In today’s industrial world, the demand for performance fabrics is growing faster than ever. Whether you’re in construction, automotive, marine, or even outdoor advertising, one synthetic fabric continues to make its mark—acrylic. Often underestimated in the shadow of polyester or nylon, acrylic fabric offers a unique balance of durability, UV resistance, and affordability, making it an ideal material across various industrial applications.
Acrylic fabric is a synthetic textile made from polymerized acrylonitrile, widely used in industrial textiles due to its weather resistance, thermal insulation, and colorfastness. Its lightweight structure and strong tensile strength allow it to be used in harsh environments without breaking down or fading.
To illustrate its real-world impact, picture this: a premium awning manufacturer in Florida once shifted from cotton blends to solution-dyed acrylic fabric. The result? 3x increase in UV stability, 5-year warranty retention, and 60% fewer customer complaints. That’s the power of understanding your fabric.
In this guide, we’ll break down what acrylic fabric really is, how it performs under industrial stress, and how your business can benefit by choosing the right type and supplier. Stick around to explore practical data, sourcing advice, and expert insights that go beyond surface-level knowledge.
What Is Acrylic Fabric Made Of and How Is It Manufactured?
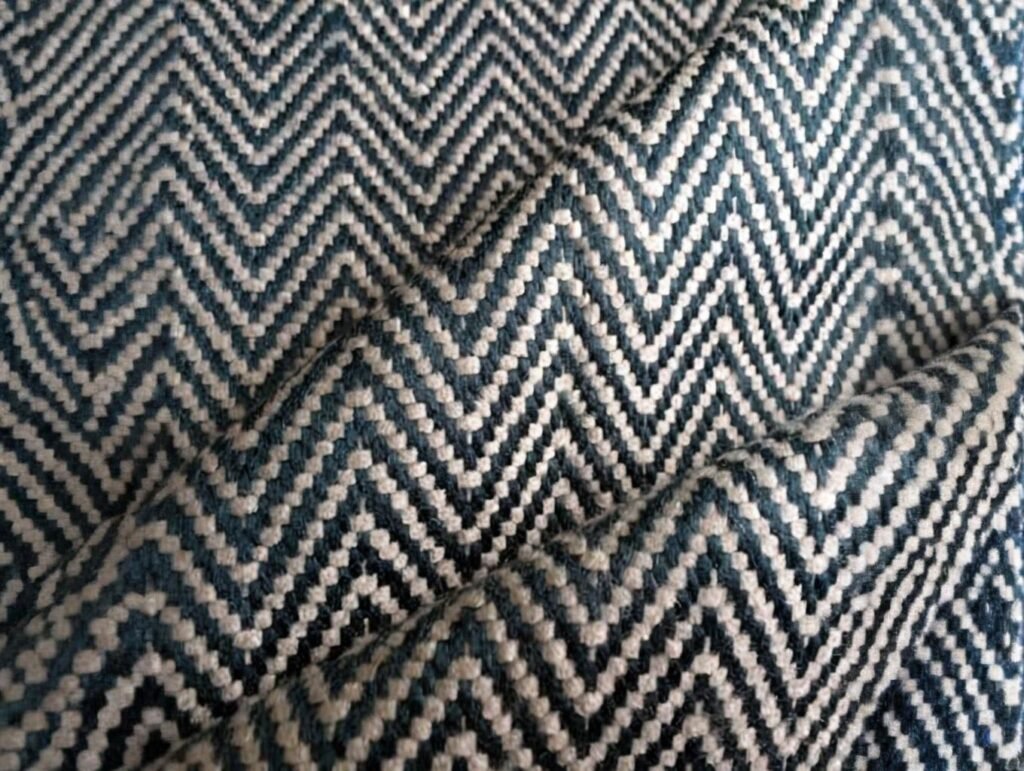
Acrylic fabric is primarily made from acrylonitrile—a synthetic polymer derived from petroleum. It undergoes wet or dry spinning, followed by heat treatment to stabilize its form and texture, creating a versatile and performance-driven textile.
Understanding the Manufacturing Process of Acrylic Fabric
- 1.1 Raw Material Extraction and Polymerization Acrylonitrile is synthesized via a chemical reaction involving propylene, ammonia, and oxygen. This monomer is then polymerized into polyacrylonitrile (PAN)—the foundation of acrylic fiber.
- 1.2 Fiber Spinning Methods There are two common spinning methods:
- Wet Spinning: Polymer is dissolved in solvent, extruded into a coagulation bath.
- Dry Spinning: Polymer solution is extruded into hot air, evaporating solvent quickly.
Method | Advantages | Disadvantages |
---|---|---|
Wet Spinning | Stronger fiber bonds, smoother yarn | Slower, more energy intensive |
Dry Spinning | Faster, cheaper | Slightly weaker structural fiber |
- 1.3 Heat Setting and Drawing After spinning, fibers are heat-treated at ~120–150°C to improve dimensional stability and wrinkle resistance. This step makes the fabric viable for outdoor, industrial, and high-tension uses.
- 1.4 Surface Treatment (Optional) Acrylic fabrics may also be treated with coatings (e.g., PU, PVC) or blended with other fibers (e.g., modacrylics) to enhance flame resistance or elasticity.
Leading industrial awning brands such as Sunbrella® use solution-dyed acrylic yarns. This means the pigment is locked in during fiber formation—not just surface-coated—resulting in unmatched fade resistance.
How Does Acrylic Fabric Compare to Other Synthetic Industrial Fabrics?
Compared to polyester, nylon, or polypropylene, acrylic fabric stands out for its UV resistance, thermal insulation, and ability to retain shape under exposure to sunlight and heat—making it ideal for outdoor or heat-intensive industrial environments.
Acrylic vs. Other Synthetic Industrial Fabrics
- 2.1 Acrylic vs Polyester Polyester is stronger in tensile strength but weaker in UV resistance.
Property | Acrylic | Polyester |
---|---|---|
UV Resistance | ★★★★★ | ★★★☆☆ |
Tensile Strength | ★★★★☆ | ★★★★★ |
Thermal Insulation | ★★★★☆ | ★★★☆☆ |
Cost per Kg (USD) | $2.5–$3.0 | $1.8–$2.5 |
Dye Retention | Excellent (SD) | Good |
- 2.2 Acrylic vs Nylon Nylon is abrasion-resistant but tends to yellow or degrade faster in UV-exposed environments. Acrylic maintains color and form over time.
- 2.3 Acrylic vs Polypropylene (PP) PP is cheap and moisture-resistant but melts at low temperatures (~160°C), while acrylic can withstand ~190°C and resists color fading.
A marine seating company once replaced polyester-based fabrics with solution-dyed acrylic in boat upholstery. After two years, they saw a 70% reduction in UV-related returns and 40% higher customer retention.
- 2.4 Blending Possibilities Acrylic can also be blended with natural or other synthetic fibers for customized performance:
- Acrylic-Cotton Blends – For improved softness in interior industrial décor
- Acrylic-Polyester Blends – For enhanced tear strength in awnings and banners
Performance Comparison of Common Industrial Textiles
Fabric Type | UV Resistance | Abrasion Resistance | Thermal Insulation | Colorfastness | Cost Efficiency |
---|---|---|---|---|---|
Acrylic | Excellent | Moderate | High | Excellent | Moderate |
Polyester | Moderate | High | Moderate | Good | High |
Nylon | Poor | Excellent | Low | Moderate | Moderate |
PP | Low | Moderate | Low | Poor | Excellent |
What Are the Key Properties That Make Acrylic Ideal for Industrial Use?
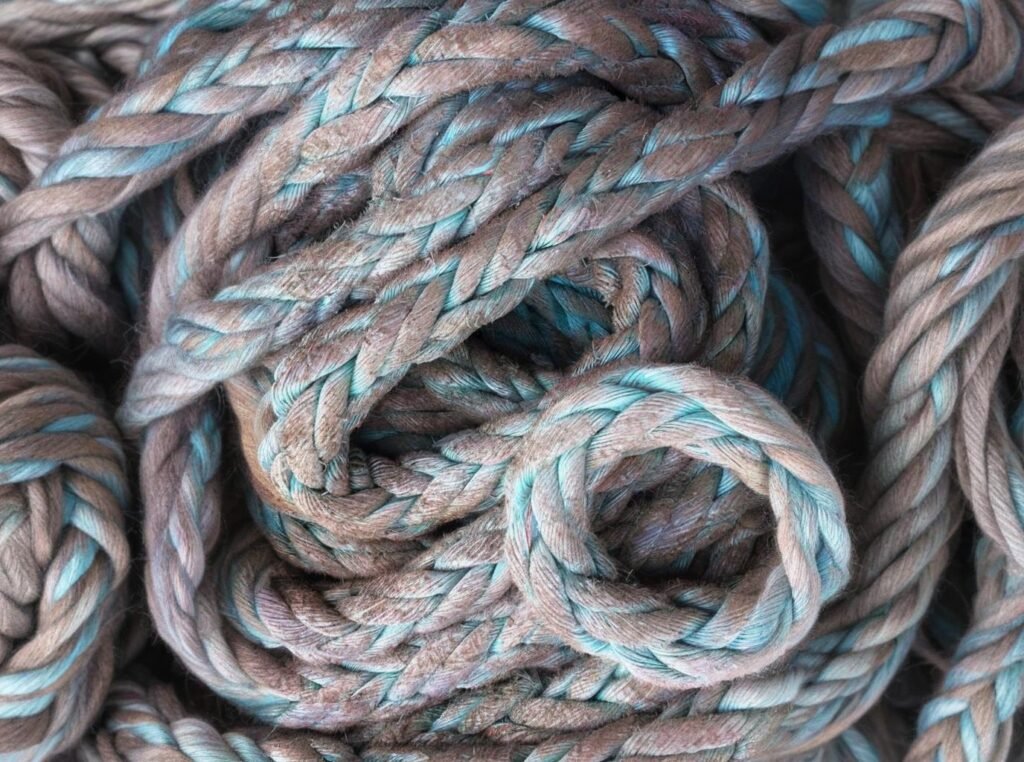
Acrylic fabric is known for several key properties that make it stand out in industrial textiles, including UV resistance, weather durability, lightweight nature, and thermal insulation. These properties help acrylic excel in harsh environments.
Breaking Down Acrylic’s Core Properties
- 3.1 UV Resistance Acrylic fabric is renowned for its exceptional UV stability, thanks to the molecular structure of polyacrylonitrile. This property makes it perfect for outdoor applications such as tents, sails, and outdoor furniture coverings. Key Advantage: Acrylic fabrics resist UV degradation much longer than polyester or nylon. This gives acrylic a longer lifespan in direct sunlight, which is critical for industrial sectors that require longevity in their textile solutions. Real World Example: A large outdoor event company that switched to acrylic fabric for tent covers reported a 50% reduction in fabric replacement costs over five years, as their acrylic tents showed significantly less fading compared to previous polyester models.
- 3.2 Water Resistance and Weather Durability Acrylic fabrics tend to absorb very little moisture, making them ideal for applications exposed to rain, humidity, or snow. This also prevents the fabric from weakening due to water retention.
- Example: Acrylic fabric is a staple in marine industries, where it’s used for covers, tarps, and upholstery, providing a long-lasting, mildew-resistant solution.
- 3.3 Thermal Insulation Acrylic fibers are naturally more insulating than polyester or nylon due to the air pockets they trap in their structure. This makes acrylic fabrics beneficial in applications requiring thermal regulation. Example: Acrylic is often used in industrial insulation for pipes and cables, providing effective protection against temperature fluctuations.
- 3.4 Lightweight & Flexible Acrylic is lighter than some other synthetics, such as nylon, while still providing the necessary strength and durability. This makes it useful in applications where both weight and strength matter, such as protective covers, outdoor cushions, and even in automotive interiors. Real-World Insight: In the automotive industry, acrylic fabrics are favored for sunshades and convertible tops, where low weight and UV resistance are crucial for both performance and aesthetics.
Property | Acrylic Fabric | Nylon Fabric | Polyester Fabric |
---|---|---|---|
UV Resistance | ★★★★★ | ★★★☆☆ | ★★★★☆ |
Thermal Insulation | ★★★★☆ | ★★★☆☆ | ★★☆☆☆ |
Water Resistance | ★★★★☆ | ★★★☆☆ | ★★★★★ |
Weight | ★★★★☆ | ★★★☆☆ | ★★★★☆ |
Durability | ★★★★☆ | ★★★★★ | ★★★☆☆ |
Which Industrial Applications Commonly Use Acrylic Fabric?
Acrylic fabric’s versatility makes it a preferred choice across several industries, including automotive, marine, outdoor advertising, and construction. Its strength, durability, and ability to withstand harsh environments make it invaluable in these sectors.
Key Industries Using Acrylic Fabric
- 4.1 Automotive Industry Acrylic fabrics are used in automotive upholstery, sunshades, and convertible tops due to their UV resistance and lightweight nature. The fabric’s ability to maintain color and resist fading under direct sunlight makes it an essential material in vehicles exposed to high levels of UV radiation. Case Study: A leading automotive manufacturer switched to acrylic-based convertible tops and saw improved color retention and lower warranty claims related to UV damage. Acrylic’s ability to resist fading ensured a longer-lasting product, increasing customer satisfaction.
- 4.2 Marine Industry Acrylic fabrics are heavily used for marine applications such as boat covers, awnings, and sails. Acrylic’s superior resistance to UV rays and water makes it the ideal choice for outdoor fabrics exposed to sun, saltwater, and high moisture levels. Example: Sailmakers have long relied on acrylic fabrics for sails and other outdoor marine applications. One global marine equipment supplier reported that their acrylic sails lasted twice as long compared to other synthetic options like polyester.
- 4.3 Outdoor Advertising Acrylic fabric is widely used in banners, flags, and billboards due to its ability to retain vibrant colors even in long-term outdoor conditions. The material’s weather and UV resistance make it a great choice for high-visibility advertising displays that need to endure the elements. Industry Insight: A large outdoor advertising company replaced their PVC banners with solution-dyed acrylic fabric and experienced 40% less fading and higher client retention, as clients noticed the durability of the printed graphics.
- 4.4 Construction and Industrial Tarps Acrylic fabrics are often used in construction for tarps and covers due to their high tensile strength and weather durability. The fabric’s ability to block UV rays and resist chemical exposure is critical in heavy-duty construction environments. Case Study: A construction company reported that acrylic tarps provided better longevity and strength compared to standard tarps, which led to reduced replacement costs and increased efficiency on job sites.
Summary of Industrial Applications of Acrylic Fabric
Industry | Acrylic Use Case | Key Benefits | Typical Products |
---|---|---|---|
Automotive | Convertible tops, sunshades | UV resistance, color retention | Car sunroofs, upholstery |
Marine | Sails, covers, upholstery | Water resistance, durability | Boat covers, awning fabric |
Outdoor Advertising | Billboards, flags | UV resistance, colorfastness | Outdoor banners, flags |
Construction | Tarps, covers | Durability, UV protection | Heavy-duty tarps, mesh covers |
How Do You Choose the Right Type of Acrylic Fabric for Your Industry?
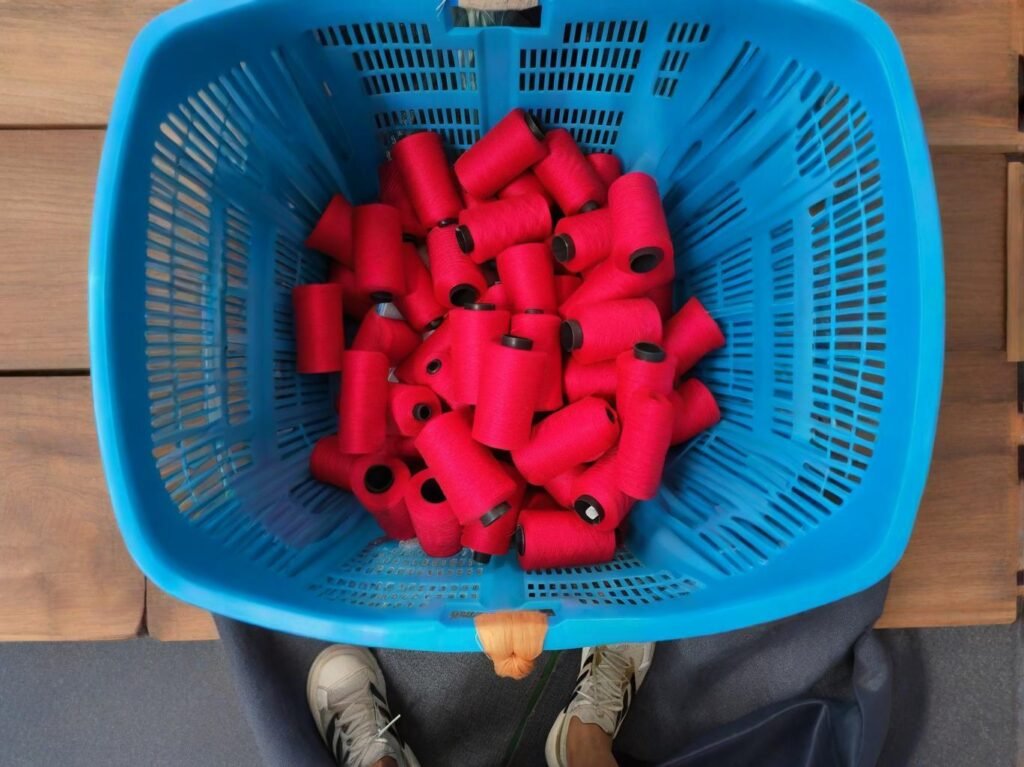
Choosing the right acrylic fabric depends on your industry’s performance demands, such as UV exposure, mechanical strength, fire safety, and finishing treatments. You must also consider coating, weave type, dye method, and blending.
Key Selection Criteria for Acrylic Fabric
- 5.1 Coated vs. Uncoated Acrylic
- Coated Acrylic: Often includes PVC or PU layers for waterproofing or fire resistance. Common in awnings, tarps, or flame-retardant covers.
- Uncoated Acrylic: More breathable and soft, ideal for upholstery or automotive interior applications.
Use Case | Recommended Type | Notes |
---|---|---|
Outdoor tents | Coated solution-dyed | Enhanced water resistance |
Indoor seating | Uncoated yarn-dyed | Comfort and breathability |
Industrial tarps | Coated flame-retardant | Meets safety compliance |
- 5.2 Solution-Dyed vs. Yarn-Dyed Acrylic
- Solution-Dyed: Color pigments are added during the fiber creation process. Best for UV resistance and long-term color retention.
- Yarn-Dyed: Color is applied after spinning; slightly more affordable but less color-stable outdoors.
Tip for Buyers: If your application is outdoor-heavy or exposed to sunlight for more than 2 hours daily, always prioritize solution-dyed acrylic.
- 5.3 Weave Type: Plain, Twill, or Satin Different weaves provide different mechanical strengths and surface textures.
Weave Type | Strength | Surface | Applications |
---|---|---|---|
Plain | High | Rough | Outdoor banners, heavy tarps |
Twill | Medium | Smooth | Automotive upholstery, shading |
Satin | Low | Glossy | Decorative, non-load bearing fabric |
- 5.4 Blended Acrylic Fabrics For custom requirements, you may choose blends like:
- Acrylic/Polyester (50/50) – Increases tear strength
- Acrylic/Modacrylic (80/20) – Improves flame retardancy
- Acrylic/Natural fibers – Improves softness for lifestyle textiles in industrial hotels or lounges
Case Example: A German architectural shading brand adopted 100% solution-dyed acrylic for all their premium retractable awnings. Their testing showed UV degradation reduced by 82% compared to older yarn-dyed polyester models over 3 years.
Is Acrylic Fabric Resistant to Chemicals, UV, and Abrasion?
Yes, acrylic fabric is chemically stable, highly UV-resistant, and moderately abrasion-resistant. Its unique polymer structure helps resist degradation from light, heat, mildew, and some industrial solvents, making it ideal for extended outdoor or hazardous use.
Evaluating Resistance Properties
- 6.1 UV Resistance Testing Acrylic scores high on the AATCC TM16 UV exposure test. After 1,000 hours of simulated sun exposure, solution-dyed acrylic retains over 85% of its original color strength, outperforming polyester (70%) and nylon (55%).
Fabric Type | Color Retention @ 1000hrs | ASTM UV Grade |
---|---|---|
Acrylic (SD) | 85–95% | 4–5 |
Polyester | 70–80% | 3 |
Nylon | 55–65% | 2 |
Application Note: In outdoor canopies or marine fabrics, this color retention significantly extends replacement cycles and reduces cost of ownership.
- 6.2 Chemical Resistance Acrylic fibers are resistant to many acids and industrial cleaning solvents but are weak against alkalis (like strong bleaches).
Chemical Type | Resistance Level | Notes |
---|---|---|
Acids (mild/strong) | High | No degradation in acidic rain |
Solvents (IPA, acetone) | Medium | Surface finish may dull |
Alkalis (NaOH) | Low | May degrade with prolonged use |
Tip: In environments like chemical labs or cleaning-intensive settings, pre-coating acrylic with a fluorocarbon finish enhances chemical durability.
- 6.3 Abrasion Resistance Acrylic’s abrasion rating is moderate. On the Martindale abrasion test, solution-dyed acrylic scores 15,000–25,000 cycles, enough for heavy-duty cushions and commercial upholstery.
Fabric | Martindale Score (Cycles) | Use Recommendation |
---|---|---|
Acrylic (SD) | 20,000 avg | Suitable for heavy seating |
Nylon | 40,000+ | Ideal for industrial straps |
Cotton | 10,000 | Light-duty use |
A hospitality chain tested acrylic seating fabric in their high-traffic lobby furniture. After 18 months, abrasion marks were minimal, and the color remained vibrant. This reduced their reupholstery frequency by 30% annually.
What Are the Environmental and Safety Considerations of Using Acrylic in Industry?
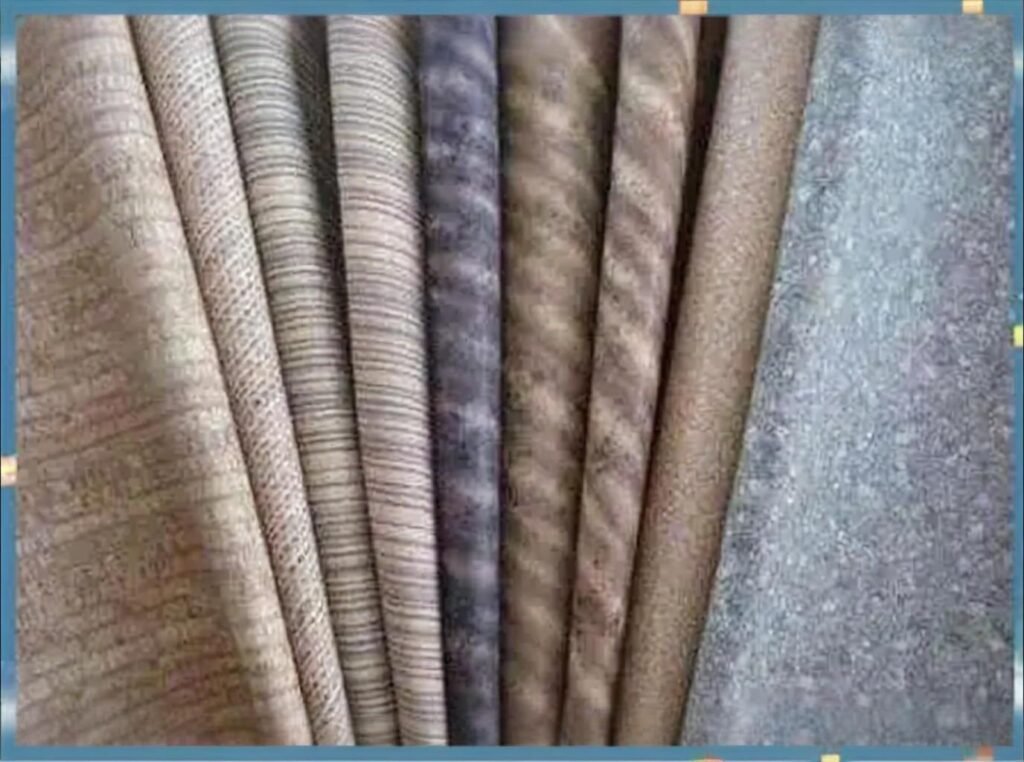
Acrylic fabric presents both benefits and challenges when it comes to environmental impact and workplace safety. It offers high durability and reduces replacement cycles, but its petroleum-based origin and recyclability limitations require careful lifecycle management.
Sustainability and Health Impacts of Acrylic Fabric
- 7.1 Environmental Footprint of Acrylic Production Acrylic is derived from acrylonitrile—a petroleum-based compound. This process is energy-intensive and emits volatile organic compounds (VOCs), particularly during dry spinning.
Metric | Acrylic Fabric | Polyester Fabric | Cotton |
---|---|---|---|
Raw Material Source | Petroleum | Petroleum | Natural |
Water Usage (liters/kg fabric) | ~70 | ~40 | ~10,000 |
Carbon Emissions (kg CO₂e/kg) | ~20 | ~15 | ~2.1 |
Observation: While cotton has lower carbon emissions per kg, it requires vastly more water. Acrylic performs best when evaluated over its long lifespan and lower replacement rate.
- 7.2 Recyclability & End-of-Life Concerns Unlike polyester, which has mature mechanical and chemical recycling pathways (like rPET), acrylic recycling is still under development. It’s currently downcycled into insulation or blended composites, not closed-loop. However, some manufacturers are researching depolymerization technologies for post-industrial acrylic waste.
- 7.3 Fire Safety and Worker Exposure Acrylic is naturally flammable and must be treated to meet flame-retardant standards like:
- NFPA 701 (U.S. flammability standard for industrial textiles)
- BS 5867 (UK)
- ISO 6940/6941 (Global test methods)
Case Study: A hospital curtain supplier sourced FR-treated acrylic fabric to comply with NFPA 701 and passed third-party audits for patient safety in critical care units.
- 7.4 OEKO-TEX® and REACH Compliance Many high-end acrylic suppliers offer certified OEKO-TEX Standard 100 fabrics, ensuring absence of harmful chemicals. REACH-compliant coatings also reduce toxic substance exposure in EU-regulated markets.
Recommendation for Buyers: Ask your supplier if their acrylic fabric is OEKO-TEX or REACH certified. This can simplify export compliance, especially in EU or North American markets.
How Can B2B Buyers Source Custom Acrylic Fabrics from Manufacturers?
B2B buyers can source acrylic fabrics through certified OEM/ODM textile manufacturers that offer customization in fiber blends, coatings, finishes, and dyeing methods. Key considerations include MOQ, sampling speed, quality control, and export support.
Strategic Sourcing Guide for B2B Acrylic Fabric Buyers
- 8.1 Define Your Requirements Clearly
- End use (indoor, outdoor, marine, automotive?)
- Key performance needs (UV, flame resistance, waterproofing?)
- Desired certifications (NFPA 701, OEKO-TEX, ISO?)
Example: A commercial awning brand requested UV-resistant, solution-dyed, PU-coated acrylic fabric in 30 custom colors for their high-end product line—with GRS and OEKO-TEX labels to support sustainability claims.
- 8.2 Choose an Experienced OEM/ODM Partner Work with suppliers that offer:
- Free sampling & design assistance
- Low minimum order quantity (MOQ)
- Fast lead times (2–4 weeks for bulk)
- Quality assurance (100% inspection, lab testing)
- Export documentation (Form A, CO, MSDS)
Manufacturer Checklist | SzoneierFabrics (Yes/No) |
---|---|
Custom Dyeing (Solution/Yarn) | ✅ |
Coating Options (PU, PVC, FR) | ✅ |
Low MOQ (100m or less) | ✅ |
Fast Sampling (3–5 days) | ✅ |
Certifications (OEKO, REACH) | ✅ |
- 8.3 Request Technical Data Sheets (TDS) Always ask for TDS including:
- Fabric weight (GSM)
- Tensile strength (ASTM D5034)
- Colorfastness (AATCC TM61/16)
- UV aging test results (ASTM G155 or AATCC TM169)
Buyers working with outdoor furniture brands may want fabrics with GSM ≥ 250, Martindale ≥ 20,000 cycles, and UV grade ≥ 4–5.
- 8.4 Establish Long-Term Collaboration Sourcing isn’t just transactional. Build long-term partnerships with manufacturers who invest in innovation and respond quickly to design or compliance updates.
Why Acrylic Fabric Is a Smart Investment for Industrial Textiles
Acrylic fabric has proven its worth across industries—from automotive and marine to outdoor advertising and construction. Its unique combination of UV resistance, thermal insulation, and aesthetic versatility make it a top-tier choice for industrial applications requiring durability and performance.
While its environmental profile poses challenges, manufacturers are moving toward cleaner production and treatment methods. As sustainability and customization become the norm, working with a manufacturer that understands both performance and compliance is critical.
Ready to Custom Order Acrylic Fabric?
At SzoneierFabrics, we specialize in custom acrylic fabric manufacturing for B2B clients. Whether you’re building a high-performance awning collection, marine covers, industrial tarps, or architectural textiles, we’ve got you covered with:
- ✅ Free samples & design
- ✅ Low MOQ customization
- ✅ Short lead times
- ✅ OEKO-TEX & REACH compliant options
- ✅ Global export support
Contact us now to get your custom quote or free samples.