What Is the Difference Between Viscose and Rayon Fabric in Manufacturing?
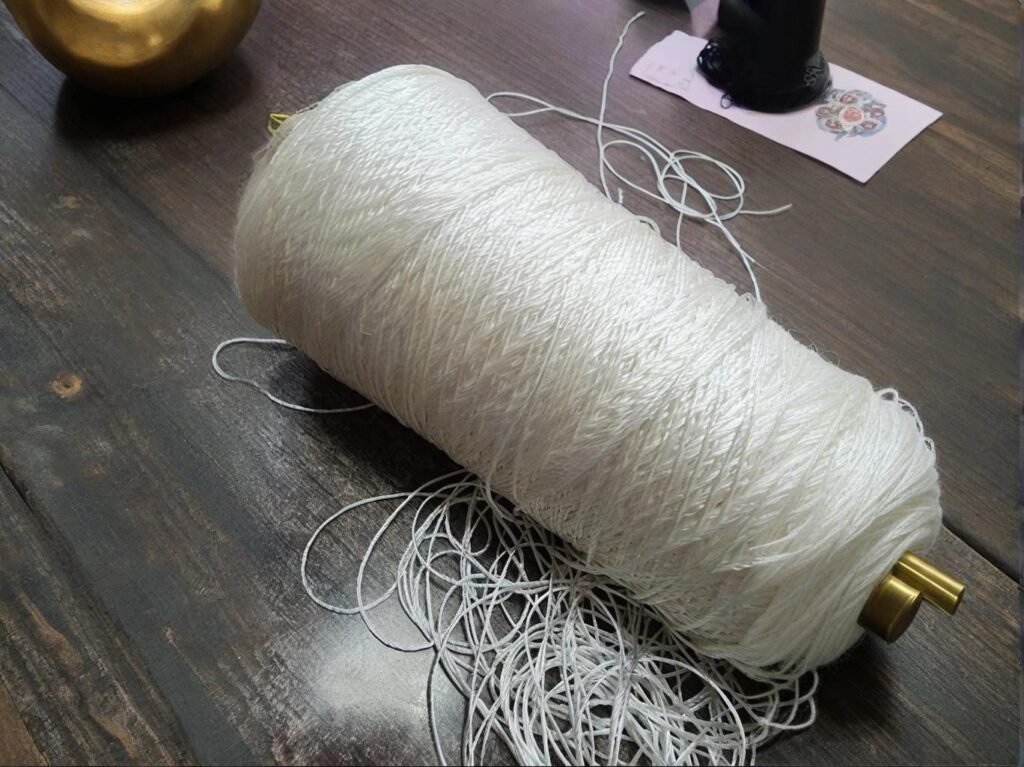
In the world of textile production, where performance, sustainability, and sourcing efficiency dictate decisions, the terms viscose and rayon are often tossed around like interchangeable twins. But behind the label lies a world of difference—especially when it comes to manufacturing methods, chemical usage, and environmental impact. For sourcing professionals and designers, understanding these differences isn’t just academic—it can change the quality, safety, and commercial viability of the final product.
Viscose is a specific type of rayon produced through the viscose process using carbon disulfide, while rayon is a broader category that includes viscose, modal, and lyocell, each with distinct manufacturing and performance characteristics.
This distinction has implications far beyond terminology. From dye behavior and drape to worker safety and ecological responsibility, choosing between viscose and other rayon variants can shape everything from product appeal to your brand’s ESG (Environmental, Social, and Governance) metrics.
Let’s start by unraveling their origins—what they’re made of, and why their base materials matter.
What are rayon and viscose fabrics made from?
Both rayon and viscose fabrics are derived from regenerated cellulose, typically extracted from wood pulp. The difference lies not in their raw material source, but in the way they are processed. While viscose is one of the oldest and most widely used forms of rayon, newer variants like modal and lyocell use modified methods to improve performance and reduce environmental impact.
Fiber Origin and Chemistry
A. Common Raw Materials Used
Raw Material Source | Used In | Notes |
---|---|---|
Beechwood pulp | Modal, viscose | Popular in Europe |
Bamboo pulp | Viscose (marketed as bamboo rayon) | Needs heavy chemical processing |
Eucalyptus, Pine, Spruce | Lyocell, viscose | Closed-loop systems preferred |
While the input material (cellulose) is often the same, it’s the processing path that determines whether the output is labeled viscose, modal, lyocell, or simply “rayon.”
B. Chemical Regeneration Process
Viscose and other rayons are semi-synthetic: not entirely natural, yet not fully synthetic like polyester. They’re created by chemically dissolving cellulose and extruding it into fibers.
- Viscose uses carbon disulfide (CS₂), sodium hydroxide, and sulfuric acid.
- Modal uses a modified viscose method under gentler conditions.
- Lyocell uses NMMO (N-Methylmorpholine N-oxide) in a closed-loop system.
“The term ‘rayon’ is like the word ‘fruit’—it can mean apple (viscose), banana (modal), or pear (lyocell). Viscose just happens to be the most common type of rayon.” — Textile Chemist, Hangzhou Institute of Textiles
How is the manufacturing process of viscose different from other types of rayon?
The viscose process involves more chemical exposure, higher emissions, and a more labor-intensive workflow compared to the lyocell or modal processes. While viscose remains dominant due to its low cost and wide availability, more sustainable rayon variants are gradually reshaping the textile landscape.
Step-by-Step Process Comparison
A. Manufacturing Process Flowchart
Process Stage | Viscose Rayon | Modal Rayon | Lyocell Rayon |
---|---|---|---|
Cellulose Extraction | Wood pulp | Wood pulp | Wood pulp |
Pre-treatment | Alkali steeping (NaOH) | Alkali steeping (controlled) | Direct dissolution in NMMO |
Dissolution | Carbon disulfide (CS₂) used | CS₂ used (less volume) | No CS₂, uses non-toxic solvent |
Fiber Spinning | Acid bath extrusion | Acid bath extrusion | Direct extrusion (closed loop) |
Waste Recovery | Partial | Moderate | High (closed loop \~99% recovery) |
Water Consumption | High | Moderate | Low |
Worker Safety Risk | High (due to CS₂ exposure) | Moderate | Low |
B. Environmental and Workplace Safety Impact
Viscose’s reliance on carbon disulfide raises concerns over worker safety and environmental damage. Exposure to CS₂ is linked to neurological effects in factory settings.
Case Data: In 2023, a viscose plant in South Asia was fined over \$1.2 million due to poor chemical waste handling. In contrast, a lyocell mill operating under EU REACH standards was praised for 98.5% solvent recovery.
C. Machinery and Infrastructure Requirements
Viscose production is cheaper to set up in low-regulation regions, which is why most viscose mills operate in China, India, and Indonesia. Modal and lyocell require advanced solvent recovery systems, which increases startup cost but reduces lifecycle emissions.
Which chemicals are used in viscose and rayon production, and how do they affect fabric quality?
The key chemical difference lies in the use of carbon disulfide (CS₂) in traditional viscose production, while newer rayon types like modal and lyocell use more advanced, often closed-loop, chemical processes. These chemical differences don’t just impact safety—they significantly influence the texture, strength, absorbency, and dye affinity of the final fabric.
Chemical Inputs and Fabric Performance
A. Primary Chemicals in Each Process
Chemical | Used In | Function | Impact on Fabric |
---|---|---|---|
Sodium hydroxide (NaOH) | All rayons | Prepares pulp for regeneration | May cause fiber weakening if not washed thoroughly |
Carbon disulfide (CS₂) | Viscose | Dissolves cellulose for spinning | Can leave residual smell or instability |
Sulfuric acid (H₂SO₄) | Viscose | Coagulates the fiber from solution | Affects shrinkage and fiber clarity |
NMMO (solvent) | Lyocell | Direct solvent for cellulose | Enhances softness, stability, and eco-profile |
B. Residual Chemical Traces and Quality Control
In poorly regulated viscose production, residual CS₂ or sulfur may remain in the fiber, leading to:
- Color inconsistencies in batch dyeing
- Slight chemical odor in finished garments
- Faster fiber degradation after washing
However, in modern viscose mills that implement multi-stage washing and heat-setting, these issues can be significantly minimized.
“Our lab tested rayon from three different mills. The modal and lyocell samples showed more stable shrinkage and better dye take-up. The viscose samples varied more—likely due to residual processing chemicals.” — Fabric Testing Lab Director, Sweden
C. Impact on Dyeing and Printing
- Viscose: Accepts dye well but is more reactive to heat and moisture during setting.
- Modal: Better dimensional stability during dyeing, with deeper color penetration.
- Lyocell: Offers the best blend of dye affinity and colorfastness, especially for digital printing.
4. What are the environmental impacts of viscose vs. rayon production?
The environmental impact of viscose production is one of its biggest controversies. Traditional viscose mills often discharge hazardous effluents, use large quantities of water, and contribute to deforestation when pulp is not sustainably sourced. In contrast, modal and lyocell are widely seen as more sustainable alternatives thanks to closed-loop chemical recovery systems and certified wood sourcing.
Sustainability Scorecard
A. Pollution and Chemical Emissions
Metric | Viscose | Modal | Lyocell |
---|---|---|---|
Chemical Recovery Rate | \~30–50% | 50–60% | Up to 99.5% |
Water Usage per kg fiber | \~150–250L | \~100–150L | \~50–100L |
Air Emissions (e.g., CS₂) | High | Moderate | Very Low |
Common Wastewater Contaminants | Sulfates, CS₂ | Less toxic byproducts | Minimal |
B. Deforestation and Pulp Sourcing
Many viscose mills historically sourced pulp from endangered forests in Indonesia, Brazil, or Canada. The shift toward FSC (Forest Stewardship Council)-certified pulp is improving this trend—but not universally.
- LENZING™ uses 100% FSC-certified pulp in modal and lyocell.
- Asia Pacific Rayon (Indonesia) has begun closed-loop practices, but watchdogs still cite pulp traceability gaps.
- Some Chinese viscose mills continue to face criticism for lacking transparency in wood sourcing.
2024 Report: Changing Markets Foundation reported that only 36% of global viscose mills met sustainable forestry and pollution control standards, while over 80% of modal/lyocell production now qualifies as “responsible” under EU textile rules.
C. Certifications That Indicate Lower Environmental Impact
Certification | Rayon Type | What It Proves |
---|---|---|
FSC | All | Pulp sourced from responsibly managed forests |
OEKO-TEX® Standard 100 | All | No harmful substances in the finished fabric |
EU Ecolabel | Modal, Lyocell | Closed-loop processing and eco-performance |
LENZING ECOVERO™ Label | Viscose | Certified low-impact viscose with traceability |
Do rayon and viscose fabrics have different performance characteristics?
While viscose and other rayon types share a soft, breathable feel, their performance characteristics vary depending on the manufacturing process. Factors such as tensile strength, shrinkage, drape, pilling resistance, and care instructions are significantly influenced by whether the fabric is viscose, modal, or lyocell.
Performance Profile Comparison
A. Mechanical Properties of Viscose vs. Other Rayons
Property | Viscose | Modal | Lyocell |
---|---|---|---|
Dry Strength | Moderate | Higher than viscose | Highest among rayons |
Wet Strength | Low (30–50% weaker) | Moderate | Good wet strength |
Shrinkage (post-wash) | High if untreated | Low | Low |
Wrinkle Resistance | Poor | Moderate | Moderate–Good |
Pilling Resistance | Low | Good | Excellent |
Drape & Softness | Excellent | Very soft | Crisp, smooth feel |
💡 Insight: Modal is preferred for garments needing a cotton-rayon blend feel, while lyocell is great for structured yet breathable styles. Viscose, though beautiful in drape, may require lining or reinforcement for durability.
B. Comfort and Skin Contact
Viscose, modal, and lyocell are all skin-friendly. However:
- Viscose: Can feel slightly cooler on the skin but may lose shape after repeated washes.
- Modal: Naturally smooth, great for intimates and activewear.
- Lyocell: Best suited for moisture-wicking applications, like eco sleepwear or sustainable athletic wear.
“We noticed that viscose T-shirts in our retail store lost form after just three washes, while modal versions held up much better and received fewer returns.” — Textile Sourcing Manager, EU-based clothing brand
C. Finishing Enhancements
Some viscose fabrics are chemically or mechanically finished to improve performance:
- Sanforizing to reduce shrinkage
- Silicone washing to improve hand feel
- Anti-pilling coatings for longevity
That said, modal and lyocell often don’t require such treatments, reducing the production footprint.
6. Which industries or applications prefer viscose over other rayon types?
The use of viscose vs. modal or lyocell depends on product type, brand positioning, and target customer base. While viscose remains a go-to for affordable, high-drama drape fashion, modal and lyocell are more popular in premium segments that emphasize softness, performance, or sustainability.
Industry Application Overview
A. Fashion Industry
Product Type | Preferred Fiber Type | Reason |
---|---|---|
Flowing dresses | Viscose | Superior drape, affordable for mass production |
T-shirts | Modal | Soft hand feel, durable through wash cycles |
Denim alternatives | Lyocell | Structure + softness, great for blended yarns |
Linings & Scarves | Viscose | Lightweight, printable, silky feel |
Loungewear | Modal / Lyocell | Breathable, luxurious feel against the skin |
B. Home Textiles
- Modal: Preferred for bed sheets, pillowcases, and plush throws due to its softness and durability.
- Viscose: Still common in curtains and upholstery linings due to its affordability and print quality.
- Lyocell: Rising fast in the eco bedding and towel market.
C. Technical and Specialty Applications
- Lyocell blends (with polyester, elastane, or wool) are increasingly used in performance wear.
- Flame-retardant viscose (treated) is used in workwear and industrial safety gear.
D. Brand and Market Positioning
Market Segment | Common Rayon Type | Example Brands Using It |
---|---|---|
Fast fashion | Viscose | H\&M, Zara |
Premium essentials | Modal | Hanro, Calvin Klein Underwear |
Eco-conscious labels | Lyocell | Patagonia, Tentree, Thought |
“In 2025, we’re seeing a shift. Mid-tier brands that previously used viscose for cost reasons are switching to ECOVERO™ or modal to align with eco goals and Gen Z’s values.” — Apparel Industry Analyst, McKinsey Textile Summit
How do certification standards apply differently to viscose and other rayons?
Certification standards are essential for verifying environmental, ethical, and performance claims in fabric sourcing. While all rayon types can be certified, the standards and their stringency vary depending on the production method. Viscose often requires stricter monitoring due to its chemical intensity, while modal and lyocell more easily align with eco-label requirements thanks to cleaner manufacturing systems.
Key Textile Certifications and How They Apply
A. Common Certifications Across Rayon Types
Certification | Applies To | Validates What | Adoption Rate |
---|---|---|---|
OEKO-TEX® Standard 100 | All | No harmful substances in the final fabric | High |
FSC (Forest Stewardship) | All | Pulp from responsibly managed forests | Medium |
GRS (Global Recycled Std) | Rayon Blends | Use of recycled materials in blended fibers | Low–Growing |
EU Ecolabel | Modal, Lyocell | Low emissions, water use, and high biodegradability | High |
LENZING™ Certification | Branded fibers | ECOVERO™, TENCEL™ Modal and Lyocell | High (Lenzing) |
B. Viscose-Specific Compliance Challenges
Because viscose production often involves carbon disulfide and sulfuric acid, mills must comply with:
- ZDHC (Zero Discharge of Hazardous Chemicals) protocols
- Local environmental regulations for wastewater and air emissions
- Chemical recovery and containment plans
“We required OEKO-TEX® certification for a viscose order last year. Only 2 out of 6 mills had the documentation ready. In contrast, 5 out of 6 modal suppliers already met EU Ecolabel or had GRS paperwork in place.” — Sourcing Director, UK-Based Loungewear Brand
C. Certification in Branding and Consumer Communication
Brands now display eco-certifications prominently on packaging and e-commerce product pages. Having fibers like ECOVERO™ or TENCEL™ helps increase consumer trust and even price elasticity.
D. Traceability Tools
- LENZING™ Fiber Identification enables traceable fibers using molecular tagging
- Digital QR Codes linked to supply chain certificates are becoming a norm for premium rayon garments
Is viscose or rayon better for your specific textile manufacturing needs?
The best choice between viscose and other types of rayon depends on your end-use application, budget, brand values, and logistics timeline. If you’re launching a cost-sensitive line with dramatic drape, viscose may suit your needs. If you’re building a premium or sustainable brand, modal or lyocell likely provides better alignment.
Choosing Based on Your Use Case
A. Budget and Order Size
Scenario | Best Fit | Why |
---|---|---|
Small MOQ, fast launch | Viscose or modal | Viscose is widely available, modal is stable |
Mid-tier fashion with soft finish | Modal | Great for hand feel and long-term shape |
Sustainable premium collection | Lyocell | High eco value, excellent durability |
Digital print scarf or wrap | Viscose | Absorbs color well, great drape |
Custom blend for athleisure | Lyocell blend | Soft + performance |
B. Supplier Collaboration and Flexibility
Working with a supplier who understands the technical nuances between rayon types is crucial. Look for partners who can:
- Offer side-by-side swatch comparisons
- Recommend fabric based on dye type and pattern complexity
- Provide real test reports on shrinkage, pilling, and colorfastness
Why SzoneierFabrics Is the Ideal Partner for Rayon and Viscose Projects
With more than 18 years of experience in textile R\&D and manufacturing, SzoneierFabrics is uniquely positioned to guide you through the rayon-versus-viscose decision. Whether you’re sourcing for casualwear, accessories, or home textiles, Szoneier offers:
- Customized rayon blends tailored to your GSM, texture, and drape needs
- Low MOQs starting at 100–300 meters for sample runs or seasonal collections
- Fast sampling turnaround within 3–5 business days
- Free expert consultation on fabric selection, sustainability, and finishing
- Compliance-ready documentation for OEKO-TEX®, FSC, or customer-requested audits
“We developed a two-tone modal-rayon blend for our luxury sleepwear line with SzoneierFabrics. They helped us reduce shrinkage, enhance softness, and still meet our low MOQ needs. We wouldn’t go elsewhere.” — Co-founder, Canadian Boutique Apparel Brand
Can't find the answers?
No worries, please contact us and we will answer all the questions you have during the whole process of bag customization.
Make A Sample First?
If you have your own artwork, logo design files, or just an idea,please provide details about your project requirements, including preferred fabric, color, and customization options,we’re excited to assist you in bringing your bespoke bag designs to life through our sample production process.