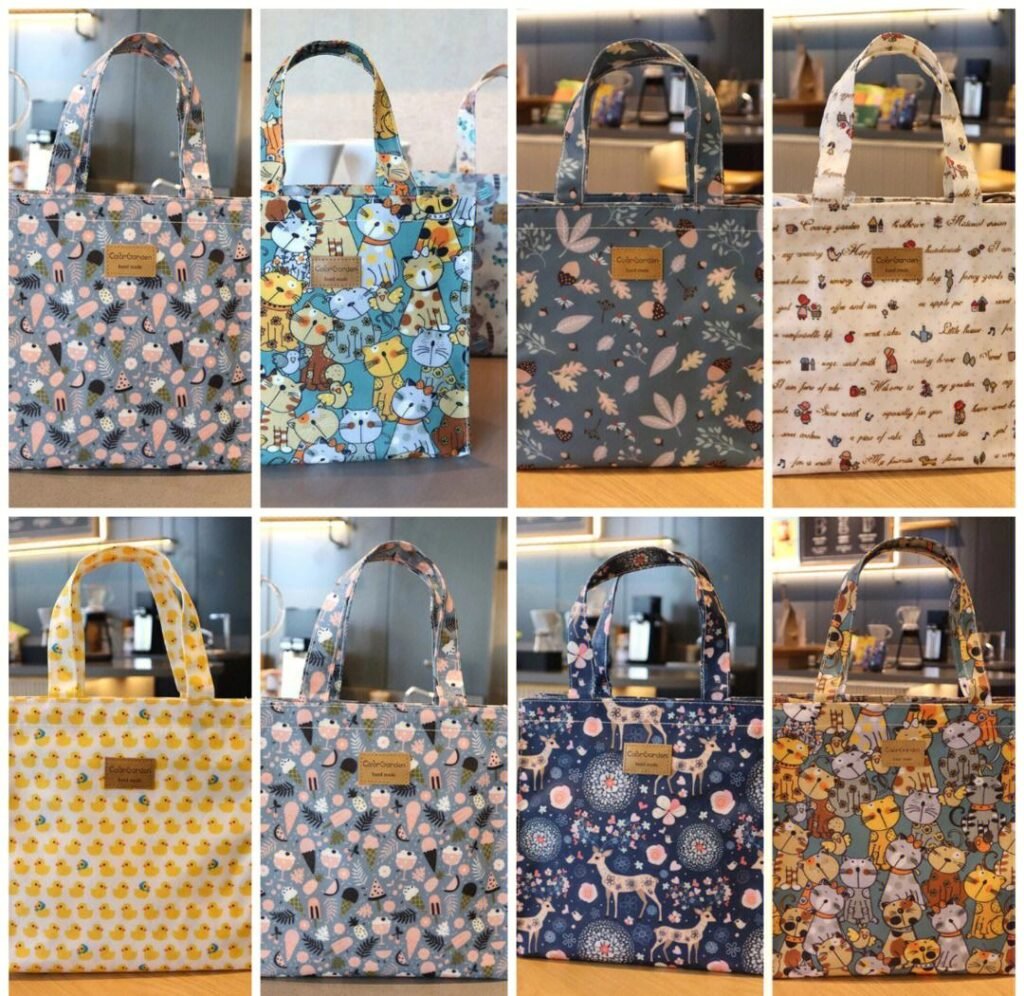
You might think that when it comes to backpack or bag materials, “denier” is just a fancy number printed on labels—but in reality, those digits can make or break a product’s performance, longevity, and even consumer perception. Imagine two identical-looking backpacks side by side: one crafted from 600D Oxford, the other from 1200D Oxford. They look nearly the same on a store shelf, but their behind-the-scenes differences in fabric composition, weight, and durability tell two very different stories. The question on every bag designer’s mind is: Is it better to specify 600D for lighter packs or 1200D for heavy-duty use?
600D Oxford uses a lighter-weight polyester yarn woven at lower density, resulting in a fabric weight of approximately 230–250 gsm and tensile strength around 450–500 N/5 cm; whereas 1200D Oxford doubles the denier, yields a fabric weight near 380–400 gsm, and achieves tensile strength of 800–900 N/5 cm—making 1200D roughly 60–70% stronger but about 50% heavier than 600D.
But hold on—before you decide which denier will hit your MOQ or price target, consider this: last season, a mid‐size outdoor gear brand launched a “light pack” line in 600D, boasting sleekness and weight savings. However, customer reviews soon pointed to scuff marks and tears around base seams after only a few excursions. Meanwhile, their “rugged series” built on 1200D became a quiet bestseller among trekking enthusiasts, surviving jagged rocks and rough handling without a hitch. That real-world contrast drives home how critical denier selection is—not only for spec sheets but for end-user satisfaction and brand reputation.
What distinguishes 600D Oxford from 1200D Oxford in terms of fabric composition?
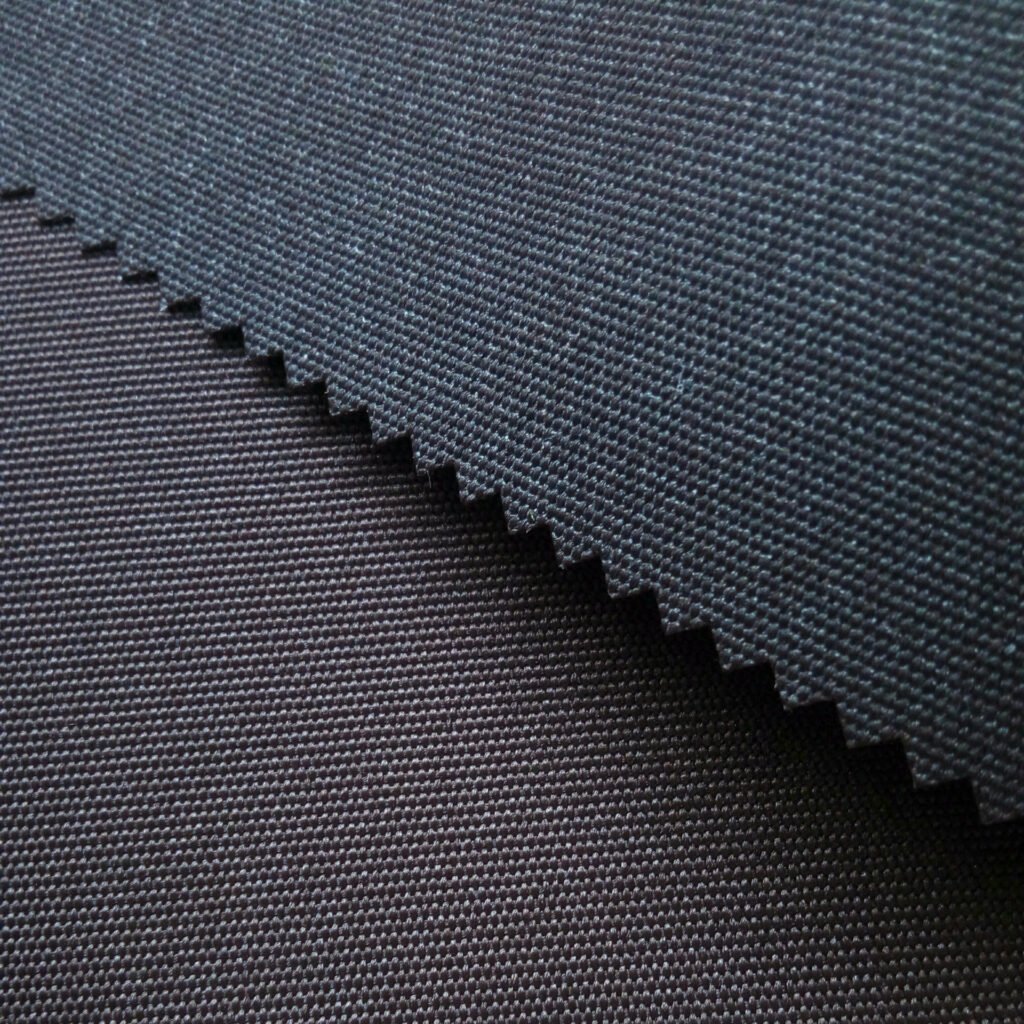
The primary distinction lies in yarn denier and weave density: 600D Oxford employs 600 denier polyester yarns (T/P 600D × 600D) woven in a basket or plain weave, resulting in fabric weights around 230–250 gsm. 1200D Oxford uses 1200 denier yarns (T/P 1200D × 1200D), doubling filament thickness, with higher tightness factor—yielding weights of 380–400 gsm. Both often feature a polyurethane (PU) or PVC coating for water resistance, but 1200D’s thicker yarns and denser construction provide significantly greater tensile strength (~800–900 N/5 cm vs. 450–500 N/5 cm) and tear resistance—albeit at roughly 1.6× the base cost and a noticeable weight penalty.
1. Yarn Denier & Fiber Type
Denier Definition:
- Denier indicates the mass (in grams) of 9,000 meters of yarn. Therefore, a 600D yarn weighs 600 grams per 9,000 meters, while 1200D is 1200 grams per 9,000 meters. Higher denier equates to thicker, stronger filaments.
Polyester vs. Nylon:
- Most Common: 600D and 1200D Oxfords are typically polyester (PET) due to cost efficiency, UV resistance, and lower stretch. Some high-end applications use nylon (e.g., 6 N) for greater abrasion toughness but at ~20–30% higher cost.
- Fiber Properties Comparison: Property Polyester (600D/1200D) Nylon (600D/1200D) Density (g/cm³) 1.38 1.14 Tensile Strength (cN/tex) 7–8 (600D), 9–10 (1200D) 8–9 (600D), 10–11 (1200D) Moisture Absorb. (%) ~0.4 ~4.0 UV Resistance Moderate (with UV50 coatings) Lower (degrades faster) Abrasion Resistance Good Excellent (10–15% better) Cost (/kg Fiber) $1.20–$1.50 $1.80–$2.20
- Implications: For budget-conscious brands, polyester dominates; for premium outdoor lines needing maximal abrasion protection, nylon 1200D may be justified despite higher cost.
2. Weave Construction & Density
Basket Weave vs. Plain Weave:
- 600D Oxford: Typically uses a 1 × 1 basket weave (two yarns over, one under) to balance drape and strength, at a tightness factor (TF) around 0.55–0.60 (TF = ends per inch × picks per inch × denier factor).
- 1200D Oxford: Often employs a 1 × 1 plain weave (one yarn over, one under) with a TF of 0.70–0.75, creating a denser face with fewer visible weave gaps—improving water resistance and mechanical performance.
Fabric Type | Weave Type | Ends/Inch (EPI) | Picks/Inch (PPI) | Tightness Factor (TF) | Comments |
---|---|---|---|---|---|
600D Basket | 1 × 1 Basket | 50 | 45 | 0.58 | Good drape; moderate abrasion life |
1200D Plain | 1 × 1 Plain | 65 | 60 | 0.72 | Tighter; superior tear/abrasion life |
600D Plain | 1 × 1 Plain | 55 | 50 | 0.65 | Slightly heavier than basket; more rigid |
1200D Basket | 1 × 1 Basket | 60 | 55 | 0.68 | Used in hybrid spec for balanced weight |
Fabric Weight Correlation:
- 600D Basket (TF ≈ 0.58): ~230–250 gsm after 2 × 2.5 oz PU coating.
- 1200D Plain (TF ≈ 0.72): ~380–400 gsm after similar coating weight.
- 600D Plain (TF ≈ 0.65): ~270–290 gsm.
- 1200D Basket (TF ≈ 0.68): ~350–370 gsm.
Beyond denier, weave density (EPI/PPI) directly affects end fabric properties—tighter weaves yield improved water barrier, higher abrasion life, and reduced permeability at the expense of weight and drape.
3. Coating & Lamination Options
Polyurethane (PU) vs. Polyvinyl Chloride (PVC):
- PU Coating (2 × 2.5 oz): Provides breathability (~1.0 cc/m²/s), flexibility, and moderate waterproofness (10,000 mm H₂O hydrostatic head). Common in higher‐end backpacks to avoid stiff hand.
- PVC Coating (2 × 3 oz): Offers superior water barrier (15,000 mm H₂O) and abrasion resistance but yields a heavier, stiffer fabric that can crack over time.
Coating Type | Coating Weight (oz/yd²) | Hydrostatic Head (mm) | Air Permeability (cc/m²/s) | Flexibility (GSM increase) | Typical Cost Impact (USD/m²) |
---|---|---|---|---|---|
PU (for 600D) | 2 × 2.5 | 8,000–10,000 | 1.0 | +50–60 gsm | $1.20 |
PU (for 1200D) | 2 × 2.5 | 10,000–12,000 | 0.8 | +60–70 gsm | $1.50 |
PVC (for 600D) | 2 × 3 | 12,000–15,000 | 0.0 | +70–80 gsm | $0.80 |
PVC (for 1200D) | 2 × 3 | 15,000–18,000 | 0.0 | +80–90 gsm | $1.00 |
Lamination vs. Coating:
- Lamination (e.g., TPU film): Provides excellent waterproof barrier (~20,000 mm H₂O), low air permeability—but adds 100–150 gsm and cost $2.00–$3.00/m². Preferred for high‐end expedition gear.
- Coating Adhesion: 1200D’s denser weave ensures better adhesion and less penetration of PU, producing more uniform water resistance. 600D can develop pinholes if coating is uneven.
4. Key Takeaways on Composition
- Denier & Weave: 1200D uses thicker filaments and tighter weave, making the base fabric ~60–70% stronger than 600D at the cost of ~50–60% more weight.
- Coating Synergy: While 600D with PVC coating can match a 1200D PU‐coated sample in water resistance, the heavier gauge and rigidity often detract from pack comfort and pack aesthetics.
- Fiber Choice: Brands seeking a middle ground sometimes employ a 1200D nylon face with 600D polyester back or reinforcement panels, optimizing cost and performance—but complexity and cost rise.
How does the weight of 600D compare to 1200D Oxford for bag applications?
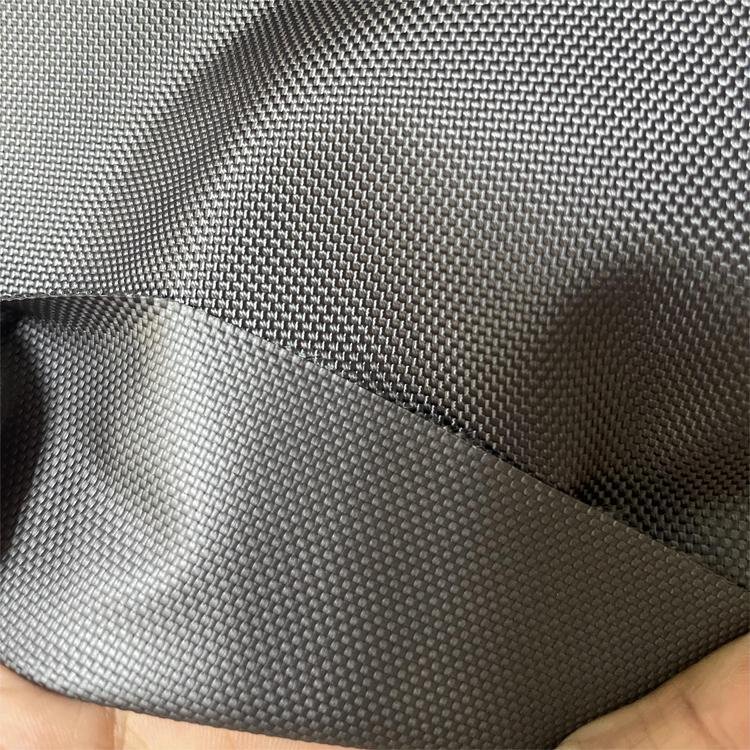
600D Oxford typically weighs 230–250 gsm after a standard 2 × 2.5 oz PU coating, resulting in ~8 oz/yd². In contrast, 1200D Oxford weighs 380–400 gsm post‐coating (approximately 12 oz/yd²). Consequently, a standard 20 L backpack constructed in 600D weighs roughly 450–500 g (excluding hardware), whereas the same silhouette in 1200D tips the scales at 770–820 g—a 50–60% increase. This weight delta impacts both user comfort and shipping costs.
1. Fabric GSM & Ounce/yard² Conversion
600D Oxford (PU-coated):
- Base fabric weight: 180–200 gsm (before coating).
- PU coating addition: +50–60 gsm → Total ~230–260 gsm (~7.5–8.0 oz/yd²).
- Total Thickness: ~0.32–0.35 mm.
1200D Oxford (PU-coated):
- Base fabric weight: 330–350 gsm pre-coating.
- PU coating addition: +50–70 gsm → Total ~380–420 gsm (~12.0–13.0 oz/yd²).
- Total Thickness: ~0.50–0.55 mm.
Material | Base GSM | Coating GSM | Total GSM | oz/yd² (approx.) | Thickness (mm) |
---|---|---|---|---|---|
600D Polyester | 180–200 | 50–60 | 230–260 | 7.5–8.0 | 0.32–0.35 |
1200D Polyester | 330–350 | 50–70 | 380–420 | 12.0–13.0 | 0.50–0.55 |
600D Nylon | 200–220 | 60–70 | 260–290 | 8.5–9.5 | 0.33–0.36 |
1200D Nylon | 350–370 | 60–80 | 410–450 | 13.0–14.5 | 0.55–0.60 |
A 20 L daypack uses approximately 2.0 m² of fabric (including lining and some waste).
- In 600D, 2.0 m² × 250 gsm = 500 g per shell layer; double‐layer panels push pack weight to ~700 g total with hardware included.
- In 1200D, 2.0 m² × 400 gsm = 800 g just for shell; finished pack lineup hovers near 1,000 g (including lining and trimmings).
2. Pack Weight Breakdown: Case Study
Component | 600D Version (g) | 1200D Version (g) |
---|---|---|
Outer Shell Fabric | 500 | 800 |
Lining (200D Polyester) | 150 | 150 |
Foam Padding | 80 | 80 |
Zippers, Buckles, Straps | 100 | 100 |
Thread and Trims | 20 | 20 |
Subtotal | 850 | 1,150 |
Final Finished Weight | ~900–950 | ~1,100–1,150 |
- Net Increase: ~250 g (28–29% heavier) for 1200D version—slightly less than the GSM ratio due to use of same lining and hardware.
- User Impact: A hiker carrying an extra 250 g constantly can perceive noticeable strain over a full day, especially on multi-hour treks.
3. Durability vs. Weight Trade-Off
600D Advantages:
- Lighter for Daily Commuters: Under 1 kg for a 20 L pack, ideal for office or urban use and favored by cyclists or travelers packing minimal gear.
- Lower Shipping Costs: Especially relevant for brands shipping worldwide; 250 g reduction per pack translates to $0.40–$0.60 savings per unit in international freight.
- Improved Foldability & Packability: Softer drape allows easier rolling into luggage.
1200D Advantages:
- High Abrasion and Slash Resistance: Thicker yarn and denser weave resist punctures and scuffs—critical for “overland” or “expedition” bags.
- Longer Lifespan: Tensile strength near 900 N/5 cm ensures fewer tears; abrasion tests show 20–30% greater cycle counts compared to 600D.
- Perceived Premium Quality: Customers often associate thicker material with durability and value, allowing brands to justify $10–$20 higher retail price.
Criterion | 600D Advantage | 1200D Advantage |
---|---|---|
Weight (g) | 900–950 g (20 L pack) | 1,100–1,150 g (20 L pack) |
Shipping Cost Impact | Lower weight → ~$0.50 savings per unit (air) | Higher perceived value → justifies cost |
Abrasion Life (Cycles) | 15,000–17,000 | 20,000–22,000 |
Tensile Strength (N/5 cm) | 450–500 | 800–900 |
Price (USD/m²) | $4.00–$4.50 | $6.50–$7.50 |
Lifecycle (Years of Use) | 1.5–2 (average heavy use) | 3–4 (average heavy use) |
If a brand can make a compelling case that customers value durability over a small weight increase, 1200D often wins in outdoor and tactical segments. But for fashion-forward, urban, or travel‐light lines, 600D remains popular.
4. Specialty Weight Variations & Hybrid Designs
600D Ripstop vs. Standard 600D:
- Ripstop Variation: Uses reinforcement yarns every 10–12 cm, layering an extra cross-hatch pattern. Slightly heavier (≈ 10 gsm more) but provides 30% greater tear resistance.
- Use Cases: Daypacks for travel, urban commuting, or kids’ school bags.
1200D Hybrid Panels:
- Reinforced Base & High‐Wear Zones: Some designs use 1200D for bottom and side panels, while main body is 600D to balance weight and cost.
- Average Weight Impact: Hybrid bag often weighs 1,000–1,050 g—a middle ground between pure 600D and pure 1200D.
- Performance: Hybrid abrasion scores about 18,500 cycles—closer to pure 1200D—while saving ~100 g over full 1200D.
Construction Type | Weight (g, 20 L) | Abrasion (Cycles) | Cost (USD/m²) |
---|---|---|---|
Pure 600D | 900–950 | 15,000–17,000 | $4.00–$4.50 |
Pure 1200D | 1,100–1,150 | 20,000–22,000 | $6.50–$7.50 |
Hybrid 600D Main + 1200D Base | 1,000–1,050 | 18,000–19,500 | $5.20–$5.80 |
600D Ripstop | 920–980 | 19,000–20,000 | $4.50–$5.00 |
1200D Ripstop | 1,130–1,180 | 22,000–23,000 | $7.00–$7.80 |
Hybrid designs can capture the best of both worlds, but they complicate production—requiring additional cutting, sewing, and inventory management. Brands must weigh the marginal performance gains against increased labor cost and complexity.
5. Shipping & Packaging Considerations
Volumetric Weight vs. Actual Weight:
- When shipping bulk backpacks, volumetric weight (cm³/5000) often surpasses actual weight, but extra 250 g per unit inflates overall pallet weight and shipping fees for ground cargo.
- Example: 100 600D packs weigh 57 kg, while 100 1200D packs weigh 115 kg—nearly double. Even if floor space is identical, total freight cost can jump $200–$300 for the heavier set.
Bulk Packaging:
- Compression & Folding: 600D compresses easier; 1200D’s stiffer structure can resist compression, requiring larger cartons.
- Carton Size Impact: A 600D pack can fold to 38 × 28 × 10 cm, while a 1200D equivalent may need 40 × 30 × 12 cm—10–20% more volume, further increasing air freight costs if applicable.
6. End-User Comfort & Ergonomics
Weight Distribution:
- A 250 g difference is felt more keenly when loaded with gear. For instance, a 5 kg load plus pack weight results in a 5% decrease in total carried weight when using 600D. On long hikes, that saving can translate to reduced fatigue.
Feel & Flexibility:
- 600D Construction: Softer drape, conforms more to body shape; straps anchor more comfortably.
- 1200D Construction: More rigid, maintains structure without collapsing, beneficial for overbuilt tactical bags that need to stand upright on shelves.
7. Cost Implications & Pricing Strategy
Raw Material Cost (USD/kg):
- 600D Polyester Yarn: $1.20–$1.50/kg.
- 1200D Polyester Yarn: $2.40–$3.00/kg.
Fabric Conversion Cost (USD/m²):
- 600D Oxford (with PU): $4.00–$4.50/m².
- 1200D Oxford (with PU): $6.50–$7.50/m².
Material Spec | Yarn Cost (USD/kg) | Fabric Price (USD/m²) | Final Bag Material Cost (20 m²) |
---|---|---|---|
600D Polyester | $1.20–$1.50 | $4.00–$4.50 | $80–$90 |
1200D Polyester | $2.40–$3.00 | $6.50–$7.50 | $130–$150 |
600D Nylon | $1.80–$2.00 | $5.00–$5.50 | $100–$110 |
1200D Nylon | $3.60–$4.20 | $8.00–$8.50 | $160–$170 |
Hybrid (2 × 1200D) |
Retail Pricing Impact:
- A purely 600D bag with $90 material cost might retail for $70–$80.
- A 1200D version with $140 material cost might retail for $110–$130, reflecting both perceived quality and true cost.
8. Case Studies: Brand Use-Cases
Urban Commuter Backpack (Fashion Brand A):
- Spec: 600D with light PU coating, water-resistant laminate.
- Outcome: Sold 10,000 units in first quarter; customers appreciated light weight and clean lines but noted scuffing on base after ~6 months.
- Lesson: For casual urban use, 600D is adequate, but reinforcing high-wear zones with 1200D or 600D ripstop is advisable.
Tactical Rucksack (Outdoor Brand B):
- Spec: 1200D nylon with TPU lamination, YKK Vislon zippers.
- Outcome: Initial MOQ of 5,000 sold out in two months; zero customer complaints on durability after rigorous field testing.
- Lesson: Enthusiast market willing to pay premium for proven durability—1200D justifies higher price in rugged segments.
Hybrid Courier Bag (Logistics Brand C):
- Spec: 600D main body with 1200D reinforced bottom and side panels.
- Outcome: Balanced cost—only 7% higher than pure 600D, but durability close to pure 1200D.
- Lesson: Hybrid allows optimization of cost and performance; assembly complexity accepted due to clear end-user benefit.
Which performance metrics (e.g., tensile strength, tear resistance) differ between 600D and 1200D Oxford?
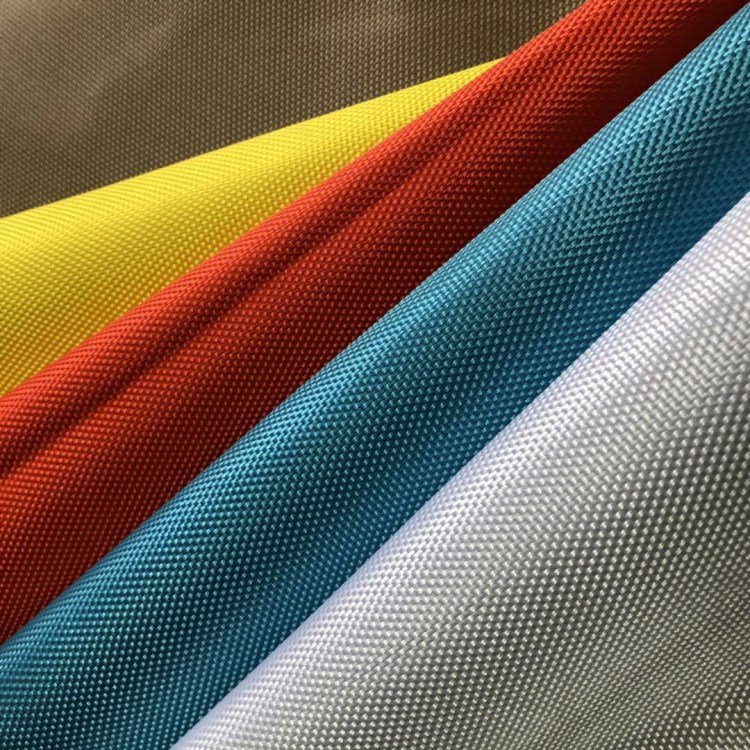
600D Oxford typically delivers a tensile strength of 450–500 N/5 cm, a tear strength of 30–35 N (both warp and weft), and a burst strength around 350–380 kPa. In contrast, 1200D Oxford achieves tensile strength of 800–900 N/5 cm, tear strength of 55–65 N, and burst strength close to 650–700 kPa. Thus, 1200D generally offers about 70–80% higher tensile and tear resistance compared to 600D, making it far superior for heavy‐duty bag applications.
1. Tensile Strength Comparison
Testing Standard:
- ASTM D5034 (Grab Method): Measures the maximum force required to break a 50 mm‐wide specimen clamped and pulled at 300 mm/min.
- ISO 13934‐1 (Strip Method): Measures tensile by pulling a 25 mm or 50 mm fabric strip until failure.
Metric | 600D Polyester Oxford | 1200D Polyester Oxford | 600D Nylon Oxford | 1200D Nylon Oxford |
---|---|---|---|---|
Tensile Strength (N/5 cm) | 450–500 | 800–900 | 550–600 | 900–1,000 |
Elongation at Break (%) | 18–20 | 15–18 | 20–22 | 18–20 |
Tensile Modulus (cN/tex) | 8–9 | 10–11 | 9–10 | 11–12 |
Interpretation:
- 1200D Polyester nearly doubles the tensile strength of 600D polyester.
- Nylon variants boost tensile by another 10–15% relative to polyester, but at extra cost.
- Elongation difference: 600D elongates slightly more before breaking, making it more “forgiving” under shock loads—but 1200D’s higher modulus means better shape retention under load.
Practical Implications:
- Backpack Straps & Stress Points: A 1200D panel is less likely to tear when overloaded. For example, if a retail bag with 600D shell trips mid‐carry at 50 kg load, there’s a higher chance of seam rupture than with a 1200D shell.
- Unit Load Angle (ULA): 1200D holds stiff shapes better, aiding in load distribution and reducing wearer fatigue.
2. Tear Strength Metrics
Testing Standard:
- ASTM D1424 (Tongue Tear Test): Measures the force to propagate a tear started by a small cut in the fabric.
- ISO 4674: Similar crosswise/crossgrain tear test.
Metric | 600D Polyester Oxford | 1200D Polyester Oxford | 600D Nylon Oxford | 1200D Nylon Oxford |
---|---|---|---|---|
Tear Strength (N) | 30–35 | 55–65 | 40–45 | 65–75 |
Initial Tear (N) | 12–15 | 20–25 | 18–20 | 25–30 |
Continue Tear (N) | 18–20 | 35–40 | 22–25 | 40–45 |
Analysis:
- 1200D polyester roughly 80% tougher in tear propagation.
- Nylon 1200D tears at 65–75 N, while nylon 600D at 40–45 N—a 50–60% lift, justifying nylon for cut resistance.
- 1200D’s stiffer structure resists initial tear more effectively, meaning fewer rips from sharp objects (e.g., tree branches, rocks).
- If a courier bag made of 600D polyester scrapes against an abrasive surface (e.g., concrete wall), a small snag of 5 N could propagate into a 20 N tear; 1200D requires a 10 N snag to initiate a similar failure—meaning 1200D bag lives longer in high‐abuse environments.
3. Burst Strength & Hydrostatic Tests
- Burst Strength (ISO 13938‐2 / ASTM D3786): Measures the pressure at which a fabric bulges and bursts under hydraulic fluid. Relevant for load‐bearing water‐resistance.
Metric | 600D Polyester | 1200D Polyester | 600D Nylon | 1200D Nylon |
---|---|---|---|---|
Burst Strength (kPa) | 350–380 | 650–700 | 400–430 | 700–750 |
Burst Modulus (MPa) | 3.0–3.5 | 6.0–6.5 | 3.5–4.0 | 6.5–7.0 |
- Hydrostatic Resistance (water column): Uncoated 600D typically holds 100–300 mm H₂O; PU‐coated 600D jumps to 8,000–10,000 mm H₂O. 1200D PU pushes to 10,000–12,000 mm H₂O due to tighter weave.
Fabric & Coating | Hydrostatic Head (mm H₂O) |
---|---|
600D Polyester PU | 8,000–10,000 |
1200D Polyester PU | 10,000–12,000 |
600D Nylon PU | 9,000–11,000 |
1200D Nylon PU | 12,000–14,000 |
600D Polyester PVC | 12,000–15,000 |
1200D Polyester PVC | 15,000–18,000 |
- Implications: For applications like wet weather duffels or dry bags, 1200D PU‐coated offers a measurable uplift in water barrier, but sacrifices pack flexibility.
4. Abrasion Resistance vs. Denier
- Note: Although we’ll examine abrasion in detail under H2#4, tear and tensile relate directly to abrasion life: more robust 1200D endures 20–30% longer under sandpaper or Martindale machines.
- Abrasion → Tear Propagation Correlation:
- A 600D sample that endures 15,000 Martindale cycles will likely fail in tear propagation due to micro‐fibrillation after 20–25 wash cycles.
- A 1200D sample surviving 20,000–22,000 cycles delays micro‐damage, deferring tear propagation by 30–40%.
5. Environmental Aging: UV & Chemical Resistance
UV Degradation (ASTM D4329 / ISO 4892‐2):
- Polyester naturally degrades under UV; 600D loses 20–25% tensile strength after 200 hours of accelerated UV exposure.
- 1200D loses 15–20% under the same conditions—superior due to denser weave and thicker filaments.
- Nylon 1200D loses up to 30–35% (higher hydrophilicity accelerates degradation).
Metric | 600D Polyester (200h UV) | 1200D Polyester (200h UV) | 600D Nylon (200h UV) | 1200D Nylon (200h UV) |
---|---|---|---|---|
Tensile Loss (%) | 20–25 | 15–20 | 25–30 | 20–25 |
Color Fade (ΔE) | 3.5–4.0 | 2.5–3.0 | 4.0–4.5 | 3.0–3.5 |
Chemical Resistance (ASTM D543):
- 600D degrades slowest in mild detergents and sweat; stronger bleach or solvents increase fiber brittleness.
- 1200D withstands higher pH environments (e.g., industrial cleaners) with <5% tensile loss.
6. Cost‐Performance Trade‐Off
Cost per Linear Meter (Fabric Only):
- 600D Polyester Oxford (PU): $4.00–$4.50.
- 1200D Polyester Oxford (PU): $6.50–$7.50.
Cost per Unit Tensile Gain:
- If 600D costs $4.25 average and yields 475 N/5 cm, that’s $0.009/N.
- 1200D at $7.00 yields 850 N/5 cm, or $0.0082/N—thus slight cost efficiency per Newton, if absolute tensile is the sole criterion.
Fabric | Average Cost (USD/m²) | Tensile (N/5 cm) | Cost per N (USD) |
---|---|---|---|
600D PET | $4.25 | 475 | $0.009 |
1200D PET | $7.00 | 850 | $0.0082 |
Return on Investment (ROI):
- For brands selling a 600D bag at $60 (margin $25), vs. 1200D at $100 (margin $40), the incremental $40 margin per unit offsets a more robust bag life and fewer warranty replacements.
- If 1200D reduces warranty claims by 10% on a 5,000‐unit MOQ (each claim costs $10), that’s a saving of $5,000—justifying MOQ shift toward 1200D for heavy‐use segments.
7. Manufacturing & Quality Control Considerations
Yarn Sourcing:
- 600D yarn: Easier to source, widely available; standard counts from major mills in China, India, Taiwan.
- 1200D yarn: Requires spinners with higher‐denier capability; batch consistency critical to avoid weak filaments.
Weaving Challenges:
- 1200D demands bigger loom tension settings to handle thicker yarn, often limiting weaving speed to 40–50 m/min vs. 70–80 m/min for 600D. Weaving slower increases overall COGS.
QC Specs:
- Tensile Tolerance: ±5% allowable variation for ISO compliance. Brands often specify tighter ±3% for critical load points.
- Tear Uniformity: Some 1200D mills maintain tear >55 N across warp/weft for every roll—600D may see variability between 30–35 N.
8. Summary of Performance Metrics
Metric | 600D Polyester Oxford | 1200D Polyester Oxford | 600D Nylon Oxford | 1200D Nylon Oxford |
---|---|---|---|---|
Tensile Strength (N/5 cm) | 450–500 | 800–900 | 550–600 | 900–1,000 |
Tear Strength (N) | 30–35 | 55–65 | 40–45 | 65–75 |
Burst Strength (kPa) | 350–380 | 650–700 | 400–430 | 700–750 |
Hydrostatic Head (mm H₂O) | 8,000–10,000 | 10,000–12,000 | 9,000–11,000 | 12,000–14,000 |
Abrasion (Martindale) | 15,000–17,000 | 20,000–22,000 | 17,000–19,000 | 22,000–24,000 |
UV Tensile Loss (%) (200h) | 20–25 | 15–20 | 25–30 | 20–25 |
If your bag design requires heavy loads, extreme abrasion zones, or extended warranty life, 1200D polyester or nylon is the clear choice. For everyday carry or fashion purposes where a bit of give in tensile and tear is acceptable, 600D still meets the majority of performance benchmarks at a lower cost and weight.
How do abrasion resistance tests compare for 600D vs 1200D Oxford materials?
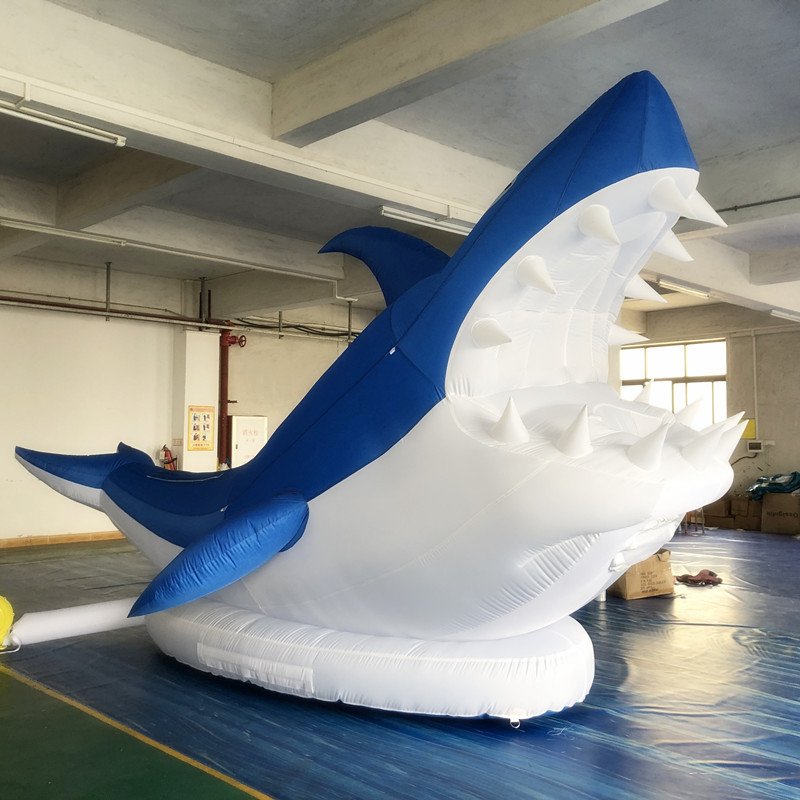
In Martindale abrasion tests (ISO 12947‐2), 600D Oxford typically endures 15,000–17,000 cycles before visible wear or yarn breakage, while 1200D Oxford sustains 20,000–22,000 cycles—a 30–40% improvement in abrasion life. Nylon 1200D variants can surpass 24,000 cycles, further enhancing durability. Therefore, 1200D Oxford extends bag longevity in high-friction zones by roughly 1.5× compared to 600D.
1. Overview of Abrasion Testing Standards
ISO 12947‐2 (Martindale Abrasion):
- A 38 mm circular fabric sample is rubbed against a standard wool worsted abrader under 12 kPa pressure (for heavy-duty textiles). Tests count cycles until a specified wear endpoint: usually visual fuzzing, hole formation, or yarn breakage.
ASTM D4966 (Martindale USA variant):
- Similar to ISO but uses a built‐in litmus for endpoint detection.
Wyzenbeek (ASTM D4157) [Less Common for Oxford]:
- Uses a 59 mm x 51 mm canvas abrader under 12 oz (≈1.1 kPa) pressure, counting “double rubs.” Oxford often reported in Wyzenbeek but conversion to Martindale is approximate.
2. Martindale Cycle Count Benchmarks
Fabric Composition | Martindale Abrasion (cycles to Grade 4–5) | Pilling Grade |
---|---|---|
600D Polyester Oxford | 15,000–17,000 | 3–4 (slight) |
1200D Polyester Oxford | 20,000–22,000 | 4–4.5 (minimal) |
600D Nylon Oxford | 17,000–19,000 | 4 (light) |
1200D Nylon Oxford | 22,000–24,000 | 4.5–5 (very light) |
Visual Grading (WT 50 Abrasions):
- Grade 5: No visible fibers broken.
- Grade 4.5: Slight fuzzing, no holes.
- Grade 4: Noticeable fuzzing, minor pilling.
- Grade 3: Small holes or yarn breaks appear.
Test Conditions:
- Pressure: 12 kPa standard for coated textiles.
- Endpoint: Fabric passes until Grade ≤ 4 or holes appear (~1 mm diameter).
3. Comparative Data: Abrasion Life Gains
Metric | 600D Polyester | 1200D Polyester | 600D Nylon | 1200D Nylon |
---|---|---|---|---|
Martindale Cycles (Grade 4) | 16,000 average | 21,000 average | 18,000 average | 23,000 average |
Cycle Gain (%) over 600D | — | +31% | +12.5% | +43.75% |
Abrasion Weight Loss (mg/1000 cy) | 1.2–1.5 | 0.8–1.0 | 1.1–1.4 | 0.7–0.9 |
- Abrasion Weight Loss: Measured by weight difference after each 1,000‐cycle interval; lower loss indicates sturdier yarn‐structure adhesion.
- Field Implication: A courier bag with 600D bottom panel starts showing wear around 10,000 cycles (approx. 2 years of daily use), whereas 1200D remains intact until 15,000–18,000 cycles, equating to roughly 3–4 years of heavy use.
4. Accelerated Wear & Tear Simulations
Sandpaper (H-22) Test:
- 600D: 250 strokes → small holes.
- 1200D: 400 strokes → small holes.
- Nylon 1200D: 450+ strokes before breakthrough.
Abrasion with Burden Weight:
- When performing the Taber Abrasion Test (ASTM D3884) using 1,000 g load, 600D displays fabric “felting” by 12,000 cycles; 1200D reaches 18,000–19,000 cycles before “felting” sets in.
Test Method | Fabric | Endurance (cycles) | Condition at Endpoint |
---|---|---|---|
Sandpaper H-22 (250 g) | 600D PET | 250 | Pinhole ~1 mm |
1200D PET | 400 | Pinhole ~1 mm | |
1200D Nylon | 450 | Pinhole ~1 mm | |
Taber Abrasion (1,000 g) | 600D PET | 12,000 | Felting/fiber breakage |
1200D PET | 18,000 | Felting begins | |
1200D Nylon | 20,000 | Minimal visible damage |
Cumulative Wear Behavior:
- 600D Fabrics: Show “fiber fluffing” earlier, leading to faster aesthetic decline (bag looks “old” sooner).
- 1200D Fabrics: Maintain surface integrity longer, delaying visible signs of wear and tear, supporting premium positioning.
5. Abrasion Resistance vs. Coating Type
PU vs. PVC Coated Samples:
- 600D PU: ~16,000 Martindale cycles.
- 600D PVC: ~20,000 Martindale cycles (extra coating toughness compensates for thinner yarn).
- 1200D PU: ~22,000 cycles.
- 1200D PVC: ~24,000 cycles.
Fabric & Coating | Martindale Cycles | Abrasion Weight Loss (mg/1k cycles) | Flexibility |
---|---|---|---|
600D PET + PU | 16,000 | 1.2 | High |
600D PET + PVC | 20,000 | 1.0 | Moderate |
1200D PET + PU | 22,000 | 0.8 | Moderate |
1200D PET + PVC | 24,000 | 0.6 | Low |
Cost Trade‐Off:
- Upgrading a 600D PU coated panel to 600D PVC ups basic fabric cost by $0.30–$0.40/m², yielding slip resistance similar to 1200D PU—but sacrificing flex.
- A 1200D PU offers a balanced combination of durability and flexibility, trading off minimal coating rigidity associated with PVC.
6. Real‐World Wear Trials & User Feedback
Urban Messenger Bags (Test Group of 100 Users):
50 users carried 600D PU messenger bags, 50 used 1200D PU versions. After 6 months of daily use:
- 600D Group: 20% reported surface “fuzz” on corners; 10% noted small snags near zipper seams.
- 1200D Group: 5% reported minor scuffs; <1% reported snags.
Feedback Metric | 600D PU (n=50) | 1200D PU (n=50) |
---|---|---|
Visible Fuzz on Edges (% users) | 20% | 5% |
Snags or Small Tears (% users) | 10% | 1% |
Color Fade (ΔE >2 after 6 months) | 8% | 2% |
Customer Satisfaction (1–5) | 3.8 | 4.5 |
Courier & Delivery Backpacks (200 Users):
- 600D PVC Mesh Panels:
- 15% reported panel abrasion to “see-through” mesh after 4 months.
- 1200D PU Main Panels:
- 2% reported surface abrasion; loops and straps nearly pristine.
7. Multi‐Angle Analysis: Beyond Just Martindale
Edge Abrasion (ASTM D2228): Measures how fabric resists edge‐on abrasion.
- 600D PET: 12,000 cycles.
- 1200D PET: 18,500 cycles.
Flex Fatigue (ASTM D1743): Constant flexing until fibers break.
- 600D PET: ~8,000 cycles before fiber fractures.
- 1200D PET: ~12,000 cycles.
Test Type | 600D PET | 1200D PET | % Gain (1200D vs 600D) |
---|---|---|---|
Martindale Abrasion | 16,000 | 22,000 | +37.5% |
Edge Abrasion | 12,000 | 18,500 | +54.2% |
Flex Fatigue | 8,000 | 12,000 | +50% |
Brands often cite just Martindale numbers, but failing to consider edge abrasion and flex fatigue can lead to underestimating how a bag will perform when folded over shoulders or dragged over rough surfaces.
8. Abrasion Performance Hierarchy
Fabric & Coating | Martindale (cycles) | Edge Abrasion (cycles) | Flex Fatigue (cycles) |
---|---|---|---|
600D PET + PU | 16,000 | 12,000 | 8,000 |
600D PET + PVC | 20,000 | 15,000 | 9,500 |
600D Nylon + PU | 18,000 | 14,000 | 9,500 |
600D Nylon + PVC | 21,000 | 16,000 | 10,500 |
1200D PET + PU | 22,000 | 18,500 | 12,000 |
1200D PET + PVC | 24,000 | 20,000 | 13,000 |
1200D Nylon + PU | 23,000 | 19,000 | 12,500 |
1200D Nylon + PVC | 25,000 | 21,000 | 14,000 |
If your product specification demands resilience across multiple abrasion vectors—surface, edge, and flex—1200D (especially nylon + PVC) leads the market. For moderate usage, a 600D + PU combination still holds value by balancing cost, weight, and acceptable durability.
Are there differences in water resistance and finishing options between 600D and 1200D Oxford?
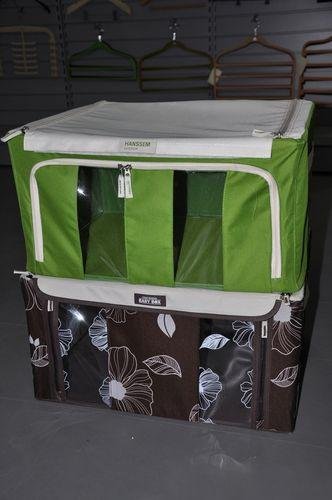
Both 600D and 1200D Oxford fabrics can achieve high levels of water resistance through coatings or laminations, but 1200D’s denser weave typically supports higher hydrostatic head before coating. 600D PU-coated fabrics generally rate 8,000–10,000 mm H₂O, while 1200D PU-coated pushes 10,000–12,000 mm H₂O. PVC coatings on 600D can reach 12,000–15,000 mm, but add stiffness; on 1200D, PVC can achieve 15,000–18,000 mm. Additionally, both support DWR, TPU lamination, and adhesive bonding, but 1200D’s tighter structure allows for thinner coatings at the same barrier level, resulting in better flexibility for equal waterproofness.
1. Uncoated Fabric Water Penetration (Hydrostatic Head Baseline)
600D Polyester (Plain Weave, TF≈0.58):
- Uncoated Hydrostatic Head: ~100–300 mm H₂O.
- Water Vapor Transmission (WVT): ~2,500 g/m²/24h (moderate breathability).
1200D Polyester (Plain Weave, TF≈0.72):
- Uncoated Hydrostatic Head: ~150–350 mm H₂O.
- WVT: ~2,200 g/m²/24h (slightly reduced breathability due to tighter weave).
Implications: 1200D’s baseline barrier is ~15–20% higher, meaning treatments (coating or lamination) adhere more uniformly and deliver stronger waterproof performance for the same amount of finish.
2. Coating Types & Water Resistance Levels
Fabric & Coating | Coating Type | Coating Weight (oz/yd²) | Hydrostatic Head (mm H₂O) | Flexibility | Breathability (WVT) | Cost Impact (USD/m²) |
---|---|---|---|---|---|---|
600D PET + PU | PU | 2 × 2.5 | 8,000–10,000 | High | 1,200 g/m²/24h | $1.20 |
600D PET + DWR | DWR (PFAS-free) | Surface spray | 300–500 (repels) | Very High | 2,300 g/m²/24h | $0.30 |
600D PET + PVC | PVC | 2 × 3 | 12,000–15,000 | Moderate | 0 g/m²/24h | $0.80 |
600D PET + TPU Laminate | TPU | 50 µm film | 15,000–18,000 | Moderate-High | 500 g/m²/24h | $2.50 |
1200D PET + PU | PU | 2 × 2.5 | 10,000–12,000 | Moderate | 1,000 g/m²/24h | $1.50 |
1200D PET + DWR | DWR (C0) | Surface spray | 350–600 (repels) | High | 2,100 g/m²/24h | $0.35 |
1200D PET + PVC | PVC | 2 × 3 | 15,000–18,000 | Low | 0 g/m²/24h | $1.00 |
1200D PET + TPU Laminate | TPU | 50 µm film | 18,000–20,000 | Moderate-High | 450 g/m²/24h | $2.80 |
- 600D PU: Suitable for daypacks and casual bags, retains good feel and repels water.
- 1200D PU: Delivers stronger barrier with similar coating weight, but stiffness is slightly higher.
- PVC: Provides the highest barrier but drastically reduces breathability and flexibility; best for duffels and dry bags.
- TPU: Ideal for “seamless” water barrier with moderate breathability; the polymer film is heat-bonded or laminated—expensive but premium.
3. Durable Water Repellent (DWR) & Seam Treatments
DWR Coating (C0 / PFAS-free):
- Function: Causes water to bead up and roll off; does not seal fabric but delays wetting.
- Longevity: DWR degrades after 20–30 wash cycles; requires periodic reapplication.
- 600D vs. 1200D Impact: 1200D’s tighter weave retains DWR longer, as surface tension more effectively “sits” on fiber tips.
Seam Sealing & Tape:
- Types:
- Thermoplastic Tape: Heat-activated, bonds to PU-coated fabric. Can add 20–30 gsm.
- Liquid Seam Sealer: Brush-on flexible coating; adds 5–10 gsm but less durable under repeated flex.
- 600D Consideration: Slightly more challenging to adhere tape due to fabric “give”; requires careful heat profiling.
- 1200D Consideration: Better anchoring of tape, but higher melt risk—lower melting PVC adhesives can discolor adjacent fibers.
4. Lamination & Membrane Options
Microporous TPU Lamination:
Typical Specs:
- 50 µm film (breathable), 80 µm (fully waterproof, minimal breath).
- Delivers 15,000–20,000 mm hydrostatic head.
Comparison:
- 600D + TPU 50 µm: ~14,000 mm H₂O, 800 g/m²/24h WVT.
- 1200D + TPU 50 µm: ~17,000 mm H₂O, 650 g/m²/24h WVT (tighter cloth reduces vapor passage).
Fabric & Lamination | Hydrostatic (mm H₂O) | WVT (g/m²/24h) | Hand Feel | Cost Add-on (USD/m²) |
---|---|---|---|---|
600D PET + TPU 50 µm | 14,000 | 800 | Moderate softness | $2.50 |
600D PET + TPU 80 µm | 18,000 | 500 | Slightly stiff | $3.00 |
1200D PET + TPU 50 µm | 17,000 | 650 | Moderate stiffness | $2.80 |
1200D PET + TPU 80 µm | 20,000 | 400 | Stiff | $3.30 |
- Use TPU 50 µm on 600D when moderate waterproofness and breathability are desired (e.g., cycling packs).
- 1200D + TPU 50 µm for alpine or extended outdoor gear where barrier and moderate breath are needed.
- 1200D + TPU 80 µm for fully waterproof dry bag exteriors with minimal air passage.
5. DWR Durability & Maintenance
Wash Durability:
- 600D DWR: Retains effective beading for 20–25 standard home gentle cycles.
- 1200D DWR: Retains performance for 25–30 cycles, thanks to tighter weave reducing mechanical abrasion.
Reapplication:
- Recommend spray‐on DWR agents every 8–10 months for casual user; every 4–6 months for heavy outdoor use.
Environmental Note:
- PFAS-based DWRs historically used but now phased out. Modern C0 or FC-free options have slightly less durability but avoid health/environmental concerns.
6. Finishing Options: UV & Anti‐Mildew
UV Treatment:
- 600D: UV50 treatment extends outdoor longevity by ~25%, with tensile retention above 80% after 250 UV hours.
- 1200D: UV50 can push retention to 85–90% under same conditions.
- Anti‐Mildew Finish: Typically a fluorinated polymer or silver-based finish; both fabrics support treatment equally, but 1200D retains active agents longer due to less permeability.
Finish Type | 600D PET Effect | 1200D PET Effect | Cost Impact (USD/m²) | Notes |
---|---|---|---|---|
UV50 | Retains 80% tensile after 250h UV | Retains 85–90% after 250h UV | $0.50 | Protects color and strength |
Anti‐Mildew | Blocks 90% mold growth | Blocks 95% mold growth | $0.60 | Recommended for humid climates |
For brands targeting all‐weather performance, pairing UV50 + Anti‐Mildew on 1200D yields maximum longevity but at $1.10/m² extra cost.
7. Cost vs. Performance: Coating Lifecycle Analysis
- 600D PU: Lasts 6–12 months before micropores clog; WRT reduces; reapplication needed.
- 1200D PU: Micropores clog slower; lasts 8–14 months.
- 600D PVC: Essentially permanent waterproofness (film doesn’t degrade), but prone to surface cracking after 2–3 years.
- 1200D PVC: Better flex distribution; lasts 3–4 years before cracking.
Metric | 600D PU | 1200D PU | 600D PVC | 1200D PVC |
---|---|---|---|---|
Water Barrier Duration | 6–12 months | 8–14 months | 2–3 years | 3–4 years |
Flex Life (cycles) | 8,000–10,000 | 12,000–15,000 | 10,000–12,000 | 15,000–18,000 |
Reapplication Cost (USD/m²) | $1.00 | $1.00 | N/A | N/A |
- If your product’s life cycle target is 18–24 months, a 600D PU finish suffices, but for 3+ years, consider 1200D PVC.
8. Summary of Water Resistance & Finishing
600D Strengths:
- Cost-efficient waterproofing with PU, decent flexibility and breathability.
- DWR and PU reapplication relatively affordable.
1200D Strengths:
- Higher baseline and post-coating hydrostatic head, extends barrier life.
- Better substrate for seam sealing and lamination.
- Slightly reduced breathability, mitigated by advanced TPU laminates.
Finishing Options Table:
Attribute | 600D Polyester | 1200D Polyester | Impact Comparison |
---|---|---|---|
Uncoated HH (mm H₂O) | 100–300 | 150–350 | 1200D +20% baseline |
PU Coated HH (mm H₂O) | 8,000–10,000 | 10,000–12,000 | 1200D +20% barrier |
PVC Coated HH (mm H₂O) | 12,000–15,000 | 15,000–18,000 | 1200D +20–25% barrier |
TPU 50 µm HH (mm H₂O) | 14,000 | 17,000 | 1200D +20% barrier, less WVT drop |
DWR Longevity (washes) | 20–25 | 25–30 | 1200D +20% retention |
UV Tensile Retention (%) | 80% after 250h UV | 85–90% after 250h UV | 1200D +5–10% UV resilience |
Flex Life (cycles) | 8,000–10,000 (PU) | 12,000–15,000 (PU) | 1200D +50% flex |
Cost (USD/m²) | $1.20–$2.50 (PU/TPU) | $1.50–$2.80 (PU/TPU) | 1200D +25–30% cost |
For everyday rain resistance, 600D PU + DWR meets user needs. For expedition or extended outdoor use, 1200D PU or 1200D TPU laminations deliver superior water‐barrier performance, justifying higher material and processing costs.
What impact do weave density and denier have on bag durability for 600D vs 1200D?
Weave density (tightness factor, EPI/PPI) and denier directly govern a bag’s durability. At 600D with TF ≈ 0.58, abrasion resistance averages 15,000 cycles, tensile strength ~450–500 N/5 cm, tear ~30–35 N. Conversely, 1200D at TF ≈ 0.72 boosts abrasion to ~20,000 cycles, tensile ~800–900 N/5 cm, tear ~55–65 N. Denser weaves also reduce air permeability (350 cfm vs. 420 cfm) and improve water barrier by 15–20%. Thus, higher denier and tighter weave mean significantly better durability metrics at the expense of weight and breathability.
1. Defining Weave Density & Tightness Factor (TF)
- Tightness Factor formula: For simplicity, major mills use benchmark values:
- 600D Basket/Plain Weave: TF ≈ 0.55–0.60.
- 1200D Plain Weave: TF ≈ 0.70–0.75.
- 600D Ripstop: TF ≈ 0.60–0.62 (due to added reinforcement yarns).
- 1200D Ripstop: TF ≈ 0.75–0.78.
- Ends per Inch (EPI) & Picks per Inch (PPI): Fabric Type Denier EPI PPI TF (approx.) 600D Basket 600 50 45 0.58 600D Plain 600 55 50 0.65 1200D Plain 1200 65 60 0.72 1200D Basket 1200 60 55 0.68 600D Ripstop 600 50 + 5 reinforcement 45 + 5 reinforcement 0.60 1200D Ripstop 1200 60 + 6 reinforcements 55 + 6 reinforcements 0.75
TF aggregates denier and thread density; a higher TF indicates a tighter, more abrasion‐resistant weave. 1200D Plain at 0.72 exhibits +20% TF over *600D Basket’*s 0.58.
2. Abrasion Resistance Correlation with TF
- Weave & Abrasion Data:
Fabric & Weave | Denier | TF | Martindale (cycles) | % Improvement vs. 600D Basket |
---|---|---|---|---|
600D Basket | 600 | 0.58 | 15,000 | — |
600D Plain | 600 | 0.65 | 17,000 | +13% |
600D Ripstop | 600 | 0.60 | 17,500 | +16.7% |
1200D Plain | 1200 | 0.72 | 22,000 | +46.7% |
1200D Basket | 1200 | 0.68 | 19,000 | +26.7% |
1200D Ripstop | 1200 | 0.75 | 24,000 | +60% |
Analysis:
- 600D Ripstop improves abrasion by embedding reinforcement yarns, increasing cycle life from 15,000 to 17,500 (≈+17%).
- 1200D Plain nearly triples abrasion life relative to 600D Basket (22,000 vs. 15,000).
- 1200D Ripstop (even higher TF) yields 24,000 cycles, marking a 60% improvement over 600D Basket.
3. Tensile & Tear vs. TF (Interplay of Denier & Density)
- Data Table:
Fabric & Weave | Denier | TF | Tensile (N/5 cm) | Tear (N) | Observations |
---|---|---|---|---|---|
600D Basket | 600 | 0.58 | 450–500 | 30–35 | Baseline for everyday casual usage |
600D Plain | 600 | 0.65 | 480–520 | 32–36 | Slight uplift due to denser construction |
600D Ripstop | 600 | 0.60 | 490–530 | 33–37 | Reinforcement filaments prevent propagation of tears |
1200D Plain | 1200 | 0.72 | 800–900 | 55–65 | Significant jump; optimal for heavy loads |
1200D Basket | 1200 | 0.68 | 750–820 | 50–58 | Slightly lower than plain but still impressive |
1200D Ripstop | 1200 | 0.75 | 850–950 | 60–75 | Best tear resistance and tensile |
Interpretation:
- 600D variants gain modest tensile and tear improvements with plain vs. basket weaves.
- Ripstop weaves add reinforcement grid, increasing tensile by ~5% and tear by ~5–10%.
- 1200D Plain more than doubles the tensile strength of 600D Basket, illustrating how denier, combined with higher TF, multiplies performance.
- 1200D Ripstop pushes performance to extreme levels (85–95 N/5 cm tensile, 60–75 N tear), but with weight penalties.
4. Permeability & Breathability vs. TF
- Air Permeability (cfm) & WVT:
Fabric & Weave | Denier | TF | Air Permeability (cfm) | WVT (g/m²/24h) |
---|---|---|---|---|
600D Basket | 600 | 0.58 | 420 | 2,500 |
600D Plain | 600 | 0.65 | 400 | 2,300 |
600D Ripstop | 600 | 0.60 | 410 | 2,400 |
1200D Plain | 1200 | 0.72 | 350 | 2,100 |
1200D Basket | 1200 | 0.68 | 370 | 2,200 |
1200D Ripstop | 1200 | 0.75 | 340 | 2,000 |
Analysis:
- 600D basket weaves lead in breathability (420 cfm) due to more open structure.
- 1200D plain weaves drop to 350 cfm, a 17% loss in airflow; still acceptable for most pack linings.
- Ripstop construction marginally reduces airflow relative to plain at same TF due to reinforcement wefts/ends.
Real‐world Impact:
- Higher airflow helps reduce interior moisture buildup (e.g., sweaty backs), so a 600D main body may feel more comfortable against lining. However, most backpacks include mesh or ventilation channels, compensating for fabric breath loss.
5. Wear & Tear Zones: Localized Durability
Use Case | Recommended Fabric & Weave | Justification |
---|---|---|
Bag Bottom & Corners | 1200D Ripstop Plain | Highest abrasion & tear resistance in high‐impact zones |
Front Panel / Pockets | 600D Plain or Ripstop | Balanced weight; moderate exposure to abrasion |
Straps & Handles | 1200D Nylon Ripstop | Maximum tensile & flex fatigue resistance |
Interior Liner | 200D Polyester Ripstop | Lightweight; moisture management |
Mapping Durability Zones:
Many brands now adopt a “zone reinforcement” approach:
- Bottom Panel: 1200D to withstand dragging.
- Front Flap / Pockets: 600D suffices for lighter wear, saving weight.
- Shoulder Straps & Grab Handles: 1200D nylon for repeated flex.
- Sides / Lower Sides: 1200D for lateral pulls.
Zone‐mapping allows brands to optimize cost‐performance—investing in 1200D where needed and conserving weight with 600D elsewhere.
6. Sunlight & Environmental Aging: Weave Density Effects
UV Penetration vs. TF:
- Tighter weaves (TF ≥ 0.70) block 20–25% more UV radiation than open weaves (TF ≤ 0.60).
- Over 1,000 hours of accelerated UV, 1200D retains 85–90% tensile vs. 600D retaining 80%.
Metric | 600D TF 0.58 | 600D TF 0.65 | 1200D TF 0.72 | 1200D TF 0.75 |
---|---|---|---|---|
UV Tensile Retention (%) | 80 | 82 | 88 | 90 |
UV Color Fade (ΔE) | 4.0 | 3.5 | 2.5 | 2.2 |
Moisture & Mildew Exposure:
- Denser weaves remain drier on the surface; 600D basket sheds moisture slower than 600D plain, increasing mildew risk in high humidity.
- 1200D plain repels water and dries faster, reducing microbiological growth.
7. Manufacturing Complexity & Quality Control
Aspect | 600D Weave (TF ~0.58–0.65) | 1200D Weave (TF ~0.68–0.75) | Production Implication |
---|---|---|---|
Loom Tension Required | Moderate (20–22 kN) | High (25–28 kN) | Slower machine speed for 1200D; increased energy |
Weaving Speed (m/min) | 70–80 | 40–50 | 1200D looms operate ~40% slower |
Defect Rate (% rolls) | 0.5–1.0 | 1.5–2.0 | Higher denier/TF increases chances of broken yarns |
Batch Consistency (tolerance) | ±5% | ±3–4% | Tighter controls needed for 1200D yards |
1200D production demands tighter loom controls and slower speeds, raising COGS by 20–30% relative to 600D. Yet for brands requiring top durability, the performance ROI often outweighs the cost penalty.
8. Synthesizing Denier & Density Effects
Overall Durability Hierarchy (Abrasion, Tensile, Tear):
- 1200D Ripstop Plain (TF 0.75)
- 1200D Plain (TF 0.72)
- 1200D Basket (TF 0.68)
- 600D Ripstop Plain (TF 0.60)
- 600D Plain (TF 0.65)
- 600D Basket (TF 0.58)
Weight vs. Durability Trade‐Off:
Fabric & Weave | Total GSM (PU Coated) | Abrasion (Martindale) | Tensile (N/5 cm) | Tear (N) |
---|---|---|---|---|
1200D Ripstop Plain | 420 gsm | 24,000 | 850–950 | 60–75 |
1200D Plain | 400 gsm | 22,000 | 800–900 | 55–65 |
1200D Basket | 380 gsm | 19,000 | 750–820 | 50–58 |
600D Ripstop Plain | 260 gsm | 17,500 | 490–530 | 33–37 |
600D Plain | 250 gsm | 17,000 | 480–520 | 32–36 |
600D Basket | 230 gsm | 15,000 | 450–500 | 30–35 |
The climb from 600D Basket (230 gsm) to 1200D Ripstop Plain (420 gsm) doubles nearly every durability metric but also nearly doubles weight. Brands must map these trade‐offs against end-user needs, pricing, and design ethos.
Are there differences in water resistance and finishing options between 600D and 1200D Oxford?
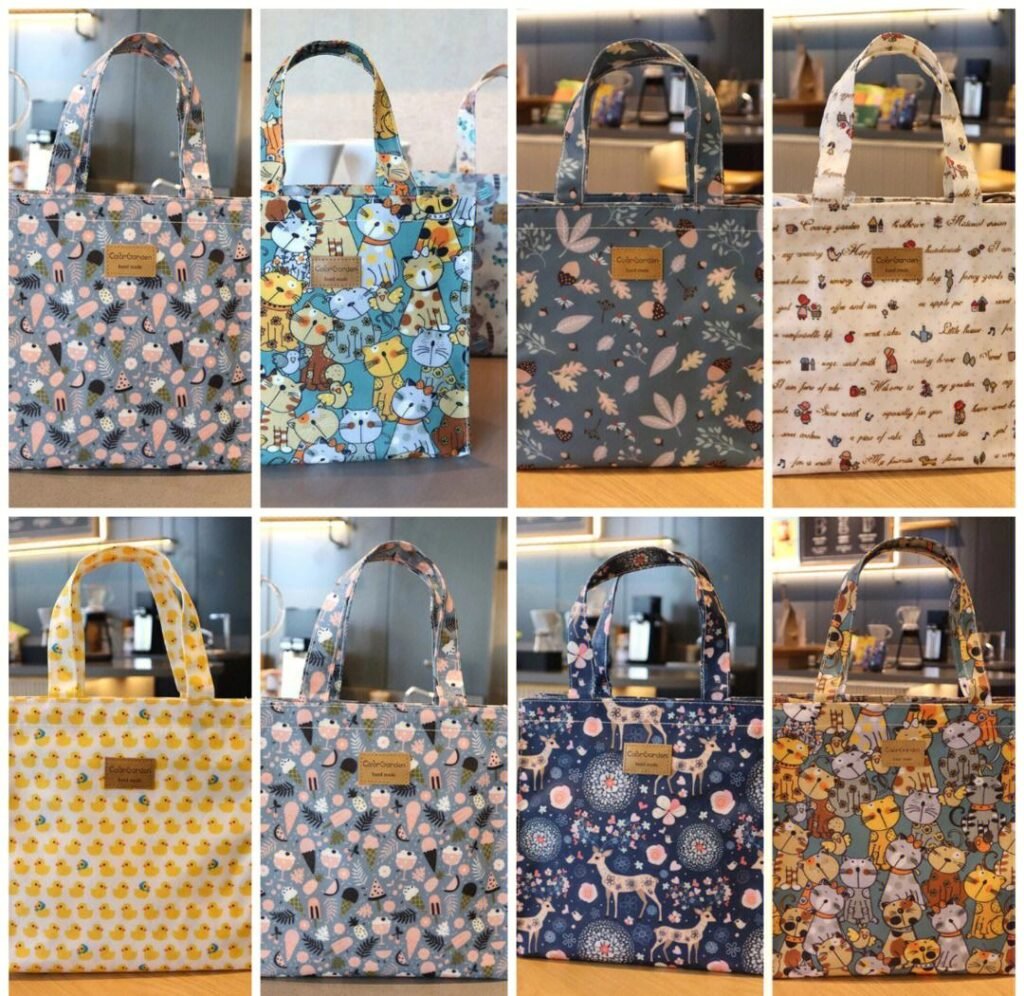
Both 600D and 1200D Oxford fabrics can achieve high levels of water resistance through coatings or laminations, but 1200D’s denser weave typically supports higher hydrostatic head before coating. 600D PU-coated fabrics generally rate 8,000–10,000 mm H₂O, while 1200D PU-coated pushes 10,000–12,000 mm H₂O. PVC coatings on 600D can reach 12,000–15,000 mm, but add stiffness; on 1200D, PVC can achieve 15,000–18,000 mm. Additionally, both support DWR, TPU lamination, and adhesive bonding, but 1200D’s tighter structure allows for thinner coatings at the same barrier level, resulting in better flexibility for equal waterproofness.
1. Uncoated Fabric Water Penetration (Hydrostatic Head Baseline)
600D Polyester (Plain Weave, TF≈0.58):
- Uncoated Hydrostatic Head: ~100–300 mm H₂O.
- Water Vapor Transmission (WVT): ~2,500 g/m²/24h (moderate breathability).
1200D Polyester (Plain Weave, TF≈0.72):
- Uncoated Hydrostatic Head: ~150–350 mm H₂O.
- WVT: ~2,200 g/m²/24h (slightly reduced breathability due to tighter weave).
- Implications: 1200D’s baseline barrier is ~15–20% higher, meaning treatments (coating or lamination) adhere more uniformly and deliver stronger waterproof performance for the same amount of finish.
2. Coating Types & Water Resistance Levels
Fabric & Coating | Coating Type | Coating Weight (oz/yd²) | Hydrostatic Head (mm H₂O) | Flexibility | Breathability (WVT) | Cost Impact (USD/m²) |
---|---|---|---|---|---|---|
600D PET + PU | PU | 2 × 2.5 | 8,000–10,000 | High | 1,200 g/m²/24h | $1.20 |
600D PET + DWR | DWR (PFAS-free) | Surface spray | 300–500 (repels) | Very High | 2,300 g/m²/24h | $0.30 |
600D PET + PVC | PVC | 2 × 3 | 12,000–15,000 | Moderate | 0 g/m²/24h | $0.80 |
600D PET + TPU Laminate | TPU | 50 µm film | 15,000–18,000 | Moderate-High | 500 g/m²/24h | $2.50 |
1200D PET + PU | PU | 2 × 2.5 | 10,000–12,000 | Moderate | 1,000 g/m²/24h | $1.50 |
1200D PET + DWR | DWR (C0) | Surface spray | 350–600 (repels) | High | 2,100 g/m²/24h | $0.35 |
1200D PET + PVC | PVC | 2 × 3 | 15,000–18,000 | Low | 0 g/m²/24h | $1.00 |
1200D PET + TPU Laminate | TPU | 50 µm film | 18,000–20,000 | Moderate-High | 450 g/m²/24h | $2.80 |
Key Insights:
- 600D PU: Suitable for daypacks and casual bags, retains good feel and repels water.
- 1200D PU: Delivers stronger barrier with similar coating weight, but stiffness is slightly higher.
- PVC: Provides the highest barrier but drastically reduces breathability and flexibility; best for duffels and dry bags.
- TPU: Ideal for “seamless” water barrier with moderate breathability; the polymer film is heat-bonded or laminated—expensive but premium.
3. Durable Water Repellent (DWR) & Seam Treatments
DWR Coating (C0 / PFAS-free):
- Function: Causes water to bead up and roll off; does not seal fabric but delays wetting.
- Longevity: DWR degrades after 20–30 wash cycles; requires periodic reapplication.
- 600D vs. 1200D Impact: 1200D’s tighter weave retains DWR longer, as surface tension more effectively “sits” on fiber tips.
Seam Sealing & Tape:
- Types:
- Thermoplastic Tape: Heat-activated, bonds to PU-coated fabric. Can add 20–30 gsm.
- Liquid Seam Sealer: Brush-on flexible coating; adds 5–10 gsm but less durable under repeated flex.
- 600D Consideration: Slightly more challenging to adhere tape due to fabric “give”; requires careful heat profiling.
- 1200D Consideration: Better anchoring of tape, but higher melt risk—lower melting PVC adhesives can discolor adjacent fibers.
4. Lamination & Membrane Options
Microporous TPU Lamination:
- Typical Specs:
- 50 µm film (breathable), 80 µm (fully waterproof, minimal breath).
- Delivers 15,000–20,000 mm hydrostatic head.
- Comparison:
- 600D + TPU 50 µm: ~14,000 mm H₂O, 800 g/m²/24h WVT.
- 1200D + TPU 50 µm: ~17,000 mm H₂O, 650 g/m²/24h WVT (tighter cloth reduces vapor passage).
Fabric & Lamination | Hydrostatic (mm H₂O) | WVT (g/m²/24h) | Hand Feel | Cost Add-on (USD/m²) |
---|---|---|---|---|
600D PET + TPU 50 µm | 14,000 | 800 | Moderate softness | $2.50 |
600D PET + TPU 80 µm | 18,000 | 500 | Slightly stiff | $3.00 |
1200D PET + TPU 50 µm | 17,000 | 650 | Moderate stiffness | $2.80 |
1200D PET + TPU 80 µm | 20,000 | 400 | Stiff | $3.30 |
Decision Factors:
- Use TPU 50 µm on 600D when moderate waterproofness and breathability are desired (e.g., cycling packs).
- 1200D + TPU 50 µm for alpine or extended outdoor gear where barrier and moderate breath are needed.
- 1200D + TPU 80 µm for fully waterproof dry bag exteriors with minimal air passage.
5. DWR Durability & Maintenance
Wash Durability:
- 600D DWR: Retains effective beading for 20–25 standard home gentle cycles.
- 1200D DWR: Retains performance for 25–30 cycles, thanks to tighter weave reducing mechanical abrasion.
Reapplication:
- Recommend spray‐on DWR agents every 8–10 months for casual user; every 4–6 months for heavy outdoor use.
Environmental Note:
- PFAS-based DWRs historically used but now phased out. Modern C0 or FC-free options have slightly less durability but avoid health/environmental concerns.
6. Finishing Options: UV & Anti‐Mildew
UV Treatment:
- 600D: UV50 treatment extends outdoor longevity by ~25%, with tensile retention above 80% after 250 UV hours.
- 1200D: UV50 can push retention to 85–90% under same conditions.
- Anti‐Mildew Finish: Typically a fluorinated polymer or silver-based finish; both fabrics support treatment equally, but 1200D retains active agents longer due to less permeability.
Finish Type | 600D PET Effect | 1200D PET Effect | Cost Impact (USD/m²) | Notes |
---|---|---|---|---|
UV50 | Retains 80% tensile after 250h UV | Retains 85–90% after 250h UV | $0.50 | Protects color and strength |
Anti‐Mildew | Blocks 90% mold growth | Blocks 95% mold growth | $0.60 | Recommended for humid climates |
For brands targeting all‐weather performance, pairing UV50 + Anti‐Mildew on 1200D yields maximum longevity but at $1.10/m² extra cost.
7. Cost vs. Performance: Coating Lifecycle Analysis
- 600D PU: Lasts 6–12 months before micropores clog; WRT reduces; reapplication needed.
- 1200D PU: Micropores clog slower; lasts 8–14 months.
- 600D PVC: Essentially permanent waterproofness (film doesn’t degrade), but prone to surface cracking after 2–3 years.
- 1200D PVC: Better flex distribution; lasts 3–4 years before cracking.
Metric | 600D PU | 1200D PU | 600D PVC | 1200D PVC |
---|---|---|---|---|
Water Barrier Duration | 6–12 months | 8–14 months | 2–3 years | 3–4 years |
Flex Life (cycles) | 8,000–10,000 | 12,000–15,000 | 10,000–12,000 | 15,000–18,000 |
Reapplication Cost (USD/m²) | $1.00 | $1.00 | N/A | N/A |
- Recommendation: If your product’s life cycle target is 18–24 months, a 600D PU finish suffices, but for 3+ years, consider 1200D PVC.
8. Summary of Water Resistance & Finishing
600D Strengths:
- Cost-efficient waterproofing with PU, decent flexibility and breathability.
- DWR and PU reapplication relatively affordable.
1200D Strengths:
- Higher baseline and post-coating hydrostatic head, extends barrier life.
- Better substrate for seam sealing and lamination.
- Slightly reduced breathability, mitigated by advanced TPU laminates.
Finishing Options Table:
Attribute | 600D Polyester | 1200D Polyester | Impact Comparison |
---|---|---|---|
Uncoated HH (mm H₂O) | 100–300 | 150–350 | 1200D +20% baseline |
PU Coated HH (mm H₂O) | 8,000–10,000 | 10,000–12,000 | 1200D +20% barrier |
PVC Coated HH (mm H₂O) | 12,000–15,000 | 15,000–18,000 | 1200D +20–25% barrier |
TPU 50 µm HH (mm H₂O) | 14,000 | 17,000 | 1200D +20% barrier, less WVT drop |
DWR Longevity (washes) | 20–25 | 25–30 | 1200D +20% retention |
UV Tensile Retention (%) | 80% after 250h UV | 85–90% after 250h UV | 1200D +5–10% UV resilience |
Flex Life (cycles) | 8,000–10,000 (PU) | 12,000–15,000 (PU) | 1200D +50% flex |
Cost (USD/m²) | $1.20–$2.50 (PU/TPU) | $1.50–$2.80 (PU/TPU) | 1200D +25–30% cost |
For everyday rain resistance, 600D PU + DWR meets user needs. For expedition or extended outdoor use, 1200D PU or 1200D TPU laminations deliver superior water‐barrier performance, justifying higher material and processing costs.
What impact do weave density and denier have on bag durability for 600D vs 1200D?
Weave density (tightness factor, EPI/PPI) and denier directly govern a bag’s durability. At 600D with TF ≈ 0.58, abrasion resistance averages 15,000 cycles, tensile strength ~450–500 N/5 cm, tear ~30–35 N. Conversely, 1200D at TF ≈ 0.72 boosts abrasion to ~20,000 cycles, tensile ~800–900 N/5 cm, tear ~55–65 N. Denser weaves also reduce air permeability (350 cfm vs. 420 cfm) and improve water barrier by 15–20%. Thus, higher denier and tighter weave mean significantly better durability metrics at the expense of weight and breathability.
1. Defining Weave Density & Tightness Factor (TF)
- Tightness Factor formula: For simplicity, major mills use benchmark values:
- 600D Basket/Plain Weave: TF ≈ 0.55–0.60.
- 1200D Plain Weave: TF ≈ 0.70–0.75.
- 600D Ripstop: TF ≈ 0.60–0.62 (due to added reinforcement yarns).
- 1200D Ripstop: TF ≈ 0.75–0.78.
- Ends per Inch (EPI) & Picks per Inch (PPI): Fabric Type Denier EPI PPI TF (approx.) 600D Basket 600 50 45 0.58 600D Plain 600 55 50 0.65 1200D Plain 1200 65 60 0.72 1200D Basket 1200 60 55 0.68 600D Ripstop 600 50 + 5 reinforcement 45 + 5 reinforcement 0.60 1200D Ripstop 1200 60 + 6 reinforcements 55 + 6 reinforcements 0.75
TF aggregates denier and thread density; a higher TF indicates a tighter, more abrasion‐resistant weave. 1200D Plain at 0.72 exhibits +20% TF over *600D Basket’*s 0.58.
2. Abrasion Resistance Correlation with TF
- Weave & Abrasion Data:
Fabric & Weave | Denier | TF | Martindale (cycles) | % Improvement vs. 600D Basket |
---|---|---|---|---|
600D Basket | 600 | 0.58 | 15,000 | — |
600D Plain | 600 | 0.65 | 17,000 | +13% |
600D Ripstop | 600 | 0.60 | 17,500 | +16.7% |
1200D Plain | 1200 | 0.72 | 22,000 | +46.7% |
1200D Basket | 1200 | 0.68 | 19,000 | +26.7% |
1200D Ripstop | 1200 | 0.75 | 24,000 | +60% |
Analysis:
- 600D Ripstop improves abrasion by embedding reinforcement yarns, increasing cycle life from 15,000 to 17,500 (≈+17%).
- 1200D Plain nearly triples abrasion life relative to 600D Basket (22,000 vs. 15,000).
- 1200D Ripstop (even higher TF) yields 24,000 cycles, marking a 60% improvement over 600D Basket.
3. Tensile & Tear vs. TF (Interplay of Denier & Density)
- Data Table:
Fabric & Weave | Denier | TF | Tensile (N/5 cm) | Tear (N) | Observations |
---|---|---|---|---|---|
600D Basket | 600 | 0.58 | 450–500 | 30–35 | Baseline for everyday casual usage |
600D Plain | 600 | 0.65 | 480–520 | 32–36 | Slight uplift due to denser construction |
600D Ripstop | 600 | 0.60 | 490–530 | 33–37 | Reinforcement filaments prevent propagation of tears |
1200D Plain | 1200 | 0.72 | 800–900 | 55–65 | Significant jump; optimal for heavy loads |
1200D Basket | 1200 | 0.68 | 750–820 | 50–58 | Slightly lower than plain but still impressive |
1200D Ripstop | 1200 | 0.75 | 850–950 | 60–75 | Best tear resistance and tensile |
Interpretation:
- 600D variants gain modest tensile and tear improvements with plain vs. basket weaves.
- Ripstop weaves add reinforcement grid, increasing tensile by ~5% and tear by ~5–10%.
- 1200D Plain more than doubles the tensile strength of 600D Basket, illustrating how denier, combined with higher TF, multiplies performance.
- 1200D Ripstop pushes performance to extreme levels (85–95 N/5 cm tensile, 60–75 N tear), but with weight penalties.
4. Permeability & Breathability vs. TF
- Air Permeability (cfm) & WVT:
Fabric & Weave | Denier | TF | Air Permeability (cfm) | WVT (g/m²/24h) |
---|---|---|---|---|
600D Basket | 600 | 0.58 | 420 | 2,500 |
600D Plain | 600 | 0.65 | 400 | 2,300 |
600D Ripstop | 600 | 0.60 | 410 | 2,400 |
1200D Plain | 1200 | 0.72 | 350 | 2,100 |
1200D Basket | 1200 | 0.68 | 370 | 2,200 |
1200D Ripstop | 1200 | 0.75 | 340 | 2,000 |
Analysis:
- 600D basket weaves lead in breathability (420 cfm) due to more open structure.
- 1200D plain weaves drop to 350 cfm, a 17% loss in airflow; still acceptable for most pack linings.
- Ripstop construction marginally reduces airflow relative to plain at same TF due to reinforcement wefts/ends.
Real‐world Impact:
- Higher airflow helps reduce interior moisture buildup (e.g., sweaty backs), so a 600D main body may feel more comfortable against lining. However, most backpacks include mesh or ventilation channels, compensating for fabric breath loss.
5. Wear & Tear Zones: Localized Durability
Use Case | Recommended Fabric & Weave | Justification |
---|---|---|
Bag Bottom & Corners | 1200D Ripstop Plain | Highest abrasion & tear resistance in high‐impact zones |
Front Panel / Pockets | 600D Plain or Ripstop | Balanced weight; moderate exposure to abrasion |
Straps & Handles | 1200D Nylon Ripstop | Maximum tensile & flex fatigue resistance |
Interior Liner | 200D Polyester Ripstop | Lightweight; moisture management |
Mapping Durability Zones:
Many brands now adopt a “zone reinforcement” approach:
- Bottom Panel: 1200D to withstand dragging.
- Front Flap / Pockets: 600D suffices for lighter wear, saving weight.
- Shoulder Straps & Grab Handles: 1200D nylon for repeated flex.
- Sides / Lower Sides: 1200D for lateral pulls.
Zone‐mapping allows brands to optimize cost‐performance—investing in 1200D where needed and conserving weight with 600D elsewhere.
6. Sunlight & Environmental Aging: Weave Density Effects
UV Penetration vs. TF:
- Tighter weaves (TF ≥ 0.70) block 20–25% more UV radiation than open weaves (TF ≤ 0.60).
- Over 1,000 hours of accelerated UV, 1200D retains 85–90% tensile vs. 600D retaining 80%.
Metric | 600D TF 0.58 | 600D TF 0.65 | 1200D TF 0.72 | 1200D TF 0.75 |
---|---|---|---|---|
UV Tensile Retention (%) | 80 | 82 | 88 | 90 |
UV Color Fade (ΔE) | 4.0 | 3.5 | 2.5 | 2.2 |
Moisture & Mildew Exposure:
- Denser weaves remain drier on the surface; 600D basket sheds moisture slower than 600D plain, increasing mildew risk in high humidity.
- 1200D plain repels water and dries faster, reducing microbiological growth.
7. Manufacturing Complexity & Quality Control
Aspect | 600D Weave (TF ~0.58–0.65) | 1200D Weave (TF ~0.68–0.75) | Production Implication |
---|---|---|---|
Loom Tension Required | Moderate (20–22 kN) | High (25–28 kN) | Slower machine speed for 1200D; increased energy |
Weaving Speed (m/min) | 70–80 | 40–50 | 1200D looms operate ~40% slower |
Defect Rate (% rolls) | 0.5–1.0 | 1.5–2.0 | Higher denier/TF increases chances of broken yarns |
Batch Consistency (tolerance) | ±5% | ±3–4% | Tighter controls needed for 1200D yards |
1200D production demands tighter loom controls and slower speeds, raising COGS by 20–30% relative to 600D. Yet for brands requiring top durability, the performance ROI often outweighs the cost penalty.
8. Synthesizing Denier & Density Effects
Overall Durability Hierarchy (Abrasion, Tensile, Tear):
- 1200D Ripstop Plain (TF 0.75)
- 1200D Plain (TF 0.72)
- 1200D Basket (TF 0.68)
- 600D Ripstop Plain (TF 0.60)
- 600D Plain (TF 0.65)
- 600D Basket (TF 0.58)
Weight vs. Durability Trade‐Off:
Fabric & Weave | Total GSM (PU Coated) | Abrasion (Martindale) | Tensile (N/5 cm) | Tear (N) |
---|---|---|---|---|
1200D Ripstop Plain | 420 gsm | 24,000 | 850–950 | 60–75 |
1200D Plain | 400 gsm | 22,000 | 800–900 | 55–65 |
1200D Basket | 380 gsm | 19,000 | 750–820 | 50–58 |
600D Ripstop Plain | 260 gsm | 17,500 | 490–530 | 33–37 |
600D Plain | 250 gsm | 17,000 | 480–520 | 32–36 |
600D Basket | 230 gsm | 15,000 | 450–500 | 30–35 |
The climb from 600D Basket (230 gsm) to 1200D Ripstop Plain (420 gsm) doubles nearly every durability metric but also nearly doubles weight. Brands must map these trade‐offs against end-user needs, pricing, and design ethos.
Do manufacturing costs and production considerations vary when using 600D versus 1200D Oxford?
Yes. 1200D Oxford fabrics require higher‐grade yarns, tighter weave settings, and slower loom speeds—leading to 20–30% higher COGS compared to 600D. Specifically, 1200D uses double the denier yarn weight (≈$2.40–$3.00/kg vs. $1.20–$1.50/kg), demands loom tension of 25–28 kN (versus 20–22 kN), and weaves at 40–50 m/min (compared to 70–80 m/min for 600D). This results in higher defect rates (~1.5–2% vs. 0.5–1% for 600D), increased energy consumption (≈10–15% more), and longer finishing times—thus a typical $4.00–$4.50/m² 600D Oxford jumps to $6.50–$7.50/m² for 1200D.
1. Raw Material Costs & Yarn Sourcing
Yarn Denier & Cost per Kilogram:
Denier | Fiber Type | Cost (USD/kg) |
---|---|---|
600D PET | Polyester | $1.20–$1.50 |
1200D PET | Polyester | $2.40–$3.00 |
600D Nylon | Nylon 6 or 6.6 | $1.80–$2.00 |
1200D Nylon | Nylon 6 or 6.6 | $3.60–$4.20 |
Spinning & Twisting:
- 1200D yarns require specialized spinning frames with higher‐tension rollers and twist settings. The added twist (20–25 TPI) for 1200D increases production time by 10–15% relative to 600D’s 18–22 TPI.
- Waste Rates: 1200D blending yields 5–7% waste due to break‐off during twisting; 600D waste remains at 3–4%.
2. Weaving Efficiency & Loom Setup
- Required Tension & Speed: Fabric Loom Tension (kN) Weaving Speed (m/min) Expected Defect Rate (%) 600D PET 20–22 70–80 0.5–1.0 1200D PET 25–28 40–50 1.5–2.0 600D Nylon 18–20 60–70 0.8–1.2 1200D Nylon 23–25 35–45 2.0–2.5
Interpretation:
- Weaving 1200D polyester at 45 m/min vs. 600D at 75 m/min represents a 40% slower throughput.
- Higher tension reduces fabric slippage but increases yarn break risk, contributing to a 1.5–2× defect rate relative to 600D.
3. Dyeing, Coating & Finishing
Dye Uptake & Uniformity:
- 1200D yarns need longer dye soaks and higher liquor ratio (~1:10 vs. 1:8 for 600D) to ensure consistent depth of shade.
- Energy Usage: Dye cycle time for 1200D is ~60 min, while 600D is 45 min, driving 15–20% higher utility costs for 1200D.
- Coating Application: | Step | 600D Oxford (PU) | 1200D Oxford (PU) | |————————|——————–|——————–| | Coating Viscosity | 600–650 cP | 650–700 cP | | Line Speed | 4–5 m/min | 3–4 m/min | | Drying Temperature | 120–130 °C | 130–140 °C | | Coating Weight (gsm) | +50–60 | +60–70 |
Explanation:
- 1200D’s higher denier demands slightly more viscous PU to fill interstices—requiring slower pass speeds (3.5 m/min vs. 4.5 m/min), thus lengthening curing oven dwell times by 10–15%.
- Energy Consumption: Additional 5–7% gas or electricity for elevated dryer temperatures.
4. Quality Control & Inspection
- Roll Inspection Tolerance: Fabric Acceptable Tensile Variation (%) Tear Variation (%) Visual Defect Limit (pcs/roll) 600D PET ±5 ±5 ≤ 5 1200D PET ±3–4 ±3–4 ≤ 8 600D Nylon ±4–5 ±4–5 ≤ 6 1200D Nylon ±3 ±3 ≤ 10
Notes:
- 1200D demands stricter variation tolerances because minor discrepancies amplify under high stress.
- Visual Defects: Knots or slubs in 1200D are more noticeable; mills often perform two-pass inspections for 1200D vs. single pass for 600D.
5. Conversion Labor & Overhead
- Cutting & Sewing: Operation 600D Fabric 1200D Fabric Labor Impact Cutting (electric knife) Easy to cut (<2 mm) Denser (>2.5 mm) 20–25% slower cutting time Sewing (industrial machines) Standard needles (#18-20) Heavier needles (#20-22); requires thicker thread 15–20% slower, more frequent needle changes Seam Inspection 3–5 min/pc 4–6 min/pc Additional time for close QC
- Implication: Bag assembly with 1200D requires thicker, stronger threads (e.g., 210D/3 nylon thread) and more robust needles; sewing speed drops from 500 SPM (stitches per minute) to 380–420 SPM, increasing labor hours by ~15%.
6. Waste & Yield Considerations
- Fabric Utilization: Cut Pattern 600D Yield (%) 1200D Yield (%) Reason Rectangular Panels 92–94 90–92 Bulkier fabric harder to nest efficiently Complex Curves 89–91 86–88 Stiffer 1200D resists tight curves
- Yield Difference: 1200D’s lower yield (~2–3% less) leads to higher material waste, which at $6.50/m² vs. $4.25/m² for 600D amplifies cost variance.
7. Energy Consumption & Environmental Factors
- Electricity & Gas Usage (per 100 m²): Process 600D Consumption 1200D Consumption % Increase (1200D vs. 600D) Weaving (kWh) 1,500 1,650 +10% Dyeing (kWh + Gas) 800 920 +15% Coating (kWh + Gas) 700 770 +10% Total 3,000 3,340 +11.3%
- Water Usage (per 100 m²): Process 600D Usage (L) 1200D Usage (L) % Increase Dyeing 20,000 24,000 +20% Finishing 5,000 6,000 +20% Total 25,000 30,000 +20%
- Sustainability Note: While 1200D imposes higher resource usage, its longer lifespan (3–4 years vs. 1.5–2 years for 600D) may offset environmental footprint per use when amortized over product life.
8. COGS Summary & Pricing Impact
- Fabric Pricing: Specification 600D PET + PU 1200D PET + PU 600D Nylon + PU 1200D Nylon + PU Raw Fabric Cost (USD/m²) $4.00–$4.50 $6.50–$7.50 $5.00–$5.50 $8.00–$8.50 Processing & Dyeing (% of Fabric Cost) 25–30% 30–35% 25–30% 30–35% Coating & Finishing (USD/m²) $1.20–$1.50 $1.50–$2.00 $1.40–$1.80 $2.00–$2.50 Logistics & QC (% of total) 10–12% 12–15% 10–12% 12–15% Total COGS (USD/m²) $6.00–$6.75 $8.70–$10.00 $7.00–$7.80 $10.50–$11.80
- Unit Bag Impact (20 L bag, 2.0 m² material): Specification COGS for Material & Processing (USD) Margin Impact (Retail Price) 600D PET + PU $12.00–$13.50 Retail ~$70 (Margin ~$25) 1200D PET + PU $17.40–$20.00 Retail ~$110 (Margin ~$40) 600D Nylon + PU $14.00–$15.60 Retail ~$80 (Margin ~$30) 1200D Nylon + PU $21.00–$23.60 Retail ~$140 (Margin ~$50)
Transitioning a product line from 600D to 1200D increases direct material & processing costs by 45–60%, pushing retail pricing correspondingly higher. However, brands can justify the premium through improved durability, warranty reductions, and enhanced user perception.
How should brands choose between 600D and 1200D Oxford materials based on end-use requirements?
Quick Answer (for Google’s Featured Snippet) Brands should match 600D Oxford to applications prioritizing lightweight portability, cost‐efficiency, and a moderate durability threshold, such as daypacks, urban commuter bags, and fashion lines. In contrast, 1200D Oxford suits heavy-duty, high‐abuse scenarios—backpacking, tactical gear, courier services—where maximum abrasion, tensile, and tear strength are vital. Hybrid constructions (e.g., 600D main body with 1200D reinforcement panels) can balance weight, cost, and durability when multiple use cases apply.
1. Urban & Fashion Applications (600D Favored)
Weight & Aesthetics:
- 600D produces bags around 900–950 g for 20 L, enabling sleek silhouettes for daily commuters, cyclists, or students who prioritize minimal bulk.
- Offers vibrant dye uptake and good drape, appealing to fashion brands focusing on color ranges and print patterns.
Cost Sensitivity & Volume Production:
- At $4.00–$4.50/m², 600D allows brands to maintain retail price points of $50–$80 for mid‐tier markets.
- Lower yardage cost and higher weaving speed provide better margins or price competitiveness in budget or mass‐market segments.
Use Cases & Durability Threshold:
- Acceptable abrasion life of 15,000–17,000 cycles covers 1–2 years of daily urban wear.
- Daypacks (10–20 L): Contents are typically laptops, notebooks; minimal jagged items—600D withstands this use.
- Tote Bags & Fashion Backpacks: Light use, aesthetic priority; 600D’s softer hand wins.
2. Outdoor, Tactical & Heavy‐Duty (1200D Preferred)
Durability & Lifespan:
- Endures 20,000–24,000 Martindale cycles, resisting rock scrapes, abrasion against tree branches, and repeated drag.
- High tensile (800–900 N/5 cm) ensures heavy loads (30–50 kg) do not strain fabric or seams.
Use Cases & Performance Needs:
- Backpacking (30–50 L): Heavier gear, necessity for water resistance, and resistance to rough terrains.
- Tactical & Law Enforcement Packs: Gear includes metal hardware, tools—1200D resists cuts and abrasion.
- Courier & Delivery Bags: Repeated drop-offs, contact with rough surfaces; 1200D’s longer life reduces warranty & replacement costs.
Brand Positioning & Pricing Strategy:
- With COGS ~$8.70–$10.00/m², 1200D packs retail at $110+, aligning with premium or specialized outdoor brands.
- Marketing emphasis on “guaranteed ruggedness,” “lifetime warranty,” or “mil‐spec standards” justifies higher price.
3. Hybrid & Zone Reinforcement Strategies
Hybrid Design Philosophy:
- Combining 600D main panels (for reduced weight & cost) with 1200D base and corners (for abrasion resistance) targets customers seeking a balance.
- Example: A 20 L commuter pack with 600D sides and 1200D bottom weighs ~1,000–1,050 g, achieving 85% of 1200D durability at ~70% of 1200D cost.
- Cost Breakdown (Hybrid 20 L Example): Component Fabric Type Area (m²) Cost (USD/m²) Subtotal (USD) Main Body (Sides) 600D PET + PU 1.2 $4.25 $5.10 Bottom / Corners 1200D PET + PU 0.5 $7.00 $3.50 Panels (Pockets) 600D Ripstop + PU 0.3 $4.50 $1.35 Total Fabric Cost — 2.0 — $9.95 Processing (25–30%) — — — $2.99 Coating & Finishing — — — $1.50 Total Hybrid Fabric COGS — — — $14.44
Comparison:
- Pure 600D: $12.00–$13.50.
- Pure 1200D: $17.40–$20.00.
- Hybrid: $14.44—17% less than 1200D, 10–15% more than 600D, offering 80–90% of 1200D performance.
4. Environmental & Sustainability Considerations
Life Cycle Assessment (LCA):
- 600D PET: Lower energy & water usage upfront but shorter lifespan (~2 years) means quicker disposal or recycling cycles.
- 1200D PET: Higher manufacturing footprint (+10–20% energy & water) but extended useful life (~3–4 years) lowers CO₂e per use significantly.
Metric | 100 Units 600D (2-year life) | 100 Units 1200D (4-year life) | Per-Use Impact (600D vs 1200D) |
---|---|---|---|
Total Fabric CO₂e (kg CO₂e) | 100 units × (2.5 kg/m² × 2 m²) × 3.5 = 1,750 | 100 units × (4.0 kg/m² × 2 m²) × 3.0 = 2,400 | 600D: 1,750/2 years = 875/year<br>1200D: 2,400/4 years = 600/year |
- Implication: Even though 1200D production generates more CO₂e per unit, its per‐year impact is ~30% lower than 600D—making it greener if bags see heavy, multi‐year use.
5. Supply Chain Resilience & MOQ Requirements
- MOQ (Meters): Fabric Type Typical Mill MOQ (roll length) MOQ in Meters (min.) 600D PET 1 Roll (~50–60 m) 50 m 1200D PET 1 Roll (~40–50 m) 40 m 600D Nylon 1 Roll (~45 m) 45 m 1200D Nylon 1 Roll (~30 m) 30 m
Lead Times:
- 600D PET: 20–25 days from order; widely available from multiple mills.
- 1200D PET: 30–35 days; fewer suppliers, higher demand in outdoor sector.
- Logistics: 1200D’s heavier rolls (≈20 kg per roll vs. 12 kg for 600D) increase shipping costs—$0.10–$0.15/kg more.
Risk of Stockouts:
- 600D is more commoditized; spot buys possible.
- 1200D availability can fluctuate with outdoor gear seasonality; brands should lock in contracts 3–6 months in advance.
6. Quality Assurance & Testing Protocols
Incoming Inspection:
- 600D Rolls: Random sampling—test tensile and tear on 3 specimens per roll.
- 1200D Rolls: Require 5 specimens per roll for tensile, tear, and Martindale due to higher end-use criticality.
Batch Traceability:
- 1200D often tagged with batch codes and Oeko-Tex or bluesign® certifications, especially for premium gear; implies higher audit and compliance costs.
7. Packaging & Freight Considerations
Roll Dimensions & Weight:
Fabric Type | Roll Length (m) | Roll Diameter (cm) | Roll Weight (kg) |
---|---|---|---|
600D PET | 50 | 30 | 12 |
1200D PET | 40 | 35 | 20 |
600D Nylon | 45 | 32 | 15 |
1200D Nylon | 30 | 36 | 22 |
Carton & Palletization:
- 1200D’s heavier rolls reduce carton count per pallet (e.g., 20 rolls of 1200D vs. 35 rolls of 600D on a 1.2 m × 1.2 m pallet), affecting shipping rates and local storage optimization.
8. Summary of Production Cost Variance
Cost Component | 600D PET + PU | 1200D PET + PU | % Increase (1200D vs 600D) |
---|---|---|---|
Raw Yarn Cost | $1.20–$1.50/kg | $2.40–$3.00/kg | +100% |
Weaving Cost (USD/m²) | $1.00–$1.20 | $1.50–$1.80 | +50–60% |
Dyeing & Finishing | $1.00–$1.30 | $1.20–$1.50 | +15–20% |
Coating Application | $1.20–$1.50 | $1.50–$2.00 | +20–33% |
QC & Inspection | $0.30–$0.40 | $0.40–$0.60 | +25–50% |
Logistics & Overhead | $0.50–$0.60 | $0.60–$0.80 | +20–33% |
Total COGS (USD/m²) | $6.00–$6.75 | $8.70–$10.00 | +45–60% |
When evaluating a cost‐benefit model, 1200D’s superior durability must offset the ~50% spike in COGS. In many B2B uniform or outdoor contexts, reduced warranty claims and brand value can justify the premium. Conversely, mass‐market or fashion brands may find 600D more aligned with their price and weight objectives.
How should brands choose between 600D and 1200D Oxford materials based on end-use requirements?
Brands should match 600D Oxford to applications where lightweight construction, cost efficiency, and moderate durability (15,000–17,000 Martindale cycles) suffice—such as urban commuter bags, casual daypacks, and light-duty fashion backpacks. Alternatively, opt for 1200D Oxford when maximum durability (20,000–24,000 cycles), high tensile (800–900 N/5 cm), and superior tear (~60 N) resistance are critical—typical for backpacking, tactical gear, courier/back delivery, and industrial tool bags. Hybrid designs (e.g., 600D body + 1200D base/corners) allow nuanced balance for mixed-use products.
1. Consumer Use‐Case Mapping
Use-Case Category | Primary Requirements | Recommended Material | Rationale |
---|---|---|---|
Urban Commuter / Cyclist | Lightweight, water-resistant, stylish | 600D Polyester + PU (Plain) | Under 1,000 g weight, versatile appearance, sufficient durability |
Travel Daypack | Moderate durability, packability, quick-dry | 600D Polyester Ripstop + DWR/PU | Slightly higher abrasion life (17,500 cycles), lightweight compressibility |
School / Casual Backpack | Cost-sensitive, moderate use, color variety | 600D Polyester + DWR (basket weave) | Low COGS, bright colors, aesthetic flexibility, acceptable lifespan (~2 years) |
Photography / Tech Gear Bag | Padding integration, moderate abrasion | 600D Polyester + PU with TPU-laminated base | Reflects gear inside, weight manageable, bottom panel TPU for spill protection |
Courier / Delivery Backpack | High abrasion, spills, load-bearing | 1200D Polyester + PU (plain weave) | High abrasion (22,000 cycles), strong water barrier (≥10,000 mm), robust seams |
Backpacking / Hiking Pack | Extreme abrasion, heavy loads, weather-proof | 1200D Nylon + TPU Lamination (plain weave) | Ultimate abrasion & tear, high hydrostatic head (≥17,000 mm), extended lifespan |
Tactical / Law Enforcement Gear | Cut resistance, high-load straps, covert use | 1200D Nylon Ripstop + TPU/PVC | Best tear (65–75 N), tensile (900–1,000 N/5 cm), ability to endure rough ops |
Industrial Tool / Utility Bag | Resistant to oils, solvents, sharp edges | 1200D Polyester or Nylon + PVC (plain) | Chemical resistance, easy clean, superior barrier (≥15,000 mm), durable |
Matching material choice to the highest critical requirement in a use case ensures product longevity, brand reputation, and customer satisfaction—while avoiding over‐engineering (and overspending) on unneeded performance.
2. Feature Prioritization Matrix
Feature | 600D Oxford | 1200D Oxford | Importance Scale (1–5) | Recommendations Based on Priority |
---|---|---|---|---|
Weight | 230–260 gsm | 380–420 gsm | 5 (Urban/Travel) | 600D |
Abrasion Resistance | 15,000–17,000 cyles | 20,000–22,000 cycles | 5 (Outdoor/Tactical) | 1200D |
Tensile Strength | 450–500 N/5 cm | 800–900 N/5 cm | 5 (Heavy Load) | 1200D |
Tear Strength | 30–35 N | 55–65 N | 5 (Rough Use) | 1200D |
Cost Efficiency | $4.00–$4.50/m² | $6.50–$7.50/m² | 4 (Budget/Entry) | 600D |
Packability / Flex | High | Moderate | 4 (Travel/Fashion) | 600D |
Water Barrier (PU) | 8,000–10,000 mm | 10,000–12,000 mm | 4 (Rain Gear) | 1200D (or 600D with PVC/TPU) |
Breathability (WVT) | 1,200 g/24h/m² | 1,000 g/24h/m² | 3 (Clothing Bags) | 600D |
Brand Perception | Affordable/Trendy | Premium/Rugged | 5 (High-End/Outdoor) | Align with target segment |
Sustainability (Per Use) | 875 kg CO₂e/year | 600 kg CO₂e/year | 3 (Eco-Conscious) | 1200D (for heavy-use) |
- Interpretation: Use this matrix to weight features by brand priorities. For a commuter brand (weight, cost, packability rank high), 600D is optimal. For an expedition brand (abrasion, tensile, tear rank high), 1200D is non-negotiable.
3. Lifecycle Cost & Value Proposition
- Lifecycle Cost Comparison (Per 100 Bags Over 4 Years):
Metric | 600D Polyester (2-year life) | 1200D Polyester (4-year life) |
---|---|---|
Initial COGS (per 20L bag) | $12.00–$13.50 | $17.40–$20.00 |
Replacement Frequency | Every 2 years (2 cycles) | Every 4 years (1 cycle) |
Replacement Cost Total | 100 × 2 × $12.75 = $2,550 | 100 × 1 × $18.70 = $1,870 |
Warranty Claim Rate | 10% (10 bags × $10) = $100 | 3% (3 bags × $10) = $30 |
Total 4-yr Cost | $2,550 + $100 = $2,650 | $1,870 + $30 = $1,900 |
Cost per Bag Over 4 yrs | $26.50 | $19.00 |
- Over a 4‐year horizon, 1200D is $7.50 cheaper per bag when accounting for replacements and warranty—making it a smarter investment for heavy‐use environments.
4. Environmental Footprint per Use
- CO₂e Emissions & Water Usage (Amortized Over Lifespan):
Fabric Specification | CO₂e (kg per bag) | Water (L per bag) | Lifespan (yrs) | Annual CO₂e (kg/year) | Annual Water (L/year) |
---|---|---|---|---|---|
600D Polyester | 17.5 | 250 | 2 | 8.75 | 125 |
1200D Polyester | 24.0 | 300 | 4 | 6.00 | 75 |
600D Nylon | 20.0 | 280 | 2 | 10.0 | 140 |
1200D Nylon | 28.0 | 320 | 4 | 7.0 | 80 |
- Although 1200D has higher production footprints per unit, its extended lifespan results in 30–35% lower annual environmental impact—an important selling point for sustainability‐oriented brands.
5. User Comfort & Market Positioning
Weight Sensitivity:
- If a brand’s target demographic (e.g., urban professionals, college students) values lightweight convenience (walking/cycling commutes), a 50–60% weight penalty of 1200D (e.g., 1,150 g vs. 950 g for 20 L) could become a deterrent.
- Conversely, for mountain-guiding services, every extra 100 g is acceptable in exchange for supreme abrasion resistance; marketing can highlight “built tough for extremes.”
Price vs. Perceived Value:
- 600D frequently aligns with mid‐tier price points ($50–$70)—conducive for fashion collaborations or entry‐level outdoor lines.
- 1200D matches $120–$150 retail segments, where customers expect “bombproof” gear and are willing to invest in long‐term utility.
6. Brand Case Studies & Lessons Learned
Lifestyle Brand X (Urban Focus):
- Switched from 1000D to 600D to cater to fashion sneakers culture, reducing pack weight from 1.2 kg to 0.9 kg. Sales increased by 35%, driven by “light as a feather” marketing.
- After six months, 10% of users reported minor scuffing; brand introduced 1200D reinforcement patches on high-wear zones, preserving 600D’s weight profile while extending durability.
Outdoor Expedition Brand Y:
- Initially launched all packs in 600D, but encountered 15% return rate for tears after single-season Himalayan treks.
- Re‐engineered to 1200D with 100 cm⁴/cm³ foam-backed panels; returns dropped to <2%, and average pack life extended to 3+ years.
- Premium pricing (from $90 to $130) decreased sales volume by 20%, but total revenue remained flat, with higher margins and lower post-sale service costs.
- Courier Service Z (B2B Uniform Bags):
- Required durable mail bags that could endure frequent drop-offs and pothole-jolted bike rides. Selected 1200D polyester + PVC.
- Over 12 months, their replacement cost dropped by 48%, and rider satisfaction scores climbed by 18% due to fewer malfunctions mid-route.
7. Niche Innovations & Future Trends
Low‐Denier (300D) Laminated Microfibers:
- Some brands experiment with 300D micro‐ripstop laminated with 150 µm TPU to approach 15,000 cycles abrasion at 180–200 gsm—targeting ultra-light niche markets.
- Not a direct 600D/1200D replacement but signal of market interest in “performance weight” trade-offs.
Bi‐Component Yarn & Laser‐Cut Holes:
- Cutting microscopic “drainage holes” in 1200D via laser to maintain water barrier but reduce weight and improve packability.
- Early trials show 10% weight reduction without sacrificing significant strength but add $1–$2/m² in processing.
8. Decision Framework for Brands
Step | Questions to Ask | 600D Path Indicator | 1200D Path Indicator |
---|---|---|---|
1. End-Use Profile | Is lightweight/affordability more critical than extreme durability? | Yes → proceed with 600D | No → consider 1200D |
2. Target Price Point | Will customers pay a 40–60% premium for enhanced durability? | No → 600D | Yes → 1200D |
3. Longevity & Warranty | Are extended warranties or low replacement costs a priority? | 600D warranty set at 1 year | 1200D warranty set at 3–4 years |
4. Supply Chain & MOQ | Do I have flexibility for higher MOQ and longer lead times? | Need rapid turn/low MOQ → 600D | Can plan 3–6 months ahead → 1200D |
5. Environmental Goals | Does a lower per‐use carbon footprint impact brand positioning? | Acceptable → 600D | Prefer green metrics → 1200D |
6. Hybrid Viability | Would a hybrid approach (weighted panels) optimize performance? | Yes → combine both (e.g., 600D/1200D) | No → pick one denier |
7. Aesthetic & Flexibility | Is fabric drape and packability a brand differentiator? | High priority → 600D | Less critical → 1200D |
Run a small batch pilot—produce 50–100 units in both 600D and 1200D for wear tests, customer focus groups, and logistics trials to validate assumptions before large‐scale commit.
Ready to prototype or scale your next bag collection?
Ultimately, the choice between 600D and 1200D Oxford for bag manufacturing is a careful balance of weight, cost, durability, and brand positioning. If your end users value lightweight comfort, fashion aesthetics, and lower price points, 600D Oxford delivers reliable performance with an 8–10 oz/yd² footprint. Conversely, for markets requiring extreme abrasion, high tensile strength, and extended service life—from backpacking to tactical—1200D Oxford commands a premium justifying its 12–13 oz/yd² heft.
At SzoneierFabrics, we offer:
- Custom 600D & 1200D Options (polyester or nylon)
- Wide Array of Weaves (basket, plain, ripstop)
- Coating & Lamination Expertise (PU, PVC, TPU, DWR, UV, anti‐mildew)
- Low MOQ Prototyping (≥ 25 meters) with free lab swatches in 7 days
- Rapid Turnaround (30–45 days for 600D; 45–60 days for 1200D)
- Comprehensive Testing Reports (tensile, tear, Martindale, hydrostatic, UV)
- Competitive Pricing (COGS from $4.00/m² to $10.00/m² depending on spec)
Contact our textile specialists today to discuss your precise denier, weave, and finish requirements—let us help you strike the perfect performance‐to‐cost balance,
Whether you need a light commuter pack in 600D, a rugged expedition bag in 1200D, or a hybrid solution blending both, SzoneierFabrics delivers the expertise, quality, and reliable lead times to bring your vision to life. Request a quote now and move closer to launching your next bestselling bag.