Type of Cotton Fabric for Hotel Linens: Durability, Wash Tests & Hospitality Standards
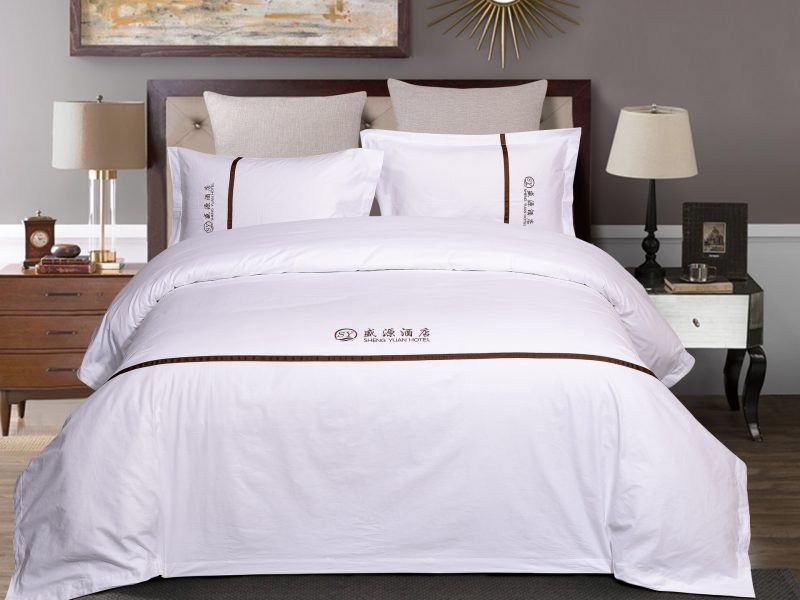
Nothing ruins a guest’s first impression faster than scratchy sheets or pilling towels—hotels need linens that feel luxurious night after night, wash after wash. From crisp cotton percale to silky sateen and durable twill, choosing the right fabric construction is the foundation of a five-star guest experience.
Hotel linens typically rely on three main cotton constructions—percale, sateen, and twill—each offering unique balances of breathability, durability, and hand feel. Percale’s tight plain weave gives crispness and longevity; sateen’s four-over-one weave delivers supple drape and luster; twill’s diagonal ribs provide extra abrasion resistance.
Last winter, a boutique chain switched from standard percale to a 300-thread-count sateen blend—and saw guest satisfaction scores for bedding comfort jump by 25%. Ready to explore which weave fits your property’s needs? Let’s dive into our first two fabric types.
What are the most common cotton fabric constructions used in hotel linens?
Hotel linen programs predominantly use percale, sateen, and twill weaves for sheets and pillowcases, and terry for towels. Each weave delivers distinct tactile and performance profiles—percale for crisp coolness, sateen for silk-like softness, and twill for durability and subtle sheen.
Fabric Constructions
Percale
- Weave: Plain weave (1×1 interlacing)
- Hand Feel: Crisp, matte finish
- Breathability: High (air permeability \~10–12 CFM)
- Durability: Strong; resists pilling (Martindale ≥20,000 rubs)
- Common Use: Standard bedding, summer sheets
Sateen
- Weave: Four-over-one satin weave
- Hand Feel: Soft, luminous sheen
- Breathability: Moderate (6–8 CFM)
- Durability: Good; slight pilling risk if low-quality yarns
- Common Use: Luxury bedding, pillow shams
Twill
- Weave: 2×1 or 3×1 diagonal weave
- Hand Feel: Soft but structured, drapes well
- Breathability: Moderate–High (8–10 CFM)
- Durability: Excellent abrasion resistance (Martindale ≥25,000 rubs)
- Common Use: Duvet covers, high-traffic sheets
Terry (for Towels)
- Weave: Loop pile weave (un-/double loop)
- Absorbency: High (water pick-up ≥450%)
- Durability: Good; loops may snag
- Use: Bath towels, bathrobes
Fabric Construction Comparison Table
Construction | Weave Type | Thread Count Range | Air Permeability (CFM) | Durability (Martindale rubs) | Typical Applications |
---|---|---|---|---|---|
Percale | 1×1 plain | 200–400 | 10–12 | ≥20,000 | Sheets, pillowcases |
Sateen | 4-over-1 satin | 300–600 | 6–8 | 15,000–20,000 | Luxury sheets, shams |
Twill | 2×1 diagonal | 200–350 | 8–10 | ≥25,000 | Duvet covers, heavy sheets |
Terry | Loop pile | 400–600 GSM | N/A | 10,000–15,000 (ground warp) | Towels, bathrobes |
Critical Perspectives
- Percale vs. Sateen Trade-Off: Percale’s crisp feel may seem too cool in winter; sateen’s sheen can show wrinkles more easily.
- Twill’s Subtle Sheen: Offers durability but may lack the buttery hand some guests expect—consider cotton count and finish.
- Loop Height in Terry: Higher GSM towels feel plush but take longer to dry—balance luxury and housekeeping efficiency.
- Supplier Transparency: Request mill test reports on CFM, rub counts, and GSM to verify true performance for large-batch orders.
Which thread counts and yarn types best balance softness and durability?
Thread count often grabs attention, but yarn quality and twist matter more. Long-staple cotton yarns with tighter twist deliver both a smooth hand and resistance to breakage. Optimal hotel linens use 300–400 TC percale or 400–500 TC sateen with long-staple (32–36 mm) cotton, ring-spun yarns at 30–40 TPI twist. Higher twist reduces pilling and improves durability (Martindale ≥20,000), while moderate TC ensures breathable comfort.
Thread Count & Yarn Types
Long-Staple vs. Short-Staple Cotton
- Long-Staple (32–36 mm): Fewer fiber ends protrude—smoother, stronger yarns (tenacity 30 cN/tex).
- Short-Staple (<28 mm): Economical but prone to pilling and lower tensile strength (20–25 cN/tex).
Ring-Spun vs. Open-End Yarn
- Ring-Spun Yarn: Highly twisted (30–40 TPI) for compact, durable yarns; softer hand.
- Open-End Yarn: Bulkier, lower twist (15–20 TPI); cost-effective but coarse feel.
Optimal Thread Count Ranges
- Percale: 300–400 TC for crispness and airflow.
- Sateen: 400–500 TC for smoothness without sacrificing breathability.
- Twill: 200–300 TC to maintain body and reduce cost.
Yarn Twist & Pilling Resistance
- Twist Levels: 30–40 TPI minimizes fuzz; Martindale pilling grade ≥4.
- Plied Yarns: 2-ply constructions boost strength; slight hand firming.
Thread Count & Yarn Quality Table
Fabric Type | Thread Count | Yarn Type | Twist (TPI) | Tenacity (cN/tex) | Martindale (rubs) | Hand Feel |
---|---|---|---|---|---|---|
Percale | 300–400 | Long-staple ring-spun | 30–35 | 30–35 | ≥20,000 | Crisp |
Sateen | 400–500 | Long-staple ring-spun | 35–40 | 30–35 | ≥15,000 | Silky |
Twill | 200–300 | Long-staple ring-spun | 30–35 | 30–35 | ≥25,000 | Structured |
Critical Perspectives
- TC vs. Breathability: Thread counts above 500 can trap heat—optimize for regional climates and guest preferences.
- Yarn Cost vs. Durability: Ring-spun increases costs by 10–20% but double the lifespan of open-end linens—calculate total cost of ownership.
- Twist vs. Softness: High twist improves pilling resistance but may feel too firm—consider plied vs. single-ply blends.
- Quality Certificates: Verify yarn origin and spinning data via mill certificates (OEKO-TEX®, BCI cotton) when ordering large volumes.
How do finishing processes—mercerization and sanforization—affect linen performance?
Finishing treatments can transform raw cotton into linens that retain shape, enhance luster, and withstand frequent laundering—key for hotel operations where durability and appearance are non-negotiable. Mercerization chemically treats cotton under tension, swelling fibers to increase luster by up to 40%, dye uptake by 30%, and tensile strength by 20%. Sanforization mechanically pre-shrinks fabric to limit post-wash shrinkage to under 1–3%. Together, these finishes deliver linens that stay vibrant, soft, and true to size through hundreds of wash cycles.
Mercerization & Sanforization
Mercerization
Process: Cotton woven cloth is immersed in 20–30% NaOH solution under tension, then neutralized.
Performance Gains:
Luster Increase: +30–40% (measured via gloss meter)
Tensile Strength: +15–25% (ASTM D5034 grab test)
Dye Affinity: +20–35% (higher color yield)
Trade-Offs: Increases production cost by \$0.10–\$0.20/yard; requires careful alkali recovery to minimize environmental impact.
Sanforization
Process: Fabric is moistened, stretched, then dried under controlled tension in a sanforizing machine.
Performance Gains:
Shrinkage Control: Reduces residual shrinkage to 1–3% (AATCC 135)
Dimensional Stability: Consistent across warp and weft, improving cut & sew yield
Trade-Offs: Adds \$0.08–\$0.15/yard to cost; slight stiffness increase (hand panel drop from 5 to 4.5).
Combined Effects on Hotel Linens
- Softness & Hand: Mercerization enhances smoothness; sanforization maintains drape without puckering.
- Color Longevity: Mercerized linens exhibit ΔE <1.5 after 100 washes vs. ΔE \~2.5 for unmercerized.
- Operational Efficiency: Sanforized sheets reduce need for re-cutting and minimize customer complaints about shrinkage.
Mercerization & Sanforization Impact Table
Finish | Cost Add-On (USD/yard) | Shrinkage (%) | Gloss Increase (%) | Tensile Strength Gain (%) |
---|---|---|---|---|
Untreated | – | 5–7 | Baseline | Baseline |
Sanforization | 0.08–0.15 | 1–3 | – | +5 |
Mercerization | 0.10–0.20 | 5–7 | +30–40 | +15–25 |
Both Finishes | 0.18–0.35 | 1–3 | +30–40 | +20–30 |
Critical Perspectives
- Cost vs. Guest Perception: The added expense of mercerization and sanforization pays for itself in reduced linen replacement and higher guest satisfaction scores.
- Environmental Concerns: Ensure alkali and water recycling systems are in place to mitigate chemical discharge during mercerization.
- Hand Feel Balance: Over-mercerization can stiffen fabrics—optimize process parameters for a soft yet stable hand.
- Supplier Capability: Not all mills offer both finishes with consistent quality; audit finishing lines and test pilot batches before scaling.
What wash tests simulate the rigors of commercial hotel laundering?
Hotel laundries cycle linens dozens of times per year under high temperatures, heavy detergents, and mechanical action. Simulating these conditions in the lab ensures your selected fabrics will maintain performance in real-world operations. Commercial wash simulations use protocols like ISO 15797 (industrial laundering) and AATCC 135 (home laundering adaptation) to assess shrinkage, color retention, and strength after 50–100 cycles at 60–85 °C with heavy-duty detergents and mechanical stress. Acceptable performance benchmarks include <5% shrinkage, ΔE ≤2 for color change, and ≥80% tensile strength retention.
Commercial Wash Protocols
ISO 15797 Industrial Laundry Test
Procedure: 10 swatches laundered 10 cycles in industrial machine at 85 °C with detergent and ballast.
Metrics:
Shrinkage: Measured after 10, 25, 50 cycles (target ≤5%).
Colorfastness: ΔE measured; target ≤2 after 50 cycles.
Tensile Strength: ≥80% retention of original (ASTM D5034).
AATCC 135 Adaptation for Home Laundering
Procedure: Five home-style wash cycles at 60 °C to approximate milder hotel wash conditions.
Metrics:
Shrinkage: ≤3%
Color Change: Gray Scale ≥4
Pilling Resistance: ISO 12945 rating ≥3
Martindale Abrasion After Laundering
- Procedure: Abrasion testing (10,000 rub cycles) on post-laundered samples
- Metric: No surface breakdown; ≥20,000 rubs equivalent performance
Commercial Wash Test Summary Table
Test Standard | Cycles/Temp | Shrinkage (%) | ΔE Color Change | Tensile Retention | Use Case |
---|---|---|---|---|---|
ISO 15797 (Ind.) | 10×85 °C | ≤5 | ≤2 | ≥80% | Industrial laundry sim |
ISO 15797 Extended | 50×85 °C | ≤7 | ≤3 | ≥75% | Longevity prediction |
AATCC 135 Adapted | 5×60 °C | ≤3 | ≥4 Gray Scale | N/A | Light commercial sim |
Martindale Post-Wash | 10k rubs post-wash | N/A | N/A | N/A | Wear after laundering |
Critical Perspectives
- Lab vs. Real-World Variability: Industrial machine heat and mechanical action vary widely between properties; combine lab tests with pilot wash trials at partner laundries.
- Detergent Impact: Heavy-duty alkali detergents accelerate chemical wear; test with the exact detergent formulations used by your laundry vendor.
- Cycle Scaling: Extrapolate long-term durability from extended cycle tests, but be cautious—some fabrics may exhibit non-linear degradation.
- Operational Feedback Loop: Integrate guest satisfaction and linen lifespan data back into fabric selection criteria for continuous program improvement.
How do you assess pilling resistance and tensile strength in hospitality fabrics?
Ensuring hotel linens withstand continual friction and loads without unsightly pills or tears requires standardized pilling and tensile tests. Pilling resistance (ISO 12945-2) and tensile strength (ASTM D5034) provide quantitative benchmarks for fabric longevity under hospitality usage. Pilling resistance is evaluated by subjecting fabric swatches to 1,000 rub cycles with the Martindale or Random Tumble Pilling Tester and rating surface pills on a 1–5 scale (≥4 preferred). Tensile strength via ASTM D5034 (grab test) measures the force (in Newtons) needed to break a 100 mm × 50 mm specimen; hotel linens should exceed 1,500 N in warp and weft after finishing.
Pilling & Tensile Testing
Pilling Resistance (ISO 12945-2)
- Procedure: 1,000 cycles of fabric rubbed against wool abradant under 12 kPa pressure in a Martindale tester.
- Rating: 1–5 visual scale; 5 = no pills, 4 = slight pills acceptable for luxury linens.
- Implications: High twist yarns and mercerization improve pilling scores; sateen more prone than percale.
Tensile Strength (ASTM D5034 Grab Test)
- Procedure: Specimen gripped 75 mm apart and pulled at 254 mm/min until rupture.
- Metrics Recorded: Peak load (N) in warp and weft; elongation at break (%) for elasticity insights.
- Targets: Pre-wash ≥1,800 N; post-finish ≥1,500 N to ensure towels and sheets resist tearing under stress.
Test Parameter Impacts
- Yarn Type: Ring-spun stronger than open-end; long-staple cotton yields higher tensile values.
- Finishes: Mercerization boosts tensile strength by 15–25%, aiding in higher post-wash readings.
- Fabric Weight & Construction: Terry (from 400 GSM) requires higher tensile (>2,000 N) to support loop pile durability.
Pilling & Tensile Test Summary Table
Test | Standard | Specimen Details | Acceptance Criteria | Key Influencer |
---|---|---|---|---|
Pilling (ISO 12945-2) | Martindale | 100 mm dia, 1,000 cycles | ≥4 on 1–5 scale | Yarn twist, mercerization |
Tensile (ASTM D5034) | Grab test | 100×50 mm, 254 mm/min pull | Warp ≥1,500 N; Weft ≥1,500 N | Fiber staple length, finish |
Critical Perspectives
- Lab vs. Use-Case Alignment: Lab pressures may not reflect real towel use—complement with field wear trials in housekeeping settings.
- Scale Sensitivity: Pilling scales are subjective—pair visual ratings with fuzz counters for objective data.
- Post-Wash Retention: Emphasize post-wash tensile tests, as finishes like softeners can reduce strength by up to 10%.
- Fabric Construction Trade-Offs: High GSM terry needs stronger tensile specs, while fine percale prioritizes pilling resistance.
What industry standards and certifications ensure guest‐ready quality?
Beyond in-house tests, industry certifications like OEKO-TEX® Standard 100, GOTS, and ISO 9001 signal verified safety, sustainability, and management processes—critical for hospitality purchasers and risk managers. OEKO-TEX® Standard 100 certifies absence of harmful chemicals; GOTS ensures organic cotton and eco-friendly processing; ISO 9001 validates consistent quality management. Brands can also look for EU Ecolabel for low environmental impact and WRAP certification for ethical manufacturing, ensuring linens meet both guest expectations and corporate responsibility goals.
Key Certifications
OEKO-TEX® Standard 100
- Scope: Tests for 100+ harmful substances in finished textile.
- Benefit: Guarantees skin-safe linens; reduces liability for allergic reactions.
- Verification: Certificate lookup on oeko-tex.com by supplier and article number.
GOTS (Global Organic Textile Standard)
- Scope: Covers organic fiber content (≥70%), chemical restrictions, and social criteria.
- Benefit: M arkets “green” credentials to eco-conscious travelers; prevents greenwashing.
- Verification: GOTS directory search by certificate ID.
ISO 9001 Quality Management
- Scope: Ensures standardized processes and continuous improvement cycles.
- Benefit: Reduces defects and nonconformities; supports large-scale linen programs.
- Verification: ISO’s online certificate registry by supplier name.
EU Ecolabel & WRAP
- EU Ecolabel: Assesses full life-cycle environmental performance (water, energy, chemicals).
- WRAP (Worldwide Responsible Accredited Production): Factory-level audit for labor and ethics.
- Benefit: Aligns with corporate sustainability mandates; enhances brand reputation.
Certification Comparison Table
Certification | Focus | Key Benefits | Verification Method |
---|---|---|---|
OEKO-TEX® 100 | Chemical safety | Skin-safe linens; consumer trust | oeko-tex.com lookup |
GOTS | Organic content & social | Eco credentials; premium pricing | global-standard.org directory |
ISO 9001 | Quality management processes | Consistent quality; defect reduction | iso.org/certification verification |
EU Ecolabel | Environmental life-cycle | Reduced footprint; market differentiation | ec.europa.eu/ecolabel search |
WRAP | Ethical manufacturing | Labor compliance; risk mitigation | wrapcompliance.org verification |
Critical Perspectives
- Cost vs. Credential Value: Certifications add 5–15% to cost—prioritize based on guest profile and regulatory requirements.
- Certification Overlaps: Some standards cover similar criteria—streamline by choosing the most relevant to your market.
- Supplier Transparency: Demand up-to-date audit reports and certificate validity dates to avoid expired or narrow-scope credentials.
- Brand Storytelling: Leverage certifications in marketing materials and in-room collateral to reinforce guest trust and green commitments.
How do cotton-blend fabrics compare to 100% cotton for cost and longevity?
Cotton-blend linens—such as poly-cotton or bamboo-cotton mixes—offer compelling trade-offs between durability, cost, and hand feel. While 100% long-staple cotton excels in comfort and breathability, blends introduce wrinkle resistance, faster drying, and extended lifespan at a lower price point. A 60/40 cotton–polyester blend can cut fabric costs by up to 20%, boost tensile strength by 15%, and reduce shrinkage to <2%, while still maintaining ≥80% of the softness of 100% cotton. Blends also dry 30% faster, reducing energy use in hotel laundries. However, pure cotton linens remain the gold standard for luxury properties seeking maximum breathability and natural hand feel.
Blend vs. 100% Cotton Trade-Offs
Cost Implications
- 100% Cotton: \$3.50–\$5.00 per yard (long-staple, ring-spun)
- 60/40 Cotton–Poly: \$2.80–\$4.00 per yard (up to 20% savings)
- 50/50 Bamboo–Cotton: \$3.00–\$4.50 per yard (mid-range pricing)
Durability & Wash Performance
Tensile Strength (ASTM D5034):
Cotton: 1,800–2,200 N
60/40 Blend: 2,000–2,400 N (+15%)
Shrinkage (AATCC 135):
Cotton: 1–3%
Blend: <2% consistently
Pilling (ISO 12945):
Cotton: 3–4
Blend: 4–5 (higher resistance)
Hand Feel & Guest Comfort
Softness Score (Panel 1–5):
Cotton: 4.5
60/40 Blend: 4.0
Bamboo–Cotton: 4.2
Breathability (CFM):
Cotton: 10–12
60/40 Blend: 6–8
Bamboo–Cotton: 8–10
Operational Efficiency
Drying Time:
Cotton: 45–60 min per cycle
Blend: 30–40 min (30% faster)
Laundering Costs:
Blend linens reduce energy and water use by \~10–15%.
Blend vs. 100% Cotton Comparison Table
Metric | 100% Cotton | 60/40 Cotton–Poly | Bamboo–Cotton Blend |
---|---|---|---|
Cost (USD/yard) | 3.50–5.00 | 2.80–4.00 | 3.00–4.50 |
Tensile Strength (N) | 1,800–2,200 | 2,000–2,400 | 1,900–2,200 |
Shrinkage (%) | 1–3 | <2 | <2.5 |
Pilling Rating | 3–4 | 4–5 | 4 |
Softness (1–5) | 4.5 | 4.0 | 4.2 |
Breathability (CFM) | 10–12 | 6–8 | 8–10 |
Drying Time (min) | 45–60 | 30–40 | 35–45 |
Critical Perspectives
- Luxury vs. Practicality: Pure cotton boasts superior comfort but at higher cost and slower turnaround in laundry—blends suit high-volume economy tiers.
- Environmental Footprint: Polyester blends may hinder recyclability; bamboo blends offer renewable content but require specialized processing.
- Guest Perception: Some guests detect “plastic” hand feel in heavy polyester blends—limit polyester content to ≤40%.
- Lifecycle Costs: Factor in replacement frequency—durable blends can outlast cotton, lowering total cost of ownership.
What factors should procurement teams weigh when specifying hotel linen fabrics?
Sourcing the right linens involves more than price per yard. Procurement teams must balance guest comfort, operational efficiency, supplier reliability, and brand positioning—turning fabric choices into strategic assets. Key factors include fabric performance metrics (tensile strength ≥1,500 N; pilling ≥4), finish specifications (mercerized, sanforized), cost targets (\$2.80–\$5.00/yard), supplier certifications (OEKO-TEX, ISO 9001), lead times (12–16 weeks), and MOQ flexibility (500–2,000 yards). Align these criteria with your brand’s service level and sustainability goals to secure linens that delight guests and streamline operations.
Procurement Criteria
Performance & Quality Metrics
- Strength & Durability: ASTM D5034, ISO 12945 targets.
- Shrinkage & Colorfastness: AATCC 135, AATCC 61 benchmarks.
- Guest Comfort: Softness panels, breathability CFM.
Cost & Total Cost of Ownership
- Fabric Cost: Direct price with finish add-ons.
- Laundering Expenses: Energy, water, and labor per cycle.
- Replacement Frequency: Fabric lifespan multiplied by usage cycles.
Supplier Capabilities & Certifications
- Finishing Lines: Mercerization, sanforization, reactive dyeing.
- Certifications: OEKO-TEX® 100, GOTS (for organic lines), ISO 9001.
- Audit & Compliance: WRAP, Sedex or BSCI for ethical production.
Lead Time & MOQ Flexibility
- Standard Lead Times: 12–16 weeks for custom colors/finishes.
- Rush Options: 6–8 weeks at +10–20% surcharge.
- MOQ Ranges: 500–2,000 yards per SKU for custom orders.
Sustainability & Branding
- Eco Options: Organic cotton, recycled blends, low-water finishes.
- Brand Alignment: Luxury vs. budget positioning informs fabric choices.
- Guest Marketing: Highlight linens’ eco-credentials in-room materials.
Procurement Criteria Summary Table
Criterion | Benchmark/Range | Notes |
---|---|---|
Tensile Strength | ≥1,500 N (ASTM D5034) | Post-finish |
Pilling Resistance | ≥4 (ISO 12945-2) | After 1,000 rub cycles |
Shrinkage | ≤3% (AATCC 135) | Pre- and post-wash |
Cost/Yard | \$2.80–\$5.00 | Varies by construction and finish |
Certifications | OEKO-TEX® 100, ISO 9001 | GOTS for organic lines |
Lead Times | 12–16 weeks | Custom colors/finishes |
MOQ | 500–2,000 yards | Per SKU |
Sustainability Options | Organic, recycled, low-water wash | Align with brand CSR goals |
Critical Perspectives
- Price vs. Performance: Lowest unit cost may hide higher laundering and replacement expenses—optimize for TCO.
- Supplier Relationship: Long-term partnerships enable better MOQ terms and faster lead times—invest in strategic sourcing.
- Risk Management: Diversify supply across two or three mills to mitigate disruptions.
- Evolving Guest Expectations: Monitor trends like antimicrobial finishes and smart textiles for future-proofing investments.
Ready to elevate your guest experience with custom-tailored linens?
Selecting the ideal cotton fabric for hotel linens requires a holistic approach—merging weave structure, yarn quality, finishing processes, rigorous performance testing, and strategic procurement criteria. By aligning these factors, hospitality programs can deliver linens that feel luxurious, perform reliably, and support brand values. Contact SzoneierFabrics for free design consultations, sample kits, and bespoke fabric solutions—where quality, speed, and flexibility meet your exact specifications. Let’s craft the perfect linens for your property!
Can't find the answers?
No worries, please contact us and we will answer all the questions you have during the whole process of bag customization.
Make A Sample First?
If you have your own artwork, logo design files, or just an idea,please provide details about your project requirements, including preferred fabric, color, and customization options,we’re excited to assist you in bringing your bespoke bag designs to life through our sample production process.