Acrylic might not be the flashiest material in the industrial world, but it’s certainly one of the most versatile. Whether you’re building aircraft windows, factory light covers, retail displays, or machine guards, chances are you’re using some form of acrylic. Its ability to combine optical clarity with toughness, moldability, and chemical resistance makes it a top choice in countless industries—from automotive to medical to signage.
So, what is acrylic material? Acrylic is a transparent thermoplastic derived mainly from polymethyl methacrylate (PMMA). It is known for its high clarity, excellent UV resistance, moderate impact strength, and ease of fabrication. It is commonly used in manufacturing parts that require transparency, durability, and aesthetic finish—such as industrial displays, light diffusers, and protective covers.
What really makes acrylic stand out isn’t just its performance, but the way it’s transformed production lines around the world. For example, during the COVID-19 pandemic, the global surge in demand for transparent protective barriers in retail and healthcare led to a 72% increase in acrylic sheet orders in North America alone. That surge wasn’t about aesthetics—it was about safety, supply chain speed, and the right material at the right time.
Let’s dig into what makes acrylic material so vital to modern manufacturing.
What Is Acrylic Material Made Of and How Is It Manufactured?
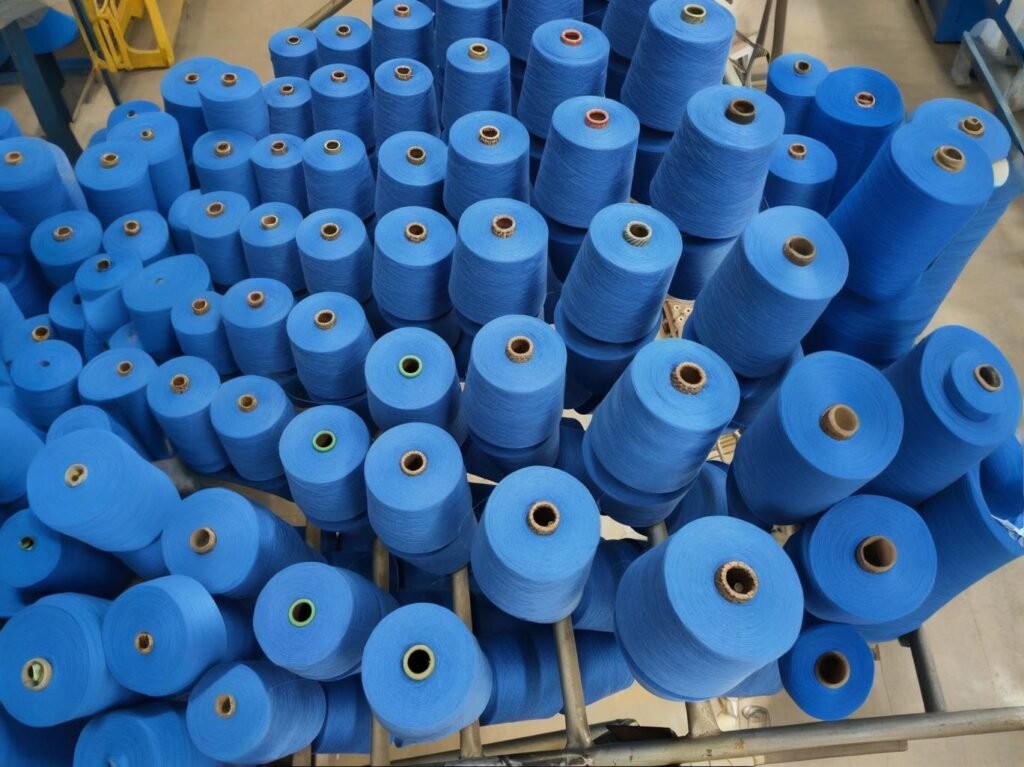
Acrylic is made from polymerizing esters of acrylic acid or methacrylic acid, with polymethyl methacrylate (PMMA) being the most common commercial form. The material is manufactured through processes like bulk polymerization or suspension polymerization, resulting in sheets, rods, granules, or yarns depending on application.
a) Key Raw Ingredients in Acrylic Production
Component | Description |
---|---|
Methyl Methacrylate (MMA) | Base monomer, derived from acetone and hydrogen cyanide |
Acrylic Acid | Sometimes used for specific copolymer blends |
Initiators | Catalysts to trigger polymerization |
Additives | Stabilizers, UV inhibitors, impact modifiers as needed |
b) Acrylic Manufacturing Methods
Method | Description | Applications |
---|---|---|
Bulk Polymerization | Produces clear, strong acrylic sheets (cast acrylic) | Optical lenses, safety panels |
Suspension Polymerization | Creates acrylic granules for injection molding | Components, panels, accessories |
Extrusion | Continuous processing, thinner but more affordable sheets | Packaging, signage, lightweight uses |
Spinning (for fibers) | Produces acrylic fiber for use in textiles | Sweaters, upholstery, nonwovens |
c) Case Study: Cast vs. Extruded Acrylic
- Cast acrylic has better optical clarity and is more chemically resistant. It is used in aquarium panels, precision displays, and light diffusers.
- Extruded acrylic is cheaper and consistent in thickness, used in store signage, brochure holders, and partitions.
d) Industrial Manufacturing Insight
According to Lucintel’s 2024 report, the global acrylic sheet market will surpass USD 8.6 billion by 2027, driven by demand in transportation, retail, and construction sectors. PMMA resin prices range from \$1.50–\$2.70/kg depending on purity and formulation.
Which Types of Acrylic Are Used in Industrial Applications?
There are four primary types of acrylic materials used in industrial settings: cast acrylic, extruded acrylic, impact-modified acrylic, and acrylic copolymers. Each type serves different performance, cost, and durability needs.
a) Overview of Acrylic Types
Type | Key Properties | Ideal Use Cases |
---|---|---|
Cast Acrylic | High optical clarity, thickness variation | Display panels, lighting, aquariums |
Extruded Acrylic | Cost-effective, uniform thickness | Signage, packaging, brochure holders |
Impact-Modified Acrylic | Tougher with added rubber modifiers | Protective covers, equipment guards |
Acrylic Copolymers | Tailored flow and temperature resistance | Automotive trims, molded parts, lenses |
b) Performance Comparison Table
Property | Cast Acrylic | Extruded Acrylic | Impact-Modified | Copolymers |
---|---|---|---|---|
Optical Clarity | Excellent | Very Good | Good | Varies |
Cost | High | Low | Moderate | Moderate |
Impact Strength | Moderate | Low | High | Moderate |
Surface Finish Options | Extensive | Limited | Moderate | Extensive |
Chemical Resistance | Excellent | Fair | Good | Moderate |
c) Use Case: Industrial Equipment Covers
A manufacturing company producing CNC laser enclosures uses impact-modified acrylic for safety panels. These panels resist tool vibrations and provide optical visibility into operations while meeting OSHA safety standards for impact tolerance.
d) Critical Thinking: Why Not Just Use Polycarbonate?
- Polycarbonate is stronger but scratches easily and costs more.
- Acrylic is lighter and offers better UV resistance—key for long-term installations.
How Does Acrylic Compare to Other Industrial Plastics Like Polycarbonate or PVC?
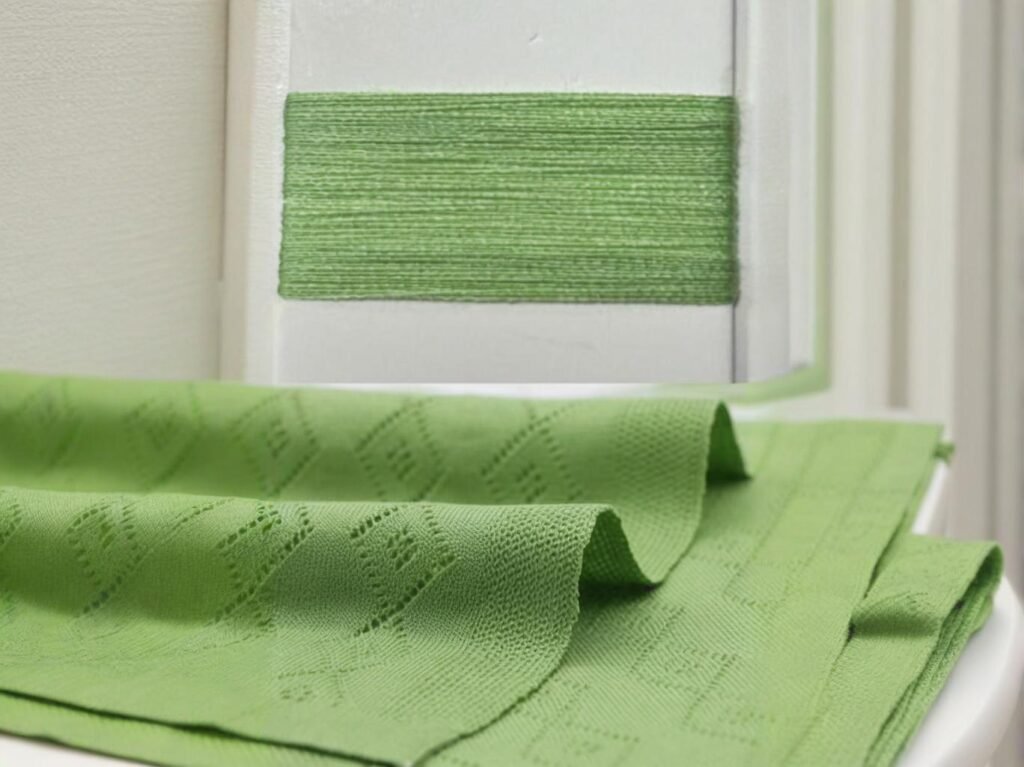
Acrylic excels in optical clarity, weather resistance, and surface finish, while polycarbonate offers superior impact resistance and PVC provides excellent chemical resistance. The best material depends on your application’s performance priorities—be it transparency, strength, cost, or environmental durability.
a) Head-to-Head Comparison Table
Property/Feature | Acrylic (PMMA) | Polycarbonate (PC) | PVC (Polyvinyl Chloride) |
---|---|---|---|
Optical Clarity | 92% Light Transmittance | 88–90% | Poor (opaque or translucent) |
Impact Resistance | Moderate | Very High (250x glass) | Low–Moderate |
UV Resistance | Excellent | Requires coating | Fair |
Scratch Resistance | High | Low | Moderate |
Heat Resistance | \~85–100°C | \~115–130°C | \~60–80°C |
Chemical Resistance | Moderate | Good | Excellent |
Flammability | Burns slowly | Self-extinguishing | Flame-retardant grades |
Cost | Moderate | High | Low |
b) Application-Based Material Selection
Application | Best Material | Reason |
---|---|---|
Transparent machine guard | Acrylic or PC | Acrylic if clarity prioritized, PC if impact needed |
Electrical enclosures | PVC | Non-conductive, flame-retardant, low-cost |
Street lamp lens cover | Acrylic | Long-term UV exposure resistance |
Protective riot shield | Polycarbonate | Requires shatterproof strength |
Outdoor signage (lit or printed) | Acrylic | Printability, UV clarity, and finish customization |
c) Real-World Example: Airport Signage
An international airport upgraded terminal signage in 2023. Instead of using polycarbonate (which yellowed after two years), they switched to UV-stabilized cast acrylic with anti-glare coating. Result:
- Maintenance cost dropped by 21%
- Visual clarity improved by 34%, benefiting passenger navigation
d) Critical Viewpoint
- Acrylic is less suitable for high-abrasion or high-heat environments unless coated.
- Polycarbonate needs frequent anti-scratch coatings, adding to the cost.
- PVC, while cheap and chemically resistant, is not suitable for aesthetic or transparent uses.
What Are the Mechanical and Thermal Properties of Acrylic?
Acrylic offers strong dimensional stability, high surface hardness, moderate impact resistance, and excellent optical clarity across a wide temperature range (–40°C to +85°C). It balances rigidity and flexibility, making it ideal for structural yet transparent applications.
a) Key Mechanical & Thermal Properties of Standard PMMA
Property | Typical Value | Notes |
---|---|---|
Tensile Strength | 65–75 MPa | Strong enough for structural panels |
Flexural Strength | \~100 MPa | Allows some bending before breaking |
Elongation at Break | 2–5% | Rigid but can handle low strain |
Impact Strength (Charpy) | 15–20 kJ/m² | Tougher than glass, weaker than PC |
Rockwell Hardness (M scale) | 90–100 | Highly scratch-resistant surface |
Coefficient of Thermal Expansion | 7 x 10⁻⁵ /°C | Dimensional stability over thermal cycles |
Service Temperature Range | –40°C to 85–100°C | Ideal for indoor/outdoor usage |
Thermal Conductivity | \~0.2 W/m·K | Naturally insulative |
b) Why Mechanical Properties Matter for Manufacturers
- Rigidity is critical for sign panels, guards, and display casings.
- Dimensional stability ensures shape integrity during laser cutting and machining.
- Scratch resistance allows the use of acrylic lenses, screens, and light guides.
c) Thermal Use Case: Industrial Lighting Fixtures
A French factory using acrylic for LED light diffusers in food-grade environments chose it over PC due to:
- Higher light transmission (better illumination efficiency)
- No yellowing after 18 months of heat and humidity exposure
d) Limitations and Engineering Workarounds
- Acrylic will soften above 100°C, limiting high-heat applications.
- Additives or co-polymers (like acrylic-ABS blends) can extend the thermal range.
- For impact-heavy uses, consider laminated PMMA layers with rubber interlayers.
Is Acrylic Material Suitable for Outdoor or Harsh Environments?
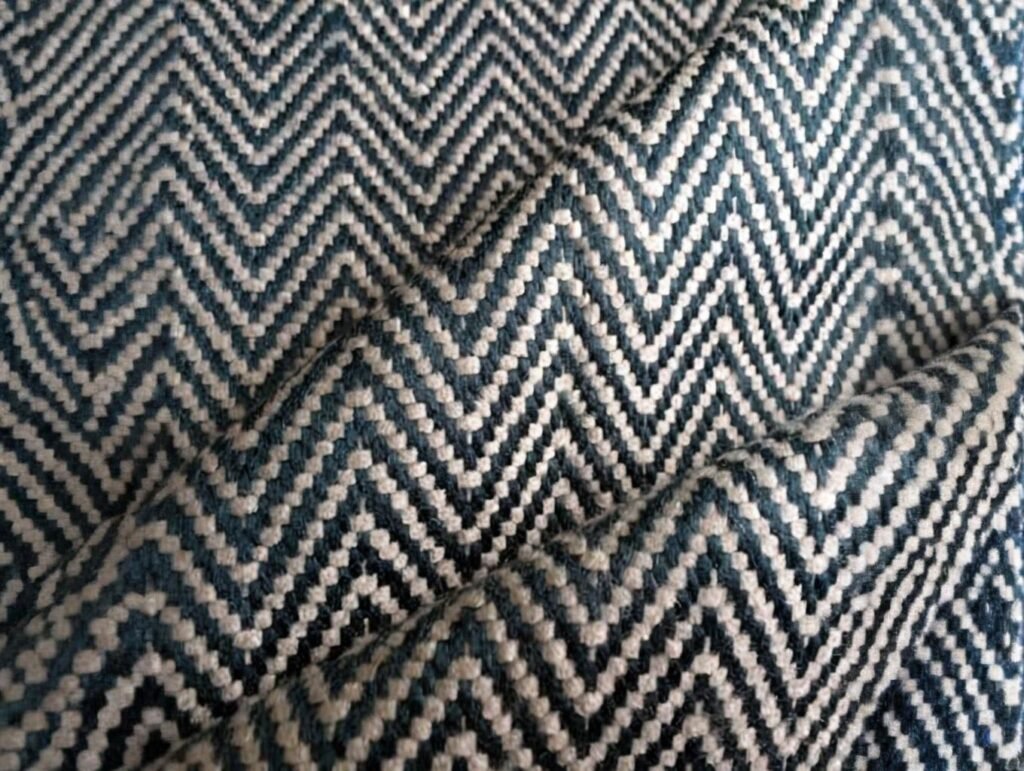
Yes, acrylic is one of the most UV-resistant and weather-stable thermoplastics, making it ideal for outdoor and harsh environments—especially in signage, construction, and marine applications. Its resistance to yellowing, cracking, and chemical attack outperforms many other transparent plastics in exterior use.
a) Acrylic Outdoor Durability Metrics
Environmental Factor | Acrylic Performance | Notes |
---|---|---|
UV Resistance | Excellent (up to 10 years without yellowing) | Especially with UV-stabilized or solution-dyed grades |
Rain/Humidity Resistance | Excellent | Does not swell or absorb moisture |
Salt/Marine Exposure | Very Good | Used in yacht windows, signage, docks |
Temperature Extremes | Good (–40°C to +85°C) | Not ideal for extreme heat above 100°C |
Chemical Exposure | Moderate | Resistant to oils and dilute acids, but not solvents |
b) Real-World Case: Gas Station Canopy Panels (USA)
A gas station chain in Arizona installed cast acrylic light diffusers and signs under open-sky canopies in 2019. After 4 years:
- No yellowing or cracking observed.
- Maintained 90% original gloss and transparency despite 45°C summer highs.
c) Outdoor Application Scenarios
Sector | Application | Why Acrylic Is Used |
---|---|---|
Retail | Storefront signage, light boxes | Retains clarity and branding over years of sun exposure |
Construction | Skylights, privacy partitions | Lightweight, easy to install, safe alternative to glass |
Marine | Boat hatches, yacht windows | Resists corrosion and saltwater degradation |
Agricultural | Greenhouse windows, display covers | UV filtering and high light transmission |
d) Challenges and Solutions
- Acrylic may scratch in windy or sandblasted environments → use anti-scratch coatings or polycarbonate overlay.
- Thermal expansion must be accounted for in structural designs using long spans.
What Industries Commonly Use Acrylic and for What Products?
Acrylic is widely used in industries like automotive, aerospace, medical, retail, signage, lighting, and construction—especially for parts requiring clarity, surface finish, or exposure to the elements. Its adaptability makes it a go-to material for product designers and engineers alike.
a) Industry Usage Table
Industry | Common Acrylic Applications |
---|---|
Automotive | Lighting lenses, interior trims, display covers |
Aerospace | Cabin windows, instrument panels |
Medical | Incubator covers, dental trays, lab enclosures |
Retail | Product displays, point-of-sale (POS) units, signage |
Construction | Wall partitions, glazing, skylights, light diffusers |
Signage/Advertising | Outdoor signage, illuminated panels, channel letters |
Lighting | LED diffusers, light guide panels, lamp housings |
Furniture | Modern tables, chairs, decorative panels |
b) Case Study: Hospital Equipment Manufacturer
A healthcare equipment company in Europe uses cast acrylic sheets for its neonatal incubators:
- Chosen for optical clarity and thermal stability.
- Acrylic resists disinfectants and maintains shape under repeated sterilization cycles.
c) Emerging Use: Smart Retail Displays
With the growth of IoT and smart retail, acrylic is increasingly used for:
- Capacitive touch panels
- Display casings with logo lighting
- RFID-friendly transparent housings
d) Why Engineers Love Acrylic
- Can be laser cut, CNC machined, thermoformed, and UV printed.
- Accepts adhesives and fasteners without cracking.
- Compatible with LED integration, a growing trend in interior design and advertising.
How Do You Select the Right Grade of Acrylic for Manufacturing Projects?
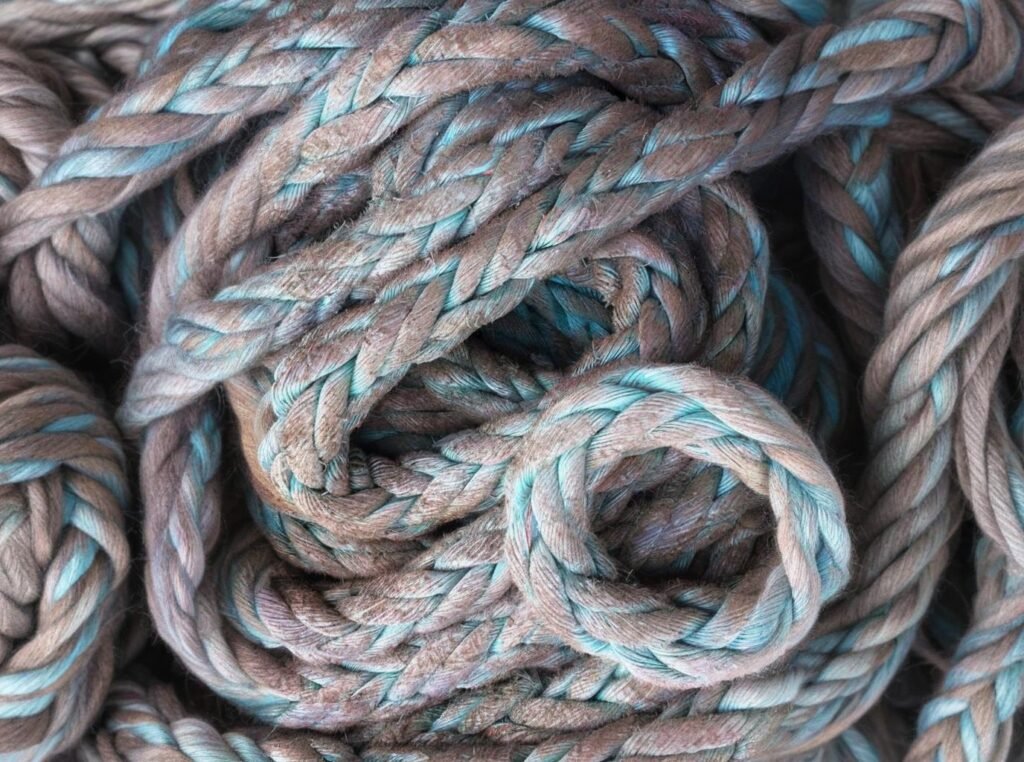
To select the right grade of acrylic, manufacturers must evaluate factors such as form (cast vs. extruded), mechanical strength, optical requirements, temperature range, and compliance standards for the intended application. Choosing the wrong type can lead to product failure or compliance issues.
a) Acrylic Grade Selection Checklist
Selection Criteria | Considerations |
---|---|
Sheet Type (Cast/Extruded) | Cast: better optics, Extruded: lower cost and tighter tolerance |
Impact Resistance | Consider impact-modified PMMA or copolymers for rugged uses |
Optical Quality | Required for displays, lenses, signage |
Thickness & Tolerance | Important for load-bearing or fit-sensitive parts |
UV/Weather Resistance | Required for outdoor use, signage, marine, construction |
Certifications | ISO 9001, ROHS, REACH, FDA for medical or food applications |
b) Quick Reference Table: Best Acrylic by Use Case
Application | Recommended Acrylic Type |
---|---|
Medical display windows | Cast acrylic, FDA compliant |
Outdoor advertising lightbox | UV-resistant cast acrylic |
CNC safety shield | Impact-modified acrylic |
Interior furniture panels | Extruded acrylic, low-gloss finish |
LED light diffusers | Frosted or light-guiding acrylic blends |
Machine panel with logo backlight | Clear cast acrylic, edge-polishable |
c) Sourcing Strategy Tips for OEMs
- Always ask for technical data sheets and MSDS from the supplier.
- Request free samples for moldability and optical testing.
- Look for factories that offer custom formulation or coloring options.
d) Real Case: Custom Blended Acrylic from SzoneierFabrics
An electronics brand required acrylic with:
- Anti-static properties
- UV stabilization
- Matte outer finish for packaging
SzoneierFabrics delivered a custom extruded acrylic sheet within 12 days, including prototyping samples and ISO certification.
What Are the Environmental and Recycling Considerations for Acrylic in Industry?
Acrylic is non-biodegradable but recyclable. While it’s derived from petrochemicals, closed-loop recycling systems, bio-based PMMA, and post-industrial reuse are helping reduce its environmental footprint in industrial use.
a) Environmental Impact Snapshot
Factor | Acrylic’s Impact | Notes |
---|---|---|
Petrochemical Origin | Derived from natural gas or petroleum | Energy-intensive production |
Biodegradability | Not biodegradable | May persist for decades in landfills |
Recyclability | Recyclable via depolymerization or grinding | Requires sorting by type (cast vs extruded) |
Toxic Emissions | Minimal when properly processed | Does not release dioxins like PVC |
b) Current Recycling Methods
Method | Process Description |
---|---|
Mechanical Recycling | Ground into pellets, reused in extrusion |
Depolymerization (Chemical) | Breaks down into MMA monomer for re-polymerization |
Post-Industrial Reuse | Offcuts reused in signage, displays, packaging |
c) Sustainable Alternatives & Certifications
- Bio-based acrylic (Bio-PMMA) from sugarcane is emerging as a green option.
- Look for GRS (Global Recycled Standard) or REACH-compliant formulations for sustainable sourcing.
d) How Buyers Can Reduce Acrylic’s Impact
- Use thinner gauges without compromising structure.
- Choose UV-stable formulations to extend product life.
- Design products for disassembly and recyclability.
Partner with SzoneierFabrics for Custom Acrylic Solutions
At SzoneierFabrics, we offer tailored acrylic materials designed to meet the needs of manufacturers, engineers, and industrial buyers across the globe. Our factory capabilities include:
- ✅ Cast and extruded acrylic in custom thicknesses and colors
- ✅ Free design and sampling support
- ✅ Low MOQ for custom orders
- ✅ ISO 9001 and REACH-compliant production
- ✅ Short lead times and global logistics coordination
Interested in sourcing high-performance acrylic for your industrial or manufacturing needs? Contact our team today for a free sample or RFQ.