Polyester vs Polyamide Cost Analysis: Which Offers Better Value?
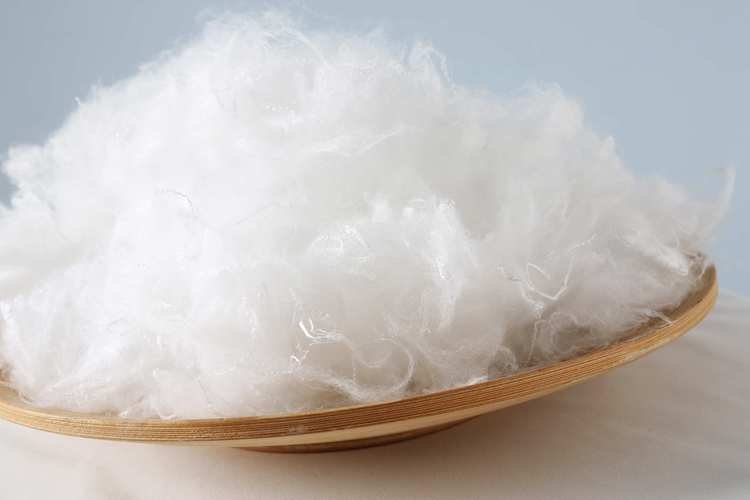
In a market where every penny counts and performance must meet price, choosing the right synthetic fabric—polyester or polyamide (nylon)—can have a profound impact on product margins, quality perception, and long-term brand performance. While both are petroleum-based fibers with broad applications across apparel, industrial textiles, bags, and upholstery, their cost-to-performance ratios vary dramatically depending on usage, finish, and supply chain access. Polyester generally offers lower raw material and production costs, while polyamide (nylon) delivers higher performance at a premium price. The better value depends on your product’s durability, end-use, and market positioning goals.
And here’s the catch: price alone rarely tells the whole story. A \$0.40/yard difference in fabric cost can make or break a project—unless you understand what you’re truly paying for. In this guide, we unpack every cost variable and value lever to help sourcing managers, fabric buyers, and brand owners make smarter decisions.
Let’s dive in with a side-by-side cost breakdown.
What Are the Fundamental Cost Drivers Behind Polyester and Polyamide Fabrics?
The primary cost differences between polyester and polyamide come from raw materials, production processes, energy consumption, and finishing treatments. Polyester is derived from ethylene glycol and dimethyl terephthalate, both more readily available and easier to process. Polyamide, on the other hand, requires more precise polymerization (often caprolactam-based), resulting in higher base costs. Polyester is cheaper to produce due to simpler raw materials and lower energy input, while polyamide’s higher strength and complex polymer structure raise manufacturing and processing costs.
Breakdown of Direct and Indirect Cost Variables
Cost Driver | Polyester | Polyamide (Nylon) |
---|---|---|
Raw Material Cost (per kg) | \$0.90–\$1.20 | \$1.80–\$2.50 |
Polymerization Complexity | Low | High |
Energy Required for Processing | Moderate | High |
Dyeability Efficiency | Excellent (disperse dyes) | Requires acid dyes (costlier) |
Finishing & Coating Compatibility | High (PU, PVC, DWR compatible) | High, but some coatings cost more |
Global Production Volume | Very High (economies of scale) | Moderate to High (region-dependent) |
Key Takeaways:
- Polyester benefits from global supply chain optimization, particularly in China, India, and Vietnam.
- Polyamide costs are heavily influenced by origin—Japan- and Korea-made nylon tends to be more expensive due to quality control and technology.
- For coated technical fabrics (e.g., TPU-coated), the cost gap can narrow due to shared post-processing needs.
Buyer Tip: Always check the denier, weave, and finish. For instance, 300D polyester oxford might cost \$0.85/meter, while 300D nylon oxford costs \$1.40/meter—but has 30% better abrasion resistance.
Which Fabric Has a Lower Price per Yard or Meter in Bulk Manufacturing?
Polyester consistently has a lower per-yard or per-meter price compared to polyamide, especially at high-volume MOQs. In 2024 B2B sourcing data, the average price of polyester fabric (100–300D) ranged from \$0.60 to \$1.20 per yard, while polyamide (nylon) fabrics ranged from \$1.20 to \$2.50 per yard, depending on denier, weave, and finish. Polyester fabric typically costs 30–50% less than polyamide (nylon) fabric when purchased in bulk, making it more economical for budget-conscious brands or large-scale production.
Bulk Price Comparison by Fabric Type
Fabric Type | Polyester (\$/yard) | Polyamide/Nylon (\$/yard) |
---|---|---|
210D Oxford | \$0.65–\$0.85 | \$1.20–\$1.60 |
300D Oxford | \$0.75–\$0.95 | \$1.40–\$1.80 |
600D Oxford | \$0.85–\$1.10 | \$1.60–\$2.10 |
Ripstop (Lightweight) | \$0.90–\$1.20 | \$1.80–\$2.30 |
Taffeta (Lining) | \$0.60–\$0.80 | \$1.10–\$1.50 |
Bulk Sourcing Considerations:
- MOQ: Polyester suppliers typically accept lower MOQs (300–500 yards), while nylon suppliers often require 500–1000 yards minimum.
- Lead Time: Polyester fabrics are quicker to source due to larger global stock availability.
- Shipping Cost Impact: Nylon’s slightly heavier density per yard can increase freight charges by 5–8% on large-volume orders.
A Southeast Asian sportswear brand switched from 210D nylon to coated 300D polyester for lining. Though it saved \$0.55 per yard, product returns due to fabric abrasion increased by 9%, leading to higher warranty claims—proving value must be balanced against end-use durability.
How Do Raw Material and Energy Costs Affect Polyester vs Polyamide Pricing?
Raw material and energy inputs are two of the biggest cost influencers in synthetic fabric manufacturing. Polyester benefits from lower-cost inputs and less energy-intensive processing, whereas polyamide (nylon) requires higher-temperature polymerization and specialized monomers, which elevate both energy and raw cost components—especially in volatile markets. Polyester costs are less sensitive to oil price fluctuations and require less energy for production, while polyamide’s more complex chemistry makes it costlier and more volatile in pricing.
Cost Chain from Oil Barrel to Finished Fabric
1. Raw Material Volatility
Material | Base Source | Market Sensitivity | Recent 12-Month Cost Change |
---|---|---|---|
Polyester (PET) | Crude oil → Ethylene glycol | Moderate | +8% |
Polyamide (PA6) | Crude oil → Caprolactam | High | +16% |
- Polyester’s base monomers (DMT or PTA) are globally produced with more stable supply chains.
- Polyamide monomers like caprolactam are more niche and subject to geopolitical and environmental regulatory shifts.
2. Energy Requirements
Process Stage | Polyester (kWh/kg) | Polyamide (kWh/kg) |
---|---|---|
Polymerization | 4.5–6.0 | 8.0–9.5 |
Spinning & Drawing | 3.0–4.0 | 4.0–5.5 |
Heat Setting & Finishing | 2.0–2.5 | 2.5–3.0 |
- Polyamide consumes 40–60% more electricity across its production cycle.
3. Global Impact Example: In 2023, rising European energy prices drove up polyamide prices by 20–30%, while polyester prices remained relatively stable due to China-based production and pre-bought energy contracts.
If you’re operating in energy-sensitive regions (e.g., Europe, Japan), polyester offers better long-term pricing predictability, while polyamide may require hedging or long-term supplier agreements.
Is Polyamide’s Higher Performance Worth the Extra Cost for Your Product?
Yes—but only if the application demands high tensile strength, stretch recovery, abrasion resistance, or performance in extreme environments. Otherwise, polyester may deliver better overall ROI in price-sensitive segments like promotional wear, fashion, or non-technical apparel. Polyamide’s extra cost is justified for heavy-duty, technical, or outdoor-use products. For general consumer or low-abrasion items, polyester often offers better value for money.
Performance vs. Value Chart
Feature | Polyester | Polyamide (Nylon) | Which Offers More Value? |
---|---|---|---|
Tensile Strength | Good | Excellent | Polyamide |
Abrasion Resistance | Moderate | Very High | Polyamide |
Stretch Recovery | Low–Moderate | High (esp. PA66 blends) | Polyamide |
UV Resistance | High | Low–Moderate | Polyester |
Moisture Absorption | Low (0.4%) | Higher (3–4%) | Polyester (dry feel) |
Color Retention (UV exposed) | Excellent | Moderate | Polyester |
Price Performance Balance | Excellent (budget) | Strong (premium) | Depends on use case |
4. Real-Life Applications Where Polyamide Wins:
- Hiking backpacks and tactical gear: Polyamide is 30–40% more durable under friction.
- Performance sportswear (e.g., yoga leggings): Blended with elastane for stretch and shape retention.
- Military or rescue outerwear: Withstands cuts, abrasions, and harsh weather.
5. When Polyester is Enough:
- Printed fashion jackets or lifestyle totes
- Interior linings or cheap promotional gear
- Recycled eco-fabric applications, where brand messaging trumps tech spec
🎯 Decision Tip: If your product will face frequent motion, stretch, abrasion, or load-bearing, polyamide’s premium may be worth every cent. For low-impact or disposable items, polyester wins on efficiency.
What Are the Maintenance and Lifecycle Costs of Polyester vs Polyamide?
Though polyester is cheaper upfront, polyamide often lasts longer in high-stress applications, reducing replacement frequency. That said, polyester holds better against UV damage and mold, especially in humid environments, which may extend its usable life in certain climates. So, total cost of ownership depends on wear cycles, care frequency, and application context. Polyamide jackets or gear last longer under high abrasion but may require more care. Polyester resists UV and mold better, with lower maintenance needs, making it ideal for low-maintenance, high-turnover products.
Lifecycle Comparison Chart
Factor | Polyester | Polyamide (Nylon) |
---|---|---|
Average Lifespan (clothing) | 2–4 years (light use) | 3–6 years (heavy-duty use) |
Wash Cycles (before pilling) | 30–40 | 50–80 |
UV Resistance (outdoor use) | Excellent | Fair–Moderate |
Mold Resistance | Excellent | Moderate |
Care Required | Low | Moderate (can degrade if overheated) |
Repairs/Restitch Rates | Lower (weaker under strain) | Lower (but more prone to fraying) |
A U.S. outdoor workwear brand switched to nylon for high-friction zones in jackets (elbows, shoulders). Though unit cost increased by \$0.70, field testing showed a 2.3x reduction in repair frequency, ultimately saving over \$12,000 in customer support labor in one year.
🧠 Pro Tip for Sourcing Teams: For school uniforms, fast fashion, or interior linings, polyester’s low maintenance is a win. But for technical gear, military, or pro sportswear, polyamide’s lifecycle value pays back over time.
Are There Differences in MOQ, Sampling, and Production Lead Times?
polyester is more widely available, with lower minimum order quantities (MOQs) and faster sample turnaround, especially in Asia. Polyamide tends to be sourced through specialized mills, requiring more time and larger initial investment. Polyester typically has lower MOQs (300–500 yards), faster sample lead times, and more stock availability. Polyamide often requires higher volumes and longer customization timelines due to its specialized nature.
Supply Chain and Production Speed Comparison
Process Stage | Polyester | Polyamide (Nylon) |
---|---|---|
MOQ for Custom Colors | 300–500 yards | 500–1000 yards |
MOQ for Coated Fabric | 500 yards (common) | 800–1000 yards (specialized) |
Lab Dip/Color Swatch Time | 3–5 working days | 5–8 working days |
Sample Yardage Time | 5–7 working days | 7–10 working days |
Bulk Production Lead Time | 15–20 days | 20–30 days |
- Stock Availability: Polyester fabrics—especially oxford, twill, taffeta—are widely available and replenishable.
- Weave Flexibility: Polyester supports wider customization with jacquard, dobby, or mixed blends.
- Small Batch Sampling: Many suppliers (like SzoneierFabrics) allow polyester prototype runs as low as 100–200 yards.
🎯 Buyer Strategy: If speed to market or iterative sampling is key (e.g., for fashion or seasonal gear), polyester offers faster turnaround and lower risk. For longer-term, high-margin technical products, nylon’s slower but specialized supply chain can still be profitable.
Do Recycled Polyester and Recycled Polyamide Change the Cost Equation?
recycled versions of polyester (rPET) and polyamide (such as ECONYL) often cost more than virgin polyester but less than virgin nylon, depending on production volume, certification, and source. While rPET is now widely available and competitively priced, recycled nylon remains a premium product due to its complex recovery and regeneration process. Recycled polyester offers a low-cost sustainable option, while recycled polyamide is pricier but higher in performance and eco-branding appeal. The cost gap is narrowing as technology scales.
Sustainability Cost and Value Breakdown
Material Type | Avg. Price (\$/yard) | Recycled Availability | Certification Options |
---|---|---|---|
Virgin Polyester | \$0.70–\$1.10 | High | GRS, OEKO-TEX |
Recycled Polyester (rPET) | \$0.95–\$1.30 | Very High | GRS, Repreve®, EcoCircle |
Virgin Polyamide (Nylon) | \$1.40–\$2.50 | Medium | OEKO-TEX |
Recycled Polyamide (ECONYL, etc.) | \$1.80–\$3.00 | Low–Medium | ECONYL®, GRS, Bluesign® |
1. Production Differences:
- rPET: Made from post-consumer bottles, low-cost logistics, compatible with standard polyester machinery.
- Recycled Nylon: Often involves ocean plastics or fishing nets, requiring depolymerization and repolymerization.
2. Buyer Use Cases:
- rPET is widely used in eco-conscious fashion, bags, linings, promotional gear.
- Recycled polyamide is preferred in premium outdoor, activewear, and luxury accessories.
🌱 Sustainability Insight: Many brands pay 10–25% more for recycled materials—but command 30–50% higher retail pricing. For example, Patagonia and Allbirds use rPET in outerwear to align with ESG goals and consumer preference for transparent sourcing.
How Should B2B Buyers Decide Based on Use Case, Budget, and Market Positioning?
The choice between polyester and polyamide—virgin or recycled—should be based on a total value framework, not just cost per meter. Buyers must weigh fabric performance, branding goals, sourcing flexibility, sustainability priorities, and final product pricing strategy. Choose polyester for affordability and fast scaling, polyamide for durability and performance. Recycled variants add branding power and sustainability value, especially in mid-to-high-end markets.
Final Decision Matrix for B2B Buyers
Buyer Type | Use Case | Recommended Fabric | Reason |
---|---|---|---|
Fashion Apparel Brand | Seasonal collections | rPET or virgin polyester | Low cost, easy printing, quick sampling |
Outdoor Gear Brand | Hiking, tactical, jackets | Polyamide or ECONYL | Strength, abrasion resistance |
Eco-Focused Brand | Sustainable products | rPET or ECONYL | Brand messaging + sustainability |
Bag Manufacturer | Backpacks, duffels | 600D polyester or nylon | Balance of strength and cost |
Luxury Activewear | Leggings, technical tops | Nylon-elastane blends | Stretch, premium hand feel |
Choose Smart, Not Just Cheap
Choosing between polyester and polyamide isn’t just about saving pennies—it’s about aligning function, brand vision, sustainability, and speed to market. Polyester offers predictable supply, low MOQs, and fast sampling, while polyamide delivers rugged performance and lifecycle durability. And when recycled options are in play, the decision becomes a strategic branding advantage.
At SzoneierFabrics, we understand every buyer is different—some need a cost-effective 600D polyester with water resistance; others want a GRS-certified ECONYL® blend that reinforces a luxury brand’s climate commitment. Whatever your case, we’ve got you covered.
📩 Start Your Fabric Customization Journey Today
✅ Free consultation & technical support ✅ Low-MOQ custom fabrics in polyester or nylon ✅ Certified recycled options (rPET, ECONYL®, GRS fabrics) ✅ Fast sampling in 5–7 days ✅ 100% quality assurance and short lead time
📧 Email: Info@szoneierfabrics.com 🌐 Website: https://szoneierfabrics.com 📞 Phone: (+86) 13823134897
Can't find the answers?
No worries, please contact us and we will answer all the questions you have during the whole process of bag customization.
Make A Sample First?
If you have your own artwork, logo design files, or just an idea,please provide details about your project requirements, including preferred fabric, color, and customization options,we’re excited to assist you in bringing your bespoke bag designs to life through our sample production process.