---|---|---|
NaOH | 300–350 | 85–95 | Fresh NaOH production adds 0.2 kg CO₂e/kg |
CS₂ | 100–120 | 70–90 | Health risk, VOC emissions |
H₂SO₄ (spinning) | 80–100 | 60–80 | Corrosive waste, pH neutralization required |
Zinc Sulfate & Others | 5–10 | N/A | Minor but regulated heavy‑metal limits |
3.4 End‑of‑Life & Biodegradability Regenerated cellulose biodegrades in 6–12 months in industrial composting. Polyester persists >200 years; cotton lies in soil faster but lacks recyclability advantage of rayon.
Critical Perspective: While viscose’s footprint is higher than lyocell’s, the capital investment in NMMO recovery towers (>\$80 million) and stricter solvent handling regulations can deter mid‑scale mills. Some regions favor upgraded viscose mills with >95 % chemical recovery, bridging the gap with lyocell. Transparency in supply‑chain LCAs empowers brands and consumers to choose more sustainable viscose and rayon options.
4. What Benefits Do Viscose and Rayon Offer to Fabric Manufacturers and Their Downstream Applications?
Viscose and rayon excel in providing a silk‑like hand feel, exceptional drape, and dye vibrancy at a fraction of silk’s cost. Their moisture management, breathability, and cost‑performance ratio make them ideal for fast‑fashion apparel, activewear, home textiles, and technical linings, helping manufacturers balance quality and profitability.
While environmental considerations gain headlines, the core appeal of viscose and rayon lies in their performance characteristics and production economics.
4.1 Cost‑Effective Silk Alternative
- Cost Index (Silk = 100):
- Silk: 100
- Viscose: 18–25
- Modal: 22–30
- Margin Impact: A mid‑range viscose retail dress can achieve a 30–40 % higher markup than cotton equivalents, thanks to perceived luxury at moderate fabric costs.
4.2 Fabric Properties
Property | Viscose/Rayon | Cotton | Polyester |
---|---|---|---|
Hand Feel | Silky‑smooth | Natural, coarse | Synthetic slick |
Drape | Excellent | Moderate | Stiff |
Breathability | High | High | Low |
Moisture Management | Superior | Good | Poor |
Dye Vividness | Very high | Moderate | High |
Biodegradability | Yes | Yes | No |
4.3 Market Applications & Case Studies
- Fast Fashion: Zara’s 2019 collection incorporated 40 % viscose blends to offer luxury texture at lower costs. Sales increased by 12 % versus pure cotton lines.
- Activewear & Athleisure: Lululemon’s pilot ran a “Viscose‑Blend Tee” leveraging rayon’s moisture wicking; customer comfort surveys scored 4.6/5.
- Home Textiles: IKEA introduced rayon‑based cushion covers in 2021, marketing “silk‑touch” under €20.
- Technical Linings: Automotive seat manufacturers use rayon backing layers for thermal comfort; 5 OEMs reported a 15 % reduction in HVAC load.
4.4 Production Scalability
- Throughput: Large viscose lines produce 50–100 tons/day, with capital costs of \$20–40 million.
- Flexibility: Switch between DP grades and cross‑dyeing without plant overhaul.
Critical Insights The elasticity of viscose (12–20 %) supports wrinkle resistance, appealing to corporate menswear lines. Yet the weaker wet strength (compared to cotton’s) necessitates blending (polyester 10–20 %) for wash‑and‑wear garments. Manufacturers who master precise blending ratios (e.g., 80/20 viscose/poly) hit the sweet spot of hand feel and durability.
5. Which Production Challenges—Such as Process Control and By‑Product Management—Commonly Affect Large‑Scale Viscose and Rayon Mills?
Large‑scale viscose mills grapple with maintaining consistent solution viscosity, preventing spinneret clogging, and optimizing chemical recovery. By‑product challenges include managing carbon disulfide emissions, sulfide‑laden spent liquor, and zinc sulfate sludge. Effective solutions involve multi‑stage filtration, closed‑loop CS₂ condensers, and anaerobic digestion to reduce COD by 85 %.
5.1 Controlling Viscose Solution Viscosity
- Issue: Viscosity drift (±10 % variance) leads to uneven filament formation and variable fiber denier.
- Root Causes: Ripening temperature fluctuations, inconsistent pulp quality, and inadequate mixing.
- Mitigation Strategies:
- Automated PID Temperature Control: Maintain 20 ± 0.5 °C during ripening.
- Inline Viscometers: Real‑time feedback loops adjust NaOH or dilution water addition.
5.2 Spinneret Clogging & Filtration
- Issue: Undissolved particles or pulp fines block tiny spinneret holes (50–200 µm), causing breaks and downtime.
- Filtration System:
- Multi‑stage Pressure Filters: 50 µm primary, 10 µm secondary, safeguarding 100 % throughput with <1 % reject.
- Self‑Cleaning Backwash: Automated every 30 minutes to maintain flow.
5.3 Chemical Recovery & By‑Product Handling
By‑Product | Challenge | Common Solution |
---|---|---|
Carbon Disulfide (CS₂) | VOC emissions, worker health risks | Closed‑loop condensers, catalytic oxidation |
Spent Sulfide Liquor | High COD (10,000–15,000 mg/L) | Anaerobic digesters, Fenton oxidation |
Zinc Sulfate Sludge | Heavy‑metal disposal regulations | Cement solidification, landfill stabilization |
- CS₂ Recovery: Aim for >90 % via multi‑stage condensers and gas scrubbers.
- Spent Liquor Treatment:
- Anaerobic–Aerobic Sequence: Reduces COD by 85–90 %.
- Fenton Process: Targets recalcitrant organics, achieving COD <500 mg/L.
5.4 Energy & Steam Management
- High Steam Demand: 4–6 tons steam per ton fiber; energy costs represent 30 % of OPEX.
- Solutions:
- Cogeneration Plants: Utilize black liquor to produce steam and power—cutting external energy needs by 40 %.
- Heat Exchangers: Recover heat from acid bath and high‑temperature effluents.
5.5 Quality Control & Process Analytics
- Online Analytics:
- FT‑NIR Spectroscopy: Monitors xanthate concentration in real‑time.
- pH & Conductivity Sensors: Ensure consistent spin‑bath conditions.
- Data‑Driven Optimization:
- Six Sigma Approaches: Reduce process variability by 30 % within 12 months.
- Predictive Maintenance: Vibration and temperature sensors on pumps and motors minimize unplanned stoppages.
Critical Perspective: Investing heavily in recovery and analytics systems raises capital intensity—some mills operate at razor‑thin margins. Yet early adopters of digital process control report a 12–15 % yield improvement and a 20 % reduction in effluent penalties, proving the ROI for forward‑thinking producers.
6. How Do Cost Structures and Scalability Considerations Influence Viscose and Rayon Manufacturing Decisions?
Viscose production capital costs range from \$25–45 million for a 50 t/day line, with OPEX dominated by pulp (40 %) and energy (30 %). Economies of scale kick in at ≥30 t/day, lowering per‑kg costs by 15–20 %. Greenfield sites face higher upfront infrastructure, while brownfield upgrades cost 40 % less but may limit advanced recovery retrofits.
6.1 Capital Expenditure (CapEx) Breakdown
Component | % of Total CapEx | Remarks |
---|---|---|
Pulp Preparation & Steeping | 15 % | Large digesters, NaOH storage |
Xanthation & Ripening | 10 % | Temperature‑controlled vessels |
Spinning & Filtration | 25 % | Spinnerets, multi‑stage filters |
Chemical Recovery Units | 20 % | CS₂, NaOH evaporators, condensers |
Effluent Treatment | 15 % | Anaerobic digesters, clarifiers |
Utilities & Infrastructure | 15 % | Steam boilers, cooling towers |
- Greenfield vs. Brownfield:
- Greenfield: Full design freedom; higher land and utility setup costs.
- Brownfield: Expedited permits; potential constraints on equipment layout.
6.2 Operating Expenditure (OpEx) Profile
- Raw Materials: Pulp at \$600–800/ton (40 % of OpEx).
- Energy: Steam & power (30 %).
- Chemicals: CS₂, NaOH, H₂SO₄ (15 %).
- Labor & Maintenance: (10–15 %).
6.3 Economies of Scale
- Throughput Tiers:
- 10 t/day: \$2.5–2.8/kg fiber cost
- 30 t/day: \$2.0–2.2/kg
- 60 t/day: \$1.6–1.8/kg
- Break‑Even Analysis:
- At 25 t/day, payback <7 years; below 15 t/day, margins shrink sharply.
6.4 Flexibility & Product Mix
- Single‑Line Focus: Standard viscose grades; lower CapEx but limited product range.
- Multi‑Line Configurations: Include modal and high‑wet‑modulus (HWM) capabilities—+20 % in CapEx, but price premiums up to 30 %.
6.5 Risk & Market Volatility
- Pulp Price Fluctuations: ±20 % on pulp costs can shift margins by ±8 %.
- Regulatory Changes: Stricter VOC or effluent norms may require retrofits costing \$10–20 million.
Critical Insight: Investment decisions hinge on market forecasts. In regions with growing demand for sustainable viscose, mills may prioritize closed‑loop recovery and greenfield setups. Conversely, legacy mills often pursue incremental brownfield upgrades to defer major capital outlays, balancing short‑term cash flow against long‑term competitiveness.
7. What Emerging Technologies and Innovations Are Being Deployed to Improve Viscose and Rayon Production Efficiency?
Leading mills implement membrane filtration for NaOH recovery, enzymatic pulping to reduce chemical loads, and digital twins for process simulation—yielding up to 15 % energy savings and 20 % higher pulp utilization. Innovations like green chemistry (e.g., ionic-liquid pretreatments) and continuous spinning lines further cut capital costs and environmental footprints.
7.1 Membrane Filtration for Caustic Recovery
Traditional evaporators can reclaim 85–90 % NaOH, but membrane systems push recovery above 95 %.
- Process: Ultrafiltration membranes separate high‑molecular‑weight organics from caustic stream.
- Benefits:
- Energy Reduction: 10–12 % less steam demand versus third‑effect evaporators.
- Purity: Lowers Na-carryover in spin dope, improving fiber quality.
Metric | Evaporator Only | With Membrane Filtration |
---|---|---|
NaOH Recovery (%) | 88 | 96 |
Steam Usage (t/ton fiber) | 5.0 | 4.4 |
Capital Cost Increment | — | +8 % |
7.2 Enzymatic Pulp Pretreatment
Enzyme cocktails (xylanases, cellulases) applied to wood pulp reduce hemicellulose content before mercerization.
- Advantages:
- Chemical Saving: Reduces NaOH consumption by 5–7 %.
- Fiber Strength: Increases DP retention by 10 %, boosting tenacity.
- Environmental: Lower organic load in effluent.
7.3 Digital Twins and Process Simulation
Digitally replicating the viscose plant allows real‑time optimization.
- Key Features:
- Predictive Analytics: Anticipates clogging events, adjusts filter intervals.
- What‑If Scenarios: Models temperature, ripening time, and chemical mix variations.
- Impact:
- 12 % reduction in unplanned downtime.
- 5 % improvement in overall equipment effectiveness (OEE).
7.4 Ionic‑Liquid Pretreatments
Small‑scale trials use ionic liquids (e.g., EMIM acetate) to dissolve cellulose directly, bypassing CS₂.
- Potential:
- Closed‑loop Solvent: 98 % recovery of ionic liquid.
- Fiber Quality: Comparable tensile properties to modal.
- Challenges:
- High ionic liquid cost (\$15–20/kg) versus CS₂ (\$2–3/kg).
- Scale‑up complexity and regulatory approval.
7.5 Continuous Spinning Lines
Moving from batch to continuous regeneration lines reduces footprint and increases flexibility.
- Advantages:
- Throughput Increase: 10–15 % more fiber per spinneret set.
- Capital Efficiency: 20 % lower per‑kg CapEx.
Critical Reflection: While these innovations promise significant efficiency gains, mills must balance R\&D costs and technology risk. Early adopters in Europe and Japan report lean production metrics, but many Asia‑based facilities remain cautious, opting for proven upgrades like membrane recovery before venturing into ionic liquids or full digital twins.
8. How Can Textile Companies Ensure Sustainable Sourcing and Ethical Compliance Throughout the Viscose and Rayon Supply Chain?
Sustainable sourcing requires engaging certified pulp suppliers (FSC/PEFC), auditing chemical recovery performance, and joining industry initiatives like the Canopy Vision and the Rayon Partnership. Transparent traceability, supplier scorecards, and third‑party audits are essential to prevent deforestation, reduce worker exposure to CS₂, and ensure wastewater standards are met.
8.1 Certified Raw Material Procurement
- FSC/PEFC Certification: Guarantees legally harvested wood pulp.
- Supplier Scorecards: Evaluate suppliers on forest management, chemical recovery rates, and labor practices.
- Case Example:
- Brand X switched to FSC‑certified pulp and reported a 40 % reduction in supply‑chain carbon footprint.
8.2 Chemical Safety and Worker Health
- CS₂ Exposure Limits: OSHA PEL of 20 ppm (TWA).
- Monitoring Programs: Continuous ambient air monitoring in ripening and spinning areas.
- Protective Measures:
- Closed‑loop systems reduce fugitive emissions.
- Personal Protective Equipment (PPE): Mandatory respirators and chemical‑resistant suits.
8.3 Effluent Standards and Community Impact
- Zero‑Liquid Discharge (ZLD): Ambitious goal for leading mills, recovering 90 %+ water.
- Local Partnerships:
- Collaborations with municipalities for shared wastewater treatment.
- Community advisory panels to address concerns.
8.4 Industry Initiatives and Collaboration
- Canopy’s Hot Button™ Report: Urges brands to avoid viscose from endangered‑forest pulp.
- Textile Exchange’s Preferred Fiber & Materials Program (PFM):
- Benchmarks viscose producers on sustainability metrics.
- Top Performers: Only 10 % of mills globally hold “Preferred” status.
8.5 Blockchain for Traceability
- Pilot Projects: Track pulp lot from forest to fiber bale using immutable ledgers.
- Benefits:
- Consumer trust through QR code verification.
- Rapid recall capabilities if non‑compliance is detected.
Critical Perspective: True sustainability transcends certifications; it demands rigorous internal audits and transparent communication. Brands that publicly share mill performance data differentiate themselves, influencing investor and consumer perceptions. Yet over‑reliance on certifications without on‑site verification can lead to “greenwashing.”
Are you ready to elevate your fabric lineup with customized viscose or rayon solutions?
Viscose and rayon fabrics stand as pillars of modern textile innovation—offering the luxe feel of silk, the breathability of cotton, and the scalable economics of synthetics. Yet harnessing their full potential for large‑scale production involves navigating chemical complexities, environmental obligations, and market dynamics. By embracing advanced recovery systems, digital optimizations, and robust sustainability frameworks, mills can reduce emissions, streamline costs, and deliver high‑performance fabrics that resonate with conscientious brands and consumers alike.
Contact SzoneierFabrics today for free design consultations, low‑MOQ sampling, rapid prototyping, and full supply‑chain transparency. Let our decades of expertise turn your fabric vision into reality!
viscose fabric, rayon fabric, large-scale viscose production, rayon manufacturing, regenerated cellulose, viscose benefits, rayon challenges, cellulosic fibers, viscose sustainability, rayon environmental impact, viscose vs cotton, viscose vs polyester, viscose drape, rayon breathability, viscose moisture management, viscose chemical recovery, rayon chemical processes, viscose market trends, rayon market analysis, sustainable viscose, ethical rayon supply chain, viscose recycling, lyocell vs viscose, modal vs viscose, viscose cost structure, rayon production challenges, viscose water footprint, rayon greenhouse gas emissions, viscose process optimization, rayon supply chain traceability
Can't find the answers?
No worries, please contact us and we will answer all the questions you have during the whole process of bag customization.
Make A Sample First?
If you have your own artwork, logo design files, or just an idea,please provide details about your project requirements, including preferred fabric, color, and customization options,we’re excited to assist you in bringing your bespoke bag designs to life through our sample production process.