
Silk fabric, long celebrated for its elegance, sheen, and softness, remains one of the most luxurious textiles on the market. But behind its perfect finish lies a complex and delicate manufacturing process. For B2B buyers, importers, and sourcing agents, one of the biggest frustrations isn’t pricing or lead time—it’s receiving a roll of silk with visible tension marks, streaky dye lines, or uneven sheen under light.
Tension marks and uneven dyeing are two of the most common weaving defects in silk fabric production, often caused by mechanical inconsistency, yarn irregularities, or improper finishing techniques. Industrial solutions include optimizing loom tension control, pre-treatment calibration, and dye protocol standardization.
If you’ve ever opened a silk shipment only to find flaws that disrupt your production timeline, you’re not alone. In this article, we’ll break down the causes of these defects and provide practical, factory-level strategies to prevent and resolve them—so you can make better sourcing decisions and avoid expensive reworks or returns.
Let’s begin with a comprehensive overview of the most common weaving flaws in the silk industry.
What Are the Most Common Weaving Defects in Silk Fabric Production?
Silk fabric weaving defects typically arise during yarn preparation, loom setup, or the weaving and dyeing processes. The most frequently reported issues include tension streaks, warp-line variations, broken filaments, slubs, uneven color zones, and shimmer inconsistencies.
The most common weaving defects in silk fabric are tension marks, warp line inconsistencies, broken filaments, slubs, and uneven dye zones—usually caused by improper loom settings, inconsistent yarn feed, or poor finishing control.
Key Weaving Defects Explained
1. Tension Marks (Stress Lines)
- Long vertical streaks due to uneven warp tension
- Most noticeable in charmeuse and crepe de chine under angled light
- Commonly occur in rolls with inconsistent reeling or warped beam settings
2. Warp & Weft Irregularities
- Warp “shadowing” from thread count deviation
- “Weft bars” caused by density variation in shuttle changeovers
3. Slubs and Filament Breakage
- Often the result of poor degumming, leading to raw sericin residue
- Appear as rough spots or knots on smooth silk surfaces
4. Shimmer Disparity
- Irregular light reflection due to inconsistent fiber orientation
- Problematic for satin and glossy silk used in premium garments
Defect Type | Visual Effect | Main Cause | Affected Silk Types |
---|---|---|---|
Tension Marks | Vertical streaks | Uneven loom tension | Charmeuse, Habotai |
Warp-Line Variance | Dull/fuzzy vertical zones | Misaligned yarn feed | Crepe de chine, organza |
Broken Filaments | Rough texture spots | Yarn stress during reeling | Twill, satin |
Uneven Dye Patches | Blotchy color zones | Inconsistent pre-treatment | Dyed charmeuse, printed silks |
5. Real Case Example:
A German interior design brand reported receiving 500 meters of 19-momme silk charmeuse with subtle shimmer inconsistency. Post-analysis showed the issue was caused by a 1.2mm warp tension shift on one loom during a 6-hour run—barely visible to the eye but devastating under spotlight usage on drapery.
How Do Tension Marks Form During the Silk Weaving Process?
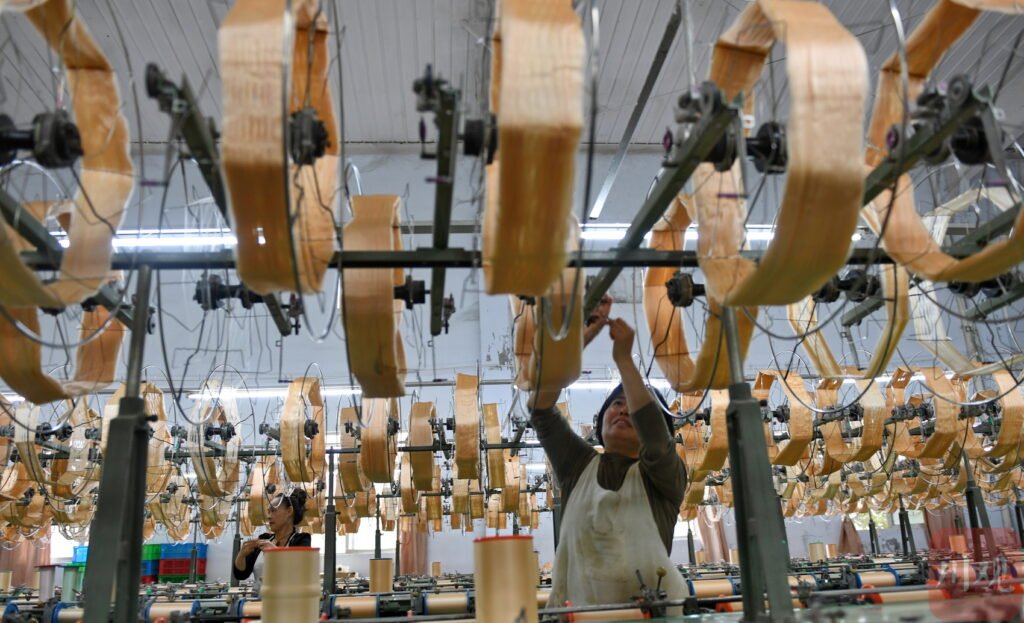
Tension marks occur when the warp threads on the loom are under inconsistent or excessive stress during weaving. This causes fibers to stretch unevenly, leading to visible lines or bands—especially under directional light. These defects often emerge after dyeing or finishing, making them difficult to detect at the grey fabric stage.
Tension marks in silk fabric result from uneven warp stress during weaving, often caused by improper beam setup, poorly calibrated tension settings, or inconsistent yarn sizing.
Mechanisms Behind Tension Marks
1. Improper Beam Loading
- Uneven pressure on the warp beam leads to thread elongation and compression bands.
- Typical in older looms or when switching from fine (8–10 momme) to heavy (22–30 momme) silk.
2. Yarn Tension Fluctuation
- Caused by:
- Faulty tension brakes
- Inconsistent yarn cone size
- Operator error in tension weight application
3. Environmental Impact
- Humidity and heat affect filament elasticity:
- High humidity = looser warp tension
- Low humidity = increased brittleness
Tension Factor | Effect on Fabric | Solution |
---|---|---|
Uneven warp pressure | Vertical stress marks | Balanced loading, beam width adjustments |
Yarn sizing variation | Irregular tension across threads | Pre-weaving yarn conditioning |
Ambient humidity shift | Shrinking/stretching post-finishing | Temperature-controlled production rooms |
4. Modern Loom Sensor Failures
- New electronic looms (like Tsudakoma or Toyota air-jets) have auto-tension controls, but these sensors require frequent recalibration.
- One missed calibration check can affect hundreds of meters in a single shift.
“We had a week where the auto-tension system read normal, but the fiber showed consistent 0.3g/cm² deviation—too minor for alarms but enough to ruin sheen continuity.”
Which Types of Uneven Dyeing Affect Silk Fabrics Most Frequently?
Uneven dyeing in silk is not just a cosmetic problem—it can undermine product quality, brand trust, and resale value. Silk’s natural protein-based fiber structure makes it particularly sensitive to dye absorption conditions. The most common dyeing defects include color banding, blotchy patches, edge-to-center shading, and off-tone irregularities.
The most frequent uneven dyeing issues in silk fabrics are color banding, center-to-edge shading, patchy absorption, and dye spotting—typically caused by inconsistent fabric pre-treatment, pH imbalance, or poor dye bath circulation.
Uneven Dyeing Defects Explained
1. Center-to-Edge Color Shading
- Occurs when fabric tension varies during dyeing, resulting in lighter or darker tones across the roll.
- Particularly noticeable in light colors like blush pink or ivory.
2. Horizontal Color Banding
- Often linked to uneven dwell time in the dye bath, where different sections of fabric absorb dye at different rates.
- Prominent in reactive or acid dye processes.
3. Dye Spotting or Streaks
- Caused by undissolved dye particles, poor filtration, or chemical incompatibility in the dye bath.
- Appears as dots, lines, or smudges—especially after digital printing or immersion dyeing.
4. pH Shift Irregularities
- pH imbalance in the dye liquor can cause tone variations across the roll.
- pH below 4.0 can dull the shade; above 5.5, silk may appear “washed out.”
Defect Type | Visual Cue | Root Cause | Common in… |
---|---|---|---|
Center-edge shading | Darker or lighter near edges | Fabric tension imbalance during dyeing | Charmeuse, satin |
Color banding | Horizontal lines | Dwell time inconsistency | Crepe, broadcloth |
Spotting or dye clusters | Specks or blotches | Dye impurity or poor dispersion | Hand-dyed or digitally printed |
Off-tone variation | Inconsistent color tones | Dye bath temperature or pH fluctuation | Bulk dyed 5A/6A mulberry silk |
5. Real Buyer Experience
A U.S. fashion label ordered 1,000 meters of 6A silk for pastel spring blouses. After garment production, 40% of the shirts showed faint horizontal dye bands under store lighting. The defect traced back to a failed temperature sensor in one dye vat, which hadn’t been recalibrated in over 90 days.
What Industrial Factors Contribute to Weaving and Dyeing Defects?

Defects in silk are often the result of a chain reaction of upstream and downstream inconsistencies—not just a single point of failure. From raw yarn selection to finishing settings, every stage of production must be monitored with precision.
Silk weaving and dyeing defects are commonly caused by poor yarn quality, inconsistent warp tension, uncontrolled dye bath variables, and aging or miscalibrated machinery across production stages.
Factory-Level Factors Behind Silk Defects
1. Raw Material Inconsistency
- Mixed cocoon batches or poorly sorted filaments lead to irregular yarn thickness, which impacts both weaving tension and dye absorption.
- 6A silk requires long, uniform filaments—any deviation compromises dye uniformity.
2. Loom Setup and Maintenance
- Tension sensors, beam alignment, shuttle calibration, and warp feed speed all need routine adjustment.
- Manual looms and outdated semi-automatic models are more prone to drift and misalignment during production runs.
Machine Setting | Optimal Range | Risk If Ignored |
---|---|---|
Warp beam pressure | ≤ ±2% tolerance | Uneven filament pull |
Dye bath temperature | 85°C–95°C (acid dyeing) | Shading, fading, or tone mismatch |
Tension force sensors | Calibrated every 30 days | Missed streaks in 1000+ meters |
3. Water and Chemical Quality
- Hard water with excess calcium/magnesium disrupts dye bonding with silk proteins.
- Unfiltered dye baths may carry residues from previous runs, leading to “ghost staining.”
4. Worker Skill and Training
- Even in automated plants, operator decisions play a crucial role:
- Deciding how many rolls per dye bath
- Controlling fabric feed-in speed
- Monitoring color shifts in real-time
Tip from SzoneierFabrics technician: “When onboarding new machines, we simulate five different fabric tensions before real production. Brands that skip mock runs are the first to get defect reports.”
5. Environmental Fluctuations
- High humidity leads to yarn slackness and warping on the loom.
- Low humidity creates brittle fibers, causing micro-breaks and filament stress.
How Can Manufacturers Prevent Tension Marks in High-Grade Silk?
Preventing tension marks in high-grade silk requires a combination of precision loom calibration, consistent yarn sizing, and proactive environmental controls. Manufacturers that produce 6A-grade silk or luxury-weight charmeuse must adopt stricter tension tolerance protocols, as even micro-variations can cause visible stress lines.
Manufacturers can prevent tension marks in silk by maintaining warp beam tension below ±2%, using consistent yarn sizing, calibrating looms regularly, and controlling humidity during weaving.
Best Practices for Tension Control
1. Pre-Weaving Yarn Conditioning
- Use humidity-controlled yarn rooms to maintain consistent moisture before feeding yarn onto looms.
- Pre-condition raw silk to stabilize elongation properties, especially for high momme weights (≥22 momme).
2. Beam Loading & Warp Tension Checks
- Digital load cells should be installed to monitor live tension.
- Manual loom settings must be cross-verified with a tension meter every 50–100 meters of weaving.
Tension Thresholds by Fabric Type | Recommended Tolerance | Typical Risk if Exceeded |
---|---|---|
Charmeuse (19–22 momme) | ±1.5% | Light streaks under oblique light |
Crepe de Chine | ±2% | Ripple texture distortion |
Silk Twill | ±2% | Weft-line misalignment |
3. Loom Calibration & Maintenance Routine
- Calibration schedule:
- Daily: Warp tension & beam alignment checks
- Weekly: Shuttle travel speed review
- Monthly: Comprehensive diagnostic test via PLC panel
Advanced Japanese looms like Tsudakoma ZAX series and Toyota JAT810 have auto-alert systems when tension deviates—but still require manual override logs.
4. Operator Training & SOP Compliance
- Operators must understand:
- How to manually override tension sensors
- When to stop a run due to minor shimmer discrepancies
- Establish visual inspection protocols at every 200m checkpoint.
5. Case Study from SzoneierFabrics
In 2024, Szoneier upgraded its Suzhou-based facility to include live-monitoring IoT-enabled tension sensors. Result: Reported tension mark incidents dropped 72%, with a 15% improvement in dye consistency for 6A charmeuse exports to Germany and Italy.
What Are the Best Solutions for Fixing Uneven Dyeing in Silk Rolls?
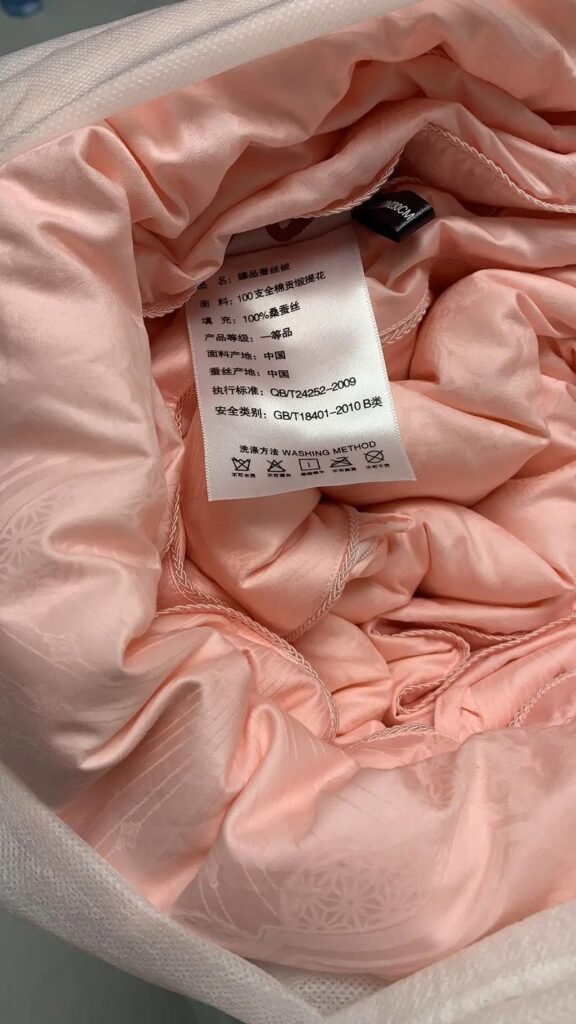
While prevention is ideal, post-dye correction methods can salvage large batches of unevenly dyed silk—provided the defects are not fiber-deep. Techniques like overdyeing, stripping, enzyme washing, and tonal redyeing are used at an industrial level to recover flawed inventory.
Unevenly dyed silk rolls can often be fixed through overdyeing, enzyme washing, or tone-corrective redyeing—though success depends on defect severity, fabric type, and dye chemistry.
Correction Methods by Defect Type
1. Overdyeing
- Adds a darker uniform layer to mask color inconsistencies.
- Ideal for banding or mild shading but limits color flexibility (must go darker).
- Risk: Duller hand-feel if not reconditioned properly.
2. Enzyme Washing
- Removes surface-level dye inconsistencies or deposits.
- Used for silk types like Eri or Habotai, where the fabric has a stronger resistance to pilling.
- Can restore evenness and enhance sheen if combined with softeners.
3. Redyeing with Corrected pH
- Applicable when initial defects are caused by pH imbalance.
- Requires:
- Dye stripping (mild acid or peroxide bath)
- pH-neutral redye bath (4.8–5.2 optimal range)
Defect Type | Recovery Method | Estimated Salvage Rate | Notes |
---|---|---|---|
Horizontal banding | Overdyeing | 80–90% | Must adjust shade expectations |
Spotty dye | Enzyme + rebuff | 60–75% | Good for scarf fabric salvage |
pH-based shading | Redye with correction | 70–85% | Requires lab-controlled process |
4. Digital Printing Recovery (for White Silk Only)
- If dyeing fails but fabric remains uncut, digitally printed overlays can hide inconsistencies.
- Useful for accessories, linings, and budget fashion items.
“Most overdye requests come in for ivory, blush, or sky blue rolls. We salvage these with a dusty rose or olive overdye, giving them a premium earthy tone that brands now label as ‘artisan washed.’”
Do Weaving Defects Impact Silk Grading and Fabric Pricing?
Absolutely. In the wholesale silk trade, weaving and dyeing defects are among the top factors that lead to fabric grade downgrades, price reductions, and sometimes product rejection. The international silk grading system—especially the 6A/5A/4A system for mulberry silk—places a premium on visual uniformity, thread strength, and dye evenness. Tension marks or blotchy dyeing can instantly downgrade fabric from 6A to 5A or below, costing manufacturers and resellers significant margin losses.
Yes, weaving and dyeing defects can downgrade silk fabric from 6A to 5A or lower, reducing its value by 15–40% depending on severity and visibility, especially in luxury product applications.
Grading and Price Impact
1. Grading Criteria Breakdown
Grade | Key Requirements | Visible Defect Tolerance |
---|---|---|
6A | No visible defects, uniform sheen, >750m fiber length | None; less than 1 per 10m max |
5A | Minor surface slubs, slight shimmer variation | ≤2 visible issues per 10m |
4A | Color shift allowed, rougher hand-feel acceptable | ≤4 minor flaws per 10m |
2. Pricing Drop by Grade (2025 Avg.)
Grade | Avg. Price (USD/meter) | Price Impact from Downgrade |
---|---|---|
6A | \$32–\$45 | — |
5A | \$24–\$32 | -20% |
4A | \$16–\$22 | -35% to -40% |
3. Luxury Use Cases & Grade Sensitivity
- High-end bedding or bridalwear customers often demand defect-free 6A silk.
- Even barely visible tension marks under strong lighting may cause product returns or reworks in retail fashion.
4. Factory Reactions
- Downgraded batches are often sold to:
- Scarf manufacturers
- Lining factories
- Handicraft or upcycled silk brands
- Some factories cut defective rolls into smaller lots (e.g., 3–10m) and offer discounted stock for sampling or prototyping use.
“We once downgraded a 500m roll of 6A charmeuse to ‘5A-batch’ status due to 3 minor banding zones. That shift cost us \$4,000 in wholesale revenue, even though the defect was barely visible.”
Is Sourcing Defect-Free Silk Fabric Possible with Low MOQ Orders?
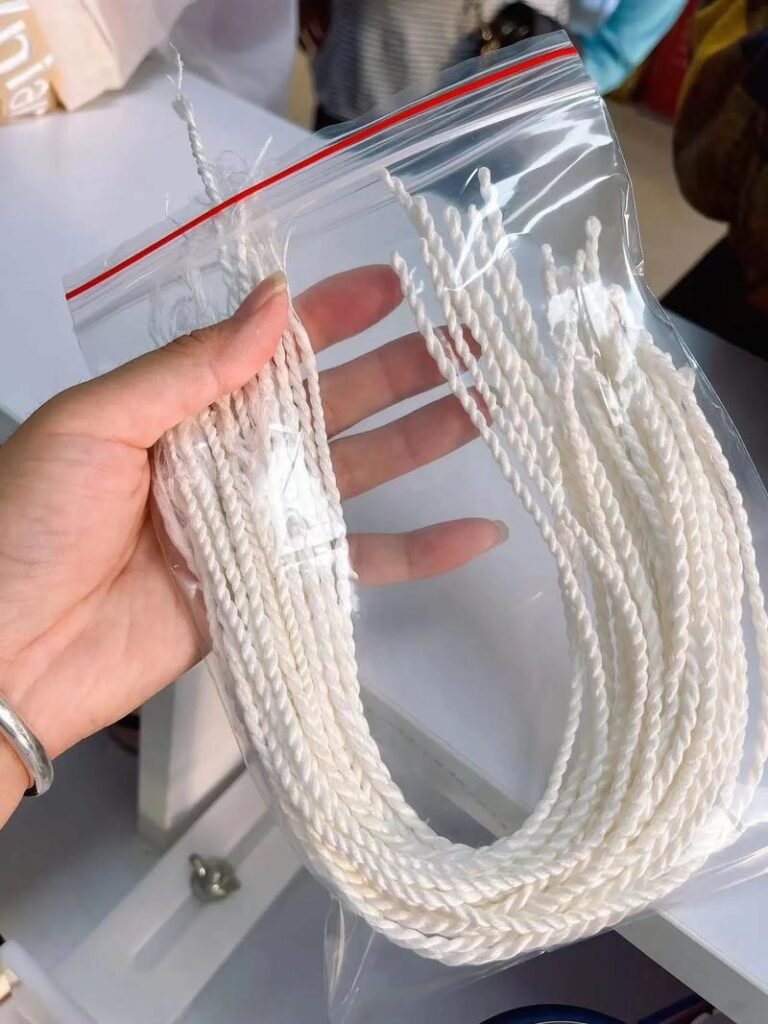
Yes—but it requires working with a reliable silk factory that has in-house quality control, flexible small-batch handling, and a history of servicing boutique B2B buyers. Traditionally, low MOQ orders are more prone to defects due to less attention from large-scale mills, but specialized manufacturers like SzoneierFabrics offer dedicated small-run solutions.
Defect-free silk fabric is possible with low MOQ sourcing if buyers choose experienced manufacturers offering quality control, swatch approvals, and small-lot inspections—like those provided by SzoneierFabrics.
How to Get High-Quality Silk in Small Batches
1. Key Tactics for B2B Buyers
Strategy | Benefit |
---|---|
Ask for 5–10m test swatches | Spot flaws before placing bulk orders |
Confirm loom type & dye house | Know if the facility can handle fine-weight silk |
Request QA report for small batch | Ensures no “leftover” or downgraded stock |
Specify defect tolerance in PO | Set your own acceptance level upfront |
2. MOQ vs Quality Matrix
MOQ Type | Risk Level (Defects) | How to Minimize |
---|---|---|
<20 meters | High (if random stock) | Always request fresh-dyed production |
50–100 meters | Medium | Confirm loom schedule & QC sign-off |
200+ meters | Lower | Easier to maintain uniformity |
3. How SzoneierFabrics Solves This
- Offers small-batch sampling (5m MOQ) with photo/video inspection before dispatch
- Provides custom-dyed 6A silk starting from 50m per color
- Delivers free swatches to test sheen, weight, and defect tolerance
- Every shipment includes a final QA checklist, even for low-volume orders
A fashion start-up in New Zealand sourced 30m of digitally printed satin silk from Szoneier. Despite the small MOQ, the shipment included:
- 3 pre-shipment photo inspections
- A digital QC report
- Full Pantone matching
No returns. The brand used the silk for a successful Kickstarter launch with rave customer reviews on product feel and print vibrancy.
📩 Let’s talk about your next silk project
No matter how beautiful silk is, even the smallest tension mark or dye inconsistency can make or break your final product—especially when your customers expect luxury. But sourcing high-quality silk fabric without defects is completely possible, even with small batch orders, if you work with the right partner.
At SzoneierFabrics, we don’t just manufacture silk—we optimize it for your brand’s exact needs.
We offer:
- ✅ Custom silk fabric production (6A/5A/4A grades)
- ✅ MOQ from just 5 meters
- ✅ Free swatches and design consultation
- ✅ Quick lead times and full QC reports
- ✅ OEM/ODM services for printed silk, dyed silk, or blended fabrics 📧 Email: Info@szoneierfabrics.com 🌐 Website: https://szoneierfabrics.com 📞 Phone: (+86) 13823134897
From premium bridalwear to digitally printed scarves—we help you avoid costly defects and create luxury-quality silk products, even on a startup budget.