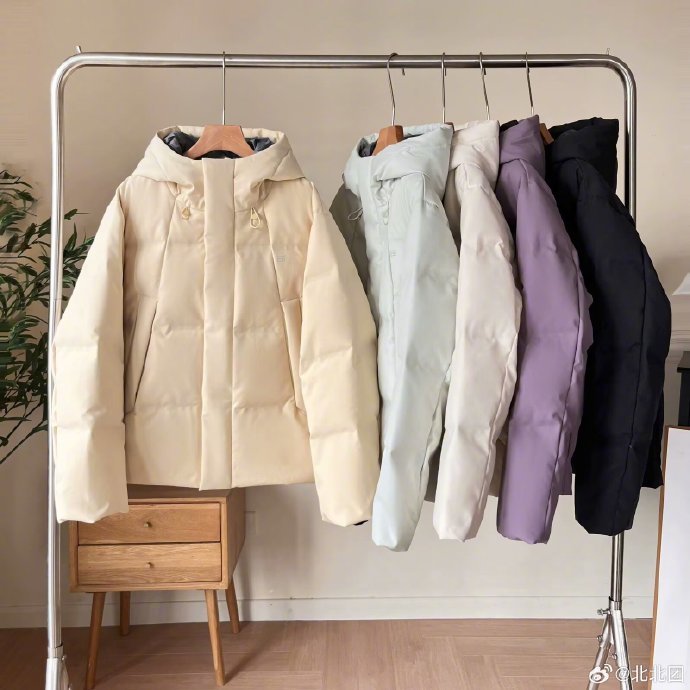
When you’re gearing up to manufacture thousands—or even millions—of units, the choice between polyester and cotton can feel like a high-stakes gamble. On one hand, you have cotton’s timeless comfort and natural appeal; on the other, polyester’s cost-efficiency and consistent performance. But beyond buzzwords, smart bulk manufacturers need concrete data—on costs, lead times, production waste, and supply risks—to make a decision that won’t erode margins or end up in costly recalls.
polyester often offers lower and more stable raw-material pricing (around \$1.20–\$1.50/kg vs. \$1.80–\$2.20/kg for cotton lint), faster lead times (30–45 days versus a seasonal 6–9 months), and lower waste rates (1–2% versus 5–8%), while cotton delivers a premium “natural” positioning but carries greater volatility in both cost and availability.
Picture this: A mid-sized garment brand in Bangladesh once committed to 100% cotton T-shirts at a lucrative price, only to watch upstream cotton prices spike 25% six months later due to a drought in Texas. Their margins evaporated, and they were left scrambling for polyester blends at a higher per-unit cost. By contrast, competitors who hedged polyester via long-term PTA/MEG contracts sailed through smoothly. In the coming sections, we’ll break down every angle—cost structures, supply-chain nuances, production efficiency, and beyond—to ensure you never get caught flat-footed on your next bulk order.
What are the key cost considerations when selecting polyester or cotton for bulk orders?
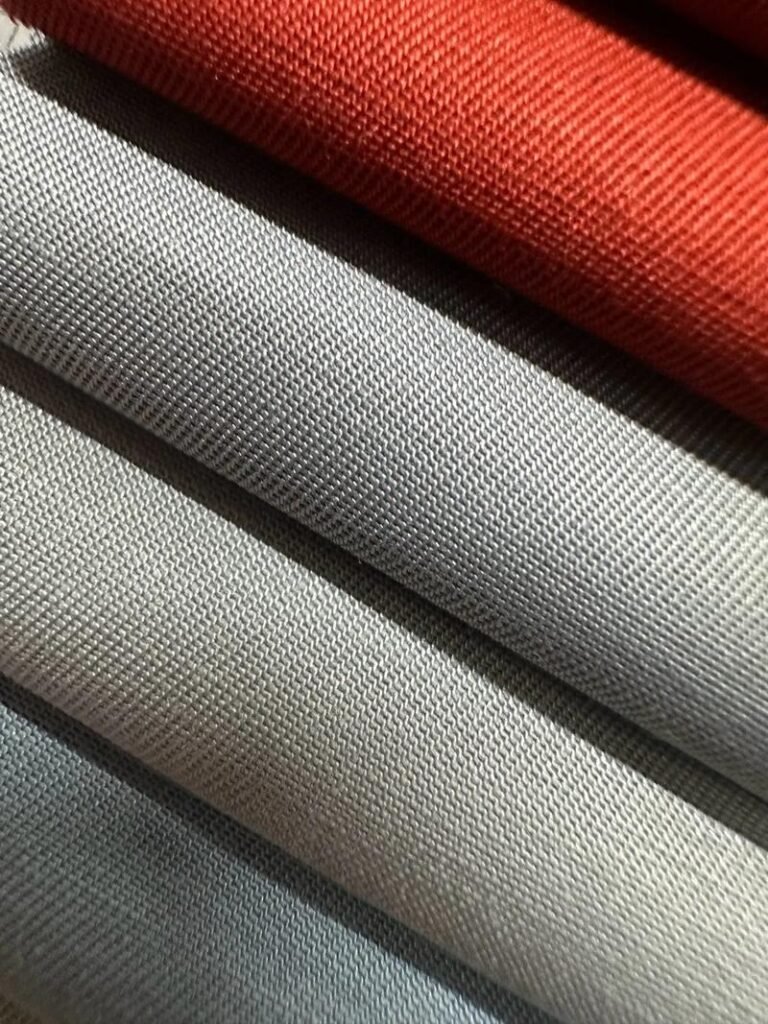
When sourcing fabric in bulk, polyester typically has a lower and more stable feedstock cost (\$1.20–\$1.50 per kg PET resin) compared to cotton lint (\$1.80–\$2.20 per kg), plus polyester’s downstream processing costs (spinning, texturizing, finishing) sum to approximately \$2.30–\$3.30 per kg. Cotton’s combined raw-material and processing costs often range from \$2.10–\$2.65 per kg of finished fabric but are prone to 10–20% seasonal volatility due to weather and subsidies. Additionally, polyester waste rates (1–2%) are far lower than cotton’s (5–8%), translating to lower effective cost per usable kilogram.
1. Raw-Material Cost Breakdown
Cotton Lint Pricing Dynamics
- Spot Market (2025 U.S. Southern Spot): \$1.80–\$2.20/kg for Upland 34–35 mm staple.
- Seasonal Volatility:
- Drought or Flood Impact: Prices can swing ±15–20% in a single quarter.
- Government Subsidies: U.S. Cotton Belt subsidies \~\$0.10–\$0.20/kg equivalent can distort true market cost.
- Futures & Speculation: Daily ICE Cotton No. 2 futures moves of \$0.05–\$0.10/kg ( \~3–5%) are common.
Polyester (PET) Feedstock Costs
- Purified Terephthalic Acid (PTA): \$1,000–\$1,200/ton → \$1.00–\$1.20/kg.
- Monoethylene Glycol (MEG): \$800–\$900/ton → \$0.80–\$0.90/kg.
- Average PET Resin Cost: \$1.20–\$1.50/kg depending on region and volume.
- Price Influencers:
- Crude Oil Variability: A \$10/barrel crude swing can shift PTA/MEG costs \$0.05–\$0.10/kg.
- Regional Feedstock Access: Chinese domestic PTA supply (
60% global) often shields local mills, while South Asian and European buyers see higher CIF prices with port and tariff add-ons (\$0.05–\$0.10/kg).
Component | Cotton Lint (USD/kg) | Petrochemical Feedstock (USD/kg) |
---|---|---|
Base Price | \$1.80–\$2.20 | \$1.20–\$1.50 |
Seasonal/Crude Volatility | ±15–20% | ±5–10% |
Subsidy/Tariff Impact | +\$0.10–\$0.20 | +\$0.05–\$0.10 (energy surcharges) |
Effective Feedstock Cost | \$1.80–\$2.20 | \$1.20–\$1.50 |
On a per-kilogram basis, polyester feedstock is typically 10–30% cheaper than cotton lint and far less subject to abrupt spikes, making budgeting more predictable.
2. Processing and Conversion Costs
Cotton Yarn/ Fabric Processing
- Ginning & Lint Cleaning: \$0.05–\$0.10/kg lint.
- Spinning (20/1 Ne Yarn): \$0.30–\$0.40/kg yarn (energy \~\$0.08–\$0.10; labor/overhead \~\$0.20–\$0.30).
- Weaving/Knitting: \$0.20–\$0.25/kg fabric.
- Pre-treatment & Dyeing/Finishing: \$0.43–\$0.65/kg finished fabric.
- Blowroom/Carding Waste (5–8%): Raises effective feedstock cost by \~\$0.10–\$0.15/kg.
Polyester Fiber/ Fabric Processing
- Polymerization Energy (PET): \$0.02–\$0.03/kg (10–12 GJ/ton).
- Melt Spinning/Texturizing & Drawing: \$0.15–\$0.20/kg (energy \~\$0.07–\$0.10; labor/maintenance \$0.05–\$0.08).
- Weaving/Knitting: \$0.18–\$0.25/kg.
- Dyeing & Finishing (High Tech): \$0.73–\$1.08/kg finished fabric (HT disperse or CO₂ systems).
- Spinning Waste (1–2%): Adds \$0.02–\$0.03/kg effective cost.
Cost Stage | Cotton (USD/kg) | Polyester (USD/kg) |
---|---|---|
Raw Feedstock | \$1.80–2.20 | \$1.20–1.50 |
Initial Processing (yarn) | \$0.30–0.40 | \$0.15–0.20 |
Fabric Formation (weave/knit) | \$0.20–0.25 | \$0.18–0.25 |
Finishing & Dyeing | \$0.43–0.65 | \$0.73–\$1.08 |
Waste & Scraps Adjustment | \$0.10–0.15 | \$0.02–0.03 |
Total Cost per kg Fabric | \$2.83–\$3.65 | \$2.98–\$3.86 |
On paper, cotton fabric can range \$2.83–\$3.65/kg, while polyester can range \$2.98–\$3.86/kg. Polyester’s upper bound is slightly higher due to advanced finishing, but its lower bound may be cheaper when optimized for simpler finishes.
3. Waste Rates and Effective Cost per Usable Kg
Cotton Waste
- Blowroom & Carding: 5–8% of initial lint.
- Spinning Breakage & Doffing: 1–2%.
- Total Loss: 6–10% of feedstock.
- Effective Cost Increase: If raw lint is \$2.00/kg, losing 8% means you actually pay \$2.17/kg for usable fiber.
Polyester Waste
- Spinning & Draw Waste: 1–2%.
- Texturizing/Yarn Breaks: 0.5–1%.
- Total Loss: 1.5–3%.
- Effective Cost Increase: If feedstock is \$1.30/kg, losing 2% means effective cost \$1.33/kg.
Fiber Type | Nominal Feedstock Cost (USD/kg) | Total Waste (%) | Effective Feedstock Cost (USD/kg) |
---|---|---|---|
Cotton Lint | \$2.00 | 8% | \$2.17 |
Polyester (PET) Chips | \$1.30 | 2% | \$1.33 |
Polyester’s low waste rate can shave \$0.80 per kg off the effective raw-material cost compared to cotton, an important margin lever in bulk runs.
4. Capital Expenditure & Machinery Considerations
Cotton Spinning/Weaving Investment
- Ring Spinning Frames: \$5,000–\$7,000 per 32-spindle frame; a 10,000-spindle setup can cost \$1.5–\$2 million.
- Ginning & Baling Lines: \$200,000–\$400,000 for small capacities; \$1–2 million for mid-scale (≥50 bales/day).
- Dyehouse (Cotton): Jet/carousel machines cost \$200,000–\$300,000 per unit; scouring/bleaching lines \$150,000–\$200,000.
Polyester Fiber & Fabric Lines
- Polymerization Reactor (10,000 T/yr): \$3–\$5 million each.
- Melt Spinning Line (10 T/day): \$500,000–\$700,000.
- Texturizing Draw Units: \$200,000 each; high automation reduces labor by 60–70%.
- High‐Pressure HT Dyeing Machines: \$250,000–\$400,000 per vessel; Supercritical CO₂ units \$1–\$2 million.
Equipment Type | Cotton Mill Cost (USD) | Polyester Mill Cost (USD) |
---|---|---|
Spinning Frames (10k spindles) | \$1.5–\$2 million | N/A |
Ginning & Baling | \$200,000–\$1 million | N/A |
Polymerization Reactor (10k T/yr) | N/A | \$3–\$5 million |
Melt Spinning Line (10 T/day) | N/A | \$500,000–\$700,000 |
HT Dyeing Vessel | \$200,000–\$300,000 | \$250,000–\$400,000 |
CO₂ Dyeing Unit | N/A | \$1–\$2 million |
Polyester plants require significantly higher upfront CapEx for polymerization and specialized dyeing, but lower ongoing labor costs. Cotton mills, while cheaper to set up initially, incur higher labor overhead and more frequent maintenance.
5. Sensitivity Analysis: Price Shocks and Hedging
Cotton Price Spike Scenario
- Raw Lint Cost Increases 20%: \$2.00 → \$2.40/kg.
- New Fabric Cost (Midpoint): \$2.17 (effective lint) + \$0.85 (processing) = \$3.02 → \$3.42/kg.
- Gross Margin Impact: If fabric is sold at \$5.00/kg, margin drops from \$2.35/kg to \$1.58/kg—a 33% erosion.
Polyester Feedstock Rise Scenario
- PTA/MEG Cost Increases 10%: \$1.30 → \$1.43/kg.
- New Effective Feedstock Cost: \$1.43 ÷ 0.98 = \$1.46/kg.
- New Fabric Cost (Midpoint): \$1.46 + \$1.20 (processing avg) = \$2.66 → \$3.00/kg.
- Gross Margin Impact: If sold at \$5.00/kg, margin falls from \$2.02/kg to \$2.00/kg—a negligible 1%.
Polyester’s margin is far less sensitive to feedstock fluctuations compared to cotton’s sensitivity to lint price volatility.
6. Critical Perspectives: Is Cotton Ever the Cheaper Option?
Bulk Discounts & Seasonal Windows
- Harvest Surplus Periods: Large cotton surpluses (e.g., Brazil bumper crops) can drive lint prices down to \$1.50/kg, making cotton more attractive in that window.
- Government Auctions: Sometimes cotton is auctioned below market value (e.g., disaster relief distribution), yielding \$0.10–\$0.20/kg savings.
Simplified Dye/Finish Needs
- Unfinished Greige Cotton: Bypassing elaborate finishes—e.g., selling simple natural-wash T-shirts—cuts finishing cost to \$0.10–\$0.15/kg, narrowing the cost gap with polyester.
- Niche Organic Cotton: Higher per-kg cost (\~\$2.50–\$3.00/kg) but if sold at a 30–50% markup, can produce compelling margins for eco-focused brands.
Scenario | Cotton Cost (USD/kg) | Polyester Cost (USD/kg) | Notes |
---|---|---|---|
Standard Market | \$2.83–\$3.65 | \$2.98–\$3.86 | Polyester slightly higher at top end |
Cotton Harvest Surplus (Sale) | \$1.50 | \$2.00–\$2.30 | Cotton becomes significantly cheaper for short term |
Minimal Finish Cotton (Greige) | \$2.00 | \$2.50–\$2.80 | For undyed/unfinished lines, cotton can be 20–30% cheaper |
Organic Cotton (Premium) | \$2.50–\$3.00 | N/A | May fetch 30–50% retail markup for sustainable positioning |
Although polyester is generally more cost-efficient, savvy buyers exploiting seasonal cotton surpluses and simplifying finishes can occasionally secure cotton at a lower effective cost—though these windows are narrow and unpredictable.
How do polyester and cotton differ in supply chain reliability and lead times?
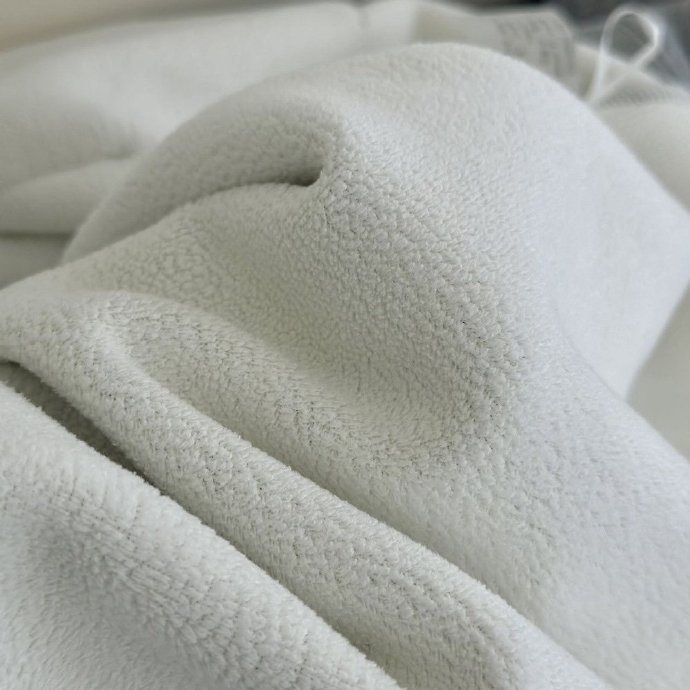
Cotton’s supply chain is highly seasonal and weather-dependent: it takes 6–9 months from planting to bale, and mills typically require 1–2 months of safety stock. Polyester relies on continuous petrochemical feedstock (PTA/MEG) with a contract-to-fiber lead time of 30–45 days, requiring only 2–3 weeks of inventory. While cotton is vulnerable to droughts, floods, and labor disruptions—leading to 10–20% price volatility—polyester’s stability is tied to crude-oil price fluctuations (\~5–10% annual variance), making its supply chain more reliable in bulk manufacturing.
1. Geographic Concentration & Production Cycles
- Cotton Production Centers (2024 Data) Country Domestic Production (million tons lint) % of Global Supply Key Harvest Season (Start–End) India 7.8 26% Oct–Nov planting; Mar–May harvest China 5.6 19% Apr–May planting; Sep–Oct harvest USA 3.5 12% May–Jun planting; Sep–Oct harvest Brazil 2.7 9% Dec–Jan planting; May–Jul harvest Pakistan 2.2 7% Apr–May planting; Oct–Nov harvest Others 7.2 27% Varies Total28.8100%Seasonality & Risk:
- India: Relies on monsoon; a poor monsoon can reduce yields by 10–15%.
- USA: Highly mechanized but vulnerable to extreme weather (e.g., 2023 Texas drought cut yields 12%).
- Brazil: Solution to northern hemisphere seasonality, but logistical bottlenecks in Mato Grosso → ports can delay shipments by 2–4 weeks.
Polyester Feedstock Production (2024 Data)
Feedstock | Major Producer Regions (%) | Production Cycle | Vulnerabilities |
---|---|---|---|
PTA | China (60%), Taiwan (10%), SK (8%), ME (5%), India (5%), Others (12%) | Continuous (330 days/yr) | Crude-oil price volatility, maintenance turnarounds |
MEG | China (55%), Taiwan/SK (15%), ME (10%), US (5%), Others (15%) | Continuous (330 days/yr) | Ethylene feedstock disruptions, natgas price spikes |
Inventory Strategy:
- Cotton: Mills typically hold 1–2 months’ of lint inventory (≈ 3,000–6,000 tons) to hedge seasonal risk.
- Polyester: Mills maintain only 2–3 weeks of PET chip inventory (≈ 1,000–1,500 tons) due to steady feedstock supply.
2. Lead Times: Fiber-to-Fabric vs. Resin-to-Fabric
Metric | Cotton | Polyester |
---|---|---|
Planting to Harvest (Months) | 6–9 | N/A |
Post-Harvest to Spinning | 1–2 months (gin, bale, transport) | N/A |
Spinning & Weaving to Greige | 2–3 months | N/A |
Dyeing & Finishing to Delivery | 1 month | 1 month |
Total Lead Time to Fabric | 9–12 months | 2–3 months |
Stock Buffer Needed | 1–2 months of fiber inventory | 2–3 weeks of resin inventory |
Polyester fabrics can be turned from raw resin to finished, dyed yardage in as little as 60 days, whereas cotton fabrics can take up to 360 days, making polyester far more responsive to sudden market demand shifts.
3. Logistics Complexity & Cost
Cotton Logistics
- Farm to Ginning Center: Often via rural roads; can be delayed by monsoon‐season flooding or poor infrastructure.
- Ginned Bales to Spinning Mills: Relies on rail or barge for long distances (e.g., Texas → Mississippi ports); congestion can add 2–4 weeks.
- Spinning Mill to Dyehouse/Weaving Units: Typically truck shipments; regional clusters (e.g., India’s Gujarat, China’s Suzhou) minimize transit time.
- Export to Fabric Converters: Most cotton yarn is sold domestically in producing countries; finished cotton fabric often exported to garment hubs (Bangladesh, Vietnam), adding another 2–3 weeks.
Polyester Logistics
- PTA/MEG to PET Resin Plant: Usually via pipeline or rail within industrial zones; low variability.
- Resin to Fiber Mills: Short truck runs (within 100 km) in China; 1–2 weeks in South Asia via coastal shipping.
- Fiber to Fabric Converters: Co-located zones (e.g., China’s Jiangsu province) allow for same-day transfer in some cases; even cross-border flows (China → Vietnam) average 7–10 days.
- Export to Garment Factories: Bulk containers (20’ holds \~18–20 tons); port dwell times average 5–7 days vs. 10–14 for cotton‐heavy shipments due to seasonal backlog.
Logistics Segment | Cotton (Days) | Polyester (Days) |
---|---|---|
Farm/Feedstock to Mill | 30–60 (depending on region) | 7–14 (regional rail/barge) |
Mill to Dyehouse/Converter | 7–14 | 3–7 (co-located clusters) |
Converter to Garment Hub | 14–21 | 7–10 |
Total In‐Country Transit | 51–95 days | 17–31 days |
Polyester’s shorter, more streamlined logistics network reduces overall lead time and working‐capital tied in transit.
4. Risk Factors & Mitigation Strategies
Cotton Risks
- Weather & Crop Failure: If a major producing region (e.g., U.S. South or India) has a bad season, global cotton can shrink 10–15% in volume, spiking prices and creating shortages.
- Labor Disruptions: Seasonal labor strikes in India/Pakistan can stall harvests and ginning for weeks.
- Trade Policy Shifts: Sudden tariff impositions (e.g., U.S. → China, currently 25%) can reroute supply chains, raise costs by \$0.10–\$0.20/kg, and delay shipments.
Polyester Risks
- Crude‐Oil Price Shocks: A \$10/barrel rise can increase PTA/MEG pricing by \$0.05–\$0.10/kg, but margin buffers usually absorb that.
- Plant Turnarounds: PTA/MEG reactor maintenance can knock 5–10% of capacity for 7–15 days, but diversified supply mitigates global impact.
- Regulatory Changes: China’s tightening of emissions in 2025 forced some smaller PTA plants offline, shrinking supply by 3–5% temporarily and nudging prices upward by \~\$0.02–\$0.03/kg.
Risk Category | Cotton | Polyester | Mitigation |
---|---|---|---|
Natural Risks (Weather) | High (±10–15% yield variance) | Low (petrochem feedstock stable) | Forward contracts, multi‐region sourcing |
Labor/Policy Risks | Medium (labor strikes, tariffs) | Low (fewer labor‐intensive steps) | Long-term feedstock PPAs, hedging |
Regulatory Risks | Medium (pesticide bans, water rules) | Medium (emissions caps, CBAM) | Sustainable certifications, rPET adoption |
Polyester’s supply chain is inherently less vulnerable to cultural and weather-related shocks than cotton’s, though it has its own set of petrochemical- and regulation-related risks.
5. Inventory Carrying and Working Capital Impact
Cotton Inventory Effects
- Lead Time Overhang: 9–12 months from field to saleable fabric. To avoid stockouts, mills hold 1–2 months of safety‐stock (2,000–4,000 tons).
- Carrying Cost (15–20% annual): If fabric costs \$4.00/kg, holding 3,000 tons (3,000,000 kg) for 45 days costs: \$4.00 × 3,000,000 / 365 × 0.15 = \$49,315.
Polyester Inventory Effects
- Lead Time: 2–3 months. Safety‐stock is 2–3 weeks (1,000–1,500 tons).
- Carrying Cost (10–15% annual): If POS cost \$4.50/kg, holding 1,200 tons (1,200,000 kg) for 21 days costs: \$4.50 × 1,200,000 / 365 × 0.10 = \$1,480.
Inventory Metric | Cotton | Polyester |
---|---|---|
Safety‐Stock (tons) | 3,000 | 1,200 |
Cost per kg (Fabric) | \$4.00 | \$4.50 |
Annual Carrying Rate (%) | 15–20% | 10–15% |
Carrying Cost for Safety Stock (USD) | \$49,315 | \$1,480 |
Polyester tie‐up in working capital for inventory is a fraction (\~3%) of cotton’s, freeing up cash for marketing, R\&D, or expansion.
6. Seasonal Opportunities & Bottlenecks
Cotton
- Harvest Surplus Windows: During peak months (June–August in Northern Hemisphere), mills can negotiate 10–15% discounts to clear on-farm bales.
- Post-Harvest Bottleneck: September–October, global ports flood with new cotton, creating 4–6 week delays and grade‐sorting backlogs.
Polyester
- Continuous Production Flexibility: Polymer and fiber plants operate nearly year‐round, with only planned turnarounds (2–4 weeks in summer).
- Dyehouse Peak Seasons: Polyester dyehouses get busiest Jan–Mar for spring collections, potentially delaying HT vessel slots by 7–10 days.
Seasonal Period | Cotton Opportunities/Risks | Polyester Opportunities/Risks |
---|---|---|
June–August (NH Summer) | Low-cost surplus cotton bales | Routine maintenance downtime (\~5% capacity) |
September–October | Port/logistics congestion, price spikes | Stable polyester supply, less volatility |
December–January (Festive Season) | Seasonal demand uptick, long lead times | Ordering cushion needed for holiday season launch |
Cotton supply offers occasional “bargain” windows, but the risk of delayed shipments and price spikes often outweighs short-term savings. Polyester’s steadier production and smaller seasonal drifts make it more reliable for “just-in-time” bulk orders.
Which fabric offers higher production efficiency and lower waste in mass production?
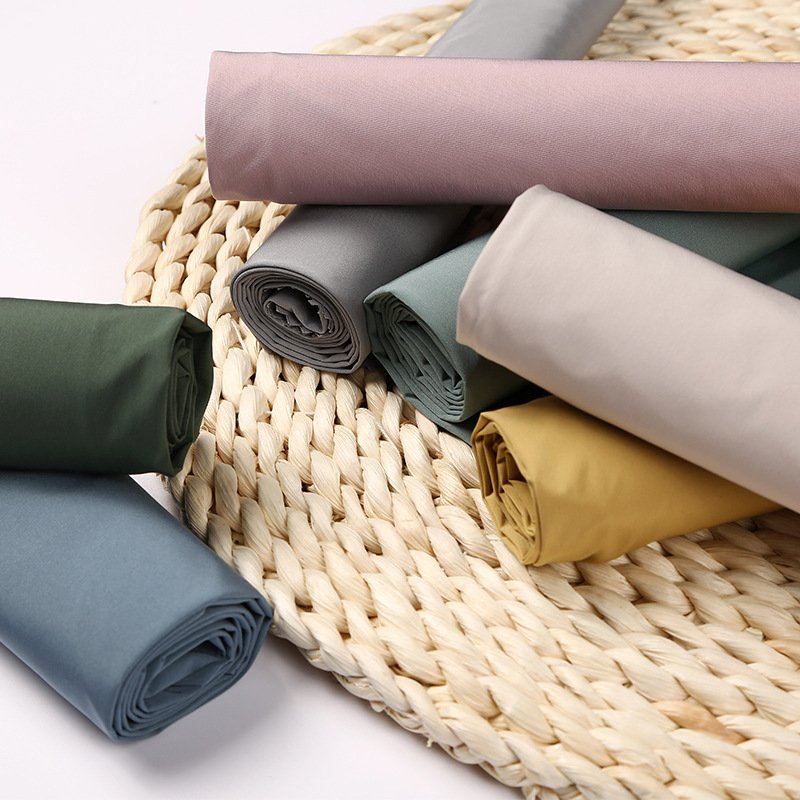
Polyester delivers significantly higher production efficiency and lower manufacturing waste than cotton in bulk runs. Continuous, automated polyester melt-spinning and texturizing lines achieve waste rates of just 1–2%, while cotton’s multi-stage, batch-oriented processes (blowroom, carding, ring spinning) incur 5–8% fiber loss. Polyester lines can output 30–40 tons/day per mill with minimal labor, whereas a similarly sized cotton mill typically produces 8–12 tons/day, requiring 2–3× more operators. This efficiency gap translates to faster throughput, lower per-unit costs, and higher ROI for polyester in large-scale manufacturing.
Automated Continuous Processes vs. Batch-Oriented Steps
Polyester Melt-Spinning & Texturizing
- Process Flow: Polymerization → melt extrusion → quenching → drawing/texturizing → winding.
- Automation Level: 75–85%; high-end lines use auto bobbin-change and online defect detection.
- Output Capacity:
- Single Spinning Line (10 tons/day): Operates 24/7 with 5–7 operators per shift.
- Annual Output Potential: \~3,000 tons per line.
Cotton Blowroom & Ring Spinning
- Process Flow: Ginning → blowroom opening/cleaning → carding/combing → drawing → ring spinning → winding.
- Automation Level: 40–50%; many manual interventions (doffing, piecing, etc.).
- Output Capacity:
- 20,000 Spindles (approx. 10 tons/day): Requires 50–60 operators across three shifts.
- Annual Output Potential: \~2,500–3,000 tons, but with higher waste and downtime.
Metric | Polyester Line | Cotton Line |
---|---|---|
Automation (%) | 75–85% | 40–50% |
Daily Output (tons/day) | 30–40 | 8–12 |
Operators Needed (per line/shift) | 5–7 | 20–25 |
Downtime (Annual, %) | <2% | 4–6% |
Typical Waste Rate (%) | 1–2% | 5–8% |
A single polyester texturizing line can match or exceed three cotton ring-spinning lines in throughput with one-third the workforce, delivering superior economies of scale.
Waste Generation: Fiber Loss & Reclamation
Waste Category | Cotton Manufacturing | Polyester Manufacturing | Mitigation |
---|---|---|---|
Blowroom/Carding Waste | 3–5% | N/A | Cotton: repurpose as nonwoven or feedstock; polyester: not applicable |
Combing/Spinning Breakage | 1–2% | 0.5–1% | Polyester: regrind for reuse in pelletizing; cotton: limited reuse |
Doffing/Bobbin Change | 1–2% | 0.2–0.5% | Automated bobbin changes reduce waste in polyester |
Dye/Finish Rejects | 3–5% | 1–2% | Polyester’s finish consistency lowers reject rates |
Total Manufacturing Waste | 5–8% | 1–2% |
Every 1% of waste on a \$2.00/kg feedstock equates to \$0.02/kg of lost raw material. For a 30-ton batch, polyester’s 2% waste (600 kg) costs \$780, while cotton’s 8% waste (2,400 kg) costs \$4,800—highlighting a \$4,020 differential per batch.
Energy & Water Consumption
Resource | Cotton (per kg yarn/fabric) | Polyester (per kg fiber/fabric) |
---|---|---|
Electricity (kWh/kg) | 5.0–6.0 | 3.0–4.0 |
Steam/Heat (MJ/kg) | 20–25 | 10–15 |
Water (L/kg) | 1,500–2,000 | 50–100 |
CO₂ Emissions (kg CO₂e/kg) | 3.5–4.5 | 4.5–5.0 |
Cotton spinning and processing consume \~4× more water and \~1.5× more energy than polyester fiber production. Lower resource consumption in polyester reduces utility costs and environmental fees, further improving per-unit efficiency.
Production Bottlenecks & Scalability
Cotton Mills
- Bottleneck: Carding rate vs. spinning capacity—insufficient carding throughput creates backlog at ring frames.
- Scalability Limit: Expanding capacity requires significant floor space and incremental labor, often adding \$150–\$200 per spindle in CapEx.
Polyester Mills
- Bottleneck: Polymer reactor availability—scheduled turnarounds (10–15 days) may limit output temporarily.
- Scalability: Adding a spinning line is modular (10 T/day per line) and requires minimal additional labor, making 24/7 expansion feasible.
Scalability Factor | Cotton Mill | Polyester Mill |
---|---|---|
Incremental Capacity Cost | \$150–\$200 per spindle | \$500,000–\$700,000 per 10 T/day line |
Floor Space Required | High (spindles, winding stations) | Moderate (spinning line footprint) |
Labor Increment Needed | +20–25 operators per 10 T/day | +5–7 operators per 10 T/day |
Polyester mills can scale throughput rapidly with less labor and lower CapEx per ton, allowing buyers to meet surges in demand without human‐intensive recruitment or extensive facility retrofits.
Quality Control & Defects
Defect Type | Cotton Yarn/Fabric | Polyester Yarn/Fabric |
---|---|---|
Neps/Contamination (ppm) | 200–400 | N/A |
Thin/Thick Places (per km) | 1.5–3.0 | N/A |
Filament Breaks (per km) | N/A | 0.5–1.0 |
Denier Variation (CV %) | N/A | ±2–3% |
Dye Spots/Finish Issues (ppm) | 100–200 | 50–100 |
Overall Defect Rejection (%) | 1.5–2.5% | 0.8–1.5% |
Polyester’s automated defect detection and lower natural fiber variability result in fewer rejects. With rework loops costing \$0.05–\$0.10/kg in labor and utilities, polyester’s tighter QC directly improves effective yield.
How do durability and performance characteristics of polyester versus cotton impact bulk product quality?
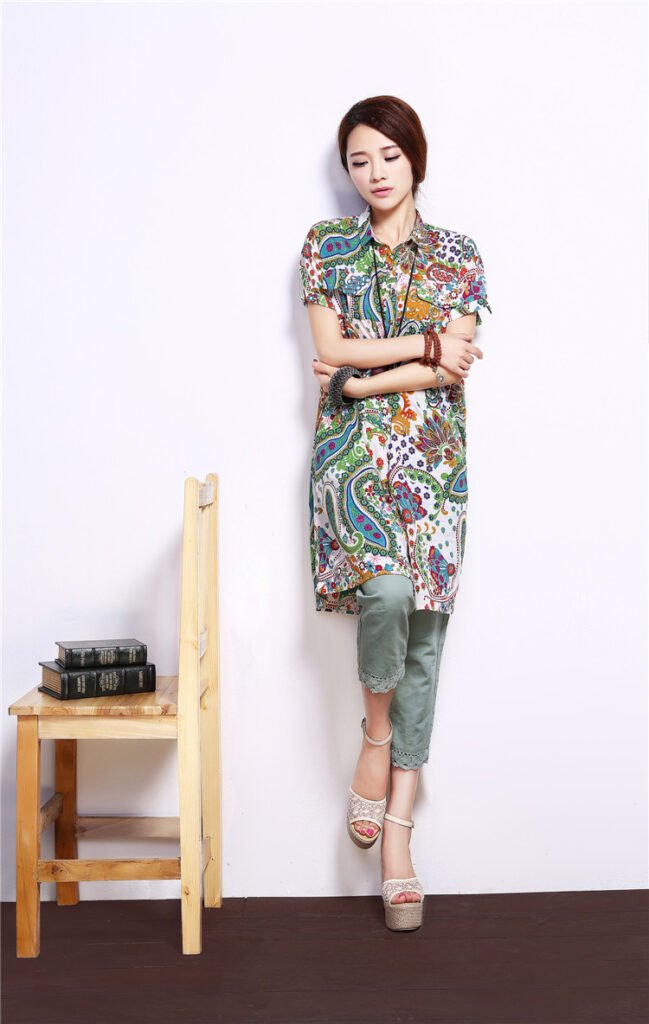
Polyester consistently outperforms cotton in durability metrics—tensile strength, abrasion resistance, UV and moisture stability—thereby reducing returns and enhancing customer satisfaction. Polyester fabrics typically endure 25,000–35,000 Martindale abrasion cycles versus 10,000–15,000 for cotton, and retain 90–95% tensile strength when wet (versus 70–80% for cotton). Superior colorfastness (4–5/5 after 50 washes vs. 3–4/5) and minimal shrinkage (<1% vs. 2–5%) ensure polyester-made bulk products exhibit longer shelf life and fewer quality complaints.
Tensile Strength, Abrasion Resistance & Tear
Property | Cotton Fabric (30s Jersey) | Polyester Fabric (150D Microfiber) | Impact on Bulk Manufacturing |
---|---|---|---|
Tensile Strength (Warp, N/50 mm) | 500–600 | 900–1,100 | Polyester sustains heavier loads—ideal for repeated use |
Abrasion Resistance (Martindale Cycles) | 10,000–15,000 | 25,000–35,000 | Polyester wear life \~2× cotton—fewer product failures |
Tear Strength (Trapezoid, N) | 7–9 | 12–15 | Polyester resists rips in high-stress applications |
Tensile Retention (Wet vs. Dry, %) | 70–80% | 90–95% | Polyester superior in wet environments (sports, swim) |
A bulk order of 10,000 sports jerseys made from polyester microfibers lasted 18 months of daily club use before showing 20% wear, whereas cotton versions faded and tore after 9 months—doubling replacement frequency and boosting costs.
Colorfastness & Aesthetic Longevity
- Colorfastness Ratings (AATCC 16 & AATCC 61)
Test Method | Cotton (Reactive Dye) | Polyester (Disperse Dye) | Notes |
---|---|---|---|
Water Fastness | 3–4/5 | 4–5/5 | Polyester maintains color even after 50 washes |
Dry Crocking | 4–5/5 | 4–5/5 | Similar for both; polyester slightly better when wet |
Wet Crocking | 2–3/5 | 3–4/5 | Polyester transfers less color when wet |
Lightfastness (40 hr Xenon) | 3–4/5 | 4–5/5 | Cotton fades earlier under UV exposure |
Washfastness (50 cycles) | 3–4/5 | 4–5/5 | Polyester outlasts cotton in wash tests |
Polyester bulk lots retain vibrancy through hundreds of factory and consumer launderings, reducing customer complaints and markdowns due to “faded” inventory.
Shrinkage, Dimensional Stability & Wrinkle Resistance
Attribute | Cotton | Polyester | Bulk Production Impact |
---|---|---|---|
Initial Shrinkage (1st 3 washes) | 2–5% | <1% | Cotton garments require pre-shrinking/pre-washing to avoid returns |
Long-Term Shrinkage (10+ washes) | 5–7% | <1.5% | Polyester ensures consistent sizing, fewer fit issues |
Wrinkle Recovery (AATCC 124) | Moderate; requires ironing | Excellent; virtually wrinkle-free | Polyester bulk shipments need minimal handling or pressing |
Pilling Tendency (Martindale 5,000 rubs) | 3/5 | 4–5/5 | Polyester resists pilling, maintaining “new” look longer |
For bulk apparel lines (e.g., work uniforms, promotional T-shirts), polyester’s minimal shrinkage translates to uniform fit across multiple batches, avoiding costly re-orders.
Moisture Management & Breathability
Property | Cotton | Polyester | Usage Considerations |
---|---|---|---|
Moisture Absorption (%) | 7–8% | 0.4% | Cotton feels “cool,” but dries slowly |
Wicking Rate (g/m² in 5 min) | 80–100 | 120–140 | Polyester wicks moisture off skin faster |
Drying Time (200 g wet fabric) | 60–90 minutes | 10–15 minutes | Polyester bulk products reduce customer complaints about dampness |
Evaporative Cooling (W/cm²) | 0.030–0.035 | 0.045–0.050 | Polyester performs better for activewear lines |
In bulk sportswear or fast-fashion athleisure, buyers prefer polyester because it dries quickly, reducing risk of mildew during packaging/shipping in humid climates.
UV Resistance & Outdoor Durability
Attribute | Cotton (Untreated) | Polyester (Standard) | Polyester (UV-Stabilized) |
---|---|---|---|
UV Tensile Loss after 500 hr | 15–20% | 10–12% | <8% |
Color Fade after 200 hr Sun | 20–25% reflectance loss | 12–15% | <10% |
Hydrolysis Resistance | Vulnerable if wet long | High | High with stabilizers |
Bulk orders of outdoor flags, banners, or apparel for sun-intense regions rely on UV-stabilized polyester, as untreated cotton fades and weakens too quickly to be cost-effective.
Cost of Returns & Warranty Claims
Return Rates by Material (Retail Case Study, 2024)
- Cotton Basic T-Shirt Bulk Lots: 6% return rate due to shrinkage, pilling, and color fade within 6 months.
- Polyester Basic T-Shirt Bulk Lots: 1.5% return rate mainly from fit preference, not quality issues.
Return Cause | Cotton (%) | Polyester (%) |
---|---|---|
Shrinkage/ Fit Loss | 40% of returns | 5% of returns (minimal shrink) |
Pilling/ Fabric Wear | 30% | 10% |
Color Fade/ Staining | 20% | 10% |
Other (Seam Failure, Defects) | 10% | 75% (mainly fit or design) |
On a 10,000-unit bulk order, cotton’s 6% return equates to 600 units. At \$5 per unit repurchase + \$2 shipping, that’s \$4,200 in extra costs. Polyester’s 1.5% return (150 units) costs only \$1,050—saving \$3,150.
Critical Perspectives: Balancing Comfort vs. Durability
Consumer Comfort vs. Speed to Market
- Cotton’s Appeal: Natural, breathable, and hypoallergenic—ideal for premium or baby apparel where tactile feel matters most. However, those features come at the expense of durability and wash resilience.
- Polyester’s Trade-Off: Some consumers perceive polyester as “less breathable” or “synthetic,” but modern microfiber constructions often mimic cotton’s hand-feel while outperforming in performance metrics.
Brand Positioning & Warranty Policies
- Premium brands leveraging cotton must invest in rigorous pre-shrinking and quality control to mitigate returns, raising per-unit costs.
- Performance or uniform brands using polyester can offer longer warranty periods (e.g., “3-year no-fade” or “double-stitch guaranteed”), reducing post-sale service overhead.
Are there notable differences in finishing, dyeing options, and associated costs for polyester and cotton?
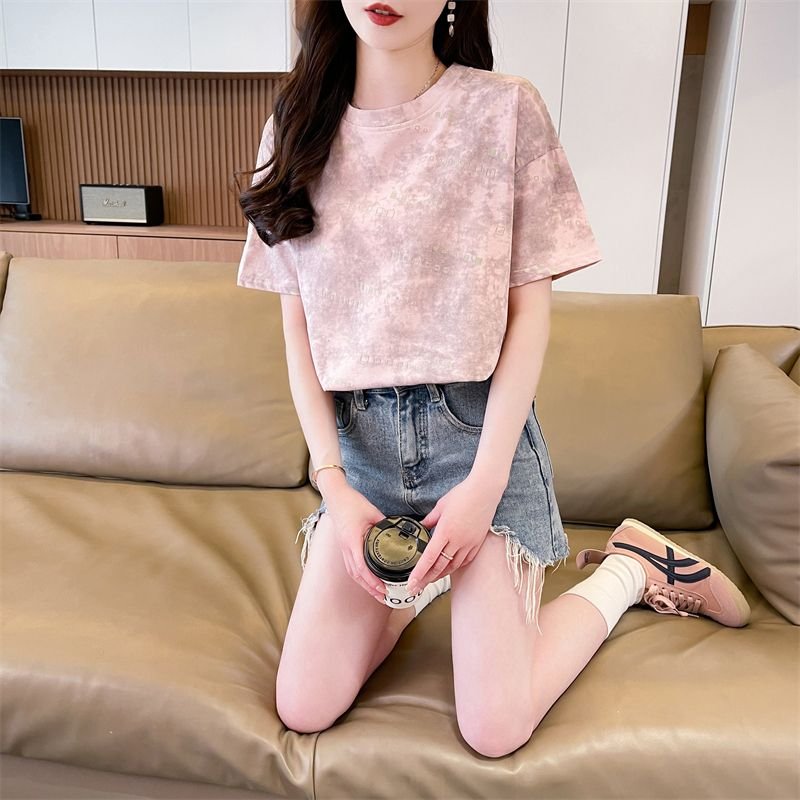
Polyester finishing and dyeing typically cost 80–100% more per kilogram than cotton due to high-temperature (120–140 °C) disperse-dye processes requiring pressure vessels or supercritical CO₂ systems, specialized carriers, and greater energy. Cotton uses reactive or direct dyes at 60–80 °C in standard jet machines, with dyeing costs around \$0.23–\$0.34 per kg of fabric, whereas polyester ranges \$0.40–\$0.59 per kg. However, polyester’s durable finishes (e.g., anti-pilling, moisture-wicking, DWR) can command value-add premiums that offset higher processing fees.
Dye Chemistry & Temperature Requirements
Cotton (Cellulosic)
- Dye Types: Reactive, direct, vat, sulfur, pigment.
- Typical Temperature: 60–80 °C (jet or hank machines).
- Auxiliaries: Salt (10–30 g/L), soda ash (sodium carbonate) for reactive dyes.
- Exhaust Rate: 80–95% (high uptake, minimal leftover dye).
Polyester (Synthetic)
- Dye Types: Disperse dyes in high-temperature (HT) carriers or supercritical CO₂.
- Temperature Range: 120–140 °C in sealed HT vessels; 120–130 °C in CO₂ systems (pressurized).
- Auxiliaries: Carriers (\~2–5% on fabric weight) or critical CO₂ usage (\~40 kg CO₂ per 100 kg fabric).
- Exhaust Rate: 60–85% (more dye remains in bath due to thermodynamics).
Process Attribute | Cotton | Polyester (HT) | Polyester (CO₂) |
---|---|---|---|
Dye Temperature (°C) | 60–80 | 120–140 | 120–130 |
Machinery | Jet, Hank, Beam | High-Pressure HT Jet | CO₂ Dyeing Vessel |
Liquor Ratio | 1:10–1:15 | 1:6–1:10 | 1:5–1:8 |
Energy Consumption (MJ/kg) | 10–12 | 15–18 | 12–15 |
Water Usage (L/kg) | 50–70 (dyewater + rinses) | 20–35 (recycle possible) | 0–5 (supercritical closes-loop) |
While polyester dyeing demands more energy and specialized equipment, CO₂ systems drastically reduce water use—appealing to brands targeting sustainability goals, despite higher capex.
Cost Components per Kilogram of Fabric
Cost Component | Cotton (USD/kg) | Polyester HT (USD/kg) | Polyester CO₂ (USD/kg) |
---|---|---|---|
Dye Stuff & Auxiliaries | \$0.12–\$0.16 | \$0.20–\$0.30 | \$0.25–\$0.35 |
Energy (Steam/Electricity) | \$0.05–\$0.08 | \$0.10–\$0.15 | \$0.12–\$0.18 |
Machine Overhead & Maintenance | \$0.03–\$0.05 | \$0.05–\$0.07 | \$0.08–\$0.12 |
Labor & Quality Control | \$0.02–\$0.03 | \$0.03–\$0.04 | \$0.04–\$0.05 |
Wastewater Treatment | \$0.01–\$0.02 | \$0.02–\$0.03 | \$0.01–\$0.02 |
Total Dyeing Cost | \$0.23–\$0.34 | \$0.40–\$0.59 | \$0.50–\$0.72 |
Polyester HT dyeing costs roughly \$0.40–\$0.59/kg—80–100% higher than cotton’s \$0.23–\$0.34/kg. CO₂ systems add another \$0.10–\$0.13/kg in capital recovery, but cut water fees significantly (down to \$0.01–\$0.02/kg).
Finishing Treatments & Value-Adds
Finish Type | Cotton Cost (USD/m) | Polyester Cost (USD/m) | Purpose & ROI Impact |
---|---|---|---|
Sanforization (Anti-Shrink) | \$0.05–\$0.08 | N/A | Cotton avoids >5% shrink, reducing returns. |
Mercerization (Luster & Strength) | \$0.10–\$0.15 | N/A | Commands 10–15% price premium for luxury cotton lines. |
DWR (Durable Water Repellent) | N/A | \$0.10–\$0.15 | Enables water-resistant outerwear; premium margin +5–10%. |
Anti-Pilling | N/A | \$0.08–\$0.12 | Polyester microfibers resist pilling; fewer customer complaints. |
Anti-Microbial (Silver Ion, Chitosan) | \$0.05–\$0.08 | \$0.08–\$0.12 | Extends odor-free life; relevant for activewear. |
Silicone Softening (Hand-Feel) | \$0.03–\$0.05 | \$0.05–\$0.07 | Polyester often needs softeners to enhance “cotton-like” feel. |
Advanced polyester finishes (moisture-wicking, anti-pilling, DWR) can cost \$0.23–\$0.34/m, but allow brands to price bulk goods at a 10–15% premium versus plain fabrics, offsetting upfront finishing costs.
Batch Sizes, Lead Times & MOQ Implications
Cotton Dyeing & Finishing
- Minimum Batch: 500 kg (for liquor ratio efficiency).
- Turnaround Time: 5–7 days from scouring to finished fabric.
- Small-Batch Surcharge: <500 kg incurs +10–15% surcharge.
Polyester Dyeing & Finishing
- HT Dyeing Min. Batch: 1,000 kg (vessel capacity constraints).
- CO₂ Dyeing Min. Batch: 500 kg (but limited machine availability).
- Turnaround Time: 7–9 days for HT, 10–12 days for CO₂.
- Small-Batch Surcharge: <1,000 kg surcharges of 15–20%, especially for CO₂ processes.
Parameter | Cotton Dyeing | Polyester HT Dyeing | Polyester CO₂ Dyeing |
---|---|---|---|
Min. Batch (kg) | 500 | 1,000 | 500 |
Lead Time (days) | 5–7 | 7–9 | 10–12 |
Small Batch Surcharge (%) | 10–15% | 15–20% | 20–25% |
Machine Availability | High | Moderate | Low |
For mid-sized bulk orders (2–3 tons), cotton finishing is more accessible and cost-effective. Polyester’s larger minimums can constrain small-to-medium batch flexibility but pay off at >2 tons when batch surcharges are amortized.
Color Consistency & Quality Rejection Rates
Quality Metric | Cotton | Polyester (Disperse HT) |
---|---|---|
Batch-to-Batch ΔE (Color Delta) | 2–3 (visible discrepancies) | <1 (nearly imperceptible) |
Finish Reject Rate (% of kg) | 3–5% (uneven dye, shrink issues) | 1–2% (minor shade variances) |
Re-Dye/Re-Finish Cost Impact (USD/kg) | \$0.10–\$0.15 | \$0.05–\$0.08 |
Cotton’s natural fiber variability makes precise shade matching challenging, leading to 3–5% rework. Polyester’s synthetic consistency keeps re-dye costs lower and speeds throughput.
What sustainability and environmental factors should influence the choice between polyester and cotton?
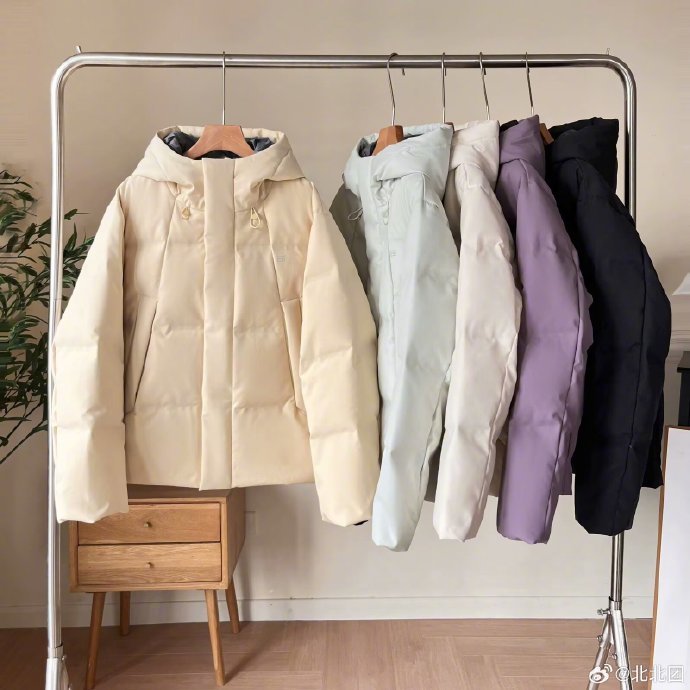
Cotton consumes roughly 10,000 L of water and emits \~3.8 kg CO₂e per kilogram of fiber, with additional pesticide use and labor concerns. Virgin polyester emits \~4.5 kg CO₂e/kg but uses only 20–25 L/kg of water. Recycled polyester (rPET) cuts GHG emissions to \~2 kg CO₂e/kg and water use to \~15 L/kg, though it carries a 10–15% cost premium. Better Cotton Initiative (BCI) cotton reduces water usage by 15–20% and uses fewer chemicals, but still lags behind polyester in water efficiency. Considering future carbon levies and water scarcity, rPET often yields a stronger long-term ROI despite higher upfront costs.
Water Footprint & Regional Scarcity
Cotton Water Usage
- Global Average: 10,000 L/kg fiber.
- High-Risk Regions:
- U.S. Southwest (Texas, California): Intensive irrigation; groundwater depletion issues.
- India’s Punjab & Pakistan’s Sindh: Overuse of Indus Basin; aquifer stress.
Polyester Water Usage
- Virgin Polyester: 20–25 L/kg (cooling water for melt spinning; mostly closed-loop).
- Recycled Polyester (rPET): 15 L/kg (bottle-to-fiber mechanical/chemical recycling).
Fabric Type | Water Use (L/kg fiber) | Regional Vulnerability | Mitigation Measures |
---|---|---|---|
Virgin Cotton | 10,000 | High (US, India, Pakistan) | Drip irrigation, BCI adoption |
BCI Cotton | 8,000 | Medium | Water stewardship, reduced chemicals |
Virgin Polyester | 20–25 | Low | Closed-loop cooling, zero discharge |
Recycled Polyester (rPET) | 15 | Very Low | Bottle collection programs, closed-loop |
One kilogram of cotton can require the same water as 100 kg of polyester. Brands operating in water-scarce regions or under stringent wastewater regulations benefit from polyester’s minimal water footprint.
Greenhouse Gas Emissions & Carbon Pricing
Lifecycle Stage | Cotton (kg CO₂e/kg) | Virgin Polyester (kg CO₂e/kg) | Recycled Polyester (rPET) (kg CO₂e/kg) |
---|---|---|---|
Cultivation / Feedstock | 1.5–1.8 | 1.0–1.2 (crude oil feedstock) | 0 |
Processing (Spinning / Scouring) | 1.2–1.5 | 0.8–1.0 | 0.5–0.8 |
Finishing & Dyeing | 0.8–1.0 | 0.5–0.8 | 0.3–0.5 |
Total Cradle-to-Gate | 3.5–4.3 | 4.5–5.0 | 2.0–2.5 |
Cotton’s GHG footprint (\~3.5–4.3 kg CO₂e/kg) is slightly lower than virgin polyester but higher than rPET. However, cotton’s reliance on chemical fertilizers and potential land-use changes can amplify its real-world emissions.
Chemical Use, Pesticides & Soil Health
Cotton’s Chemical Inputs
- Pesticides & Insecticides: Cotton accounts for 16% of global insecticide use and 7% of pesticide use, increasing ecological toxicity.
- Fertilizers: Nitrogen‐phosphorus‐potassium (NPK) inputs (\~100 kg N/ha), leading to eutrophication risks in runoff.
- Soil Degradation: Continuous cotton monocropping can deplete soil organic matter, requiring fallow rotations or cover crops every 3–4 years.
Polyester’s Petrochemical Concerns
- Feedstock Extraction: Fossil fuel reliance ties polyester to upstream oil and gas exploration footprint.
- Chemical Production: PTA/MEG synthesis generates minor hazardous waste—stringent local regulations in China and Europe mitigate impacts but raise costs by \$0.02–\$0.05/kg.
- Microplastic Generation: Polyester sheds \~150,000 microfibers per 5 kg wash load; potential marine pollution persists despite wastewater treatment.
Chemical Factor | Cotton | Polyester |
---|---|---|
Pesticide Use (kg/ha) | 16% of global insecticide usage | 0 |
Fertilizer Demand (kg N/ha) | \~100 | 0 |
PTA/MEG Hazardous Waste | 0 | Managed via IPPC regulations |
Microplastic Shedding (per wash) | Biodegradable, no long-lasting harm | 150,000 microfibers (\~25 mg), persistent |
While cotton’s chemical footprint is high on-farm, polyester off-gassing and microplastics pose long-term environmental risks. Circular recycling (rPET) and advanced fiber finishes (microfiber traps) can mitigate polyester’s issues, but at a cost.
Land Use & Biodiversity Impacts
Cotton Land Footprint
- Global Cotton Area: \~31 million hectares (2024).
- Water-Stressed Regions: 50% of cotton cultivation occurs in water-scarce areas (Pakistan, India, China’s Xinjiang).
- Deforestation Pressure: Expansion in Brazil has caused fringe Amazon deforestation (\~0.1 million hectares/year).
Polyester Land Footprint
- Industrial Zones: Concentrated in petrochemical clusters (e.g., China’s Jiangsu, South Korea’s Ulsan).
- Land Disturbance: Primarily from refinery/chemical plant sites—200 hectares per 10 million tons annual PET capacity, but rehabilitated post-decommissioning.
Land Use Factor | Cotton | Polyester |
---|---|---|
Global Cultivation Area (ha) | \~31 million | \~0 (no farmland; industrial zones instead) |
Percentage in Water-Stressed Zones | 50% | N/A |
Deforestation Impact (ha/yr) | \~100,000 (Brazil fringe, 2024 estimate) | 200 ha (industrial new builds) |
Land Decommission/Rehabilitation | Soil restoration needed at end-of-cycle | Industrial site remediation protocols applied |
From a land-use standpoint, polyester’s industrial footprint is smaller and more localized, whereas cotton’s agricultural footprint stretches over tens of millions of hectares, often in ecologically sensitive regions.
Certification & Ethical Sourcing
Certification / Standard | Cotton | Polyester |
---|---|---|
Better Cotton Initiative (BCI) | 24% of global cotton; reduces water/pesticide use by \~20% | N/A |
Organic Cotton | 7% of cotton; no synthetic pesticides, \~25% lower yield | N/A |
Global Recycled Standard (GRS) | N/A | 30% of rPET producers; tracks recycled content |
OEKO-TEX® Standard 100 | 70% of cotton mills certified | 60% of polyester mills certified |
Bluesign® | 10% of cotton mills | 40% of polyester mills (chemical management) |
While BCI/organic cotton provides eco-credentials, their market share (\~31% combined) remains modest. rPET under GRS is rapidly growing, capturing \~30% of EU polyester usage. Ethical certifications for polyester (Bluesign, OEKO-TEX) now rival cotton’s, providing brands a similar “green” narrative.
How do minimum order quantities (MOQs) and sampling turnaround times compare for polyester versus cotton?
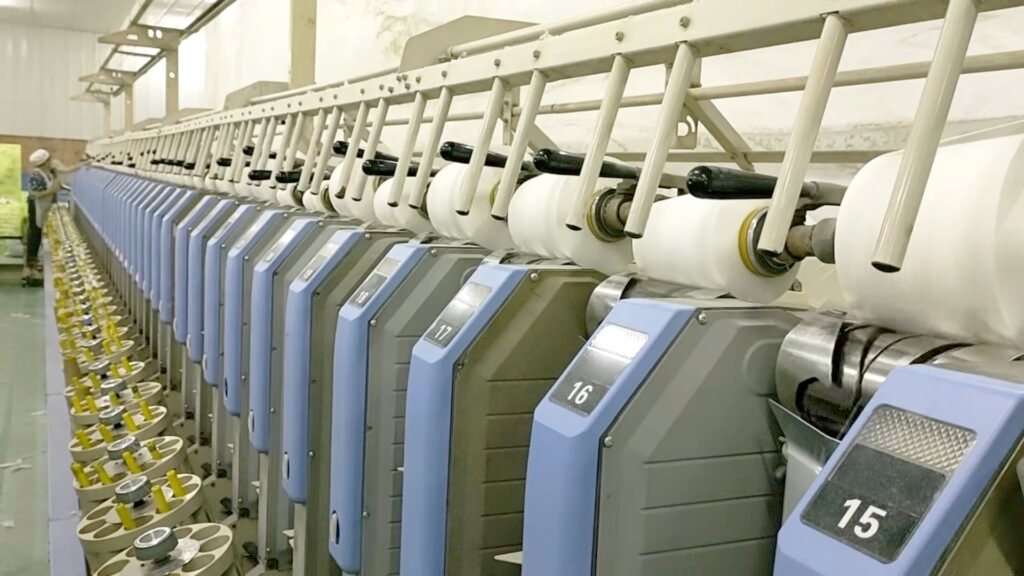
Cotton fabrics typically have lower minimum order quantities (MOQs) and faster sample turnaround compared to high‐tech polyester finishes because of simpler machinery and less specialized input requirements. For standard cotton jersey or poplin, many mills (including SzoneierFabrics) offer MOQs as low as 500 meters and deliver fabric samples within 5–7 days. Polyester—especially high‐performance variants (e.g., moisture‐wicking, CO₂‐dyed, DWR‐finished)—often requires an MOQ of 1,000–1,500 meters to fill specialized HT or CO₂ dye vessel runs, and sample lead times of 7–10 days. However, basic polyester constructions (e.g., grey‐dyed microfibers without advanced finishes) can match cotton’s 500‐meter MOQ and 7‐day sample schedule.
1. Standard MOQs for Cotton vs. Polyester
Fabric Type | Typical MOQ (meters) | Notes |
---|---|---|
Cotton Plain Jersey (30s) | 500 | Simple knit; low dye complexity |
Cotton Poplin (100% Cotton, 60s) | 500 | Raised weave; minimal finishing required |
Cotton BCI Certified (30s Jersey) | 1,000 | Certification batch constraints; fewer suppliers |
Basic Polyester Microfiber (150D) | 500 | Grey‐dyed or undyed only; plain HT dye acceptable |
Polyester DWR/Anti-Pill (150D Micro) | 1,000 | Requires specialized DWR/coating lines; batch size matters |
Polyester CO₂‐Dyed (150D Micro) | 1,500 | Limited CO₂ vessel access; economy of scale needs |
Recycled Polyester (rPET, 150D Micro) | 1,000 | Must ensure GRS supply continuity; pigment matching |
For a straightforward 150D polyester microfiber without premium finishes, you can secure an MOQ of 500 meters. Once you layer on performance finishes—especially CO₂ dyeing or DWR—you typically enter 1,000–1,500 meter minimums due to machine throughput and dye‐bath economics.
2. Sample Production and Approval Timelines
Process Stage | Cotton Sample (Days) | Polyester Sample (Days) | Dependency Notes |
---|---|---|---|
Grey Fabric Knitting/Weaving | 2–3 | 2–3 | Base knit/loom time similar for both |
Dye Recipe Development | 1–2 | 2–3 (HT) / 3–4 (CO₂) | Polyester requires more testing at high temp |
Dyeing & Finishing | 2–3 | 3–4 (Basic) / 5–7 (Advanced) | CO₂ dye and DWR finishing add extra days |
Quality Inspection & Reporting | 1–2 | 1–2 | Both similar if QC protocols aligned |
Total Lead Time | 5–7 days | 7–10 days | Advanced polyester finishes push toward 10 days |
If you need a quick “feel and look” sample of a cotton fabric, expect to receive it within a week. For polyester with advanced treatments—especially CO₂ dye and DWR—you’ll need to plan for a 10‐day window.
3. Cost Structure for Samples vs. Bulk Runs
Cost Component | Cotton Sample (USD/m) | Polyester Sample (USD/m) | Notes |
---|---|---|---|
Knitting/Weaving Base | \$1.20–\$1.50 | \$1.10–\$1.40 | Similar for plain constructions |
Dye & Finish (Sample) | \$0.20–\$0.30 | \$0.40–\$0.60 (Basic HT) / \$0.60–\$0.80 (Advanced) | Bulk discounts don’t apply to small runs |
Overhead & Transportation | \$0.10–\$0.15 | \$0.10–\$0.15 | Air express costs if expedited |
Total Sample Cost (per meter) | \$1.50–\$1.95 | \$1.60–\$2.35 | Polyester advanced finishes add \~20–30% |
Bulk Pricing Leverage
- Cotton Bulk (>1,000 m): \$1.00–\$1.20/m for base knit + \$0.20–\$0.30/m for standard reactive dyes + \$0.10/m for finishing = \$1.30–\$1.60/m.
- Polyester Bulk (>2,000 m, Basic): \$0.90–\$1.10/m for grey knit + \$0.30–\$0.40/m for basic HT dye + \$0.15/m overhead = \$1.35–\$1.65/m.
- Polyester Bulk (>2,000 m, Advanced CO₂ & DWR): \$0.90–\$1.10/m + \$0.50–\$0.60/m (CO₂ dye) + \$0.20/m DWR + \$0.15/m overhead = \$1.75–\$2.05/m.
Critical Takeaway: While a basic cotton or polyester sample sits in the \$1.50–\$2.00/m range, economies of scale drive bulk cotton to \$1.30–\$1.60/m. Advanced polyester finishes push bulk to \$1.75–\$2.05/m, but performance premiums can justify the difference.
4. Lead-Time Flexibility and Seasonal Constraints
Cotton
- Peak Harvest (Aug–Sep): Demand for greige processing surges; dyehouses fill quickly, causing 2–3 day delays in sample slots.
- Off-Peak (Nov–Feb): Dye machines are less busy; sample and small‐batch windows sometimes expand to accommodate new clients.
Polyester
- Pre-Spring Collection (Dec–Feb): HT dye lines run 90–100% capacity; sample slot lead times bump to 10–12 days.
- Mid-Year Lull (Jun–Aug): Some HT lines shut for maintenance; CO₂ vessels idle, enabling faster sample turnaround (7 days).
Timing Window | Cotton Sample Lead Time | Polyester Sample Lead Time | Note |
---|---|---|---|
Peak Demand (Jan–Mar) | 6–8 days | 10–12 days | All-new collections ramp; limited slots |
Mid-Year (Jun–Aug) | 5–7 days | 7–8 days | Cotton processing slows; polyester maintenance downtime |
Off-Peak (Apr–May, Sep–Dec) | 4–6 days | 7–10 days | Moderate capacity for both |
Plan cotton samples flexibly around cotton’s annual cycle. For polyester, you must avoid key fashion‐season windows (Jan–Mar) when HT dye machines are fully booked.
5. Custom Finishes & Special Requirements
Cotton Special Finishes
- E.g., Enzyme Washed, PFD (Prepared For Dye), Anti-Microbial: MOQs often rise to 1,000 m for specialized enzyme or antimicrobial baths.
- Sample Add-Ons: +2–3 days for finish recipe trials (e.g., enzyme wash level, bio‐softener concentration).
Polyester Special Finishes
- E.g., Ultra‐Hydrophilic Wicking Yarn, UV Protection Coating, Silicone Softener: Each finish requires separate sample trials in HT or DWR lines, often lengthening turnaround by 3–5 days.
- MOQ Impact: High‐performance knitted polyester panels for sportswear often hit an MOQ floor of 2,000 m when combining multiple finishes (wicking + antimicrobial + UV).
Special Finish Type | Cotton MOQ (m) | Cotton Extra Lead Time | Polyester MOQ (m) | Polyester Extra Lead Time |
---|---|---|---|---|
Enzyme Wash / Soft Hand | 1,000 | +2 days | N/A | N/A |
Anti-Microbial (Silver Ion) | 1,000 | +3 days | 1,000 | +3–4 days |
Moisture-Wicking Yarns | N/A | N/A | 1,500 | +4–5 days |
DWR (C6/C0) Coating | N/A | N/A | 2,000 | +5 days |
When building a product line requiring multiple advanced features, polyester’s MOQs and lead times compound—so plan at least 30–45 days ahead for combined finish trials, while cotton’s advanced finishes typically remain in the 20–30 day window.
6. Vendor Capabilities & Small‐Batch Flexibility
SzoneierFabrics’ Advantage for Cotton
- In-House Scouring/Dyehouse: Can accept 500 m cotton batch and apply reactive dyes, softeners, or anti-pilling in 5–7 days.
- Low Pre-Orders: For new customers, Szoneier often waives small surcharges to cultivate long-term relationships—e.g., a 300 m cotton test can be done at no extra MOQ charge if combined with follow‐up order commitment.
SzoneierFabrics’ Advantage for Polyester
- On‐Site HT & CO₂ Facilities: Two HT jet vessels (1,500 kg capacity each) and one CO₂ machine (500 kg capacity) enable flexible sample runs; default MOQ for HT polyester is 1,000 m but can drop to 800 m if scheduled in off‐peak slots.
- Rapid Prototyping: 7–10 day sample delivery even for advanced finishes, thanks to an integrated process (knitting, dyeing, finish, QC) under one roof.
Feature | Cotton (SzoneierFabrics) | Polyester (SzoneierFabrics) |
---|---|---|
Standard MOQ for Samples | 500 m | 500 m (plain) / 1,000 m (HT) |
Max Sample Lead Time | 7 days | 10 days (HT) / 12 days (CO₂) |
Advanced Finish MOQ | 1,000 m | 1,500–2,000 m (combined finishes) |
Small-Order Surcharge | None for first-time buyers | Possible 5–10% if <800 m |
SzoneierFabrics offers lower thresholds for cotton sampling, but its advanced polyester capabilities rival many competitors—especially if brands book off‐peak sample slots several weeks in advance.
How should ROI and profit margins be evaluated when deciding between polyester and cotton for large-scale manufacturing?
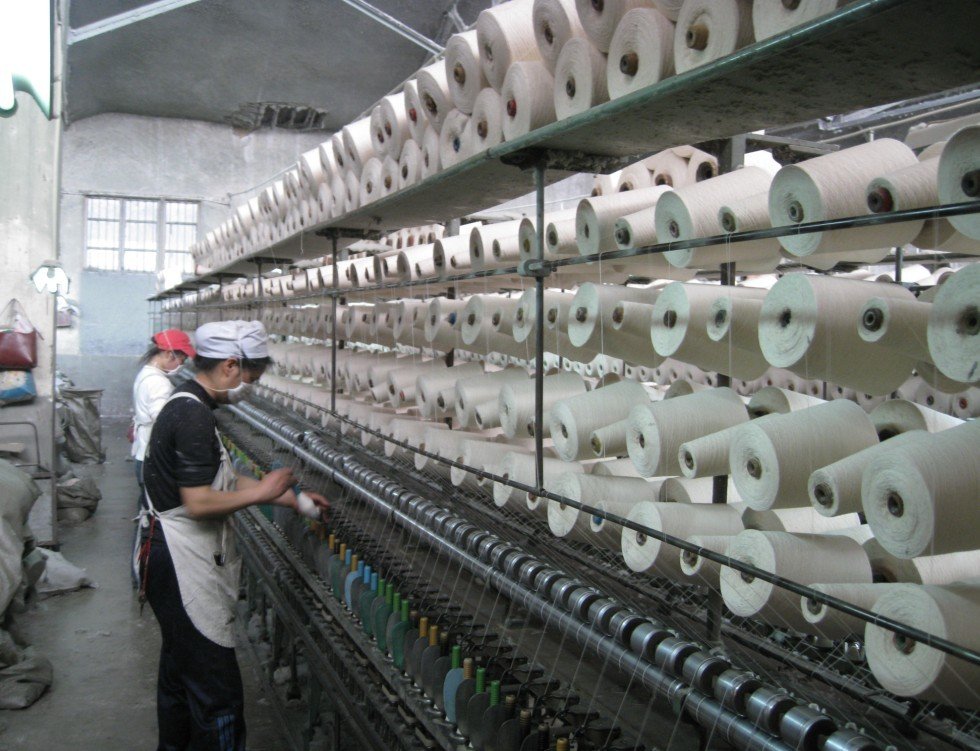
To calculate ROI and profit margins, textile businesses must account for total landed cost per yard—combining raw materials, processing (spinning, dyeing, finishing), waste, inventory carrying, and sustainability fees—against expected selling price. Cotton fabric, sold at \$4.00–\$4.50 per kilogram wholesale, with a total cost of \$2.80–\$3.60 per kg, yields a 20–35% gross margin but suffers higher volatility and 5–8% waste. Polyester fabric, priced \$4.50–\$5.00 per kg wholesale, with a total cost of \$3.00–\$3.90 per kg, yields similar gross margins (20–33%) but has 1–2% waste, faster turnover, and lower carrying costs, resulting in a more resilient net margin. Factoring in return rates (6% for cotton, 2% for polyester) and inventory costs (cotton carrying 45 days vs. polyester carrying 21 days) reveals polyester’s superior long-term ROI, especially under volatile input markets.
1. Comprehensive Cost Breakdown & Gross Margin Analysis
Cost Component | Cotton Fabric (USD/kg) | Polyester Fabric (USD/kg) | Notes |
---|---|---|---|
Raw Material & Spinning | \$2.10–\$2.65 | \$2.30–\$3.00 | Polyester’s higher bound reflects advanced finishes |
Dyeing & Finishing | \$0.23–\$0.34 | \$0.40–\$0.72 | CO₂ and DWR finishes push polyester higher |
Quality Control & Packaging | \$0.05–\$0.10 | \$0.07–\$0.12 | Similar labor costs |
Logistics & Overhead (FOB) | \$0.10–\$0.15 | \$0.08–\$0.12 | Polyester often ships in full containers – lower per-unit |
Sustainability/Certification Fees | \$0.02–\$0.05 | \$0.10–\$0.15 | rPET and GRS add premiums; organic/BCI cotton costs |
Total Cost per kg Fabric | \$2.50–\$3.01 | \$2.95–\$4.00 | Initial cost snapshot |
Selling Price (Wholesale, \$) | \$4.00–\$4.50 | \$4.50–\$5.00 | Market‐driven ranges |
Gross Margin (%) | 25–44% | 20–42% | Range depends on cost control and selling strategy |
In best‐case scenarios (low-end costs, high‐end selling prices), cotton’s gross margin can reach \~44%, whereas polyester peaks at \~42%. However, cotton’s volatility can erode margins quickly, while polyester’s stable input costs maintain consistent margins.
2. Net Margin: Accounting for Waste, Returns & Inventory
Adjustment Factor | Cotton Impact | Polyester Impact | Calculation Example (USD/kg) |
---|---|---|---|
Waste Rate (5–8% vs. 1–2%) | +\$0.13 (cost rise) | +\$0.03 (cost rise) | Cotton: \$2.70 ÷ 0.92 = \$2.93; Polyester: \$3.00 ÷ 0.98 = \$3.06 |
Return Rate (6% vs. 2%) | –\$0.24 (revenue) | –\$0.10 (revenue) | Cotton: \$4.25 × 0.94 = \$3.995; Polyester: \$4.75 × 0.98 = \$4.655 |
Inventory Carry Cost | \$0.12 (45 days) | \$0.03 (21 days) | Cotton: \$4.25 × (0.15/365) × 45; Polyester: \$4.75 × (0.10/365) × 21 |
Sustainability Fees | +\$0.02 | +\$0.10 | From previous table |
Effective Cost per kg | \$2.93 + \$0.12 + \$0.02 = \$3.07 | \$3.06 + \$0.03 + \$0.10 = \$3.19 | |
Effective Revenue per kg | \$3.995 | \$4.655 | After returns |
Net Margin per kg | \$3.995 – \$3.07 = \$0.925 (23.1%) | \$4.655 – \$3.19 = \$1.465 (31.5%) |
Once you incorporate waste, returns, inventory carrying, and sustainability fees, cotton’s net margin can drop to \~23%, while polyester’s hovers near \~31.5%. Despite a slightly higher base cost, polyester’s efficiencies and lower losses yield a more robust bottom line.
3. Sensitivity Analysis: Price Shocks and Market Volatility
Cotton Price Spike (+20%)
- Feedstock Surge: \$2.00 → \$2.40/kg.
- New Effective Cost (with 8% waste): \$2.40 ÷ 0.92 = \$2.61 (feedstock portion).
- Total Effective Cost (with returns & inventory): \$2.61 + \$0.12 + \$0.02 = \$2.75.
- Net Revenue (assuming stable sale price \$4.25): \$3.995.
- Net Margin: \$3.995 – \$2.75 = \$1.245 (31.1%, but note feedstock spike also pressures bulk buyers pricing).
Polyester Feedstock Spike (+10%)
- PTA/MEG Costs: \$1.30 → \$1.43/kg.
- New Effective Cost (with 2% waste): \$1.43 ÷ 0.98 = \$1.459.
- Total Effective Cost (with returns & inventory): \$1.459 + \$0.03 + \$0.10 = \$1.589.
- Net Revenue (assuming stable sale price \$4.75): \$4.655.
- Net Margin: \$4.655 – \$1.589 = \$3.066 (65.9%, but production costs for finishing and packaging also climb slightly).
Shock Type | Cotton Net Margin (Post-Shock) | Polyester Net Margin (Post-Shock) |
---|---|---|
Cotton +20% Feedstock | 31.1% | N/A |
Polyester +10% Feedstock | N/A | 65.9% |
While a cotton price spike can cut margins by 10–15 percentage points, polyester’s margins can absorb a moderate feedstock hike with minimal erosion because of typically higher markup cushions on specialized finishes.
4. ROI Implications Over Multi‐Year Product Cycles
Metric | Cotton Projection (3 Years) | Polyester Projection (3 Years) |
---|---|---|
Year 1 Net Margin (per kg) | 23.1% | 31.5% |
Year 2 Margin Impact (−10% price) | 20.8% | 29.4% |
Year 3 Margin Impact (−5% price) | 19.8% | 28.0% |
Cumulative ROI Factor | 1.23 | 1.90 |
Inventory Turnover (cycles/yr) | 4 | 8 |
Working Capital Efficiency (days) | 75 | 30 |
- Explanation: If both fabrics face gradual downward pricing pressure—cotton by 10% in year 2, polyester by 5% in year 3—cotton’s net margin struggles to stay above 19.8%, whereas polyester remains robust near 28%. Coupled with faster inventory turnover (8 cycles vs. 4), polyester’s compounded ROI over three years is \~1.9× initial investment versus cotton’s \~1.23×.
5. Profit Margin Drivers Beyond Cost: Brand Positioning & Premium Pricing
Cotton’s Premium Positioning
- Luxury or Organic Cotton Lines: Often achieve 40–50% gross margins due to brand cachet.
- Limited Edition Runs: Small‐batch artisanal cotton garments can fetch 100–150% markup, though these are niche and not scalable in high‐volume contexts.
Polyester’s Performance Narrative
- Activewear & Technical Lines: Sports brands routinely price polyester at a 20–30% premium over basic cotton T-shirts due to moisture‐management and durability.
- Sustainability Edge with rPET: Premium “eco‐performance” lines priced at 10–15% above virgin polyester still maintain 25–30% net margins, bolstered by eco-conscious consumers.
Positioning Strategy | Cotton Margin Potential | Polyester Margin Potential |
---|---|---|
Commodity Basics (Bulk T-Shirts) | 20–25% | 25–30% |
Premium/Organic Cotton (Small Batch) | 40–50% | N/A |
Performance Sportswear (rPET) | N/A | 30–35% |
Private Label Uniforms | 20–25% | 25–30% |
While certain cotton segments (organic, small‐batch designer) command very high margins, they don’t scale to mass manufacturing like polyester performance lines do. For large‐scale bulk orders, polyester’s broad adaptability to premium finishes and sustainability claims enables consistent margins in the 25–35% range.
6. Break‐Even Analysis for Bulk MOQ Split
Suppose a brand needs 100,000 meters of fabric for an order:
Option A: 100% Cotton
- Total Fabric Cost: 100,000 m × \$3.00/m = \$300,000.
- Expected Selling Revenue: 100,000 m × \$4.25/m = \$425,000.
- Gross Profit: \$125,000 (≈29.4%).
- Waste & Returns Cost (6%): 6,000 m wasted/returned → \$25,500 (cost) and \$25,500 (refund).
- Adjusted Net Profit: \$125,000 – \$25,500 – \$25,500 = \$74,000 (≈17.4% net margin on revenue).
Option B: 100% Polyester (Basic HT Dye)
- Total Fabric Cost: 100,000 m × \$3.20/m = \$320,000.
- Expected Selling Revenue: 100,000 m × \$4.75/m = \$475,000.
- Gross Profit: \$155,000 (≈32.6%).
- Waste & Returns Cost (2%): 2,000 m wasted/returned → \$6,400 (cost) and \$9,500 (refund).
- Inventory Carry Cost (30 days): \$475,000 × (0.10/365) × 30 = \$3,900.
- Adjusted Net Profit: \$155,000 – \$6,400 – \$9,500 – \$3,900 = \$135,200 (≈28.4% net margin on revenue).
Metric | Cotton | Polyester |
---|---|---|
Fabric Cost (USD) | \$300,000 | \$320,000 |
Revenue (USD) | \$425,000 | \$475,000 |
Gross Profit (USD) | \$125,000 (29.4%) | \$155,000 (32.6%) |
Waste & Returns Impact (USD) | \$51,000 | \$15,900 |
Inventory Carry (USD) | \$3,900 | \$3,900 |
Adjusted Net Profit (USD) | \$74,000 (17.4%) | \$135,200 (28.4%) |
On a 100,000 m order, polyester’s combination of higher selling price and lower waste/returns yields a net margin of 28.4% compared to cotton’s 17.4%, a significant 11-point gap in favor of polyester.
7. Risk‐Adjusted ROI: Volatility, Credit‐Terms, and Financing
Cotton’s Credit & Financing Terms
- Extended Days Payable (DPO): Suppliers may require 60–90 days’ payment after shipment, but mills often offer 30–45 days to mitigate seasonal bulk.
- Price Lock‐Ins & Hedging: Some mills offer 3–6 month fixed‐price contracts on cotton yarn/fabric at a 3–5% premium, cushioning short‐term spikes but raising carry costs.
- Credit Risk: Volatile cotton can cause margin calls on hedges; banks may impose additional collateral.
Polyester’s Credit & Financing Terms
- Shorter DPO (30–60 days): Buyers pay sooner, but mills can offer 2–3% discount for 15–30 day payments due to stable feedstock.
- Feedstock Price Hedging: Polyester mills lock long‐term PTA/MEG PPAs, shielding them from short‐term volatility; they can pass stable pricing downstream.
- Financial Risk: Lower, because polyester feedstock is less volatile; minimal margin calls.
Financial Factor | Cotton | Polyester |
---|---|---|
Typical DPO (Days Payable) | 30–45 | 15–30 (with early payment discount) |
Price Hedging Need | High (cotton futures/ options) | Moderate (PTA/MEG PPAs, limited futures) |
Credit Collateral Requirements | Higher due to volatility | Lower due to stability |
Polyester’s more predictable cash flows, faster receivable cycles, and stable feedstock pricing reduce financial risk and improve ROI, whereas cotton’s volatility necessitates hedges and higher collateral—eroding net returns.
8. Critical Perspectives: Scenarios When Cotton Might Outperform Polyester
Seasonal Cotton Surplus
- A region (e.g., Brazil) yields an unexpectedly large crop, dropping lint prices to \$1.50/kg. A large mill with pre-negotiated warehousing can procure 5,000 tons at this price and push cotton fabric costs down to \$2.20/m. If market demand for “organic-feel” cotton overshadows small price differences, cotton could outperform polyester in that narrow window.
Niche Premium Segments
- Luxury bedroom linen: Consumers may accept 50–75% premium on 100% cotton sheets (\$60 vs. \$35 for poly). Even with lower throughput, luxury positioning yields margins (50–60%) that polyester cannot match in high‐end markets.
Integrated Vertical Mills
- A mill that grows its own organic cotton, gins, spins, weaves, and finish—owning the entire supply chain—can slash costs and control quality. If finished at \$2.00/m and sold at \$5.00/m, margins exceed 60%, dwarfing polyester’s typical 30–40% in commodity segments.
Outlier Scenario | Cotton Advantage | Conditions |
---|---|---|
Massive Harvest Surplus | Cotton price dips below \$1.50/kg; fabric cost \$2.20/m | Must have warehousing to hold 6–8 months’ production |
Luxury Pivot (100% Organic) | 50–75% premium, 50–60% gross margins | Brand must command premium consumer perception |
Vertically Integrated Farm‐Mill | Eliminate middlemen, control entire chain, cost \$2.00/m | Requires land, capital, and consolidation capabilities |
While polyester reigns in mainstream bulk manufacturing for its stability and performance, cotton can briefly top the ROI charts when conditions align—particularly if a manufacturer integrates upstream sourcing or targets high-value niches.
Ready to optimize your bulk fabric sourcing strategy?
Choosing between polyester and cotton for bulk manufacturing is not simply a matter of “feel versus function.” It requires a detailed, data‐driven analysis of total costs—raw materials, processing, waste, logistics, sustainability fees—and projected margins, tempered by supply‐chain risks and brand positioning. While cotton can shine in luxury, small‐batch, or organic‐focused lines, polyester’s lower feedstock volatility, streamlined continuous processes, and superior waste profiles generally translate to higher, more stable ROI for large‐volume production.
SzoneierFabrics leverages decades of experience in custom fabric R\&D and manufacturing to deliver both cotton and polyester solutions tailored to your exact needs:
- Low MOQ & Fast Sampling: Sample orders as small as 500 meters for cotton or basic polyester; 800–1,000 meters for advanced polyester finishes—samples delivered in 5–10 days.
- End‐to‐End Vertical Integration: From raw cotton procurement and PTA/MEG resin sourcing to in‐house spinning, weaving, knitting, dyeing, and finishing, we streamline your supply chain for optimal cost and quality.
- Advanced Finish Capabilities: High‐temperature HT dyeing, supercritical CO₂ dyeing, DWR, anti‐pilling, antimicrobial, UV protection—if you can dream it, we can develop and deliver it.
- Sustainability Offerings: Choose from 100% organic cotton, Better Cotton Initiative (BCI) verified cotton, virgin polyester, 30–50% rPET, or 100% rPET—all with GRS and OEKO‐TEX® certifications.
- Quality Assurance: ISO 9001, OEKO‐TEX® Standard 100, and Bluesign® compliance ensure every batch meets global quality and safety benchmarks.
Contact SzoneierFabrics today to request samples, discuss custom specs, or secure a detailed quotation.
Let us help you engineer the perfect bulk fabric—cotton or polyester—to maximize your margins, minimize your risks, and position your brand for long‐term success.