Acrylic has quietly become a backbone of modern manufacturing, appearing in everything from high-end fashion to bulletproof windows. But few outside the industry truly understand what it is—or why it’s so widely used. At a time when sustainability, performance, and cost-efficiency are driving material choices across industries, acrylic stands out for its versatility, durability, and adaptability.
So, what is acrylic and why is it used in manufacturing? Acrylic is a synthetic polymer derived from acrylonitrile or related compounds, primarily used to create fabrics, plastics, coatings, and composites. It is favored in manufacturing due to its lightweight strength, UV resistance, moldability, and lower cost compared to glass, wool, or certain engineering plastics. From signage to textiles, automotive parts to packaging, acrylic offers high performance without the weight or fragility of traditional materials.
In the 1950s, DuPont branded it as “Orlon,” and since then, it has quietly become a staple in industries that need transparent panels, weather-resistant fabrics, or wool-like softness at scale. One case that highlights its power: NASA used acrylic windows in space shuttle canopies for durability in extreme environments. This level of performance trickles down today into everything from fashionwear to construction.
Let’s now explore what makes acrylic a go-to choice across sectors—and why B2B buyers are increasingly asking for it by name.
What Is Acrylic Material Made Of and How Is It Produced?
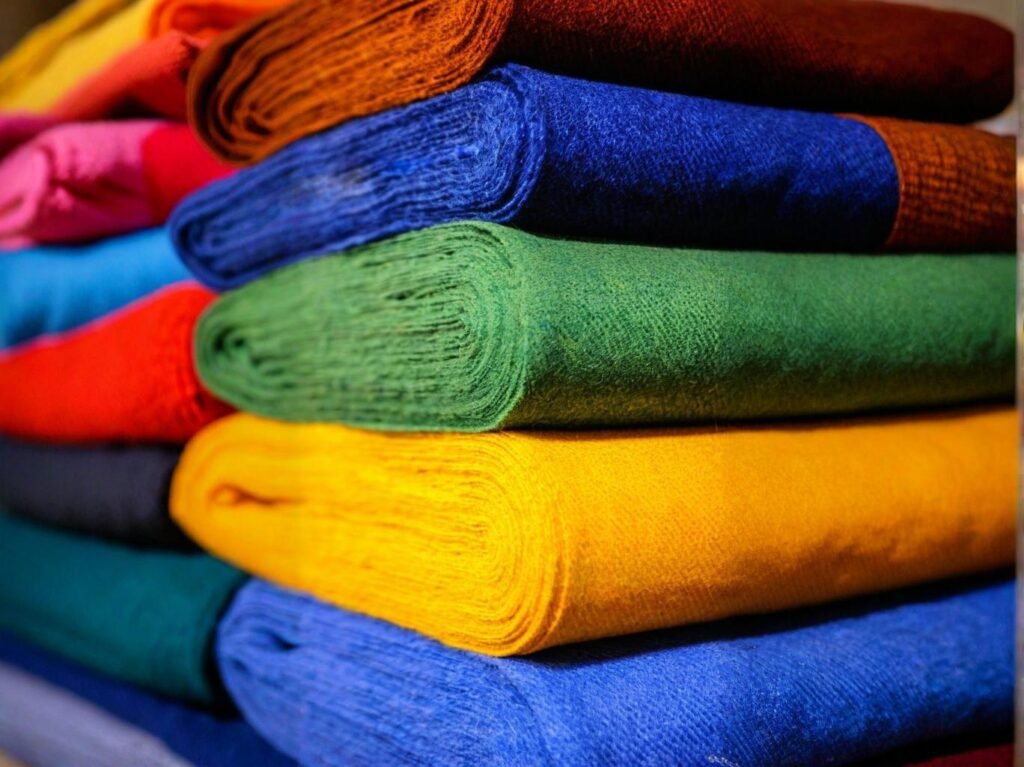
Acrylic is made from polymerizing acrylonitrile or methyl methacrylate, resulting in a lightweight yet durable thermoplastic or synthetic fiber. It can be engineered into both hard, glass-like plastics and soft, wool-like yarns depending on the formulation.
a) Key Raw Materials Used in Acrylic Production
Component | Description |
---|---|
Acrylonitrile | Core monomer used in the polymerization process. |
Methyl Methacrylate | Used in creating PMMA (commonly called acrylic glass). |
Initiators & Catalysts | Trigger polymerization reactions. |
b) Acrylic Fabric vs Acrylic Plastic: What’s the Difference?
- Acrylic fabric is used in textiles. It’s soft, warm, and often mimics wool.
- Acrylic plastic (often branded as Plexiglas or Lucite) is rigid, shatter-resistant, and often transparent.
c) Manufacturing Process Summary
- Polymerization: Monomers are reacted under heat and pressure to form polymers.
- Spinning (for textiles): Polymer is dissolved and forced through spinnerets to form filaments.
- Extrusion or Casting (for plastics): Melted polymer is molded or extruded into shapes.
d) Global Production Insight
According to a 2024 report by Grand View Research, the global acrylic fiber market size was valued at USD 5.9 billion and is expected to grow at a CAGR of 4.5% through 2030. Major producers include:
- China (Zhejiang, Jiangsu)
- India
- Japan (Mitsubishi Chemical)
- USA (Dow, Lucite International)
Why Do Manufacturers Prefer Acrylic Over Natural Fibers?
Manufacturers prefer acrylic over natural fibers like wool or cotton due to its lower cost, weather resistance, color retention, and ease of bulk production. Unlike natural fibers, acrylic doesn’t shrink, fade, or degrade quickly—making it ideal for outdoor, high-use, or color-critical applications.
a) Performance Comparison Table: Acrylic vs. Natural Fibers
Feature | Acrylic | Cotton | Wool |
---|---|---|---|
Cost | Low | Moderate | High |
UV Resistance | Excellent | Poor | Moderate |
Moisture Retention | Low (Fast-dry) | High | High |
Shrinkage Risk | Minimal | High | High |
Color Fastness | Excellent | Moderate | Low |
Maintenance | Easy | Moderate | Difficult |
b) Case Study: Outdoor Upholstery Manufacturer (USA)
A California-based patio furniture brand switched from cotton canvas to solution-dyed acrylic fabric in 2022. The result? 38% fewer product returns related to color fading and mildew. Sales increased by 19% after highlighting the material upgrade.
c) Why Acrylic Wins in Volume Manufacturing
- Acrylic yarns can be spun quickly and dyed uniformly, ideal for textile mills.
- Acrylic plastic sheets are easy to mold at low temperatures compared to glass.
- No dependency on agricultural cycles (unlike cotton or flax), making supply chains more predictable.
d) Critical Thinking: What’s the Trade-off?
- Acrylic is petroleum-based, which raises sustainability concerns.
- Natural fibers are biodegradable, while acrylic takes decades to break down.
- Solution? Blends—some brands mix acrylic with cotton for performance + eco-balance.
What Are the Different Types of Acrylic Used in Industrial Applications?
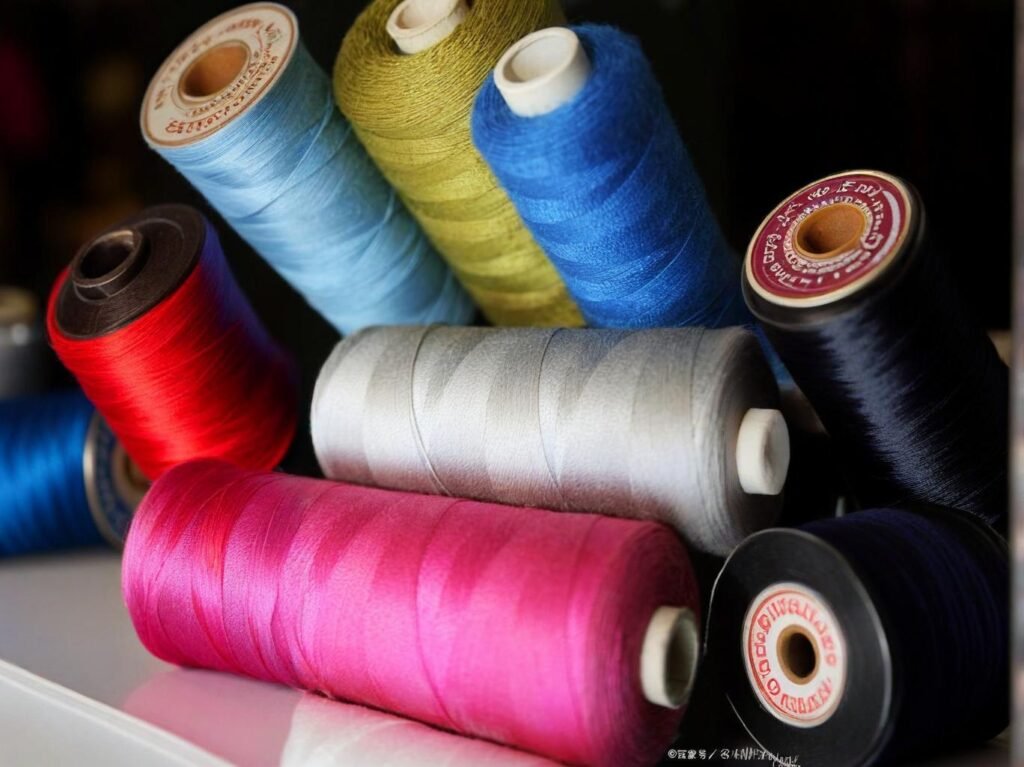
Acrylic comes in several grades and formulations—primarily acrylic plastic (PMMA), modacrylics, and acrylic fibers—each engineered to serve specific industrial needs. Whether you’re producing signage, outdoor fabrics, or safety barriers, selecting the right type is essential.
a) Major Acrylic Categories
Type | Key Features | Common Applications |
---|---|---|
PMMA (Polymethyl Methacrylate) | Rigid, transparent, shatter-resistant | Displays, windows, machine guards |
Acrylic Fibers | Soft, warm, wool-like | Apparel, blankets, upholstery |
Modacrylics | Flame-retardant, chemical-resistant | Protective clothing, wigs, filtration materials |
Cast Acrylic | Superior optical clarity, excellent for fabrication | Aquariums, illuminated signage |
Extruded Acrylic | Consistent thickness, cost-effective for large volumes | Retail displays, glazing |
b) Case Example: Acrylic vs. Polycarbonate for Shields
- A Texas-based construction equipment brand uses PMMA for cabin windows due to its 92% light transmittance and lower weight.
- Polycarbonate, while more impact-resistant, scratches easily without coating—PMMA stays clearer over time.
c) Modacrylic Spotlight: Fire Safety
According to NFPA standards, modacrylic blends meet UL94 V-0 flame retardancy, making them a preferred choice for:
- Firefighter station wear
- Industrial protective garments
- Arc-flash-resistant panels
d) Choosing the Right Acrylic
When sourcing, ask:
- What performance properties matter most (clarity, flexibility, heat resistance)?
- Is the acrylic intended for indoor or outdoor use?
- Does it need specific certifications (e.g., REACH, UL)?
This strategic selection ensures the material aligns with performance, cost, and compliance requirements.
How Does Acrylic Fabric Compare to Polyester and Nylon in Performance?
Acrylic is superior to polyester and nylon in warmth and UV resistance but falls behind in tensile strength and abrasion resistance. For outdoor textiles, acrylic often outperforms polyester in colorfastness, while nylon is preferred when durability is critical.
a) Performance Comparison Table
Feature | Acrylic | Polyester | Nylon |
---|---|---|---|
UV Resistance | Excellent | Good | Poor |
Abrasion Resistance | Moderate | High | Very High |
Moisture Wicking | Low | High | Moderate |
Thermal Insulation | High | Low | Low |
Color Retention | Excellent | Good | Fair |
Elasticity | Low | Moderate | High |
b) Use Case: Outdoor Cushions
A Florida outdoor furniture manufacturer conducted a side-by-side test in 2023:
- Acrylic cushions retained 92% of original color after 12 months of sun exposure.
- Polyester cushions retained 78%.
- Nylon cushions faded by 40%.
c) Critical Thinking: Is Acrylic Always the Best Choice?
- In marine environments, acrylic’s UV stability is an advantage.
- For sports apparel, nylon’s stretch and abrasion resistance outperform acrylic.
- Polyester offers a middle ground, balancing cost and performance.
d) Hybrid Blends: A Smart Compromise
Manufacturers often blend acrylic with:
- Polyester (to improve durability and reduce pilling)
- Cotton (to soften hand feel and enhance breathability)
This hybrid approach optimizes performance and aesthetics for target applications.
What Industries Commonly Use Acrylic for Manufacturing Products?
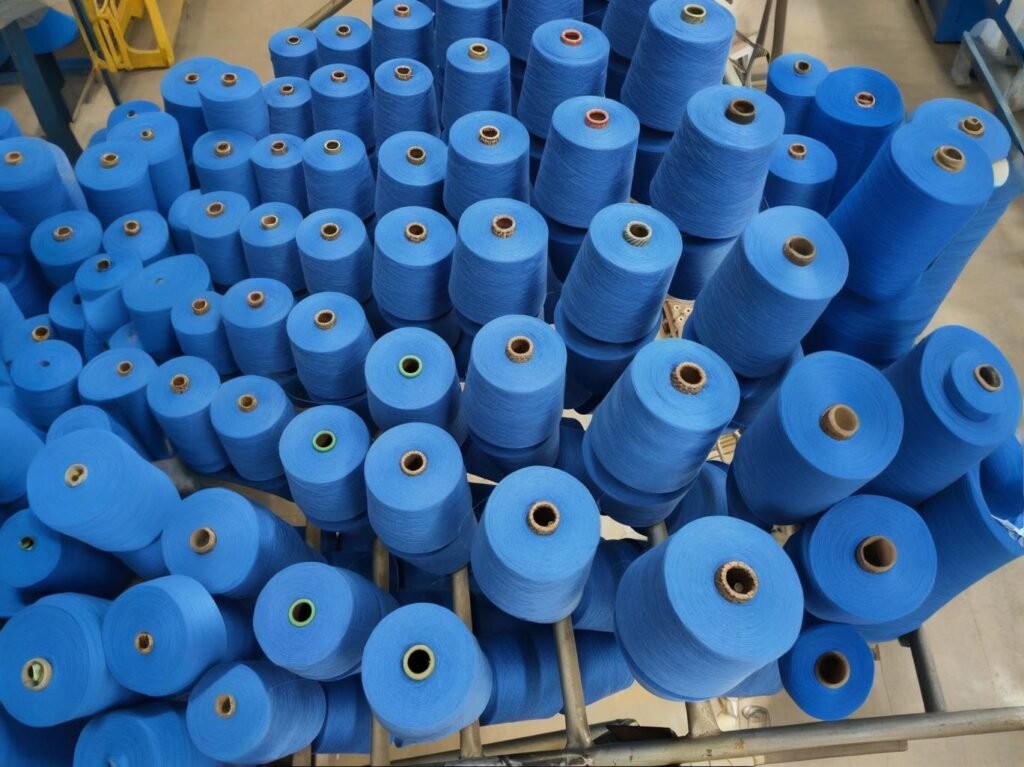
Acrylic is widely used across industries including textiles, automotive, signage, construction, healthcare, and consumer goods due to its adaptability, durability, and aesthetic appeal. Each sector leverages specific types of acrylic—from flexible yarns to rigid transparent sheets—for functional and cost-efficient production.
a) Industry Applications Table
Industry | Acrylic Form Used | Product Examples |
---|---|---|
Textile & Apparel | Acrylic fibers | Sweaters, socks, blankets, beanies |
Automotive | PMMA sheets | Headlamp covers, dashboards, windows |
Construction | Cast & extruded PMMA | Skylights, wall panels, signage, sanitary ware |
Signage & Display | Cast acrylic | Illuminated signs, POS displays, nameplates |
Healthcare | Clear PMMA & modacrylics | Incubators, lab equipment, flame-resistant gear |
Furniture | Acrylic fabrics, molded panels | Outdoor upholstery, modern furniture designs |
Retail Packaging | Transparent acrylic | Perfume boxes, luxury packaging windows |
b) Case Study: Signage Industry Boom
In 2024, global signage demand grew by 6.2%, with 42% of outdoor illuminated signs made from cast acrylic due to its:
- UV resistance
- Ease of CNC routing
- Weather durability for over 5 years
c) Emerging Sector: Acrylic in Healthcare
During the COVID-19 pandemic, acrylic barriers became ubiquitous. Now, PMMA is being used in:
- Medical cabinets
- Blood analyzers
- Dental instrument trays
d) Why B2B Buyers Love Acrylic
- Easy to laser-cut, mold, and print on
- Multiple finish options: matte, gloss, frosted
- Cost-effective substitute for glass or wool
- Available in custom colors and textures
Is Acrylic Material Durable Enough for Outdoor and Heavy-Duty Use?
Yes—acrylic is extremely durable for outdoor and heavy-duty applications, especially when solution-dyed or UV-stabilized. It resists color fading, moisture, mildew, and physical wear better than most synthetic alternatives, making it a staple in marine and commercial outdoor settings.
a) Durability Metrics of Outdoor Acrylic Fabric
Test Type | Acrylic (Solution-Dyed) | Polyester | Cotton |
---|---|---|---|
UV Exposure (1000 hrs) | 95% color retention | 78% retention | 40% retention |
Mildew Resistance | Excellent | Moderate | Poor |
Water Resistance | High (if treated) | Moderate | Low |
Tear Strength | Moderate to High | High | Low |
b) Case Study: Marine Canvas Fabrics
A yacht upholstery firm in New Zealand replaced polyester marine canvas with solution-dyed acrylic in 2021. After 2 years of exposure to saltwater and UV:
- Acrylic fabric retained over 90% of tensile strength
- No signs of mildew, and fading was minimal
- Maintenance time dropped by 32%
c) Structural Acrylic in Architecture
- Acrylic sheets used in transparent awnings and walls can last 10–15 years outdoors.
- PMMA is 17x stronger than glass yet half the weight.
- Leading brands apply anti-yellowing and anti-abrasion coatings, extending lifespan.
d) Critical Thinking: When Is Acrylic Not Ideal?
- In extremely abrasive environments, acrylic can scratch unless hard-coated.
- At temperatures above 90°C, acrylic may warp—making it less suitable for high-heat machinery enclosures.
- However, blending acrylic with other polymers (e.g., PC-acrylic co-extrusions) can solve this.
How Do You Identify High-Quality Acrylic for B2B Sourcing?
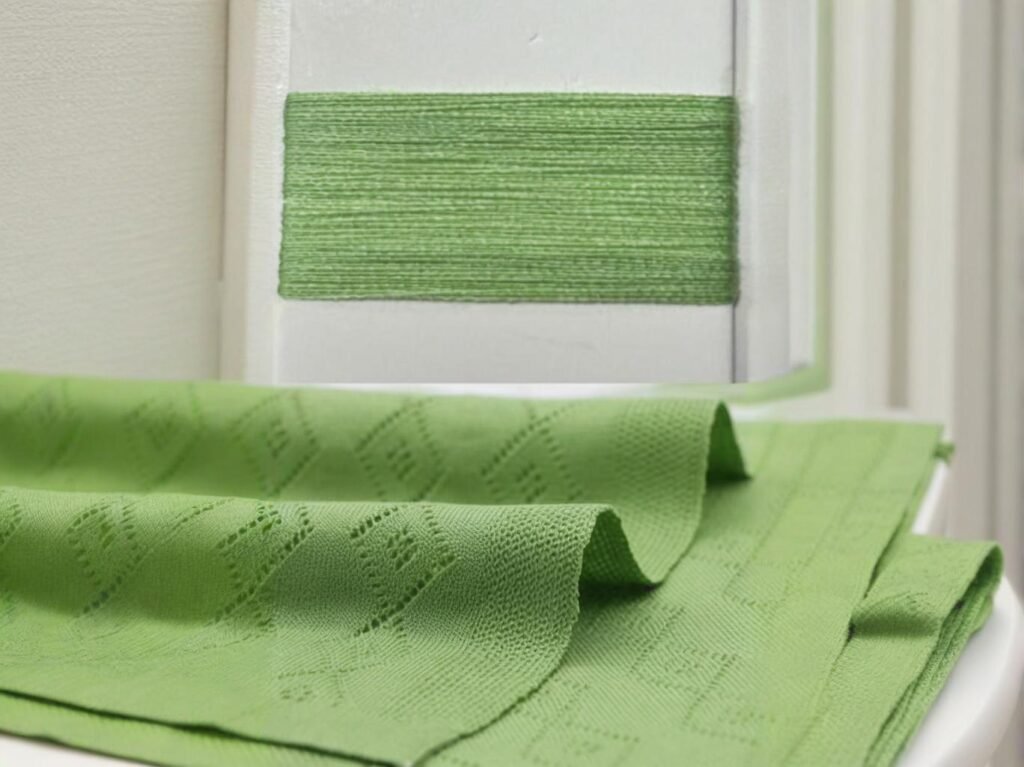
To identify high-quality acrylic, evaluate factors such as source resin purity, production method (cast vs. extruded), UV stabilization, clarity or color consistency, and compliance with certifications like REACH or ROHS. High-grade acrylic performs better in terms of strength, colorfastness, and durability—essential for bulk manufacturing and brand reputation.
a) Checklist for Evaluating Acrylic Quality in B2B Orders
Evaluation Criteria | What to Look For |
---|---|
Resin Purity | Virgin resin, not recycled (unless sustainability is prioritized) |
Production Method | Cast acrylic (higher optical clarity, better for machining) |
UV Stabilization | Additives or solution-dyed processes for outdoor performance |
Color Consistency | No streaks, yellowing, or fading under UV test |
Tensile & Impact Testing | Verified lab test reports from supplier |
Certification Compliance | REACH, ROHS, ISO 9001, ASTM standards |
Supplier Transparency | Full spec sheets, MSDS, quality control documents |
b) Case Example: Acrylic Sheet Buyer in Germany
A German industrial buyer sourcing acrylic panels for retail displays compared two vendors:
- Vendor A (China): REACH-certified, cast acrylic, high gloss, no optical distortion.
- Vendor B (India): Inconsistent thickness, slightly yellow tint, poor machining performance. Result: Vendor A’s products increased customer satisfaction by 23% after deployment.
c) Critical Tips for B2B Buyers
- Always request a sample batch before placing bulk orders.
- Review edge finish and surface smoothness under lighting.
- For fabrics, test for pilling, shrinkage, and hand feel.
d) Hidden Pitfalls to Avoid
- Extruded acrylic may be cheaper but tends to warp under machining stress.
- Low-cost “acrylic blends” sometimes contain fillers—always verify material composition with FTIR or DSC analysis if quality is critical.
What Are the Environmental Impacts and Recycling Options for Acrylic?
Acrylic is derived from petrochemicals, is non-biodegradable, and presents recycling challenges—but innovations like closed-loop recycling and bio-acrylics are emerging. Responsible sourcing, lifecycle planning, and blending strategies help reduce its environmental footprint in manufacturing.
a) Environmental Challenges of Acrylic
Concern | Explanation |
---|---|
Petrochemical Origin | Made from crude oil derivatives (e.g., methyl methacrylate) |
Non-Biodegradable | Can take 100+ years to decompose in landfills |
Microfiber Pollution | Acrylic textiles shed microplastics during washing |
Low Recycling Rates | Not commonly recycled in municipal systems |
b) Positive Developments
Innovation Type | Description |
---|---|
Closed-Loop Recycling | Mechanical or chemical recycling into new acrylic products |
Bio-Based Acrylics | Developed from renewable sources like corn or sugarcane (e.g., Bio-PMMA) |
Circular Economy Models | Acrylic offcuts reused for signage, arts, and packaging |
Blending for Longevity | Cotton-acrylic blends extend product life, reducing waste over time |
c) Sustainable Sourcing Case Study
SzoneierFabrics recently supplied a European outerwear brand with solution-dyed acrylic blended with organic cotton. The result:
- 35% reduction in water usage during dyeing.
- Extended product lifespan by over 18 months.
- Achieved OEKO-TEX® certification for textile safety.
d) What Can Buyers Do?
- Choose OEKO-TEX®, GRS, or Bluesign-certified acrylic fabrics.
- Ask for transparency on resin sourcing and post-industrial recycling.
- Prefer solution-dyed over surface-dyed acrylic (reduces effluent pollution).
At SzoneierFabrics, we understand that performance, compliance, and sustainability matter to modern B2B buyers. Whether you’re sourcing durable acrylic textiles for outdoor furniture or optical-grade acrylic sheets for displays, our team provides:
- 100% Quality Assurance
- Custom Production with Low MOQ
- Free Sampling & Design Support
- Short Lead Times for Global Orders
Ready to explore custom acrylic solutions? Contact us today for free samples, factory specifications, or a tailored quotation.