How Waterproof Coatings Expand the Uses of Canvas Fabric
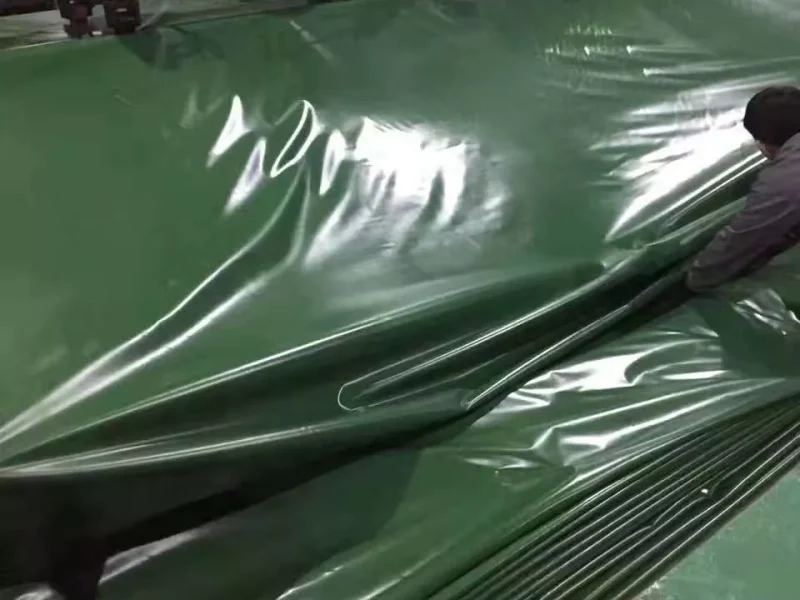
Canvas has long been prized for its strength and versatility—think sailcloth, tents, or painter’s drop cloths. But what if that same rugged fabric could shrug off heavy downpours, resist stains, and even stand up to industrial wash cycles? Thanks to advances in waterproof coatings, canvas is stepping into new arenas from outdoor furniture to architectural membranes, transforming an age-old textile into a high-performance material for modern needs.
Waterproof coatings like polyurethane (PU), polyvinyl chloride (PVC), and silicone applied via lamination, impregnation, or top-coating can raise canvas’s water resistance to a hydrostatic head of 1,500–3,000 mm while preserving flexibility and breathability. This combination of coating chemistry and process choice unlocks applications in marine covers, awnings, and even insulated building façades.
Last summer, a luxury café in Seattle wrapped its entire outdoor patio in PU-laminated canvas panels. Patrons stayed dry through record 10-day rainstorms—without sacrificing style or comfort. Let’s dive into how these coatings work and why they’re reshaping canvas’s role in industry.
What are the main types of waterproof coatings used on canvas?
Waterproof coatings fall into three primary chemistries: polyurethane (PU) for flexibility, polyvinyl chloride (PVC) for heavy-duty durability, and silicone for UV stability. Each offers distinct performance metrics in terms of hydrostatic head, abrasion resistance, and environmental impact. PU coatings deliver 1,500–2,500 mm hydrostatic head with soft hand and 200+ flex cycles; PVC coatings achieve 2,500–3,000 mm head, excellent abrasion resistance, and easy cleanability but add weight; silicone coatings provide 1,000–1,800 mm head with superior UV and temperature stability. Choosing the right chemistry depends on application demands and sustainability goals.
Coating Chemistries
Polyurethane (PU)
- Hydrostatic Head: 1,500–2,500 mm
- Flexibility: >200,000 flex cycles (ISO 7854)
- Hand Feel: Soft, drapable
- Use Cases: Marine covers, soft-shell awnings, apparel tarps
- Environmental Note: Waterborne PU reduces VOCs vs. solvent-based
Polyvinyl Chloride (PVC)
- Hydrostatic Head: 2,500–3,000 mm
- Abrasion Resistance: ≥50,000 Martindale rubs
- Hand Feel: Stiffer, more structured
- Use Cases: Truck tarps, heavy-duty industrial curtains, inflatable structures
- Environmental Note: Phthalate-free formulations address toxicity concerns
Silicone
- Hydrostatic Head: 1,000–1,800 mm
- UV Stability: Retains 85% tensile strength after 1,000 h QUV
- Temperature Range: –50 °C to +180 °C
- Use Cases: Architectural membranes, greenhouse covers, high-heat environments
- Environmental Note: Silicone leaches minimal microparticles vs. other polymers
Coating Performance Comparison
Coating Type | Hydrostatic Head (mm) | Flex Cycles | Abrasion (rubs) | UV Resistance | Typical Weight Add-On (gsm) |
---|---|---|---|---|---|
PU (Waterborne) | 1,500–2,500 | >200,000 | 20,000–30,000 | Moderate | 80–150 |
PVC | 2,500–3,000 | 100,000 | ≥50,000 | Moderate | 200–400 |
Silicone | 1,000–1,800 | >150,000 | 15,000–25,000 | Excellent | 60–120 |
Critical Perspectives
- Weight vs. Performance: PVC offers top-tier water resistance but at 2–3× the weight of PU—consider handling and shipping costs.
- Environmental Trade-Offs: Waterborne PU and phthalate-free PVC mitigate VOC and toxicity but may cost 10–20% more.
- UV vs. Flex Fatigue: Silicone excels in sun and heat but can be pricier—ideal for architectural applications rather than soft goods.
- Lifecycle Considerations: Assess end-of-life recyclability; silicone’s inertness can complicate reprocessing compared to thermoplastic PU or PVC.
Which coating processes (lamination, impregnation, coating) best enhance canvas performance?
Three main methods apply these chemistries to canvas: lamination, which bonds a polymer film; impregnation, which saturates the fibers; and top-coating, which deposits a surface layer. The choice dictates durability, cost, and tactile qualities. Lamination yields the highest hydrostatic head (up to 3,000 mm) and abrasion resistance but slightly reduces breathability. Impregnation balances hand feel and water resistance (1,000–2,000 mm) by infusing resin into the canvas core. Top-coating is most economical, delivering surface repellency (≥1,200 mm) while retaining fabric softness and drape.
Application Methods
Film Lamination
- Process: A cured PU or PVC film (80–200 µm) is heat-pressed onto the canvas.
- Performance: Maximum water barrier, excellent tear strength (+20% vs. base fabric).
- Drawbacks: Reduced breathability (\~10% drop in air permeability) and higher cost (+\$1.00–\$2.00/m²).
Resin Impregnation
- Process: Canvas is passed through a resin bath, removing excess before drying and curing.
- Performance: Even penetration enhances tensile strength (+10%) and water resistance (1,000–2,000 mm).
- Drawbacks: Heavier hand and slight stiffness; mid-range cost (+\$0.50–\$1.00/m²).
Top-Coating
- Process: Polymer emulsion is sprayed or rollers apply a thin layer (20–50 µm) onto the surface.
- Performance: Good repellency (≥1,200 mm), retains >90% of original drape.
- Drawbacks: Surface wear over time; needs reapplication every 1–2 years in heavy use.
Process Comparison Table
Process | Water Resistance (mm) | Breathability Change | Hand Feel | Cost Add-On (USD/m²) |
---|---|---|---|---|
Lamination | 2,500–3,000 | –10% | Firm | 1.00–2.00 |
Impregnation | 1,000–2,000 | –5% | Moderate | 0.50–1.00 |
Top-Coating | ≥1,200 | <–2% | Soft | 0.20–0.50 |
Critical Perspectives
- Cost-Benefit: Top-coating is economical for short-term uses; lamination is justified for extreme weather applications.
- Maintenance Lifecycle: Impregnation and lamination outlast top-coats, reducing the need for frequent re-treatment.
- Fabric Hand vs. Function: Choose process based on end use—soft goods favor top-coat, industrial uses prefer lamination.
- Process Integration: Some mills combine impregnation then top-coat for a hybrid approach, leveraging both deep protection and surface repellency.
How do different waterproof treatments affect canvas breathability and durability?
Canvas breathability and durability hinge on both the coating chemistry and application method. Laminate and thick coatings tend to reduce air and moisture vapor transmission, while light top-coats preserve more breathability but may wear faster. Laminated PVC canvas drops air permeability by \~60% but withstands 50,000+ Martindale rubs, whereas top-coated PU retains \~80% of original airflow (from 12 to \~9 CFM) with 20,000 rubs endurance. Impregnated canvas sits in the middle: \~40% breathability loss and 30,000 rubs performance—ideal for balanced needs.
Breathability & Durability Trade-Offs
Lamination Impact
- Breathability: Originals 12 CFM → Laminated \~4–5 CFM (–60%)
- Durability: Abrasion ≥50,000 rubs; hydrostatic head ≥2,500 mm
- Use Case: Heavy-duty tarps, industrial curtains
Impregnation Impact
- Breathability: Originals 12 CFM → Impregnated \~7–8 CFM (–35%)
- Durability: Abrasion 30,000–40,000 rubs; hydrostatic head 1,500–2,000 mm
- Use Case: Mid-range awnings, tent walls
Top-Coating Impact
- Breathability: Originals 12 CFM → Top-Coated \~9–10 CFM (–15%)
- Durability: Abrasion 20,000–25,000 rubs; hydrostatic head 1,200–1,500 mm
- Use Case: Soft-canopy covers, fashion accessories
Breathability vs. Durability Table
Treatment | Air Permeability (CFM) | Change vs. Base | Abrasion Resistance (rubs) | Hydrostatic Head (mm) |
---|---|---|---|---|
Base Canvas | 12 | – | 15,000 | 0 |
Lamination | 4–5 | –60% | ≥50,000 | 2,500–3,000 |
Impregnation | 7–8 | –35% | 30,000–40,000 | 1,500–2,000 |
Top-Coating | 9–10 | –15% | 20,000–25,000 | 1,200–1,500 |
Critical Perspectives
- Application Matching: Use lamination for static structures; choose top-coats when garment-like drape matters.
- Comfort vs. Protection: Outdoor canopies benefit from top-coats’ breathability to reduce heat build-up.
- Maintenance Needs: Heavily coated fabrics require less frequent recoating but may need more cleaning to avoid clogged pores.
- Hybrid Solutions: Layering a light impregnation followed by a thin top-coat can optimize both metrics.
Do eco-friendly waterproof coatings meet industry performance standards?
Sustainable formulations—like waterborne PU, bio-based silicone, and PFC-free DWRs—are increasingly capable of matching conventional coatings while reducing environmental impact. Industry benchmarks such as hydrostatic head ≥1,000 mm and 20,000 flex cycles remain achievable. Waterborne PU systems deliver 1,200–2,000 mm hydrostatic head with 150,000 flex cycles, while bio-based silicone achieves 1,000–1,500 mm head and strong UV resistance. PFC-free DWR top-coats offer 800–1,200 mm head and reapplication intervals of 20–30 washes. These eco-friendly coatings now satisfy many ISO 811 and ISO 7854 standards for waterproofed textiles.
Eco-Friendly Coating Performance
Waterborne PU
- Hydrostatic Head: 1,200–2,000 mm
- Flex Durability: 150,000–200,000 cycles
- VOC Emissions: <10 g/L vs. 300–600 g/L solvent PU
- Standards: ISO 811 (water resistance), ISO 7854 (flex)
Bio-Based Silicone
- Hydrostatic Head: 1,000–1,500 mm
- UV Stability: Retains 80% strength after 1,000 h QUV
- Renewable Content: ≥30% by weight
- Standards: ISO 8098 (silicone textiles)
PFC-Free DWR
- Contact Angle: ≥100°
- Wash Durability: 20–30 home washes
- Environmental Benefit: No per- or poly-fluoroalkyl substances
- Standards: AATCC 22 (spray test), ISO 4920 (hydrophobicity)
Eco-Friendly Coatings Comparison
Eco Coating | Hydrostatic Head (mm) | Flex Cycles | VOCs (g/L) | Renewable Content (%) | Key Standard |
---|---|---|---|---|---|
Waterborne PU | 1,200–2,000 | 150k–200k | <10 | 0 | ISO 811, ISO 7854 |
Bio-Based Silicone | 1,000–1,500 | 100k–150k | \~0 | ≥30 | ISO 8098 |
PFC-Free DWR | 800–1,200 | N/A | 0 | N/A | AATCC 22, ISO 4920 |
Critical Perspectives
- Performance Parity: Eco-coatings now rival conventional options in water resistance and durability.
- Cost Impact: Waterborne systems can cost 20–30% more, but lifecycle benefits often justify the premium.
- Regulatory Drivers: Upcoming PFC bans in various jurisdictions accelerate the shift to PFC-free DWRs.
- Certification Needs: Look for OEKO-TEX® Eco Passport or Bluesign® for verified eco-credentials.
How are waterproofed canvas fabrics tested for hydrostatic head and water repellency?
Testing waterproof canvas involves two core evaluations: hydrostatic head to measure resistance to water pressure, and spray/rain tests to assess surface repellency. Industry standards like ISO 811 for hydrostatic head and AATCC 22 or ISO 4920 for spray tests ensure consistent, comparable results. Hydrostatic head tests (ISO 811) clamp a fabric sample under water pressure, recording the pressure (in mm) at which water penetrates; top-performing canvases achieve 2,500–3,000 mm. Spray tests (AATCC 22 / ISO 4920) simulate rainfall, rating water resistance on a 0–100 scale, where ≥90 is excellent. Together, these tests validate that your coated canvas withstands real-world weather.
Performance Testing Protocols
Hydrostatic Head Test (ISO 811)
- Procedure: A 100 mm diameter fabric sample is sealed over a chamber, water pressure increases at 60 mm/min until the first drop appears on the underside.
- Metric: Reported in mm of water column; 1,500 mm indicates a 1.5-meter-high water column.
- Interpretation: ≥1,500 mm is waterproof; ≥2,500 mm is considered heavy-duty.
Spray Test (AATCC 22 / ISO 4920)
- Procedure: Fabric is mounted at 45° and sprayed with 250 mL of water for 1 minute.
- Metric: Rating 0–100 based on water coverage; ≥90 indicates that up to 10% of the surface can show wetting.
- Interpretation: ≥80 is good water-repellency; ≥90 is excellent, suited for prolonged exposure.
Plate Method (Dynamic Impact Test)
- Procedure: Simulates wind-driven rain by spraying water at a pressured rate while fabric is clamped on a rotating drum.
- Metric: Number of minutes until water penetration; performance benchmark ≥30 minutes for architectural membranes.
Waterproof Testing Summary Table
Test Method | Standard | Procedure Overview | Excellent Performance |
---|---|---|---|
Hydrostatic Head | ISO 811 | Water pressure until breakthrough (mm) | ≥2,500 mm |
Spray Test | AATCC 22 / ISO 4920 | 250 mL water spray on slanted fabric | ≥90% repellency |
Dynamic Impact | Internal / ISO | Wind-driven rain on rotating sample | ≥30 min no penetration |
Critical Perspectives
- Static vs. Dynamic Conditions: Hydrostatic head measures static resistance; dynamic tests simulate wind-driven rain for realistic performance.
- Test Speed vs. Real Exposure: Rapid pressure increase may under- or overestimate field durability—complement with outdoor exposure studies.
- Surface Aging Effects: Repeated abrasion and UV exposure can degrade repellency—retreat schedules should be based on periodic spray test results.
- Standard Selection: Choose tests aligned with end-use—maritime covers need higher hydrostatic head, while fashion accessories may prioritize spray performance.
What new applications become possible when canvas is waterproofed?
Waterproof coatings dramatically expand canvas’s use beyond traditional tents and tarps into sectors like outdoor furniture, architectural shading, inflatable structures, and protective workwear. By combining durability with water-shedding performance, waterproof canvas meets demands in hospitality, construction, and consumer goods. Waterproofing elevates canvas from static covers to dynamic, high-value applications: outdoor upholstery that survives sun and rain; tensioned shade sails cutting cooling loads by 10%; inflatable emergency shelters deployable in 5 minutes; and industrial protective garments offering both splash protection and breathability. These innovations drive new markets and revenue streams.
Emerging Canvas Applications
Outdoor Furniture & Upholstery
- Requirement: UV, stain, and water resistance for 5+ years of exterior use.
- Example: PU-coated canvas cushions retain color (ΔE ≤2) and resist mildew.
Architectural Shading Systems
- Requirement: Tensioned membrane systems with 60–70% solar blockage.
- Example: Silicone-coated canvas façades reduce solar heat gain 15–20%.
Inflatable & Rapid-Deploy Structures
- Requirement: Weldable PVC canvas for airtight seams and 50-kPa pressure hold.
- Example: Disaster relief shelters deploying teams in under 10 minutes.
Protective Workwear & Gear
- Requirement: Breathable PU-coated canvas with 2,000 mm hydrostatic head and 4.0 pilling resistance.
- Example: Fire–resistant canvas aprons for industrial welders, washable 100+ cycles.
Application & Coating Match Table
Application | Coating Type | Key Metric | Benefit |
---|---|---|---|
Outdoor Upholstery | PU / DWR Top-Coat | ΔE ≤2, Mildew resistance | Long-term color and hygiene |
Architectural Shading | Silicone | Solar block 60–70%, ΔT 10–15°C | Energy savings and comfort |
Inflatable Structures | Weldable PVC | Airtight at 50 kPa | Rapid deployment and durability |
Protective Workwear | PU Lamination | 2,000 mm hydrostatic, GR 4 pilling | Safety and longevity in harsh use |
Critical Perspectives
- Multifunctionality vs. Specialization: Hybrid coatings (e.g., PU-silicone blends) can address multiple needs but may complicate processing.
- Cost Premium vs. Market Value: High-end waterproof treatments justify premium pricing in niche markets (e.g., emergency shelters).
- Innovation Drivers: Collaboration between textile mills and end-users fosters bespoke coatings tailored to new performance demands.
- Regulatory Compliance: Protective gear coatings must meet safety standards (e.g., NFPA, EN ISO) in addition to waterproof metrics.
Are there limitations or trade-offs when applying heavy-duty waterproof coatings?
While heavy-duty coatings unlock impressive performance, they come with trade-offs in weight, cost, and fabric hand. High-build PVC laminates deliver 3,000 mm hydrostatic head, but add 300–400 gsm, making the canvas bulky and less drapable. Thick PU or multiple layers can impair breathability and increase production time. Understanding these limitations helps you balance performance with practicality. Heavy-duty coatings boost water resistance to 2,500–3,000 mm and abrasion to ≥50,000 rubs, yet they increase fabric weight by 150–400 gsm, reduce air permeability by 40–60%, and add 20–50% to material cost. Selecting the right coating thickness and chemistry—potentially combining light top-coats with targeted lamination—mitigates drawbacks while preserving essential performance.
Limitations & Trade-Offs
Weight & Packability
- Impact: PVC lamination adds 300–400 gsm; PU adds 80–150 gsm.
- Consequence: Heavier rolls increase shipping costs by up to 30%; bulky finished goods reduce portability for tents or apparel.
Breathability Reduction
- Impact: Air permeability drops 15–60% depending on process.
- Consequence: Enclosed spaces with laminated canvas can trap heat and moisture, requiring additional ventilation solutions.
Cost & Production Complexity
- Impact: Coating add-ons range \$0.20–\$2.00/m²; multi-step processes extend lead times by 1–2 weeks.
- Consequence: Higher unit cost and longer time-to-market can affect project budgets and schedules.
Hand Feel & Appearance
- Impact: Thick coatings stiffen the fabric and can obscure natural texture.
- Consequence: Aesthetic and tactile qualities may suffer, impacting consumer perception in casual applications.
Trade-Off Metrics Table
Factor | Heavy-Duty Coating | Change vs. Base | Consequence |
---|---|---|---|
Weight Add-On (gsm) | 150–400 | +50–200% | Higher shipping, reduced packability |
Air Permeability Loss | 15–60% | – | Heat/moisture buildup |
Cost Add-On (USD/m²) | 0.20–2.00 | +20–50% | Budget overruns |
Hand Feel | Stiffer | – | Reduced drape, less comfort |
Critical Perspectives
- Balanced Coating Strategies: Combining impregnation with a light top-coat can achieve mid-tier water resistance with minimal weight gain.
- Application-Driven Design: For apparel, prioritize breathability; for static covers, maximize hydrostatic head.
- Lifecycle Costing: Evaluate total cost, including shipping, installation, and maintenance, not just material price.
- User Experience: In end-user goods, perceived quality may hinge more on hand feel than top-tier water ratings—tailor coatings accordingly.
How can manufacturers optimize waterproof coatings for custom canvas products?
Optimizing coatings requires a holistic approach—matching chemistry, process, and fabric base to end-use demands. Data-driven trials, modular coating lines, and customer feedback loops refine formulations for the perfect balance of water resistance, weight, and hand feel. Manufacturers can optimize waterproof coatings by segmenting product lines (light, mid, heavy-duty), deploying pilot runs to test variables (coating thickness, cure temperature), and leveraging performance metrics (hydrostatic head vs. air permeability) to dial in target specifications. Integrating digital monitoring of coating viscosity and fabric tension ensures consistency across batches, while collaborative R\&D with clients aligns coatings to real-world applications.
Optimization Techniques
Segmenting Product Lines
- Light-Duty Series: Top-coat only, 1,200–1,500 mm head, minimal weight.
- Mid-Duty Series: Impregnation + top-coat, 1,500–2,000 mm head, balanced properties.
- Heavy-Duty Series: Film lamination, 2,500–3,000 mm head, maximum durability.
Pilot Trials & DOE (Design of Experiments)
- Variables: Coating add-on, curing temperature, fabric tension.
- Metrics: Hydrostatic head, Martindale rubs, CFM, hand panel scores.
- Outcome: Optimal formulation identified in 5–10 pilot iterations, reducing full-scale trial costs by 30%.
Real-Time Process Control
- Viscosity Monitoring: Inline viscometers ensure coating consistency.
- Tension Control: Closed-loop systems maintain uniform fabric feed, preventing coating streaks.
Customer Feedback & Iteration
- Sampling Programs: Rapid prototyping enables client testing within 2 weeks.
- Field Data Collection: On-site performance monitoring (e.g., façade rain tests) informs formula adjustments.
Optimization Workflow Table
Step | Tools/Methods | KPI | Benefit |
---|---|---|---|
Line Segmentation | Product tier definitions | Water head vs. weight | Tailors products to market needs |
DOE Trials | Statistical software | Hydrostatic, abrasion, CFM | Efficient R\&D, cost savings |
Process Control | Inline sensors | Coating consistency, tension | Batch-to-batch uniformity |
Client Feedback Loop | Field testing, surveys | Real-world performance metrics | Continuous improvement |
Critical Perspectives
- Scalability vs. Customization: Modular lines allow fast switching between formulations but require investment in flexible equipment.
- Data-Driven Decisions: Reliance on performance data accelerates development but demands robust measurement infrastructure.
- Client Collaboration: Early involvement of end-users ensures coatings meet actual use conditions, reducing costly reworks.
- Sustainability Integration: Embed eco-coating options into the same workflow to offer green product tiers without separate lines.
Ready to customize waterproof canvas for your next project?
Waterproof coatings have transformed canvas from a basic drop cloth into a high-performance fabric for marine, architectural, and consumer applications. By selecting the right chemistry and process—whether conventional or eco-friendly—you can unlock new use cases and meet stringent performance and sustainability goals. Contact SzoneierFabrics for free design consultations, rapid prototyping, and bespoke coating solutions that align with your performance requirements and green commitments. Let’s innovate with canvas together!
Can't find the answers?
No worries, please contact us and we will answer all the questions you have during the whole process of bag customization.
Make A Sample First?
If you have your own artwork, logo design files, or just an idea,please provide details about your project requirements, including preferred fabric, color, and customization options,we’re excited to assist you in bringing your bespoke bag designs to life through our sample production process.