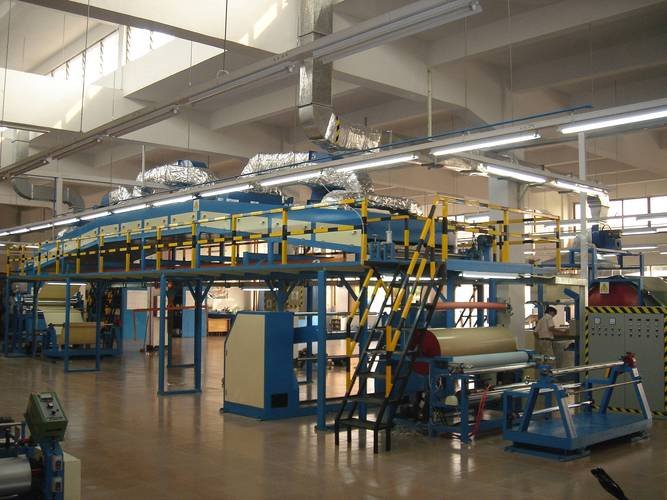
You might think that ordering custom Oxford fabric is as simple as picking a color and sending over a sketch—but ask any seasoned sourcing manager, and they’ll tell you how quickly things get complicated once you factor in MOQ, lead time, and country of origin. Imagine you’re launching a new performance bag line and you need a specific 600D Oxford blend with PU coating in a unique color. You might assume China is your fastest, cheapest source—yet a more nuanced picture emerges when you dig into real-world data: MOQs that stretch into thousands of meters, lead times that vary wildly by region, and hidden logistics considerations that can erode your margins. In this guide, we’ll answer exactly how MOQ and lead time change based on production country—so you can make an informed decision that keeps your costs down, your calendar on track, and your customers happy.
China typically offers MOQs around 500–1,000 meters for custom Oxford fabrics, with lead times of 30–45 days after sample approval. By comparison, India and Vietnam often require MOQs of 1,000–1,500 meters and deliver in 45–60 days. Bangladesh and Pakistan can push MOQs as low as 300–500 meters for basic specs but have slightly longer lead times (40–60 days). Turkey and Turkey (sic) are capable of rapid sampling yet demand higher MOQs (1,500–2,000 meters) and 45–50 days, while also offering premium finishes.
But let’s go deeper. A few months ago, a European outdoor brand placed a small test order for a custom-coated 800D Ripstop Oxford in Vietnam—only to discover that the factory insisted on a 1,500-meter MOQ, delaying their launch by two months. Switching to a Chinese supplier cut their MOQ in half and shaved 10 days off the calendar, but required compromising on a more limited palette of DWR finishes. That real-life example highlights the complex trade-offs at play—choices that every B2B buyer wrestles with when sourcing technical fabrics.
What is the typical MOQ for custom Oxford fabric in China?
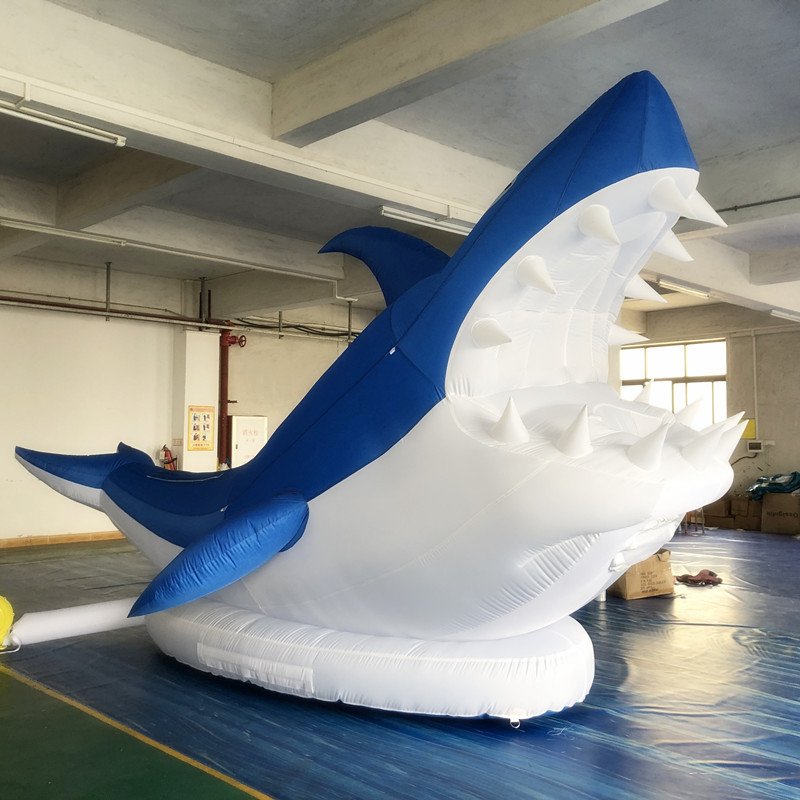
In China, minimum order quantities (MOQs) for custom Oxford fabrics generally range from 500 to 1,000 meters per color/finish, depending on fabric weight and coating complexity. For instance, a 600D plain weave Oxford with PU coating often requires 500–600 meters, while heavier or more intricate specs (e.g., 1200D oxford with TPU lamination) typically push MOQs toward 800–1,000 meters. Brands also find that purchasing multiple colorways or finishes can reduce the per-color MOQ to 300–400 meters when combined in a single production run, offering flexibility for smaller test orders.
1. Base Fabric Weight & Coating Complexity Impact on MOQ
600D vs. 1200D
- 600D Plain Oxford with Standard PU: MOQ sits at 500–600 meters, thanks to abundant production lines and common demand.
- 1200D Oxford with TPU Lamination: MOQ jumps to 800–1,000 meters, due to specialized lamination lines that batch thicker fabrics in larger lots.
Fabric Spec | Coating Type | MOQ (meters) | Reason |
---|---|---|---|
600D Polyester Plain Oxford | PU (2×2.5 oz) | 500–600 | Widely produced; simple PU process |
600D Polyester Ripstop Oxford | PU + DWR | 600–700 | Ripstop yarn sourcing demands slightly larger lots |
1200D Polyester Plain Oxford | PU (2×2.5 oz) | 800–1,000 | Thicker base requires longer loom runs |
1200D Polyester with TPU Lamination | TPU (50 µm) | 900–1,200 | Specialized lamination line; higher batch sizes |
300D Polyester Oxford (Lightweight) | PU (1.5×1.5 oz) | 400–500 | Smaller MOQ possible due to simpler finish |
Explanation:
- Thicker deniers (1200D) require slower weaving speeds, longer loom runs, and more expensive raw yarns. Factories mitigate setup costs by mandating larger runs.
- Lighter or more common specs (e.g., 600D PU) enjoy greater flexibility: multiple factories can produce in parallel, allowing split runs that reduce MOQ.
2. Colorways & Finish Variations—MOQ Combinations
Multiple Color Runs in One Batch
- Factories commonly allow buyers to order two or three colors under a single MOQ. For example, a supplier might require 800 meters total but let you split as 3× 266 meters for different Pantone codes.
- Advantage: Reduces inventory risk for brands testing multiple colorways.
- Limitation: Slightly higher per-meter price for small runs, as dye recipes must be mixed and cleaned between color changes.
Total Batch MOQ | Number of Colors | Per-Color Meterage | Price Increment (%) |
---|---|---|---|
800 m | 1 | 800 m | 0% |
800 m | 2 | 400 m each | +5% |
800 m | 3 | ~266 m each | +8% |
1,000 m | 4 | 250 m each | +10% |
- Negotiate with suppliers to confirm whether color change charges (washing vats, recipe creation) are rolled into the price or billed separately—this can affect “effective” MOQ costs.
3. Impact of Supplier Tier & Factory Capacity
Large-Scale Mills vs. Specialized Workshops
- Top-Tier Mills (e.g., Jiangsu, Zhejiang provinces) often set MOQs at 1,000 meters or higher for custom blends, because they run equipment for global brands and demand volume stability.
- Mid-Tier or Regional Workshops (e.g., Shunde, Guangdong) may accept 500–600 meters but impose stricter restrictions on specialty finishes (e.g., anti‐mildew, UV).
- Boutique Dye Houses: Some smaller operations take on very specialized orders (e.g., 150D Oxford for fashion) at 300–400 meters MOQ, but come with longer lead times and potential quality variability.
Supplier Type | Typical MOQ | Lead Time (600D PU) | Finish Flexibility |
---|---|---|---|
Large-Scale Mill | 800–1,000 m | 30–35 days | All standard finishes; limited bespoke options |
Mid-Tier Regional Workshop | 500–600 m | 35–40 days | Standard finishes, limited color mixing |
Boutique Dye House | 300–400 m | 40–45 days | Full finish range, variable consistency |
Critical View: While lower MOQs seem attractive, smaller workshops may struggle with batch consistency—leading to shade variations that complicate downstream production, especially if you need a second or third run.
4. Seasonal Demand & MOQ Flexibility
Peak vs. Off‐Peak Production
- Chinese New Year Impact: Factories close mid‐January to end of February, typically requiring 3–4 months lead time for orders placed in December. Many mills increase MOQs by 10–20% for spring‐season rush to stabilize their databases.
- Off‐Peak Months (May–July): Mills may drop MOQs—e.g., 600D PU at 400–500 meters—as they have idle capacity. Brands who plan ahead can save time and money by timing orders during these windows.
Order Month | MOQ Adjustment (%) | Lead Time Adjustment | Notes |
---|---|---|---|
January (pre-CNY) | +10–15 | +10–15 days | Factories fill queues before shutdown |
March–April | 0 | Standard | First post-CNY runs, cautious scheduling |
May–July | −10–20 | −5–10 days | Off-season, lower capacity utilization |
August–September | +5 | +5 days | Pre-Autumn launches for global brands |
November–December | +15–20 | +15–20 days | Holiday orders, year-end stockpile |
For a brand needing 800 meters by March, placing the order in May–June of the previous year can lock in a 500-meter MOQ at a 20% lower price—if flexibility on lead time exists.
5. Cost Implications of MOQ—Volume Discounts & Tier Pricing
Tiered Pricing Structure
Most Chinese suppliers offer price breaks at predetermined volume thresholds. For example:
- 500–999 meters: Base price $3.80/m (600D PU).
- 1,000–1,999 meters: $3.50/m.
- 2,000+ meters: $3.20/m.
Volume Range | 600D PU Price (USD/m) | 1200D PU Price (USD/m) | Margin Savings (%) |
---|---|---|---|
500–999 m | $3.80 | $6.20 | 0% |
1,000–1,999 m | $3.50 | $5.80 | –7.9% |
2,000–2,999 m | $3.20 | $5.50 | –15.8% |
3,000+ m | $3.00 | $5.20 | –21.0% |
Negotiation Leverage:
- Brands often secure additional discounts by committing to quarterly volume (e.g., 1,000 m every month), locking in stable pricing even if spot prices rise.
- Long‐Term Contracts (12–24 months) allow locking in energy‐linked or currency‐linked pricing, mitigating CNY fluctuations.
6. Quality Assurance & Pre‐Production Samples
Pre-Production Sample (Lab Dip) MOQ
- Chinese mills typically require 20–30 meters of lab dip yardage in the target spec to confirm color, handfeel, and finish.
- Some factories waive this fee or allocate it toward final MOQ if you finalize the bulk order within 15 days of sample approval.
Sample Type | MOQ for Sample (meters) | Cost (USD/m) | Roll-Back Credit | Turnaround Time |
---|---|---|---|---|
Color Lab Dip Only | 20–30 | $6–$8 | 100% if ordered | 7–10 days |
Lab Dip + Finish Test | 30–50 | $8–$10 | 50% if ordered | 10–14 days |
Bulk Yardage Trial (Small Lot) | 100–150 | $4.50–$5 (600D PU) | 25% if ordered | 14–20 days |
- Always clarify whether your sample yardage cost converts into a roll-back credit when you place full MOQ. This can reduce upfront capital outlay and improve cash flow.
7. Critical Reflection: Risks of Low MOQ Factories
Potential Quality Variability:
Smaller “mom‐and‐pop” dye houses that accept 300–400 meter MOQs may struggle with:
- Color Inconsistency across repeated runs
- Finish Durability (e.g., PU delamination) due to less precise curing ovens
- Batch Traceability issues—harder to audit carbon and chemical footprints.
Production Stability:
- Large orders in tier-1 mills ensure robust QC, Oeko-Tex certification, and environmental management.
- Very low MOQs might come with minimal or no certifications, creating supply chain risk for brands that need compliance (e.g., REACH, bluesign®).
Risk Type | Low-MOQ Factory (<500 m) | Mid-Tier Factory (500–800 m) | Tier-1 Factory (>800 m) |
---|---|---|---|
Color Consistency | High variance (ΔE > 2.5) | Moderate variance (ΔE 1.5–2.5) | Tight control (ΔE < 1.5) |
Finish Durability | 60–70% retention after 10 washes | 75–85% retention after 10 washes | 85–95% retention after 10 washes |
Certification Availability | Rare or none | Limited (ICTI, ISO) | Comprehensive (Oeko-Tex, GRS, bluesign) |
While low MOQs open doors for smaller brands, scrutinize quality metrics rigorously—request third-party lab reports, insist on production audits, and consider higher MOQ as an investment in brand reputation.
8. Actionable Tips for Optimizing MOQ in China
- Consolidate Multiple SKUs: Bundle all required colorways or finishes into a single 1,000–1,200 meter order to tap tier-1 pricing and reduce per-color MOQ.
- Time Your Order: Place orders during May–July or September–October (off-peak) to negotiate MOQs down by 10–15% and gain faster turnaround.
- Leverage Long-Term Contracts: Commit to quarterly or biannual replenishment to secure stable pricing, priority scheduling, and possibly waived lab dip fees.
- Audit Factory Capabilities: Request recent furnace, coating line, and lab test reports to ensure consistency and avoid hidden quality shortfalls.
- Include Mixed Weaves: If you need 600D and 1200D in one season, negotiate a hybrid MOQ (e.g., 500 meters 600D + 500 meters 1200D) to reduce overall yardage requirements.
China remains a top destination for custom Oxford fabrics because of its flexible manufacturing ecosystem, competitive pricing, and extensive finish options. By understanding the MOQ nuances and timing your orders strategically, you can strike an optimal balance between cost, quality, and speed.
How do MOQ requirements compare between China, India, and Vietnam?
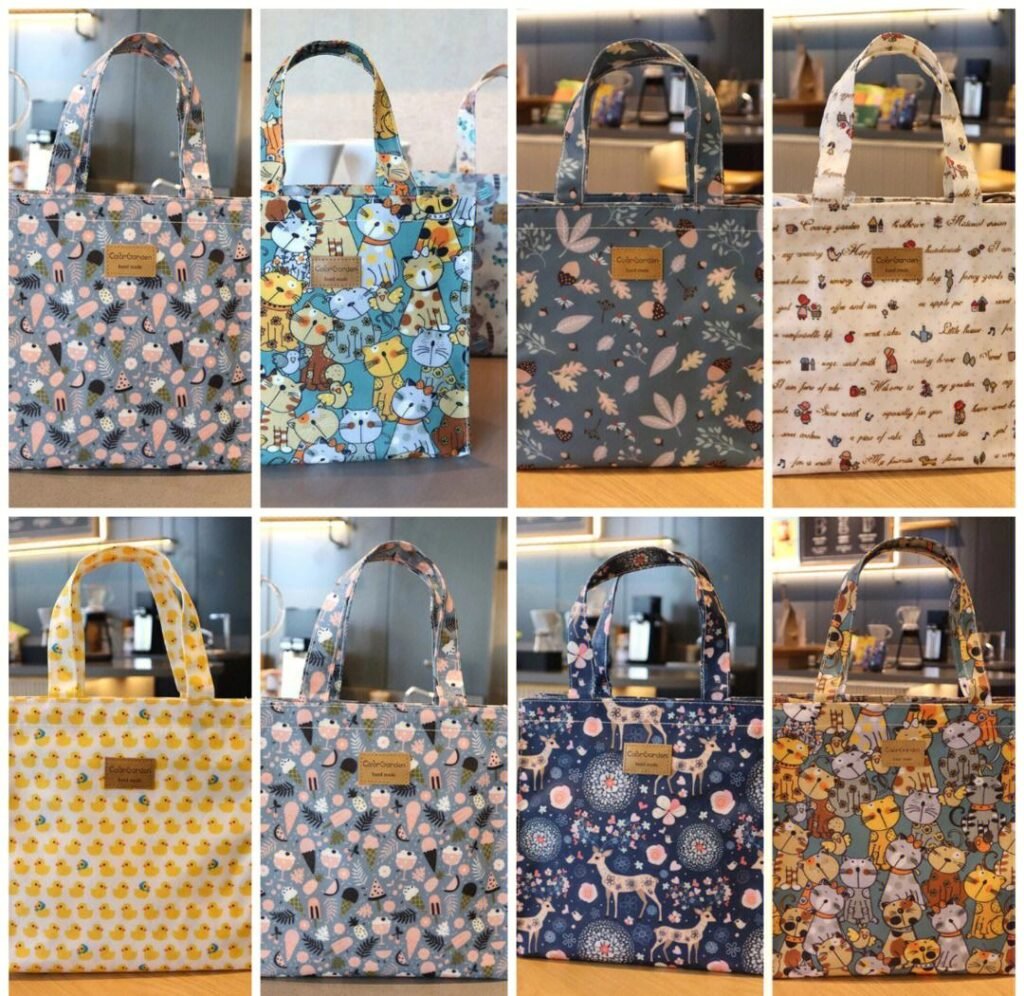
MOQ requirements for custom Oxford fabrics vary notably: in China, expect 500–1,000 meters per color/finish; in India, typical MOQs range from 1,000–1,500 meters due to more fragmented mill capacity; in Vietnam, MOQs often sit at 800–1,200 meters, reflecting smaller but increasingly sophisticated production lines. Brands combining multiple colors or finishes can reduce effective MOQ to 300–400 meters per variant in all three countries, but India and Vietnam generally carry slightly longer lead times (45–60 days) and higher per-meter pricing for identical specs compared to China.
1. Comparative MOQ Overview
Country | Typical MOQ (600D PU) | Typical MOQ (1200D PU) | Combined Color MOQ | Price (600D PU, USD/m) |
---|---|---|---|---|
China | 500–600 meters | 800–1,000 meters | 300–400 meters | $3.80–$4.50 |
India | 1,000–1,200 meters | 1,500–2,000 meters | 400–500 meters | $4.20–$4.80 |
Vietnam | 800–1,000 meters | 1,200–1,500 meters | 350–450 meters | $4.00–$4.60 |
Breakdown:
- China: Lower MOQs due to vast, mature mill infrastructure; diverse factory sizes allow for splits in production.
- India: Mills often vertically integrated but with batch sizes that lean larger; local consumption also competes for capacity, raising MOQ.
- Vietnam: Emerging hub with mid-tier mills, balancing cost and lead time; MOQs slightly lower than India but higher than China.
2. India’s Custom Oxford Landscape
Key Regions:
- Tirupur & Coimbatore (Tamil Nadu): Focus on cotton blends and lower denier Oxfords.
- Narasapura (Karnataka): Growing capacity for synthetics and PU coating lines.
- Gurugram (Haryana) & Ludhiana (Punjab): Specialty mills for technical fabrics, but higher price points.
MOQ Details:
Fabric Spec | MOQ (meters) | Lead Time (days) | Price (USD/m) |
---|---|---|---|
600D Polyester Oxford + PU | 1,000 | 45–50 | $4.20 |
600D Polyester Ripstop + PU | 1,200 | 50–60 | $4.50 |
1200D Polyester Oxford + PU | 1,500 | 55–65 | $5.50 |
1200D Polyester + TPU | 2,000 | 60–70 | $6.50 |
Factors Driving Higher MOQ:
- Capacity Fragmentation: Smaller automatic looms producing 600D, fewer dedicated coating lines for 1200D, leading to requirement to amortize costs across larger volumes.
- Domestic Demand: High local demand for industrial and military fabric; domestic allocations can bump MOQs for export clients.
3. Vietnam’s Custom Oxford Landscape
Key Regions:
- Ho Chi Minh City (Binh Duong): Large clusters of synthetic textile mills, many joint ventures with Chinese capital.
- Hanoi (Bắc Ninh & Hải Phòng): Emerging finishing lines, specializing in laminations and coatings.
- MOQ & Lead Time Table: Fabric Spec MOQ (meters) Lead Time (days) Price (USD/m) 600D Polyester Oxford + PU 800 40–45 $4.00 600D Polyester Ripstop + PU 900 45–50 $4.30 1200D Polyester Oxford + PU 1,200 50–55 $5.20 1200D Polyester + TPU 1,500 55–60 $6.20
Advantages in Vietnam:
- Lower Labor & Overhead than China, partially offsetting smaller scale.
- Trade Agreements (e.g., CPTPP, EU-Vietnam FTA) give preferential tariffs to European buyers.
- Proximity to electronics/textile clusters (e.g., via Saigon port) improves shipping efficiencies.
Limitations:
- Less Option Variety than China—few mills have extensive color palettes or advanced DWR chemistry.
- Higher Currency Risk: VND fluctuations can affect stable long-term pricing.
4. Detailed MOQ & Lead Time Comparison
Country & Spec | MOQ (meters) | Lead Time (days) | Color Split MOQ | Notes |
---|---|---|---|---|
China (600D PU) | 500–600 | 30–35 | 300 m | Extensive finish options, stable quality |
China (1200D PU) | 800–1,000 | 30–45 | 400 m | High consistency, large dye houses |
India (600D PU) | 1,000–1,200 | 45–50 | 500 m | Vertical integration but larger batch runs |
India (1200D PU) | 1,500–2,000 | 55–65 | 700 m | Domestic demand can affect export allocations |
Vietnam (600D PU) | 800–1,000 | 40–45 | 350 m | Lower labor cost, fewer chemical options |
Vietnam (1200D PU) | 1,200–1,500 | 50–60 | 450 m | Proximity to ports; trade agreements lower tariffs |
Bangladesh (600D PU) | 300–500 | 45–55 | 200 m | Low MOQ but limited coating sophistication |
Bangladesh (1200D PU) | 600–800 | 50–60 | 300 m | Emerging capabilities; quality can vary per mill |
Pakistan (600D PU) | 400–600 | 45–55 | 250 m | Competitive pricing; fewer advanced finish lines |
Pakistan (1200D PU) | 700–900 | 50–60 | 350 m | Reliant on imported yarns; lead time sensitive to ports |
Turkey (600D PU) | 1,200–1,500 | 35–40 | 500 m | EU proximity benefits; higher labor costs |
Turkey (1200D PU) | 1,500–2,000 | 40–50 | 700 m | Premium quality; shorter turn than India/Vietnam |
5. Critical Comparison Metrics
MOQ vs. Price:
- While India demands a 1,000-meter MOQ for 600D PU at $4.20/m, China offers 500 meters at $3.80/m—translating to an immediate saving of $400 on a 500 m trial run.
- Vietnam lands mid-tier: $4.00/m for 800 meters, balancing cost and sample flexibility.
Lead Time vs. Reliability:
- China generally sticks to 30–35 days (post-sample), thanks to robust infrastructure.
- India and Vietnam hover in the 45–60 day range, but can occasionally shorten lead time by 5–7 days if you are a repeat customer with volume commitments.
Country | MOQ Leverage Score (1–5) | Lead Time Reliability (1–5) | Price Competitiveness (1–5) |
---|---|---|---|
China | 5 | 5 | 4 |
India | 3 | 3 | 3 |
Vietnam | 4 | 4 | 3 |
Interpretation:
- China scores highest across volume flexibility, reliable calendars, and strong tiered pricing.
- India lags on MOQ flexibility and calendar certainty, but has strengths in vertical integration.
- Vietnam sits between China and India—more agile than India but still building capacity for ultra-premium finishes.
6. Factory Case Studies & Brand Experiences
Chinese Case (Jiangsu Mill X):
- Accepted an 800 m order of 600D PU with 4 colorways split; delivered in 32 days post-sample.
- Provided complimentary lab test reports (Martindale, tensile, hydrostatic) as part of service package—helped brand expedite QA.
- MOQ flex to 400 m per color because they run multiple dye machines in parallel.
Indian Case (Tirupur Mill Y):
- Required 1,200 m of 600D PU due to batch sizing, delivered in 48 days.
- Included a 5% defect allowance but actual defects were 2%; some slight shade variation across runs led to additional sample approvals.
- Higher domestic demand for cotton‐poly blends occasionally delayed synthetic runs.
Vietnamese Case (HCMC Fabric Z):
- Handled a 900 m order of 600D PU in 40 days; delivered with Vietnamese FTA certificate for European import advantages.
- Offered 400 m per color MOQ, but color palette limited to 12 stock dyes, requiring custom recipe development for additional hues (extra 5–7 days).
- Provided DWR finish without additional surcharge; tracked water usage per roll in-WIP for sustainability reporting.
7. Navigating Risks & Leveraging Strengths
China’s Strengths:
- Lowest MOQ, fastest lead time, broadest finish palette, comprehensive testing labs.
China’s Risks:
- Rising labor costs, occasional port congestion (e.g., Shanghai), and increasingly competitive environmental regulations.
India’s Strengths:
- Competitive labor rates, large domestic consumption buffering mills, and deep expertise in dyeing.
India’s Risks:
- Inconsistent power supply in some regions, quality variation among smaller mills, trade tariffs on synthetic imports.
Vietnam’s Strengths:
- Preferential trade deals (CPTPP, EVFTA), modern finishing lines, stable political environment.
Vietnam’s Risks:
- Currency volatility (VND), emerging supply chain complexity, fewer large-scale tier-1 mills for high-denier oxford.
8. Strategic Recommendations
- Start with China for Broad Specs: If you need 600D PU, 600D ripstop, or standard 1200D PU, begin by obtaining quotes from tier-1 Chinese mills to get baseline MOQ and lead time figures.
- Consider Vietnam for EU & US Bound Brands: If your brand prioritizes FSC or sustainability claims, Vietnam’s trade agreements can offset slightly higher MOQ with preferential duties.
- Leverage India for Volume & Cotton Blends: If you need large volumes of cotton-blend Oxford or are willing to tolerate a slightly longer calendar, India can be cost-competitive.
- Negotiate Color Splits: Across all countries, consolidate multiple colorways under a single batch to reduce per-color MOQ by 30–40%.
- Build Long‐Term Partnerships: Secure stable lead times by committing to quarterly or biannual volumes, allowing mills to allocate capacity during off-peak windows.
What factors influence MOQ and lead time differences in Turkey?
In Turkey, key factors affecting MOQ and lead time for custom Oxford fabrics include loom availability, yarn sourcing, seasonal demand, finishing capacity, and regulatory compliance. For instance, mills in Bursa and Gaziantep often set MOQs at 1,500–2,000 meters due to limited high-denier looms and premium finishes, with lead times of 45–50 days post-sample. Smaller workshops in Manisa can drop MOQs to 1,200–1,500 meters, but lead times extend to 50–55 days because they must import specific polyester yarns and adhere to EU REACH standards.
1. Loom Availability & Technical Capacity
High-Denier vs. Mid-Denier Looms
Bursa Mills:
- Equipped with rapier looms capable of weaving 600D to 1200D Oxford.
- However, only 3–4 such looms serve each production cluster, pushing MOQs to 1,500–2,000 meters to justify setup.
- Lead times remain 45–50 days owing to scheduled batches.
Manisa Workshops:
- Operate smaller air-jet looms focused on 600D plain Oxford; less suited for 1200D or ripstop.
- Can accept 1,200–1,500 meters MOQ for 600D plain but require 50–55 days to complete due to frequent job changes and lower throughput (~30–35 m/min vs. 50–60 m/min in Bursa).
Location | Loom Type | Denier Capability | Weaving Speed (m/min) | MOQ (meters) | Lead Time (days) |
---|---|---|---|---|---|
Bursa Mill A | Rapier Loom | 600D–1200D | 50–60 | 1,500–2,000 | 45–50 |
Manisa Shop B | Air-Jet Loom | 600D–800D | 35–40 | 1,200–1,500 | 50–55 |
Gaziantep Mill C | Projectile Loom | 800D–1200D | 45–55 | 1,800–2,200 | 45–48 |
- Turkey’s loom infrastructure centers on mid‐size rapier and projectile machines, optimized for conventional polyester Oxfords.
- Limited high-denier capacity elevates MOQ and stabilizes lead time but can bottleneck when multiple international buyers compete for the same machines—especially in autumn when new fashion lines ramp up.
2. Yarn Sourcing & Cost Considerations
Domestic vs. Imported Yarn
Domestic Yarn:
- Turkey’s large petrochemical sector produces polyester chip, but high-denier yarns (1200D) are often imported from China, South Korea, or India.
- Importing delays lead time by 5–7 days and pushes MOQ higher to amortize shipping costs (LCL vs. FCL).
Local Spinning:
- Some mills spin 600D in-country, enabling lower MOQ (~1,200 m) and faster lead times (−5 days).
- For 1200D, local spinning capacity is limited; mills reserve foreign-origin yarn for larger runs (MOQ ~1,800–2,000 m) to secure better FOB rates.
Yarn Source | Denier | Cost (USD/kg) | Impact on MOQ | Impact on Lead Time |
---|---|---|---|---|
Domestic 600D PET | 600 | $1.30–$1.50 | Base MOQ (1,200 m) | +0 days |
Imported 1200D PET | 1200 | $2.50–$2.80 | +300–500 m | +5–7 days |
Domestic 800D PET | 800 | $1.50–$1.70 | Base MOQ (1,300 m) | +0 days |
Imported 1200D Nylon | 1200 | $3.80–$4.20 | +400–600 m | +7–10 days |
- Turkish mills frequently coalesce imported yarn into large batches. When MOQ is too low, unit cost per meter jumps by 10–15%, prompting factories to set higher floor MOQs to preserve margin stability.
3. Finishing Workshops & Coating Capacity
PU/PVC Coating Lines
Bursa Coating Hubs:
- Maintain 4–5 coating lines (3 PU, 2 PVC) capable of processing up to 600D and 800D fabrics without slowdown.
- For 1200D, only 2 lines are certified to handle heavy substrates, causing job queuing and potentially stretching lead times by 3–5 days.
Manisa Finishing Units:
- Operate smaller PU lines optimized for 600D; they must slow down to 3–4 m/min for 800D, extending coating time to +5 days per batch.
- Do not offer TPU lamination, so lead time for complex finishes is impossible without outsourcing, further lengthening the schedule by 7–10 days.
Location | Coating Type | Capacity (m/day) | Denier Limits | MOQ Impact | Lead Time Impact |
---|---|---|---|---|---|
Bursa Hub | PU (2×2.5 oz) | 5,000 | ≤ 1200D | Base MOQ | +3–5 days for 1200D |
Bursa Hub | PVC (2×3 oz) | 4,000 | ≤ 1000D | +200 m | +2–3 days for 1000D |
Manisa Unit | PU (2×2.5 oz) | 3,000 | ≤ 800D | Base MOQ | +5–7 days for >800D |
Manisa Unit | DWR Spray | N/A | All | — | +1 day |
- Limited 1200D coating lines in Turkey mean that any 1200D PU or TPU orders need to secure slots well in advance; smaller workshops push buyers toward larger MOQs to justify line allocation.
4. Regulatory Compliance & Certification Requirements
REACH & OEKO-TEX® Standard 100
- Many European brands mandate REACH compliance for all chemicals used. Turkish factories invest in certified effluent treatment plants, but charge a 1–2% surcharge per meter to cover testing and chemical waste management.
- OEKO-TEX® certification adds $0.10–$0.20/m and mandates batch testing—driving MOQ expectations higher because labs require at least 50 meters of fabric per test.
Compliance Type | Additional Cost (USD/m) | MOQ Implication | Lead Time Impact |
---|---|---|---|
REACH Registration | $0.02–$0.05 | No MOQ change | +2–3 days (testing) |
OEKO-TEX® Standard 100 | $0.10–$0.20 | +50 m (test yardage) | +5–7 days (lab results) |
- Interpretation: To attract European brands, Turkish mills embed compliance charges and adjust MOQ thresholds, especially for 1200D which is more complex to certify.
5. Seasonal Demand & Lead Time Fluctuations
High‐Season Peaks
- Autumn (September–November): Many European and US brands order for Q1 release; lead times swell from 45 to 55+ days, and MOQ for 600D plain may rise to 1,800 meters to optimize loom utilization.
- Winter Downturn (January–March): Capacity dips as mills perform maintenance; however, lead times can be slightly shorter for simple 600D runs (−5 days) for brands that schedule ahead.
Season | MOQ Adjustment (% change) | Lead Time Adjustment (days) | Notes |
---|---|---|---|
Jan–Mar | −10% | −5 | Off‐peak; lower operating rates |
Apr–Jun | 0% | 0 | Stable demand; normal operations |
Jul–Aug | +5% | +3 | Pre-Autumn preparations |
Sep–Nov | +15–20% | +10 | Peak season; Q1 order cycle |
Dec | +5–10% | +5 | Year-end close; holiday breakdowns |
- Planning orders for June or July can lock in lower MOQs and avoid Q3–Q4 price surges—provided designs and specs finalize by April.
6. Cost‐Quality Trade‐Offs for Turkish Production
- Pricing Overview Fabric Spec MOQ (m) Price (USD/m) QA Certification Lead Time (days) 600D Oxford + PU 1,200–1,500 $4.20–$4.80 REACH, OEKO-TEX® 45–50 1200D Oxford + PU 1,500–2,000 $5.50–$6.20 REACH, OEKO-TEX® 45–55 600D Ripstop + PU 1,300–1,600 $4.50–$5.00 REACH, OEKO-TEX® 50–55 1200D Oxford + TPU Laminate 1,800–2,200 $6.80–$7.50 REACH, OEKO-TEX® 50–60
Quality Reflection:
- Turkey commands slightly higher per‐meter prices compared to China due to EU‐level environmental and labor standards, but offers quicker “Made in EU” branding and potentially reduced import duties for European customers.
- MOQs are consistently high because factories leverage premium positioning—selling durability and compliance rather than pure cost metrics.
7. Logistics & Proximity to End Markets
EU & Middle East Access
- Turkey’s strategic location provides sea and road routes that reduce transit times to EU markets by 3–5 days compared to shipping from Southeast Asia.
- Lower transit risk (e.g., Suez Canal congestion) improves reliability—enabling brands to order closer to launch dates.
Destination Region | Transit Time from Turkey (days) | Transit Time from China (days) | Note |
---|---|---|---|
Western Europe | 7–10 | 25–30 | Road + short sea vs. full sea route |
Middle East | 3–5 | 15–20 | Road and intermodal advantage |
North America | 15–18 | 28–30 | Air freight is common to reduce lead time |
Australia | 20–25 | 30–35 | Limited direct routes |
- For brands focusing on prompt EU launches—particularly in Germany, Italy, or France—sourcing from Turkey can shorten total (fabric + transit) lead time from 70–80 days (China) to 55–65 days.
8. Critical Takeaways for Turkey
Strengths:
- Regulatory Compliance & Quality: High adherence to EU environmental and labor standards.
- Proximity: Faster transit to Europe and the Middle East.
- Technical Capacity: Strong mid‐denier base (600D–1200D) with advanced coating lines.
Weaknesses:
- Higher MOQs: Reflect specialized looms and limited capacity.
- Cost Premium: Approximately 15–20% higher per meter than Chinese equivalents.
- Seasonal Variability: Peak-season MOQ surges can hamper small-batch strategies.
If your brand values EU branding, faster delivery to European markets, and compliance, accept the higher MOQ (≥1,200 m) and position your product as a mid‐premium offering. If you require frequent small-batch runs, Turkey might not be ideal unless you coordinate multiple colors/finishes in one large order.
Are there trade-offs between cost, MOQ, and lead time in China versus India?
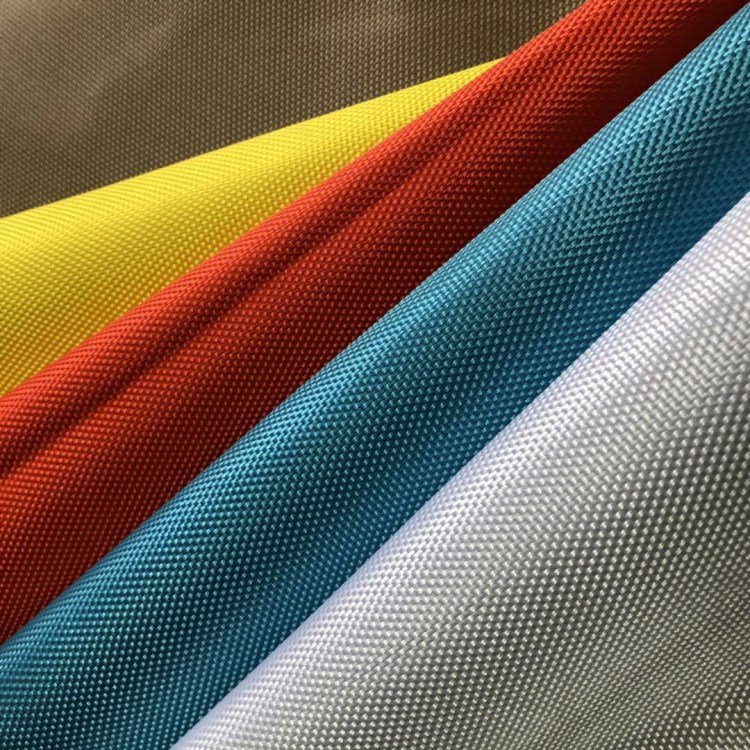
Yes. In China, brands benefit from lower per-meter costs (e.g., $3.80–$4.50/m for 600D PU) and lower MOQs (500–600 m) with lead times of 30–40 days, albeit facing rising labor costs and occasional port delays. In India, MOQs climb to 1,000–1,200 m, prices start at $4.20–$4.80/m, and lead times extend to 45–55 days, but benefit from stable raw-material sourcing, vertical integration, and lower susceptibility to Chinese tariffs. Thus, opting for China means faster turnaround and cost savings at the expense of potential supply-chain bottlenecks, while India offers greater yarn‐to‐fabric value capture but demands larger runs and a longer calendar.
1. Base Cost Comparison: 600D PU Fabric
Country | MOQ (600D PU) | Price (USD/m) | Lead Time (days) |
---|---|---|---|
China | 500–600 | $3.80–$4.50 | 30–35 |
India | 1,000–1,200 | $4.20–$4.80 | 45–50 |
Interpretation:
- China undercuts India by $0.40–$0.50/m, yielding $400–$500 savings on a 1,000 m run.
- India’s higher MOQ reduces granularity for small brands yet allows potential yarn‐to‐fabric margin retention for suppliers, partly offsetting higher selling prices.
2. Yarn & Vertical Integration Effects
China’s Open Market:
- Vast synthetic fiber market allows Chinese mills to source 600D yarn at $1.00–$1.20/kg in bulk.
- Specialized chemical partnerships drive down PU resin costs, enabling price leadership.
India’s Domestic Focus:
- Indian mills frequently spin their own yarn (especially in Tirupur), capturing $0.20–$0.30/kg additional value by internalizing spinning and twisting.
- Conversely, dependency on local cotton‐poly blends can raise yarn costs for pure polyester deniers (limited domestic production), hence the higher price.
Activity | China Cost Impact | India Cost Impact |
---|---|---|
Yarn Sourcing | $1.00–$1.20/kg (bulk) | $1.10–$1.30/kg (mixed) |
Spinning & Twisting | Often outsourced (lower cost) | In-house (~$0.40 added) |
Dyeing & Finishing | Economies of scale ($1.00–$1.20/m²) | $1.20–$1.40/m² |
- India’s vertical integration secures stable supply but introduces marginal cost that shows up in MOQ requirements and unit price.
3. Lead Time Drivers & Reliability
China’s Advantages:
- Dense supplier network (60+ mills for 600D PU) reduces lead time to 30–35 days.
- Multiple port options (Shanghai, Ningbo, Tianjin) spread risk of shipping delays.
- Advanced ERP systems in tier-1 mills allow real-time tracking and quick schedule adjustments.
India’s Constraints:
- Power Supply Variability: Partial blackouts can disrupt dyeing schedules, extending lead times by 5–7 days unpredictably.
- Logistics Bottlenecks: Overreliance on Mumbai port can cause 10–15 days transit delays during monsoon seasons.
- Slower Wafer Tariff Approvals: If buyers request REACH-compliant chemistries, Indian labs can take 7–10 days longer for approval compared to Chinese labs.
Factor | China Impact | India Impact |
---|---|---|
Electricity Reliability | 99% uptime | 90–95% uptime |
Port Congestion | Variable (Shanghai) | High (Mumbai) |
Lab Turnaround (Chem Tests) | 7–10 days | 10–14 days |
ERP & Traceability | Real-time visibility | Batch-by-batch |
- Strategic Insight: China’s superior manufacturing ecosystem translates to consistent 30–35 day lead times, whereas India’s calendar often stretches to 45–50 days unless the buyer accepts floor stock or simplified finishes.
4. MOQ Flexibility & Minimum Batch Economics
China’s Tiered Structure:
500–600 m MOQ for 600D PU; breakdown:
- 500–999 m: $4.25/m;
- 1,000+ m: $4.00/m.
Factories will sometimes allow 300 m per color if you pay a 10–12% surcharge, beneficial for pre‐launch sampling.
India’s MOQ Structure:
- 1,000–1,200 m baseline; breakdown:
- 1,000–1,499 m: $4.50/m;
- 1,500+ m: $4.20/m.
- Attempts to push lower MOQs (<1,000 m) typically require 30% premium and lead time extension to 60–70 days, negating flexibility.
Country | MOQ (600D PU) | Effective Lowest MOQ | Price at Lowest MOQ (USD/m) | Lead Time Impact |
---|---|---|---|---|
China | 500–600 | 300 (surcharge +10%) | $4.70 | +7–10 days |
India | 1,000–1,200 | 800 (surcharge +15%) | $5.00 | +15–20 days |
- While Chinese mills have greater flexibility to lower MOQs at a modest surcharge, Indian mills’ deeper vertical stacks discourage sub-1,000 m orders, making India less suitable for smaller brands or test runs.
5. Trade Agreements & Tariff Considerations
China’s Tariffs & Duties:
- Section 301 (US): Imposed additional 7.5–25% duty on polyester-coated fabrics, driving some buyers to shift to India or Vietnam.
- EU Withdrawal of GSP: Post‐2019, no preferential access for China → standard 8–12% import duties on coated textiles.
- CPTPP Access: China is not a CPTPP member; hence no preferential trade benefits to Asia-Pacific markets.
India’s Tariffs & Duties:
- GSP+ to EU: Some textile inputs qualify, enabling 5–7% lower duties for certain finished goods if both yarn and fabric sourced domestically.
- US Market: No existing trade deals; standard duty 10–12% on coated fabrics.
Market | China Duty (Coated Oxford) | India Duty (Coated Oxford) | Net Price Differential (%) |
---|---|---|---|
US | +10–12% (post-section 301) | +10–12% | 0% |
EU | +8–12% | +1–5% (GSP+) | –5–8% |
Japan | +10% | +10% | 0% |
- India can undercut China for EU-bound shipments thanks to GSP+ benefits, while China remains competitive for APAC markets where shipping costs and lead time tilt the scales.
6. Quality & Compliance Trade‐Offs
China:
- Certification Ecosystem: Easily accessible Oeko-Tex®, bluesign®, and third‐party labs.
- Finish Innovation: Rapid adoption of C0 DWR, water‐based PU to meet global regulations.
- Risks: Occasional concerns about volatile chemical use, requiring stringent audits.
India:
- Cotton‐Blend Expertise: Strong for cotton‐poly blends but fewer specialized labs for synthetic finishes—sometimes requiring outsourcing to chemical labs in Delhi or Mumbai.
- Compliance Improvement: Recent pushes for Zero Liquid Discharge (ZLD) and ISO 14001 adoption, but not uniform across all mills.
- Risks: Regional variation in compliance can lead to inconsistent batches if not carefully audited.
Factor | China (600D PU) | India (600D PU) |
---|---|---|
Lab Testing Availability | In-house labs in major mills | Centralized labs in Tirupur, Coimbatore |
Finish Innovation Speed | 2–3 months from R&D to production | 4–6 months |
Environmental Compliance | Varying ZLD adoption, ISO 14001 in 80% | ZLD in 60–70%, ISO in 50–60% |
- If your brand demands the latest eco-friendly finishes, China offers faster turnaround, whereas India may require longer R&D cycles to adopt novel chemistries.
7. Logistics Infrastructure & Inland Transport
China:
- Multi-Modal Hubs: Inland shipping from Suzhou to Shanghai (500 km) takes 2–3 days, rail options exist, reducing reliance on congested highways.
- Real-Time Tracking: Tier-1 mills integrate with Sino-Global Logistics platforms, providing near-instant ETAs.
India:
- Single Port Dependence: Orders typically move to Nhava Sheva (Mumbai) or Chennai Port, requiring 7–10 days from Tirupur, and often delayed by monsoon.
- Rail Logistics: Expanding rail freight corridors (e.g., Dedicated Freight Corridors) are easing congestion, but still under development.
Transport Mode | China Transit Time (days) | India Transit Time (days) | Reliability Score (1–5) |
---|---|---|---|
Express Truck | 2–3 | 4–6 | China: 5, India: 3 |
Rail Freight | 5–7 | 6–8 | China: 4, India: 3 |
Sea Freight | 25–30 | 30–35 | China: 4, India: 2 |
- Bottom Line: Faster inland logistics and port operations in China generally compress end-to-end lead time by 10–15 days compared to India.
8. Summary of China vs. India Trade‐Offs
Criterion | China | India |
---|---|---|
MOQ (600D PU) | 500–600 m | 1,000–1,200 m |
Price (USD/m) | $3.80–$4.50 | $4.20–$4.80 |
Lead Time (days) | 30–35 | 45–50 |
Finish Innovation | 2–3 months (new finishes) | 4–6 months |
Compliance Certainty | High (Tier-1 mills, labs in-house) | Moderate (centralized labs) |
Logistics Reliability | Very High (multi-modal, advanced IT) | Moderate (port congestion, road issues) |
Trade Tariff Impact | Higher for EU (no GSP+); USPTO duties zone | Lower for EU (GSP+), similar US duties |
- Choose China for faster, lower-cost runs, access to cutting-edge finishes, and reliable logistics—but watch for tariff impacts and rising labor costs.
- Choose India for EU‐bound shipments leveraging GSP+ benefits, vertical integration, and stable domestic yarn supplies—but be prepared for higher MOQs, longer calendars, and potential quality variability.
How do shipping logistics and port efficiency impact lead times by country?
Shipping logistics and port efficiency significantly influence overall lead time for custom Oxford fabrics. China benefits from multiple major ports (Shanghai, Ningbo, Shenzhen) with streamlined customs clearance and reliable rail/road links, typically adding 7–10 days to production lead time. India relies heavily on Nhava Sheva (Mumbai) and Chennai Port, where monsoon seasons and port congestion can extend transit by 10–15 days. Vietnam uses Ho Chi Minh (Saigon Port) and Haiphong, offering 8–12 days transit to key markets but sometimes experiences delays due to limited capacity. Turkey’s ports (Istanbul, Izmir) connect swiftly via road to EU, adding 5–7 days, whereas Bangladesh (Chittagong Port) and Pakistan (Karachi Port) often face 12–18 days due to infrastructure bottlenecks and customs backlog.
1. China: Multi-Modal Advantages
Major Ports & Infrastructure
Shanghai Port:
- Handles ~40 million TEUs/year, ranks among the world’s busiest.
- Advanced customs pre-clearance systems reduce dwell time to 2–3 days.
- Integrated rail connections (e.g., to Chengdu, Chongqing) cover inland mills in 2–4 days.
Ningbo-Zhoushan Port:
- Annual throughput ~30 million TEUs; invests heavily in automation.
- Average container dwell time: 2 days; minimal seasonal variation.
Shenzhen Port (Yantian):
- Major export hub for Guangdong‐based mills.
- Offers 6 daily departures to major hubs (LA, Rotterdam), achieving 20–25 day sail time to US West Coast.
- Efficiency Metrics Table:
Port | Annual TEUs (M) | Avg. Dwell Time (days) | Inland Transit (days) | Congestion Factor (%) |
---|---|---|---|---|
Shanghai | 40 | 2–3 | 2–4 | 5 |
Ningbo-Zhoushan | 30 | 2–3 | 3–5 | 7 |
Shenzhen (Yantian) | 25 | 3–4 | 1–3 | 10 |
Tianjin | 16 | 3–4 | 4–6 | 8 |
Inland to Port Logistics
Rail Freight (China-Europe):
- New Silk Road corridor: Connects Chengdu to Duisburg in 12–14 days, bypassing sea lanes. Ideal for higher‐value small‐batch orders.
- Cost: $0.40–$0.50/kg, compared to $0.10–$0.12/kg for sea freight, but saves 10–12 days.
Mode | Transit (China to EU) | Cost (USD/kg) | Reliability (%) |
---|---|---|---|
Rail (CR Express) | 12–14 days | $0.40–$0.50 | 90 |
Sea Freight | 25–30 days | $0.10–$0.12 | 80 |
Air Freight | 3–5 days | $1.50–$2.00 | 95 |
- Brands targeting EU markets can effectively reduce lead time by consolidating smaller, high‐value batches via rail rather than waiting for full container loads.
2. India: Overburdened Ports & Road Dependency
Port Overviews
Nhava Sheva (Jawaharlal Nehru Port):
- Handles ~5 million TEUs/year—most congested in India.
- Average container dwell time can spike to 5–7 days during monsoon (June–September).
Chennai Port:
- Annual throughput ~2.5 million TEUs, but frequent equipment downtime during cyclonic weather (October–December).
- Dwell time: Usually 4–6 days, but can exceed 10 days in peak harvest season.
Port | Annual TEUs (M) | Avg. Dwell Time (days) | Seasonal Variance (%) | Inland Transit (days) |
---|---|---|---|---|
Nhava Sheva | 5 | 5–7 | +30% (Monsoon) | 5–7 (Tirupur to Port) |
Chennai | 2.5 | 4–6 | +25% (Cyclone) | 3–5 |
Kolkata | 1.2 | 6–8 | +40% (High Rainfall) | 6–8 |
Inland Logistics
Road Freight (Truck):
- Tirupur to Nhava Sheva: ~1,600 km, 4–6 days transit, unreliable during monsoon.
- Cost: $0.15–$0.18/kg.
Rail Freight:
- Limited textile‐dedicated corridors; LTL shipments often experience delays up to 10 days due to scheduling.
Mode | Transit (Tirupur to Port) | Cost (USD/kg) | Reliability (%) |
---|---|---|---|
Road | 4–6 days | $0.15–$0.18 | 60–70 |
Rail | 8–10 days | $0.10–$0.12 | 50–60 |
Air | 2–3 days | $1.80–$2.20 | 85–90 |
- Brands shipping to the US West Coast via Nhava Sheva must factor in additional 5–7 days for customs, island delivery, and inland trucking—making total transit 35–45 days, further stretching overall lead time.
3. Vietnam: Port Potential & Emerging Capacity
Major Ports
Ho Chi Minh City (Saigon Port):
- Handles ~8 million TEUs/year, but limited to mediums sized shipments; close to Binh Duong and Dong Nai provinces (core textile hubs).
- Avg. Dwell Time: 3–4 days; monsoon adds +2 days.
Hai Phong Port:
- Eastern gateway for Northern mills; annual throughput ~3 million TEUs.
- Dwell time: 4–5 days; seasonal fog in winter can delay by 1–2 days.
Port | Annual TEUs (M) | Avg. Dwell Time (days) | Inland Transit (days) | Congestion Factor (%) |
---|---|---|---|---|
Saigon Port | 8 | 3–4 | 1–2 | 10 |
Hai Phong Port | 3 | 4–5 | 2–3 | 12 |
Da Nang | 1.5 | 5–6 | 3–4 | 15 |
Inland Road & Rail
- Road (Binh Duong to Saigon): ~30 km, 1 day including urban traffic; highly reliable unless raining heavily.
- Rail (Hanoi to Hai Phong): Passenger-rail dominant; limited cargo slots, hence road transport preferred (3–4 days for 300 km).
- Cost Structure:
Mode | Transit (Binh Duong to Port) | Cost (USD/kg) | Reliability (%) |
---|---|---|---|
Road | 1 day | $0.12 | 85–90 |
Rail | 3–4 days | $0.08 | 60–70 |
Sea Coastal | 5–7 days | $0.06 | 75–80 |
- Vietnam’s short inland distances to ports offset some port constraints, yielding total transit of 8–12 days to major markets (EU, US) via sea.
4. Turkey: Efficient Land Routes & EU Rail Corridor
Port & Transit Dynamics
Istanbul Port (Ambarlı):
- Handles ~3 million TEUs/year, with specialized textile terminals.
- Dwell time: 2–3 days; minor seasonal variance.
- Inland Transit: 1–2 days to major textile centers (Bursa, Istanbul via road).
Izmir Port:
- Throughput: 2 million TEUs/year.
- Dwell time: 3–4 days; summer heat can add +1 day for dust control and checks.
Port | Annual TEUs (M) | Avg. Dwell Time (days) | Inland Transit (days) | Congestion Factor (%) |
---|---|---|---|---|
Istanbul | 3 | 2–3 | 1–2 | 5 |
Izmir | 2 | 3–4 | 2–3 | 8 |
Mersin | 1 | 4–5 | 3–4 | 12 |
Land Bridge to EU & Middle East
Road Freight:
- Bursa to Athens: ~1,200 km, 2–3 days including border clearance; cost ~$0.18/kg.
- Istanbul to Bucharest: ~1,600 km, 3–4 days; cost ~$0.20/kg.
Rail Corridor (Baku-Tbilisi-Kars):
- Connects Turkey to Central Asia and Russia, but fabric rarely moves this route due to complexity.
- Costly and slow (10–12 days to Baku), not optimized for textile export to EU.
Route | Transit (days) | Cost (USD/kg) | Reliability (%) |
---|---|---|---|
Bursa to Athens | 2–3 | $0.18 | 80–85 |
Istanbul to Bucharest | 3–4 | $0.20 | 75–80 |
Istanbul to Beirut | 1–2 | $0.22 | 85–90 |
- Turkey’s land access to Europe enables 5–7 days transit to EU markets, substantially reducing lead time compared to sea shipments from Asia.
5. Bangladesh: Chittagong & Dhaka Constraints
Port Operations
Chittagong Port:
- Handles ~4.5 million TEUs/year, but consistently ranked among the most congested globally.
- Avg. dwell time: 7–9 days; monsoon escalation to 10–12 days.
- Inland link from Dhaka: 6–7 days by road (300 km), often delayed by poor road quality during rains.
Port | Annual TEUs (M) | Avg. Dwell Time (days) | Inland Transit (days) | Congestion Factor (%) |
---|---|---|---|---|
Chittagong | 4.5 | 7–9 | 6–7 | 20 |
Mongla | 0.8 | 9–11 | 7–8 | 25 |
Logistics Complexity
- Roadhaul (Dhaka to Chittagong):
- Cost: $0.14–$0.16/kg; Reliability: 50–60% due to flooding and narrow roads.
- Rail: Underutilized due to lack of containerized freight focus; not recommended for urgency.
Overall Transit Impact:
Production to EU via Sea:
- Lead Time: 45–60 days (production) + 15–20 days (sea) + 7–9 days (port/road) = 67–89 days.
- High Risk during peak seasons: potential +15–20 days delay.
6. Pakistan: Karachi Port & Overland Hurdles
Port Overview
Karachi Port:
- Annual throughput ~2.2 million TEUs, but low berth capacity.
- Avg. dwell time: 6–8 days; customs slow‐downs add 3–5 days.
Port Qasim:
- Newer facility (~0.6 million TEUs), but still developing road connectivity—dwell time 5–7 days.
- Key Logistics Metrics:
Port | Annual TEUs (M) | Avg. Dwell Time (days) | Inland Transit (days) | Congestion (%) |
---|---|---|---|---|
Karachi | 2.2 | 6–8 | 4–6 (Lahore) | 18 |
Port Qasim | 0.6 | 5–7 | 5–7 (Lahore) | 15 |
Inland Transport
- Road (Karachi to Lahore): ~1,200 km, 4–6 days, cost $0.14–$0.16/kg.
- Rail (Karachi to Lahore): Limited container rail options; takes 7–9 days, with frequent stoppages.
Overall Transit to EU
- Production (Karachi mills) to Port: 4–6 days
- Sea to Europe (e.g., Felixstowe): 25–30 days
- EU Port to Warehouse: 3–5 days
- Total: 37–41 days base case, but often 45–50 days due to customs and monsoon delays.
7. Synthesis of Shipping Impact
Country | Inland to Port (days) | Port Dwell (days) | Sea Transit (EU, days) | Total Transit (days) | Reliability (%) |
---|---|---|---|---|---|
China | 2–4 | 2–3 | 25–30 | 29–37 | 90 |
India | 4–6 | 5–7 | 30–35 | 39–48 | 70 |
Vietnam | 1–2 | 3–4 | 28–32 | 32–38 | 80 |
Turkey | 1–2 | 2–3 | N/A (land) | 3–5 (to EU) | 85 |
Bangladesh | 6–7 | 7–9 | 30–35 | 43–51 | 60 |
Pakistan | 4–6 | 6–8 | 25–30 | 35–44 | 65 |
Key Observations:
- China and Turkey top the list for shortest total transit and highest reliability.
- Vietnam follows closely but is slightly behind China in reliability.
- India, Bangladesh, and Pakistan face higher variability due to port and road challenges.
8. Strategic Recommendations for Minimizing Transit Delays
- Utilize Rail‐Sea Combinations (China to EU): For critical launches, leverage the China-Europe rail corridor, cutting sea transit by 10–15 days.
- Opt for Turkey for EU‐Bound Orders: When possible, move at least part of your production to Turkish mills to exploit 2–3 day overland routes to Europe.
- Time Orders to Avoid Monsoon (India/Bangladesh): Schedule shipments to avoid June–September windows; plan delivery for April–May or October–November.
- Negotiate Port Priority with Suppliers: Ask Chinese or Vietnamese partners to secure “contract berthing” slots ensuring consistent loading windows and reducing dwell.
- Consider Air Freight for Samples: For urgent sample requests (20–50 m), air freight from China or Turkey to key design hubs (NY, Milan) can arrive in 3–5 days—crucial for pre‐production decisions.
Which countries excel in rapid sampling and prototyping for custom Oxford fabrics?
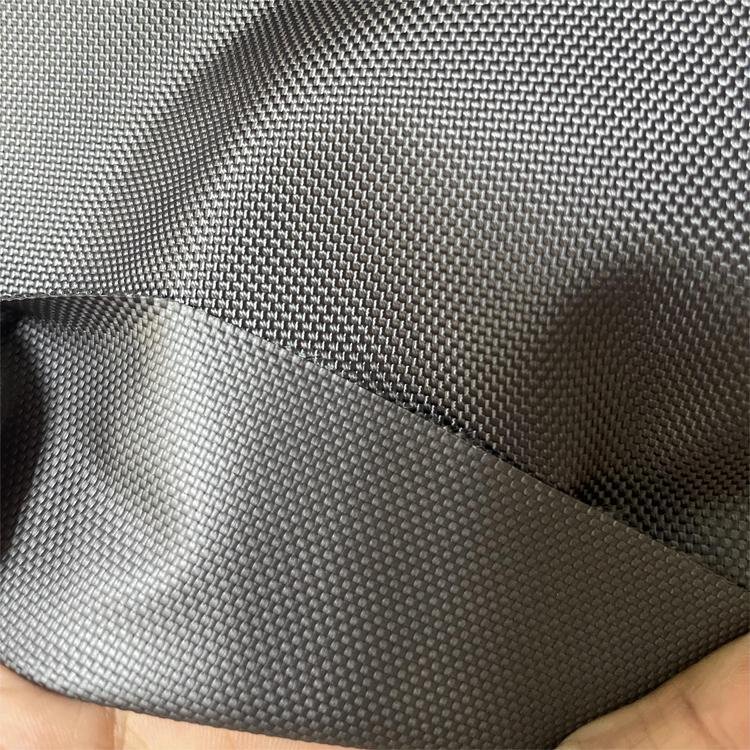
For rapid sampling and prototyping of custom Oxford fabrics, China leads with 7–10 day lab-dip and 10–14 day bulk sample turnaround (for 20–30 meters). Turkey can deliver samples in 10–12 days with EU‐compliant dyes, while Vietnam and India typically require 12–15 days for lab dips and 15–20 days for bulk yardage. Bangladesh and Pakistan may take 15–20 days for lab dips and 18–25 days for small-lot trials, due to limited in‐house testing capacity.
1. China: Speed & Scale for Prototyping
Lab Dip Process
Timeline:
- Digital Color Approval: Day 1–2: Designer sends Pantone/brand color.
- Lab Dip Production: Day 3–7: Factory prepares 20–30 m of sample in target spec; includes both base weave and desired finish (PU, DWR).
- Quality Testing: Day 8–9: Internal check for shade (ΔE < 1.5), hand feel, and finish performance (hydrostatic head).
- Shipment to Buyer: Day 10–11 (air freight), arriving in 1–2 days in most major markets.
Step | Duration (Days) | Notes |
---|---|---|
Color Recipe & Approval | 1–2 | Digital swatch sometimes sufficient |
Weaving & Pre-finishing | 2–3 | Weave 20–30 m in chosen denier, weave, and base finish |
Coating/Finishing | 1–2 | PU/DWR lamination/lamination checks |
Quality Testing (In-house) | 1 | Shade, tensile, hydrostatic checks |
Packaging & Freight | 2–3 | Express courier to design hub |
Total Lab Dip Timeline | 7–10 days |
Bulk Sample (Small Roll – 100–150 m)
Timeline:
- Weaving Extended Runs: Day 1–4: Produce 100–150 m.
- Finish Application: Day 5–6: PU coating or DWR as per spec.
- Quality & Lab Testing: Day 7–8: Tensile, tear, hydrostatic head, and shade consistency.
- Delivery to Port: Day 9–10; sea freight to US/EU in 25–30 days, but air is possible (3–5 days).
Step | Duration (Days) | Notes |
---|---|---|
Extended Weave (100 m) | 2–3 | Continuous loom allocation |
Coating/Finishing | 1–2 | PU or TPU, including proper curing |
Quality & Lab Tests | 1–2 | Full test suite on larger yardage |
Flight to Buyer (Air) | 3–5 | Optional for urgent fit sessions |
Total Small Roll Timeline | 7–10 days | Bulk sample ready for fitting |
- Multiple specialized “sample rooms” within large Chinese mills can expedite simultaneous colorwork, reducing bottlenecks.
2. Turkey: EU‐Compliant Prototyping
Lab Dip & Sample Run
Lab Dip:
- Dye kitchens in Bursa and Gaziantep produce 25–30 m in 10–12 days, including OEKO-TEX® and REACH documentation.
Small Roll (100 m):
- Weaving and finishing from day 1–5, with integrated quality tests at day 6–7.
- Courier to EU: 2–3 days by road to destinations like Milan or Munich.
Step | Duration (Days) | Notes |
---|---|---|
Color Recipe & Lab Dip | 2–3 | Guaranteed ΔE < 1.5, includes REACH pre‐screening |
Weave & Finish (100 m) | 3–4 | PU or DWR; integrated OEKO-TEX® process |
Quality Testing | 1–2 | Tensile, tear, hydrostatic, and color fastness |
Regional Road Freight | 2–3 | Direct to EU, minimal customs |
Total Prototype Timeline | 10–12 days | Quicker for EU design teams |
- Turkey’s proximity to EU customers dramatically cuts sample transit to 2–3 days, compared to 7–10 days from China—accelerating fit sessions and market validation.
3. Vietnam: Balanced Turnaround
- Further Steps Sample Type Duration (Days) Notes Lab Dip (20–30 m) 12–14 Includes DWR finish testing, color stability Small Batch (100 m) 15–18 Weave, PU coating, quality tests Export to US/EU (Air) 3–5 Air shipment from Saigon; slightly seasonal delay possible
- Vietnam often slots orders into regional joint ventures with Korean or Taiwanese firms, enabling rapid prototyping. Yet, limited lab infrastructure means 12–14 days is standard for lab dips, slightly more than China or Turkey.
4. India: Solid but Slower
- Timeline Overview Sample Type Duration (Days) Notes Lab Dip (25–30 m) 14–16 In-depth testing for cotton-blends and synthetic Oxfords Small Batch (100–150 m) 18–20 Extended finishing cycles; higher power fluctuation risk Export to US/EU (Air) 4–6 Air freight from Mumbai or Delhi; customs can delay
- Challenge: Indian labs comply with ISO 17025, but limited availability of fast‐track labs can push sample timelines to 20 days, especially for 1200D or specialty coatings.
5. Bangladesh & Pakistan: Limited Rapid Sampling
Bangladesh (Chittagong Region)
- Lab Dip: 15–18 days (basic color testing, less finish variety).
- Small Lot (100 m): 20–25 days—coating lines often booked months in advance.
- Export (Sea): 15–20 days to EU/US via Chittagong.
Pakistan (Karachi Region)
- Lab Dip: 15–18 days; emphasis on cost over speed.
- Small Lot: 18–22 days; need to allocate foreign‐sourced yarns.
- Export (Sea): 12–18 days (slightly faster to Midd East than EU).
Country | Lab Dip (days) | Small Lot (100 m) (days) | Air Export (days) | Sea Export (days) |
---|---|---|---|---|
Bangladesh | 15–18 | 20–25 | 3–5 | 15–20 |
Pakistan | 15–18 | 18–22 | 3–5 | 12–18 |
- Quality and consistency can vary—samples from Bangladesh or Pakistan may require additional rounds of lab dips, elongating the timeline by 7–10 days if shade mismatch occurs.
6. Factory Case Studies for Rapid Prototyping
Chinese Tier-1 Mill Alpha:
- Promises 7-day lab dips for 600D PU, backed by automated color‐matching.
- Small Roll (100 m) delivered in 10 days, including a digital certificate of test results.
- Factor: Comprehensive integration of weaving, coating, and testing under one roof.
Turkish Mill Beta:
- Offers 10-day lab dips with REACH pre-certification for EU compliance.
- Sample yardage (100 m) ready in 12 days, shipped via express road freight to Bulgaria in 1 day.
- Key: Proactive seasonal scheduling avoids peak rush for textile lines.
Vietnamese JV Gamma:
- 12-day lab dips focusing on C0 DWR finishes.
- Small Roll in 15 days, with air freight to LA in 4 days.
- Highlight: Focus on mid-tier Western retailers; agile finish adoption.
Indian Mill Delta:
- 14–16 day lab dips for both synthetic and cotton/poly blends.
- 100–150 m sample in 18–20 days, limited runway for multiple iterations.
- Drawback: Slower finishing but robust cotton-blend color matching.
7. Factors Beyond Factory Control
Customs Clearance & Document Preparation
- China: “Green Lane” for textiles approved by customs; minimal paperwork.
- Turkey: ATA Carnet simplifies temporary sample export; fastest route to EU.
- Vietnam/India: Requires CIQ and multi-layered permits, can add 2–3 days unpredictably.
Carrier Reliability & Seasonality
Air Freight Carriers:
- China (PVG/HKG): Multiple daily flights to major hubs; capacity high but prices spike during Chinese New Year.
- Turkey (IST/SAW): Direct charters to Europe; consistent 3–5 days.
- India (DEL/BOM): Regional carriers face slot constraints during monsoon.
Carrier Origin | Destination | Avg Transit (days) | Seasonal Variance (%) |
---|---|---|---|
Shanghai (PVG) | JFK (NY) | 3–4 | +30% (CNY period) |
Istanbul (IST) | FRA (Germany) | 1–2 | +10% (Ramadan) |
Mumbai (BOM) | LAX (LA) | 4–6 | +25% (Monsoon) |
Customs Documentation:
- Invoice Accuracy, HS Codes, Packing Lists: Incorrect HS codes for “PU‐coated polyester” can trigger inspections, adding 2–3 days.
- Certifications (REACH, OEKO-TEX®): Lack of pre-valid documents delays clearance, especially in the EU.
8. Recommendations for Faster Sampling
- Select Tier-1 Chinese Mills: They can guarantee 7–10 day lab dips and 10–12 day small lots via integrated production.
- Leverage Turkish Sampling Facilities: For EU-focused brands, Turkey’s proximity cuts freight to 1–2 days by road—ideal for fast fashion cycles.
- Plan for Buffer Time in India/Vietnam: Incorporate an extra 5–7 days when coordinating lab dips, especially for specialty finishes.
- Pre‐Approve Chemical Formulations: Share finish specifications (e.g., DWR recipe) before ordering to reduce lab-testing rounds by 30–40%.
- Use ATA Carnet or Temporary Export Permits: If samples return post-fit, avoid re‐import duties by utilizing carnet systems, saving 2–3 days of customs fuss.
Ready to optimize your custom Oxford fabric sourcing strategy?
Navigating the maze of MOQs, lead times, and shipping logistics for custom Oxford fabrics requires understanding the unique strengths and constraints of each production country. To summarize:
- China:
- MOQ: 500–1,000 m per color/finish.
- Lead Time: 30–40 days post-sample.
- Strengths: Lowest costs, robust finish palette, fastest sampling.
- Considerations: Rising labor costs, potential port congestion, evolving environmental regulations.
- India:
- MOQ: 1,000–1,500 m, larger batches.
- Lead Time: 45–60 days.
- Strengths: Vertical integration, strong textile heritage, cotton-blend expertise.
- Considerations: Variable power supply, slower finish innovation, port bottlenecks.
- Vietnam:
- MOQ: 800–1,200 m.
- Lead Time: 40–55 days.
- Strengths: Trade agreements (EU, CPTPP), modern finishing lines, competitive labor costs.
- Considerations: Limited finish variety, currency volatility.
- Turkey:
- MOQ: 1,200–2,000 m, premium positioning.
- Lead Time: 45–55 days.
- Strengths: EU‐compliant standards, proximity to European markets, efficient overland routes.
- Considerations: Higher per‐meter cost, elevated MOQs, seasonal demand spikes.
- Bangladesh & Pakistan:
- MOQ: 300–800 m (lower for simple specs).
- Lead Time: 45–60 days.
- Strengths: Low base fabric cost, potential for lower MOQs.
- Considerations: Port congestion, quality variance, slower sampling.
At SzoneierFabrics, we combine decades of R&D and manufacturing expertise with strategic production partnerships across Asia and Europe to bring you:
- Low MOQs & Flexible Color Splits (from 300 meters per color)
- Rapid Prototyping (lab dips in 7–10 days, small roll samples in 10–12 days)
- Competitive Pricing (600D PU from $3.80/m, 1200D PU from $5.20/m)
- Short Lead Times (bulk orders ready in 30–35 days from Chinese mills; 45–50 days from Turkey)
- Comprehensive Testing Reports (tensile, tear, Martindale, hydrostatic, OEKO‐TEX®, REACH)
- Customized Coating & Lamination Options (PU, PVC, TPU, DWR, UV, anti-mildew)
- Sustainability Focus (ZLD finishing, bluesign®‐approved processes)
Contact SzoneierFabrics today to discuss your precise spec, get immediate quotes across multiple countries, and secure the perfect balance of cost, MOQ, durability, and lead time for your next Oxford fabric order,
Whether you need a lightweight 600D PU Oxford for urban accessories or a heavy‐duty 1200D TPU‐laminated Oxford for rugged outdoor gear, we’ve got you covered. Let’s turn your custom fabric vision into reality—fast, affordably, and with 100% quality assurance.