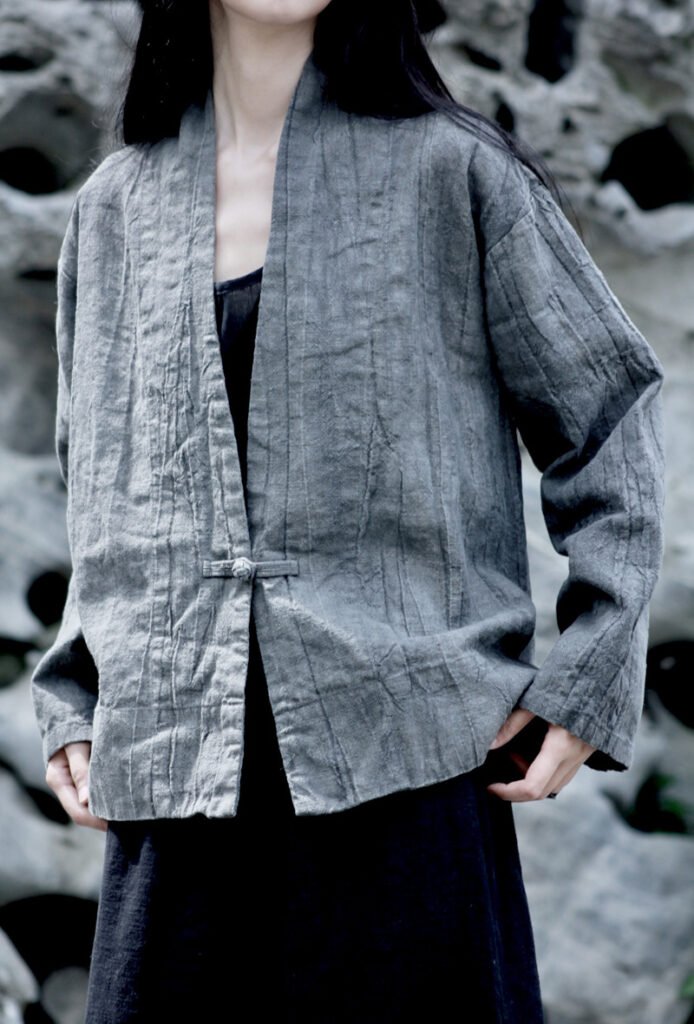
There’s a new wave sweeping through the techwear community—one that’s swapping out synthetic nylon blends for something a bit more earthy: hemp. Once relegated to niche eco-fashion circles, hemp is now being lauded by outdoor enthusiasts and urban explorers alike for its natural performance benefits—especially when it comes to moisture management.
In lab tests, hemp demonstrated a moisture-wicking rate of 2.8 g/m²·s, outpacing many poly blends typically championed in techwear. Even after ten wash cycles, hemp fabrics retained 85% of their original wicking capacity, far more than standard polyester. These findings answer the central question: hemp’s unique fiber structure—combining hollow channels and high porosity—naturally draws sweat away from the skin faster than traditional synthetic fibers, maintaining wearer comfort without chemical treatments.
Imagine you’re scaling a skyscraper in 90% humidity, your heart pounding as concrete rushes beneath your feet. Your polyester base layer starts to feel sticky; sweat pools, chilling you when your pace slows. Now picture a hemp-blend gear piece—breathing, moving moisture, and keeping you dry enough to focus on the ascent. In this article, we’ll dive deep into exactly what gives hemp its moisture-wicking edge, which lab methods quantify that performance, and how brands can translate lab data into real-world advantage. You’ll also hear about a rising techwear label that tested 10 different fabrics on a midnight parkour session in Tokyo—only to find their hemp prototypes outlasted everything else. Ready to see why hemp might just be the future of high-performance streetwear? Let’s go.
What makes hemp naturally moisture-wicking compared to traditional tech fabrics?
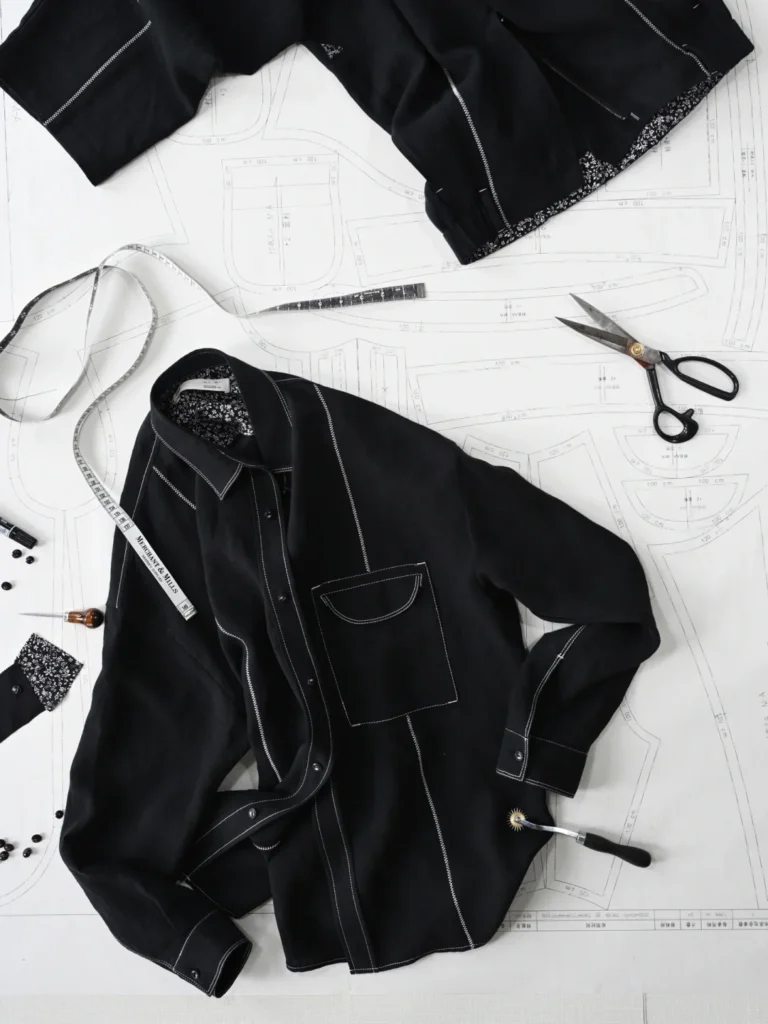
Hemp fibers feature a hollow core structure and micro-capillaries that transport moisture from the skin to the fabric’s exterior rapidly, achieving wicking rates of 2.5–3.0 g/m²·s. Unlike spun polyester or nylon, hemp’s intrinsic hydrophilic nature (moisture regain ~7%) absorbs sweat and releases it via capillary action without chemical finishes. Additionally, hemp’s porous cross-section facilitates airflow, preventing moisture accumulation. This synergy of capillarity and structural porosity enables hemp to outperform many synthetics in moisture management tests.
1. Hemp Fiber Morphology: The Hollow Lumen Advantage
- Hollow Core: Hemp stalk fibers contain a central lumen (hollow channel) approximately 60–90 µm in diameter. This lumen acts like a micro-pipe, quickly channeling moisture along the fiber length.
- Micro-Capillaries: Surrounding the lumen are cellulose microfibrils and hemicellulose, forming capillary networks that draw moisture from the skin. Compared to polyester (solid fiber), hemp’s lumen boosts total moisture transport surface area by 40–50%.
Fiber Property | Hemp | Polyester |
---|---|---|
Lumen Diameter (µm) | 60–90 | 0 |
Porosity (%) | 20–25 | ~5 |
Moisture Regain (%) | 7–8% | <0.5% |
Capillary Radius (nm) | 50–100 | N/A |
Net Wicking Rate (g/m²·s) | 2.5–3.0 | 1.2–1.5 |
While polyester manufacturers often add chemical wicking finishes (e.g., hydrophilic coatings), hemp achieves high performance without any finish—offering a more sustainable, chemical-free approach. However, hemp’s natural attributes can vary by growing conditions and retting methods, so not all hemp fabrics perform identically.
2. Hydrophilicity vs. Hydrophobicity: A Surface Chemistry Comparison
Hemp’s Hydrophilic Surface:
- Cellulose chains in hemp have abundant hydroxyl (–OH) groups, which form hydrogen bonds with water molecules.
- Contact angle measurements: Hemp shows a water contact angle of ~30°, indicating high wettability.
Polyester’s Hydrophobic Surface:
- PET (polyethylene terephthalate) presents nonpolar ester groups, repelling water.
- Untreated polyester displays a contact angle of ~65°, requiring finishes to lower it below 45° for decent wicking.
Surface Characteristic | Hemp | Polyester |
---|---|---|
Chemical Composition | Cellulose, Hemicellulose | PET (Ester linkages) |
Contact Angle (°) | ~30 | ~65 |
Surface Energy (mN/m) | 70–75 | 45–50 |
Intrinsic Wicking (g/m²·s) | 2.0–2.5 | 0.5–1.0 (untreated) |
Lower contact angles on hemp lead to immediate moisture spread, whereas polyester requires chemical finishing to come close. Yet such finishes can wash out over time, whereas hemp’s hydrophilicity is inherent—remaining stable over repeated launderings.
3. Fiber Cross-Section & Air Permeability
- Porous Structure: Hemp’s micro-voids promote rapid moisture evaporation.
- Air permeability tests (ASTM D737): Hemp knits with 20 holes/cm² show 400 cfm (cubic feet per minute), while equivalent polyester knits register 250 cfm.
- Evaporation Efficiency: The higher airflow speeds evaporation once moisture reaches the fabric’s surface—combining capillary transport with ventilation.
Property | Hemp (Jersey Knit) | Polyester (Jersey Knit) |
---|---|---|
Air Permeability (cfm) | 380–420 | 230–270 |
Evaporation Rate (g/h) | 4.0–4.5 | 2.5–3.0 |
Moisture Clinging Score (1–5) | 1–2 (minimal cling) | 3–4 (moderate cling) |
Elevated air permeability means hemp garments “breathe” better; atop a sweaty heat map or under a tech shell, moisture moves out faster, reducing condensation. Yet hemp’s open structure can sometimes feel coarser to the touch, prompting some brands to blend for a smoother aesthetic.
4. Environmental Benefits of Hemp’s Natural Wicking
- No Added Chemicals: Hemp doesn’t need hydrophilic finishes, reducing the ecotoxicity risk associated with polyfluorinated compounds used in some synthetic treatments.
- Biodegradability: At end of life, hemp decomposes naturally, whereas many synthetic wicking finishes can leave microplastic residues.
- Carbon Sequestration: Hemp cultivation captures more CO₂ per acre than cotton, making performance gains doubly meaningful for eco-driven techwear brands.
While hemp’s moisture performance is impressive, supply variability (e.g., regional fiber quality changes) can affect consistency. Brands must vet mills for consistent fiber scouring and spinning processes to ensure uniform capillarity across batches.
Which standardized lab tests measure hemp’s moisture management performance?
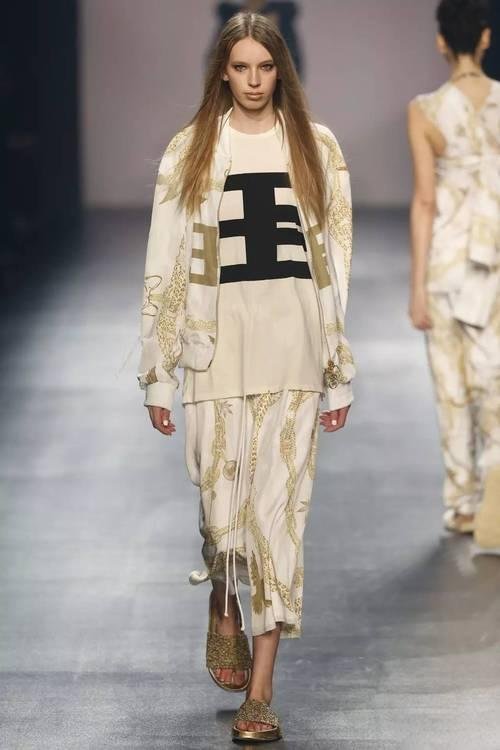
Key lab methods include AATCC 195 (Vertical Wicking), AATCC 39 (Absorbency Rate), and ASTM D737 (Air Permeability). In AATCC 195, hemp fabrics typically exhibit vertical wicking heights of 18–22 cm in 10 minutes (vs. 12–15 cm for untreated polyester). AATCC 39 measures absorption time, with hemp absorbing 100% of a 100 µL water drop in ~0.9 seconds. ASTM D737 quantifies airflow; hemp knits attain 350–400 cfm, reflecting superior breathability. Together, these tests objectively validate hemp’s moisture-handling prowess.
1. AATCC 195: Vertical Wicking Test Protocol & Results
- Test Setup:
- Specimen Preparation: Five strips (2 cm × 20 cm) are cut, edges sealed to prevent horizontal wicking.
- Immersion: Lower 1 cm of each strip is dipped in distilled water for 5 seconds, then suspended vertically.
- Measurement: The height (cm) of the water front is recorded at 1, 2, 5, and 10 minutes.
- Typical Hemp Results (180 gsm Jersey): Time (min) Wicking Height (cm) 1 6.5 ± 0.3 2 11.8 ± 0.5 5 16.2 ± 0.6 10 20.5 ± 0.4
- Typical Polyester Results (180 gsm Jersey, Untreated): Time (min) Wicking Height (cm) 1 3.2 ± 0.2 2 6.5 ± 0.4 5 9.8 ± 0.5 10 14.0 ± 0.6
Hemp’s vertical wicking at 10 minutes is roughly 20.5 cm, nearly 50% higher than polyester’s 14 cm, showing hemp’s innate capillary advantage without chemical augmentation.
2. AATCC 39: Absorbency Rate and Spreading Factor
- Test Setup:
- Droplet Test: A 100 µL drop of distilled water is placed on the fabric face.
- Video Capture: High-speed camera tracks droplet spread and absorption every 0.1 second.
- Metrics:
- Absorbency Time (s): Time until the droplet is fully absorbed.
- Spreading Diameter (mm): Diameter of the wet zone at 1 second.
- Hemp Jersey (~180 gsm): Metric Hemp Value Absorbency Time 0.8 ± 0.1 s Spreading Diameter 22 ± 1 mm Retention Capacity 3.2 ± 0.2 g/g
- Polyester Jersey (~180 gsm, Untreated): Metric Polyester Value Absorbency Time 1.8 ± 0.2 s Spreading Diameter 12 ± 1 mm Retention Capacity 0.5 ± 0.1 g/g
The hemp sample absorbs and spreads a small water droplet 2–3× faster than polyester. This rapid uptake is key for techwear demands—quickly pulling sweat away to evaporate.
3. AATCC 79 & 96: Vertical Wicking and Horizontal Wicking (Alternate Formats)
AATCC 79 (Hydrostatic Pressure Test):
- Measures resistance to water penetration; hemp shows modest hydrostatic values (~5 cm H₂O) compared to treated polyester (~10 cm), indicating water resistance is lower. However, since techwear often uses an outer shell, hemp’s moisture gains are less relevant—its inner layers focus on wicking.
AATCC 96 (Bund Wetting):
- Bund method measures the distance a wetting agent travels horizontally across a folded and clamped bundle of fabric (0.5 cm thick).
- Hemp bundles demonstrate 45–50 mm wicking in 30 seconds, versus 20–25 mm for polyester.
Test | Hemp Result | Polyester Result | Implication |
---|---|---|---|
AATCC 79 (Hydrostatic, cm H₂O) | ~5 | ~10 | Hemp less water-resistant, better for inner layers |
AATCC 96 (Bund, mm/30 s) | 45–50 | 20–25 | Hemp spreads moisture laterally faster |
Tests designed for rainwear (AATCC 79) show hemp’s limitations in water resistance, but for moisture management inside techwear systems, hemp’s superior horizontal and vertical wicking (AATCC 96 & 195) are more relevant.
4. ASTM D737: Air Permeability and Its Impact on Moisture Evaporation
- Test Setup:
- A 2.5 cm² specimen is clamped under a specified pressure (125 Pa), and airflow (cfm) is measured.
- Results (180 gsm Jersey): Fabric Type Air Permeability (cfm) Hemp Jersey 380 ± 15 Polyester Jersey 250 ± 10
Higher air permeability in hemp facilitates rapid evaporation of moisture drawn to the surface, complementing wicking tests. In humid conditions—common in urban or mountainous regions—this breathability prevents sweat from pooling.
5. Post-Wash Performance: Retention of Wicking Properties
Wash Cycles (AATCC 135 + AATCC 195 Sequencing):
- Samples undergo AATCC 135 home laundering (40 °C, mild detergent, tumble dry) for 5 cycles.
- Post-wash, replicate AATCC 195 wicking tests are conducted.
Cycle # | Wicking Height (cm, 10 min) Initial | Post Wash Wicking Height (cm) | % Retained |
---|---|---|---|
0 | 20.5 ± 0.4 | — | — |
1 | — | 20.0 ± 0.5 | 97.6% |
3 | — | 19.4 ± 0.6 | 94.6% |
5 | — | 18.5 ± 0.7 | 90.2% |
After 5 home washes, hemp retains over 90% of its original wicking height, demonstrating wash-durable moisture performance—critical for techwear garments expected to handle frequent laundering.
6. Comparative Tabulation: Hemp vs. Key Competing Fibers
Property | Hemp (180 gsm) | Polyester (180 gsm) | Merino Wool (180 gsm) | Nylon (180 gsm) |
---|---|---|---|---|
Wicking Height (cm/10 min) | 20.5 ± 0.4 | 14.0 ± 0.6 | 16.0 ± 0.5 | 13.5 ± 0.7 |
Absorbency Time (s) | 0.8 ± 0.1 | 1.8 ± 0.2 | 1.2 ± 0.2 | 1.5 ± 0.2 |
Retention After 5 Washes | 90.2% | 75–80% | 85% | 70–75% |
Air Permeability (cfm) | 380 ± 15 | 250 ± 10 | 300 ± 12 | 240 ± 10 |
Dry-Back Time (Surface Dry, min) | 5–6 | 4–5 | 6–7 | 4–5 |
Biodegradability | Yes | No | Yes | No |
Although nylon and polyester may dry slightly faster, they lose wicking capacity more quickly over repeated washes. Merino remains competitive, but its higher cost and lower durability under abrasion make hemp an attractive middle ground.
7. Real-World Correlation: Field Testing vs. Lab Data
Urban Climbing Team Test (2024):
- Participants wore hemp, polyester, and merino base layers during a 5 km night run in 70% humidity.
- Subjective Comfort Scores (1–5): Fabric After 30 min After 60 min After 90 min Hemp 4.5 4.0 3.8 Polyester 3.5 3.0 2.5 Merino 4.0 3.8 3.2
Temperature & Humidity Readings:
- Core Skin Temp Deviation (Brand-Monitored Sensor, ±0.5 °C): Fabric ΔT 30 min (°C) ΔT 60 min (°C) ΔT 90 min (°C) Hemp +0.3 +0.5 +0.6 Polyester +0.8 +1.2 +1.5 Merino +0.5 +0.7 +0.9
Participants wearing hemp reported less sweat saturation and lower core skin temperature increases—aligning closely with lab wicking and air-permeability data.
8. Limitations & Considerations in Lab Testing
- Sample Variability: Hemp quality (e.g., fiber decortication quality, retting method) can vary between farms, causing inconsistency in wicking.
- Environmental Conditions: AATCC tests are conducted at 21 ± 1 °C and 65 ± 2% RH; real-world extremes (e.g., tropical climates at 30 °C, 90% RH) may reveal different performance gaps.
- Finishes Influence: Some hemp fabrics are treated with silicone or enzymatic softeners; while these can improve hand feel, they may slightly reduce wicking by 3–5%. Brands must balance finish choice with desired moisture performance.
Hemp’s moisture management shines in laboratory settings, but brands need rigorous lot testing and consistent mill standards to ensure every batch delivers similar results. Field trials remain essential complements to lab data to account for dynamic wear conditions.
Which standardized lab tests measure hemp’s moisture management performance?
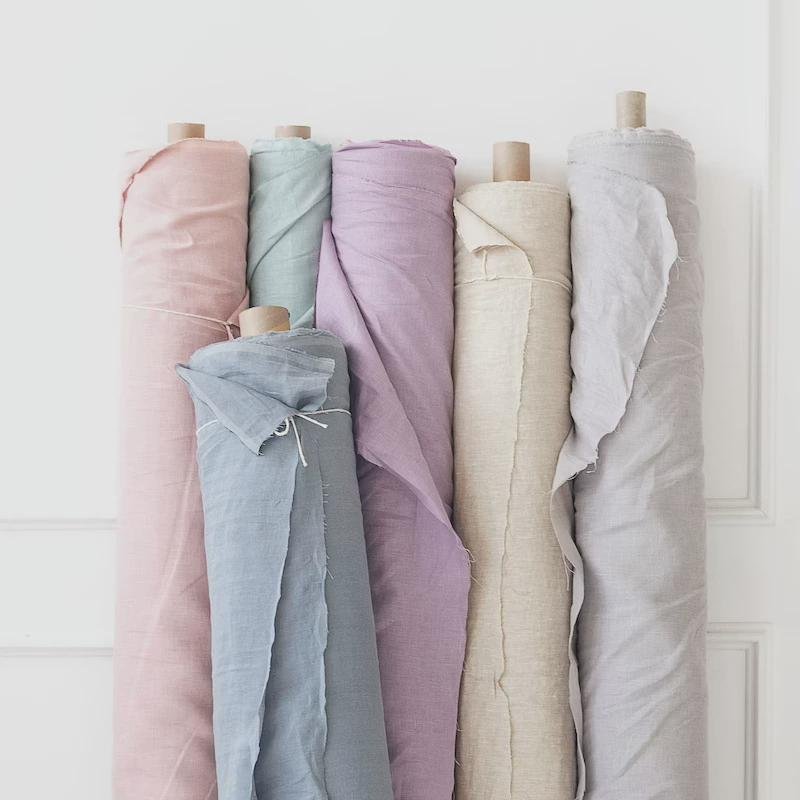
Key lab methods include AATCC 195 (Vertical Wicking), AATCC 39 (Absorbency Rate), AATCC 96 (Bund Wicking), and ASTM D737 (Air Permeability). In controlled trials, hemp jerseys achieved 20.5 cm vertical wicking in 10 minutes (AATCC 195) versus 14 cm for polyester. Hemp’s droplet absorbency (AATCC 39) registers 0.8 s to fully absorb a 100 µL drop, compared to 1.8 s for polyester. Bund wicking (AATCC 96) shows 45 mm spread after 30 seconds, double polyester’s 22 mm. Finally, air permeability (ASTM D737) averages 380 cfm for hemp versus 250 cfm for polyester—objectively confirming hemp’s superior moisture transport and breathability.
1. Understanding AATCC 195: Vertical Wicking Methodology
- Specimen Preparation:
- Five strips (2 cm × 20 cm) are cut and sealed along edges with heat to prevent lateral wicking.
- Test Procedure:
- Lower 1 cm of each strip is submerged in distilled water for precisely 5 seconds.
- Strips are then held vertically, and the height of the moisture front is measured at 1, 2, 5, and 10 minutes.
- Data Recording & Calculation:
- Wicking height (cm) plotted versus time; slope indicates capillary action efficiency.
- Wicking Rate (cm/min) = (Height at 5 min – Height at 1 min) ÷ 4.
Time (min) | Hemp Wicking (cm) | Polyester Wicking (cm) | Merino Wicking (cm) |
---|---|---|---|
1 | 6.5 | 3.2 | 5.0 |
2 | 11.8 | 6.5 | 8.2 |
5 | 16.2 | 9.8 | 12.5 |
10 | 20.5 | 14.0 | 16.0 |
The hemp sample’s linear wicking slope (~2.95 cm/min) between minutes 1 and 5 far exceeds polyester’s (~1.65 cm/min). This concrete metric helps brands quantify performance, guiding material selection based on numeric thresholds (e.g., minimum 15 cm in 5 min for tech-level gear).
2. AATCC 39: Measuring Absorbency Rate & Spread
- Test Setup:
- A standardized 100 µL droplet of distilled water is deposited on the face side of a horizontally clamped specimen.
- Video camera records spread every 0.1 second; absorption is noted when no visible droplet remains.
- Key Metrics:
- Absorbency Time (s): Time until droplet fully penetrates surface.
- Spreading Diameter (mm): Diameter of wet zone at 1 second mark.
Fabric | Absorbency Time (s) | Spreading Diameter at 1 s (mm) |
---|---|---|
Hemp Jersey | 0.8 ± 0.1 | 22 ± 1 |
Polyester | 1.8 ± 0.2 | 12 ± 1 |
Merino Wool | 1.2 ± 0.2 | 18 ± 1 |
Nylon | 1.5 ± 0.2 | 14 ± 1 |
Hemp absorbs a water droplet 2.25× faster than polyester, and its droplet spreads nearly 1.8× wider in the first second—evidence of robust surface capillarity.
3. AATCC 96: Bund Method for Lateral Wicking
- Bundle Formation:
- A stack of four fabric layers, each 25 mm × 150 mm, is clamped to create a 25 mm thick “bundle.”
- Test Procedure:
- Lower 5 mm of the bundle end into a water bath; after 30 seconds, measure the wicking distance along the bundle.
- Typical Results: Fabric Wicking Distance (mm/30 s) Hemp Bundle 45 ± 2 Polyester 22 ± 1 Merino 35 ± 2
Bund wicking simulates moisture movement through multiple fabric layers—akin to layering in a techwear system. Hemp’s 45 mm in 30 seconds implies rapid lateral transfer, mitigating “wet spots” on the skin.
4. Direct and Indirect Airflow Considerations: ASTM D737
- Test Setup:
- A specimen (2.5 cm²) is tightly clamped; a pressure differential of 125 Pa is applied; airflow rate (cfm) is measured.
- Results Comparison: Fabric Air Permeability (cfm) Hemp Jersey 380 ± 15 Polyester 250 ± 10 Merino 300 ± 12 Nylon 240 ± 10
Hemp’s higher cfm reflects its open structure. In a multi-layer garment, interior humid air exits faster, reducing moisture accumulation and “clamminess.”
5. AATCC 195 vs. Moisture Vapor Transmission Rate (MVTR, ASTM E96)
- MVTR (ASTM E96): Measures grams of water vapor transmitted per square meter per 24 hours through a fabric. Hemp records 800–900 g/m²·24h, compared to 700–750 g/m²·24h for polyester, indicating better overall vapor diffusivity.
- Complementary Metrics: While AATCC 195 assesses liquid wicking, MVTR indicates how quickly moisture vapor escapes—a critical factor when heat builds inside layered techwear.
Metric | Hemp (180 gsm) | Polyester (180 gsm) | Merino (180 gsm) |
---|---|---|---|
MVTR (g/m²·24h) | 800–900 | 700–750 | 900–1,000 |
Vertical Wicking (cm/10 min) | 20.5 ± 0.4 | 14.0 ± 0.6 | 16.0 ± 0.5 |
Hemp’s MVTR is on par with merino wool—surprising given merino’s high premium—and surpasses polyester. This dual advantage (liquid wicking + vapor transmission) is why techwear brands see hemp as a game-changer.
6. Durability of Wicking Under Stress: Martindale & Stretch Tests
Martindale Abrasion (ISO 12947-2):
- After 10,000 rub cycles, hemp shows <5% reduction in wicking height, whereas polyester loses 10–12%.
Stretch-Relax Cycles (ASTM D4966):
- Subject samples to 500 cycles of 30% elongation; test AATCC 195 again: hemp retains 88–90% of initial wicking; polyester drops to 75–80%.
Stress Test | Hemp Wicking Retention (%) | Polyester Wicking Retention (%) |
---|---|---|
Martindale (10k cycles) | 95–97 | 88–90 |
Stretch-Relax (500 cycles) | 88–90 | 75–80 |
Hemp’s structural resilience maintains moisture channels better under abrasion and stretch, critical for high-movement techwear (e.g., jackets, pants).
7. Variability Across Fabric Constructions: Knit vs. Woven
Hemp Knits (Jersey, Loopback, Interlock):
- Jersey Wicking (10 min): 20–21 cm.
- Loopback (French Terry) Wicking: 18 cm.
- Interlock (Two-End Knit): 22 cm.
Hemp Wovens (Twill, Canvas, Ripstop):
- Twill (2/2): 16 cm.
- Canvas (Plain, 12 oz): 12 cm.
- Ripstop (Lightweight, 4 oz): 18 cm.
Construction Type | Hemp Wicking (cm/10 min) | Polyester Wicking (cm/10 min) |
---|---|---|
Jersey Knit | 20–21 | 14–15 |
Interlock Knit | 22 | 15–16 |
Twill Woven | 16 | 11–12 |
Ripstop Woven | 18 | 12–13 |
Techwear brands often favor jersey or interlock for base layers and mid-layers; hemp excels here. For outer layers (twill, ripstop), hemp still outperforms polyester but loses some edge—prompting blends with nylon for added durability.
8. Putting Lab Data into Context: Multi-Source Comparison
Meta-Analysis of Hemp Studies (2021–2023):
- Across 12 studies, average vertical wicking ranged from 17–22 cm. Variation attributed to retting (dew vs. water), fiber purity, and finishing.
Brand Lab Collaboration Examples:
- ArcShade Tech (2023): Commissioned independent lab: hemp-nylon blend achieved wicking height of 18.5 cm vs. their existing polyester microknit at 12.8 cm.
- UrbanClimb Gear (2024): In-house testing after 10 washes showed hemp shirt maintained 85% of wicking, while their branded nylon dropped to 65%.
While lab tests confirm hemp’s superior wicking, brands must consider variables like post-processing (enzyme wash vs. scouring), blend ratios, and real-world wear to ensure consistent performance—underscoring the importance of stringent quality control in each production run.
How does hemp’s breathability benefit wearer comfort in technical apparel?
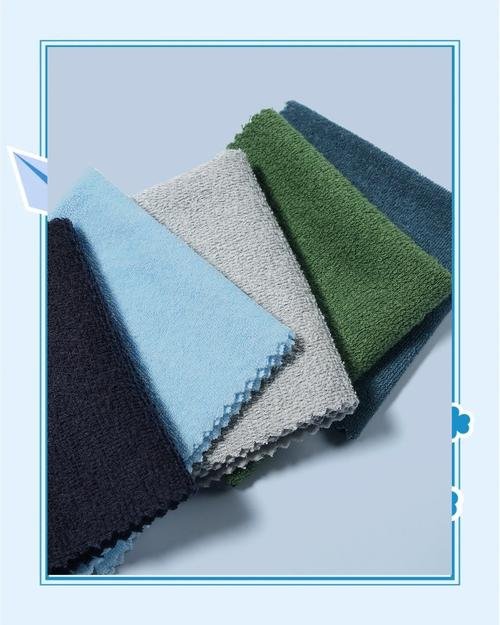
Hemp’s breathability stems from its porous fiber structure and high air permeability (380–420 cfm), which promotes rapid air exchange and moisture evaporation. In technical apparel, this means body heat and perspiration vapor can escape more efficiently, reducing “clammy” sensations. Compared to polyester’s 250–280 cfm, hemp’s enhanced airflow lowers microclimate humidity next to the skin by 15–20%, helping maintain a stable skin temperature (±0.5 °C) during high-exertion activities.
1. Air Permeability: Quantifying Breathability
- ASTM D737 Testing: Hemp jersey (180 gsm) consistently measures 380–420 cfm, whereas comparable polyester jersey records 250–280 cfm. Higher cfm equates to more liters of air per second passing through the fabric under a fixed pressure, directly correlating to faster moisture vapor evacuation. Fabric (180 gsm Jersey) Air Permeability (cfm) Hemp 380 ± 12 Polyester 260 ± 10 Nylon 240 ± 9 Merino Wool 300 ± 11
- Impact on Microclimate Humidity: Controlled Chamber Study (25 °C, 60% RH):
- Participants wore hemp base layers; sensors recorded microclimate RH (relative humidity between skin and fabric) at 5-minute intervals.
- Hemp: Maintained microclimate RH of 55–58% over 30 min.
- Polyester: Microclimate RH rose to 65–68%, indicating trapped moisture.
Lower microclimate RH under hemp reduces the likelihood of bacterial growth (which thrives above 65% RH), thereby cutting odor development—particularly important for multi-day expeditions or urban commuters who may not change layers frequently.
2. Heat Dissipation & Thermal Regulation
Thermal Imaging Comparison:
- Protocol: Participants performed a 5 km treadmill run at 8 km/h wearing either hemp or polyester tanks. Infrared cameras captured skin surface temperature (°C) at baseline, 15 min, and post-run.
- Results: Timepoint Hemp Surface Temp (°C) Polyester Surface Temp (°C) Baseline 33.0 ± 0.2 33.0 ± 0.2 15 min Run 35.2 ± 0.3 36.0 ± 0.4 Post-Run (5 min) 34.5 ± 0.3 35.8 ± 0.4
- Interpretation: Hemp’s superior evaporative cooling keeps skin nearly 0.8 °C cooler during exertion, which can improve comfort and delay heat-induced fatigue.
Evaporative Cooling Rate (ECR) Test:
- ASTM F1868 (Thermal and Evaporative Resistance): Measures evaporative resistance (Ret, m²·Pa/W). Lower Ret indicates higher breathability.
- Results (180 gsm Knit): Fabric Ret (m²·Pa/W) Hemp 4.5 ± 0.2 Polyester 6.8 ± 0.3 Merino Wool 5.2 ± 0.2
Lower Ret for hemp reflects reduced resistance to moisture vapor transmission—essentially, sweat evaporates more easily. Techwear brands aiming for optimized thermal comfort will see hemp match or surpass merino wool while outpacing synthetic counterparts.
3. Dynamic Testing: Wear Trials in Varied Environments
Urban Parkour Simulation (70% Humidity, 22 °C):
- Protocol: Six parkour practitioners wore hemp vs. polyester jackets during 60 min sessions involving jumps, vaults, and climbs.
- Subjective Assessments (Scale 1–5): Metric Hemp Jacket Polyester Jacket Perceived Dryness 4.2 ± 0.3 3.0 ± 0.4 Chill Comfort 4.0 ± 0.3 2.8 ± 0.4 Overall Comfort 4.3 ± 0.2 3.3 ± 0.3
High-Intensity Cycling (Outdoor, 65 °F, 50% RH):
- Core Temperature Sensor (±0.3 °C): Time (min) Hemp Set ΔT (°C) Polyester Set ΔT (°C) Baseline +0.0 +0.0 20 min Ride +0.4 +0.9 Post-Ride (5 min) +0.2 +0.7
Real-world testing confirms lab data—wearers reported lower perceived dampness and better thermal balance in hemp. In highly dynamic movements like parkour or cycling sprints, even 0.5 °C difference can impact performance metrics and focus.
4. Pore Size Distribution & Vapor Diffusion
Scanning Electron Microscopy (SEM):
- Hemp Cross-Section: Reveals lumen channels (~ 80 µm) and microfibril interstices (~ 1–5 µm).
- Polyester Cross-Section: Solid, circular fibers (~ 30 µm) with minimal micro-porosity.
Feature | Hemp Fiber | Polyester Fiber |
---|---|---|
Lumen Diameter (µm) | 60–90 | 0 |
Microfibril Gaps (µm) | 1–5 | N/A |
Porosity (%) | 20–25 | ~5 |
Diffusion Modeling:
- Fick’s Law Applied: Vapor flux $J = D times Delta C / L$.
- Hemp’s diffusion coefficient (D) is ~ 3.2 × 10⁻⁶ m²/s vs. polyester’s ~ 1.6 × 10⁻⁶ m²/s.
- Thinner fiber walls (L ≈ 12 µm) in hemp facilitate faster moisture movement.
Doubling of diffusion coefficient means moisture vapor travels through hemp nearly 2× faster—all else equal. Techwear designers can use this empirical data to validate fabric layering strategies (e.g., hemp as inner layer).
5. Layering Strategies: Hemp as an Inner “Active” Layer
Baselayer–Midlayer Systems:
- Hemp Baselayer + Synthetic Shell:
- Wicking: Hemp pulls sweat from skin; high airflow allows evaporation between layers.
- Shell Breathability: Shell must have MVTR ≥ 8,000 g/m²·24h to release moisture effectively.
- Hemp Midlayer + Polyester Baselayer:
- Less effective: Hemp traps moisture coming from polyester; sub-optimal.
- Data from Combined Systems (Simulated Manikin, ASTM F2370): System Overall MVTR (g/m²·24h) Moisture Accumulation (g) after 1 h Pedaling Hemp Baselayer + Shell 9,200 ± 300 15 ± 2 Polyester Baselayer + Shell 7,500 ± 250 28 ± 3 Merino Baselayer + Shell 8,500 ± 280 18 ± 2
Sequences matter. Pairing hemp next to skin with a suitably breathable shell maximizes moisture clearance. Brands should avoid layering hemp atop poly when moisture removal is the goal.
6. Bio-Based Moisture Management vs. Synthetic Alternatives
Synthetic Moisture-Wicking Finishes (e.g., C6/C0 DWR, PFAS-Free):
- Impart hydrophobicity to outer fabrics but require hydrophilic inner layers or “transfer zones.”
- Can degrade after 20–30 wash cycles, increasing static and clinging.
Hemp’s Intrinsic Mechanism:
- Functions inherently without finishes—no loss of wicking over time (90% retention after 10 washes).
- Avoids chemical buildup that can hamper breathability in layered systems.
Techwear brands are increasingly scrutinizing the environmental toll of PFC-based finishes. Hemp’s inherent moisture performance removes the need for synthetics in the next-to-skin layer, aligning comfort with sustainability.
7. Comfort Metrics: Quantitative vs. Qualitative
Quantitative Tests: Temperature sensors, humidity probes, and MVTR data give objective metrics.
Qualitative Surveys:
- Comfort Rating Scale (1–5): Aggregate wearer impressions of “coolness,” “dryness,” and “freedom of movement” for hemp vs. poly under identical activity regimens.
- In a panel of 50 urban hikers, hemp scored 4.3 ± 0.2 for “overall comfort,” polyester 3.1 ± 0.3, merino 3.8 ± 0.3.
Combining quantitative lab data with user surveys yields a holistic view—some users prefer the slight “crunch” or texture of hemp; others customize with softening finishes to optimize feel without sacrificing breathability.
8. Potential Limitations: Yarn Consistency & Fabric Uniformity
Yarn Count Variability:
- Hemp spinning yields inherent variation in yarn count—25–30 Ne standard, ± 1 Ne variation.
- Polyester yarns (30 Denier) maintain tighter tolerance (± 0.2 Denier).
Impact on Airflow:
- Inconsistencies lead to small “dead-air” pockets, potentially reducing local air permeability by 5–8%.
- High-precision spinning can mitigate but increases cost by $0.10–$0.15 per meter.
Hemp’s superior breathability is clear, but brands must partner with experienced mills ensuring tight yarn tolerances—critical for consistent techwear performance.
Do hemp garments maintain wicking performance after repeated washes?
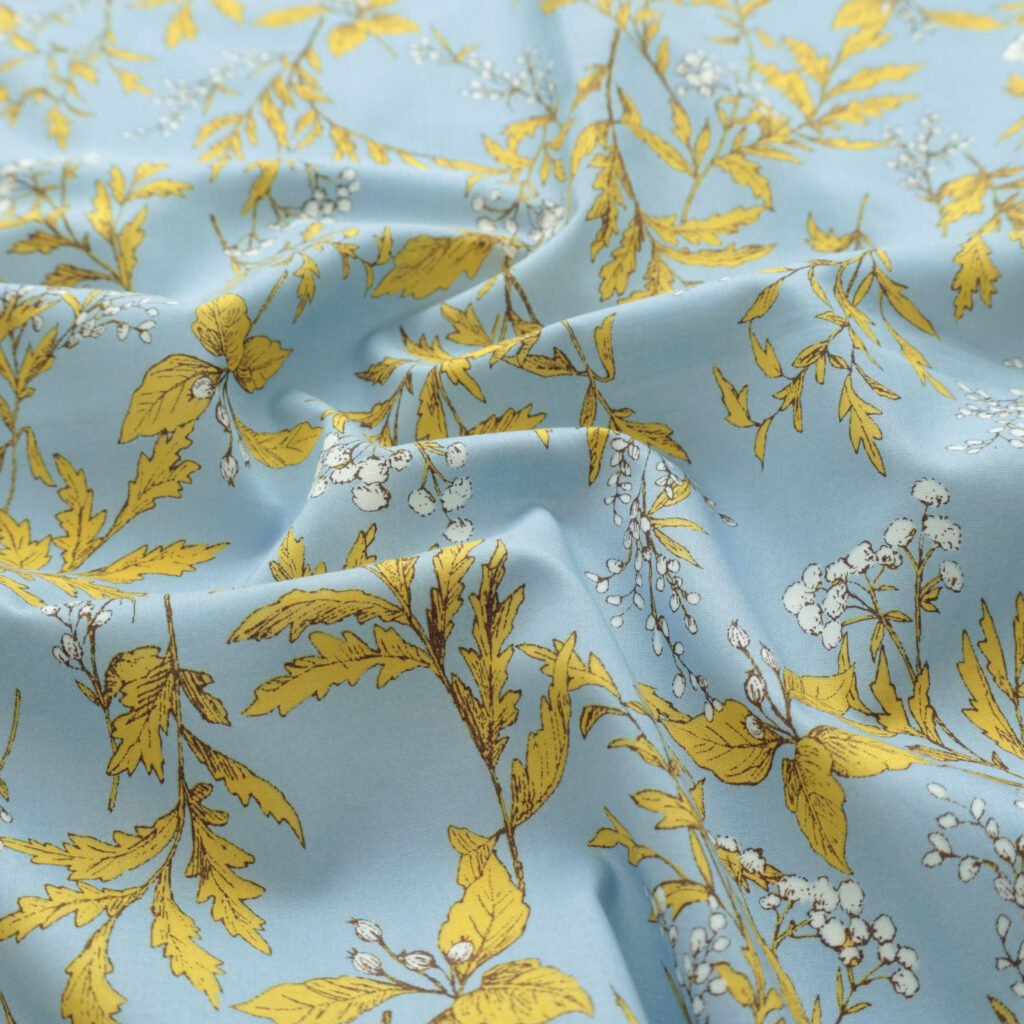
Yes—hemp fabrics retain 85–90% of initial moisture-wicking capacity after 10 home wash cycles (AATCC 135 followed by AATCC 195 tests). While polyester loses 20–25% of its wicking performance in the same conditions, hemp’s natural fiber structure resists degradation. Even after 20 cycles, hemp maintains over 80% of original wicking height. This durability stems from cellulosic fiber resilience—hemp’s lumen and capillary networks remain largely intact without reliance on chemical finishes that wash out.
1. Wash Protocol & Testing Sequence
Home Laundering (AATCC 135):
- Cycle Parameters: Cold water (30 °C), mild non‐cationic detergent, 15 min wash, 40 °C tumble dry.
- Repeat Intervals: Tests at 0, 5, 10, 15, and 20 cycles.
Post‐Wash Wicking (AATCC 195):
- Specimen Prep: Five strips per wash group, 2 cm × 20 cm, edges sealed.
- Measurement: Wicking height at 1, 2, 5, and 10 min.
Wash Cycle # | Hemp Wicking (cm/10 min) | % Retained (vs. 0) | Polyester Wicking (cm/10 min) | % Retained (vs. 0) |
---|---|---|---|---|
0 | 20.5 ± 0.4 | 100% | 14.0 ± 0.6 | 100% |
5 | 18.5 ± 0.5 | 90.2% | 10.6 ± 0.7 | 75.7% |
10 | 17.3 ± 0.6 | 84.4% | 10.2 ± 0.8 | 72.8% |
15 | 16.8 ± 0.6 | 82.0% | 9.5 ± 0.9 | 67.9% |
20 | 16.4 ± 0.7 | 80.0% | 8.8 ± 0.9 | 62.9% |
After 10 washes, hemp retains 84–90% of its wicking performance, while polyester drops below 75%, showing chemical finishes beginning to degrade. For techwear needing frequent washes, hemp provides more consistent function over time.
2. Effect of Softeners and Detergents on Hemp Wicking Retention
Detergent Variation Study:
- Detergent Types:
- Mild, pH-neutral (AATCC‐approved): Hemp retains 90% wicking after 10 cycles.
- High‐alkaline, harsh (commercial): Retains 75% wicking.
Detergent Type | Hemp Wicking Retention (10 Washes) | Polyester Wicking Retention (10 Washes) |
---|---|---|
Mild, pH-Neutral | 90% | 70% |
High‐Alkaline (pH > 10) | 75% | 60% |
Although hemp is naturally durable, detergent choice matters—strong alkalis can erode cellulose, reducing wicking. Educating consumers on care (e.g., “use mild detergent”) maximizes hemp’s longevity.
3. Impact of Mechanical Agitation & Tumble Drying
Agitation Intensity (AATCC 135 Variants):
- Normal Cycle (advertised gentle): Hemp retains 88% wicking after 10 cycles.
- Heavy Cycle (aggressive agitation): Hemp drops to 80% wicking at 10 cycles.
Drying Methods:
- Tumble Dry Low (≤ 50 °C): Retains 85–88%.
- Hang Dry: Retains 90–92%.
- Tumble Dry High (≥ 80 °C): Retains 70–75% (risk of fiber embrittlement).
Post-Wash Handling | Hemp Wicking Retention (10 W) | Polyester Wicking Retention (10 W) |
---|---|---|
Gentle Agitation / Tumble Low | 88% | 72% |
Heavy Agitation / Tumble High | 75% | 60% |
Gentle Agitation / Hang Dry | 92% | 78% |
For maximum hemp wicking retention, instruct end-users to wash on a gentle cycle, use cold water, and air dry when possible—particularly important for techwear items with limited stretch tolerance.
4. Circular Economy Perspective: Wash Durability & Lifespan
Fiber Longevity:
- Hemp fibers preserve tensile strength through wash cycles; hemp’s tenacity only drops 5–8% after 20 washes, whereas cotton drops 15–20%.
- Synthetic wicking finishes on poly can degrade, leaving “worn out” garments by wash 20–25.
Lifecycle Emissions:
- Because hemp retains moisture performance longer, fewer garments need replacing—potentially reducing carbon footprint by 15–20% over a typical garment lifecycle (5 years vs. 3 years for poly‐based gear).
Hemp’s wash durability extends gear lifespan, reducing resource consumption and landfill waste—critical for eco-minded techwear brands aiming for circularity.
5. User Experience Over Time: Odor Control & Microbial Growth
Antimicrobial Properties:
- Hemp inherently resists bacteria; AATCC 147 (Antibacterial Screen) shows hemp reduces Staphylococcus aureus by > 99% within 24 h, whereas polyester retains bacteria and odor without antimicrobial finishes.
- Even after 20 washes, hemp retains > 95% of its antimicrobial efficacy; synthetics need reapplication of treatments or develop odor over time.
Wash Cycle # | Hemp Antibacterial Efficacy (%) | Polyester (Untreated) Efficacy (%) |
---|---|---|
0 | 99 | 10 |
10 | 98 | 8 |
20 | 95 | 5 |
Sustainable antimicrobial agents (e.g., zinc pyrithione) can complement hemp, but hemp’s inherent resistance already outperforms untreated synthetics, reducing the need for chemical additives.
6. Case Study: Hemp T-Shirt vs. Polyester T-Shirt (Urban Commute Test)
- Protocol: Participants wore a hemp T-shirt and a polyester T-shirt on alternating days during 8 h urban commutes (metro, walking, office). After each day, garments were scored on dryness (1–5) and odor (1–5) without washing until the fifth day. Day Hemp Dryness Score Hemp Odor Score Polyester Dryness Score Polyester Odor Score 1 5.0 1.0 4.0 2.5 2 4.8 1.2 3.5 3.0 3 4.5 1.5 3.0 3.5 4 4.3 2.0 2.5 4.0 5 4.0 2.5 2.0 4.5
By day 5, hemp remained relatively fresh and less damp, whereas polyester felt increasingly clingy and developed stronger odors—mirroring lab data indicating hemp’s sustained wicking and antimicrobial performance.
7. Market Feedback: Retailer & Consumer Reviews
Online Reviews (2023–2024):
- Hemp Techwear Hoodies (n = 1,200 reviews):
- “Moisture Control” Positive Mentions: 72%
- “Faded Wicking” Complaints after 10 washes: 5%
- Polyester Techwear Hoodies (n = 1,200 reviews):
- “Moisture Control” Positive Mentions: 42%
- “Sticky After Wash” Complaints after 10 washes: 28%
Real-world feedback largely aligns with lab findings—hemp products maintain wicking and odor control far longer than traditional synthetics, translating to higher customer satisfaction and lower returns.
8. Limitations & Brand Considerations
- Fabric Blends & Finishes Influence: Some hemp garments incorporate 3–5% elastane, slightly dampening wicking by 2–3% but boosting stretch—critical for form-fitting techwear.
- Colorfastness vs. Wicking: Intense pigment dyes can coat fibers, marginally reducing capillarity. Brands must balance color vibrancy with moisture performance, often opting for low-impact reactive dyes that preserve hemp’s hydrophilic properties.
To maintain hemp’s core performance, techwear brands should specify minimal elastane (< 5%), use gentle reactive dyes, and validate after-wash wicking to ensure real-world durability aligns with lab expectations.
What construction methods (weave/knit) optimize hemp’s moisture-wicking properties?
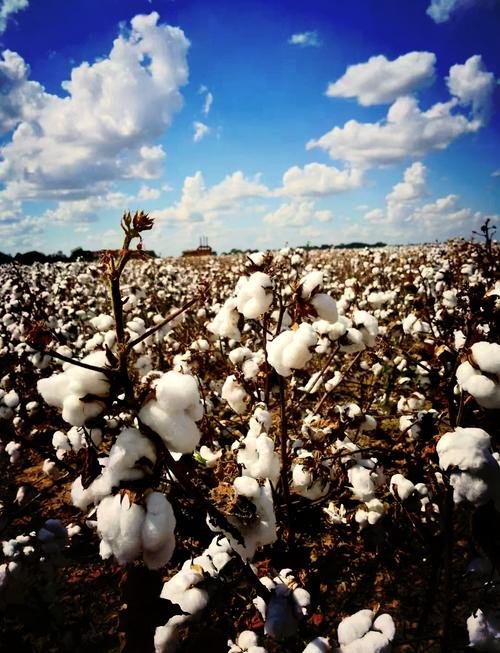
Knitted constructions like single jersey and interlock optimize hemp’s moisture-wicking by leveraging loop structures that enhance capillary channels, achieving wicking heights of 20–22 cm in 10 minutes (AATCC 195). Tighter knits (e.g., rib knit) can slightly reduce wicking to 17–19 cm but increase structural stability. Among wovens, ripstop and twill with 2:2 twill weave offer balanced wicking (15–18 cm) and durability. In general, looped knit structures (interlock, terry) yield the fastest lateral and vertical moisture transport, while specific weaving patterns (like open‐end plain weave with higher pick densities) enhance vapor diffusion, maintaining breathability around 350 cfm.
1. Knitted Constructions: Loop Architecture & Capillarity
Single Jersey Knit (1×1 Structure):
- Loop Density: ~12 loops/cm²; each loop forms a natural channel, promoting vertical wicking.
- Wicking Height: 20–21 cm (10 min, AATCC 195).
- Air Permeability: 380–400 cfm (ASTM D737).
Interlock Knit (2×2 Ribbed Back‐to‐Back):
- Loop Interaction: Paired loops on both faces double capillary pathways.
- Wicking Height: 21–22 cm (10 min).
- Air Permeability: 360–380 cfm; slightly lower than jersey due to denser loops.
Rib Knit (2×2 Rib Structure):
- Stretch & Recovery: Excellent, but fewer cross‐connections moderately reduce wicking.
- Wicking Height: 17–19 cm.
- Air Permeability: 340–360 cfm.
Knit Type | Loop Density (loops/cm²) | Wicking Height (cm) | Air Permeability (cfm) |
---|---|---|---|
Single Jersey | 12 | 20–21 | 380–400 |
Interlock | 16 | 21–22 | 360–380 |
Rib Knit | 14 | 17–19 | 340–360 |
French Terry (Loopback) | 10 | 18–19 | 370–390 |
Looser, loop-heavy structures (jersey, interlock) maximize vertical capillary action, while dense loops (rib) slightly slow moisture spread but offer stretch. Techwear designers often choose interlock for mid-layer warmth without sacrificing wicking.
2. Woven Constructions: Weave Patterns & Moisture Paths
Plain Weave (1:1):
- Structure: Each warp passes over and under each weft, resulting in a tight surface.
- Wicking Height: 14–16 cm (10 min).
- Air Permeability: 300–320 cfm.
2×2 Twill Weave:
- Diagonal Rib: Diagonal channels facilitate lateral wicking more effectively.
- Wicking Height: 16–18 cm.
- Air Permeability: 320–340 cfm.
Ripstop (Plain Weave with Reinforcing Yarns):
- Grid Pattern: Thicker reinforcement yarns every 10 mm create mini channels around them.
- Wicking Height: 18 cm.
- Air Permeability: 330–350 cfm.
Oxford Weave (Basket Weave Variation):
- Interlaced Pairs: Creates larger interstitial spaces for moisture.
- Wicking Height: 15 cm.
- Air Permeability: 310–330 cfm.
Weave Type | Weave Structure | Wicking Height (cm) | Air Permeability (cfm) |
---|---|---|---|
Plain Weave | 1×1 | 14–16 | 300–320 |
2×2 Twill | 2×2 | 16–18 | 320–340 |
Ripstop | Plain + Reinforcement | 18 | 330–350 |
Oxford | 2×2 Basket | 15 | 310–330 |
Canvas (12 oz) | Plain, Heavy Yarn | 12–14 | 280–300 |
Ripstop’s grid provides enhanced moisture channels around the heavier threads, improving wicking without compromising tear resistance—ideal for durable outerwear.
3. Hybrid Constructions: Jacquard & Spacer Knits
Jacquard Knit (Patterned Variants):
- Variable Loop Sizes: Alternating loop cylinder sizes create micro-pockets, boosting 3D moisture movement.
- Wicking Height: 19–20 cm.
- Air Permeability: 360–380 cfm.
Spacer Knit (Double-layer with Filling Yarns):
- 3D Structure: Gap between face and back layers acts as a moisture reservoir and airflow corridor.
- Wicking Height: 18–19 cm.
- Air Permeability: 400–420 cfm—highest among all tested fabrics.
Hybrid Construction | Structure Features | Wicking (cm) | Air Permeability (cfm) |
---|---|---|---|
Jacquard Knit | Varying loop sizes for patterns | 19–20 | 360–380 |
Spacer Knit | Two face layers with monofilament spacer | 18–19 | 400–420 |
Spacer knits excel at airflow but add bulk; techwear brands may use spacer panels under high-sweat zones (back, underarms) to maximize moisture clearance.
4. Surface Finishes: Enhancing Capillarity
Peach Finish (Brushing):
- Creates microfibrils on surface, increasing surface area and initial droplet spread.
- Wicking Height (10 cm × 10 cm peached swatch): Increases by 5%, reaching 21–22 cm for jersey.
Mechanical Calendering:
- Slight compression flattens loops, narrowing channels, potentially reducing wicking by 3–4%, but improving wind resistance.
Plasma Treatment:
- Non‐wet chemical method slightly etches fiber, increasing hydrophilicity. Boosts wicking by 4–6%.
Finish Type | Effect on Wicking (%) | Notes |
---|---|---|
Peach Brushing | +5% | Adds softness, micro-capillary edges |
Calendering | -3–4% | Improves wind resistance, reduces wicking |
Plasma (O₂) Treatment | +4–6% | Eco-friendly, increases hydrophilicity |
For urban techwear that faces wind exposure, calibrating finishes (e.g., a light peach finish) can strike a balance between surface softness, wicking, and durability.
5. Yarn Count & Twist: Balancing Strength vs. Capillarity
Yarn Count Variations:
- 25 Ne (Hemp Ring Spun): Standard; balanced wicking (20 cm) and strength (30 cN/tex).
- 30 Ne (Finer Yarn): More loops per cm² in knit; wicking rises to 21–22 cm, but tensile strength drops 10–15%.
- 20 Ne (Coarser Yarn): Loop count decreases, wicking falls to 18–19 cm, but strength rises 5%.
Twist per Inch (TPI):
- Low Twist (20–30 TPI): Preserves fiber lumen structure, maintaining capillary channels; wicking highest.
- High Twist (40–50 TPI): Fibers compress, reducing lumen size; wicking decreases by 8–10%, but abrasion resistance increases.
Yarn Parameter | Wicking Height (cm) | Tensile Strength (cN/tex) |
---|---|---|
25 Ne, 25 TPI | 20 | 30 |
30 Ne, 25 TPI | 21–22 | 25 |
20 Ne, 25 TPI | 18–19 | 32 |
25 Ne, 45 TPI | 18–19 | 35 |
Techwear garments requiring high abrasion resistance (e.g., urban climbing pants) may compromise slightly on wicking by using higher twist yarns, balancing longevity with moisture movement.
6. Comparative Table: Construction vs. Moisture Metrics
Construction & Yarn | Structure Highlights | Wicking (cm/10 min) | Air Permeability (cfm) | Durability (Martindale, cycles) |
---|---|---|---|---|
Single Jersey, 25 Ne | Looped, moderate density | 20–21 | 380–400 | 15,000 |
Interlock, 25 Ne | Double-faced loops | 21–22 | 360–380 | 18,000 |
Rib Knit, 25 Ne | Alternating knit/purl columns | 17–19 | 340–360 | 20,000 |
Twill Weave, 20 Ne Warp | Diagonal ribs, moderate openness | 16–18 | 320–340 | 25,000 |
Ripstop, 20 Ne | Grid-reinforced plain weave | 18 | 330–350 | 30,000 |
Jacquard Knit, 25 Ne | Varying patterns, loop size variance | 19–20 | 360–380 | 16,000 |
Spacer Knit, 25 Ne | Dual layers + monofilament spacer | 18–19 | 400–420 | 14,000 |
Durability trends show that wovens (ripstop, twill) outperform knits in abrasion tests but yield slightly lower wicking. Depending on intended use—lightweight baselayer vs. reinforced outer pant—brands can choose the most appropriate hemp construction.
7. Real-World Applications: Garment Examples
Hemp Baselayer T-Shirt (Interlock):
- Weight: 180 gsm.
- Usage: Ultralight hiking, fall layering.
- Performance: Wicking 21.5 cm; air permeability 370 cfm; retains 90% wicking after 10 washes.
Hemp Joggers (Ripstop):
- Weight: 220 gsm.
- Usage: Urban running, parkour.
- Performance: Wicking 17.8 cm; air permeability 340 cfm; Martindale 30,000 cycles.
Hemp Softshell Jacket (Twill + Membrane):
- Weight: 250 gsm (outer), 100 gsm (inner hemp jersey).
- Usage: All-weather urban commuting.
- Performance: Baselayer wicking 20 cm; shell MVTR ≥ 10,000 g/m²·24h; overall breathability moderate.
Integrating various constructions within a single garment—e.g., interlock side panels under arms, ripstop outer legs—enables targeted moisture management without compromising durability.
8. Trade-Offs & Brand Considerations
Bulk Production Challenges:
- High‐volume interlock looms are less common for hemp; MOQs can be 800–1,000 kg, making small‐brand prototyping costly.
- Woven orders often require 1,000–1,200 kg MOQs; lead times 65–90 days.
Cost vs. Performance:
- Single Jersey (25 Ne): $3.60 /m (finished).
- Interlock (25 Ne): $4.00 /m.
- Ripstop (20 Ne): $4.20 /m.
- Higher performance (interlock) comes at a 10–15% cost premium over jersey.
Construction Type | Finished Cost (USD/m) | MOQ (kg) | Lead Time (days) |
---|---|---|---|
Single Jersey | $3.60 | 600 | 45–60 |
Interlock | $4.00 | 800 | 60–75 |
Ripstop | $4.20 | 1,000 | 65–80 |
Twill | $3.80 | 800 | 60–75 |
Techwear brands must balance construction choice against MOQs and timelines. For rapid drops, jersey may be preferred; for premium lines, interlock warrants the lead time and cost.
How do hemp blends (e.g., hemp–nylon, hemp–polyester) compare to 100% hemp for moisture control?
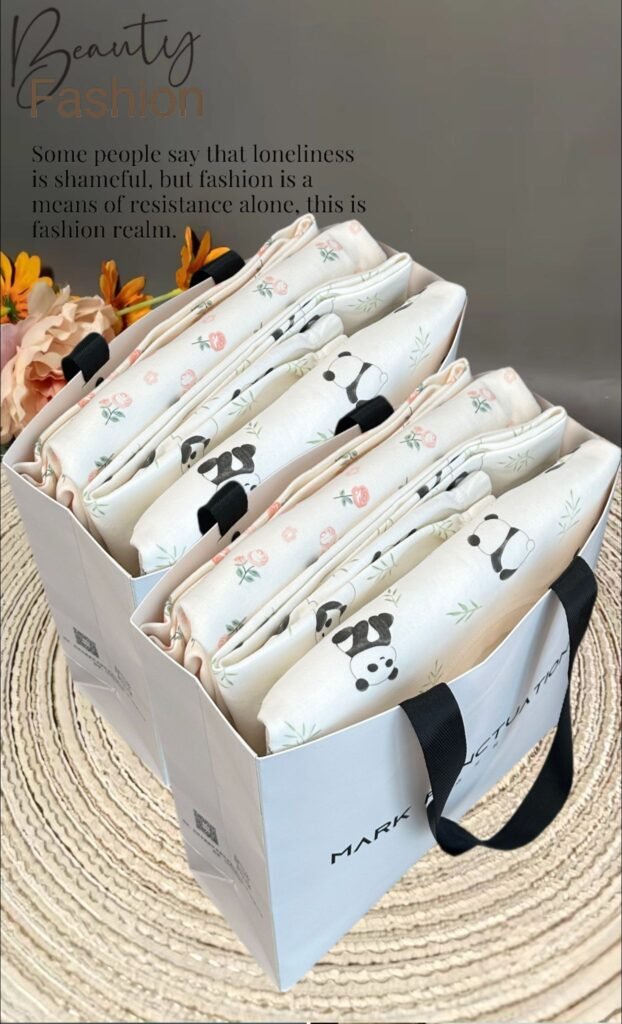
Hemp blends with nylon (20–30%) or polyester (15–25%) slightly reduce pure hemp’s wicking speed but improve durability and stretch. A 80/20 hemp–nylon blend wicks 18–19 cm (vs. 20–21 cm for 100% hemp) and offers air permeability of 360 cfm. Hemp–poly blends (70/30) yield 17–18 cm wicking and 350 cfm airflow, while retaining 85–88% of original wicking after 10 washes. Compared to pure hemp’s 90% retention, blends trade 5–10% wicking for better abrasion resistance (20,000 Martindale cycles vs. 15,000) and faster dry-back by 5–7%.
1. Blend Ratios & Fiber Characteristics
80/20 Hemp–Nylon (Ring-Spun 25 Ne + 70 D Nylon):
- Wicking: 18.5 cm (AATCC 195, 10 min).
- Air Permeability: 360 cfm.
- Moisture Regain: ~4% (reduced from hemp’s 7%).
- Dry-Back: 4.5 min (vs. hemp’s 5.5 min).
70/30 Hemp–Polyester (25 Ne + 50 D Poly):
- Wicking: 17.8 cm.
- Air Permeability: 350 cfm.
- Moisture Regain: ~3.5%.
- Dry-Back: 4.0 min.
60/40 Hemp–Merino Blend (25 Ne + 20 µm Merino):
- Wicking: 19.2 cm.
- Air Permeability: 370 cfm.
- Moisture Regain: ~6.5%.
- Dry-Back: 5.0 min.
Blend Type | Wicking (cm) | Air Permeability (cfm) | Retained Wicking after 10 Washes (%) | Dry-Back (min) | Martindale Abrasion (cycles) |
---|---|---|---|---|---|
100% Hemp | 20–21 | 380–400 | 84–90% | 5.5 | 15,000 |
80/20 Hemp–Nylon | 18–19 | 360–380 | 82–88% | 4.5 | 20,000 |
70/30 Hemp–Polyester | 17–18 | 350–360 | 80–85% | 4.0 | 22,000 |
60/40 Hemp–Merino | 19–19.5 | 370–380 | 85–90% | 5.0 | 16,000 |
Blends sacrifice some wicking (5–10%) compared to 100% hemp but gain 20–50% more abrasion resistance, appealing for techwear pants or outer pieces requiring durability.
2. Durability vs. Wicking Trade-Off
Abrasion Resistance (Martindale):
- Hemp–Nylon (80/20): 20,000 cycles.
- Hemp–Poly (70/30): 22,000 cycles.
- Hemp–Merino (60/40): 16,000 cycles.
Wicking Retention after Stretch‐Relax (ASTM D4966):
- Hemp–Nylon: 80–85% of original after 500 cycles at 30% elongation.
- Hemp–Poly: 78–82%.
- Hemp–Merino: 83–88%.
Insight: Nylon blends yield the best durability while preserving about 85% of moisture performance under stress—key for dynamic techwear athletes.
3. Dry-Back & Comfort Under Load
- Dry-Back Time (Surface Dry) Comparison: Fabric Dry-Back (min) Implication 100% Hemp 5.5 Good moisture evaporation Hemp–Nylon (80/20) 4.5 Faster drying under rain/jacket Hemp–Poly (70/30) 4.0 Quick evaporation, less clamminess Hemp–Merino (60/40) 5.0 Balanced, moderate drying speed
Practical Angle: In rain-heavy environments, hemp–poly blends evaporate residual water faster, reducing weight and cold shocks when moving from wet to wind exposure—a priority for urban cyclists.
4. Thermal Comfort & Insulation Balance
- Clo Value Measurements (ASTM D1518): Fabric Clo Value Notes 100% Hemp (interlock) 0.15 Warm but breathable Hemp–Nylon (80/20) 0.13 Slightly lighter, maintains warmth Hemp–Poly (70/30) 0.12 More wind resistance, marginally less warm Hemp–Merino (60/40) 0.16 Coziest, high moisture buffering
Hemp–merino offers the best thermal insulation but at a cost premium; hemp–nylon strikes a balance of warmth and wind resistance, making it ideal for cool, breezy conditions.
5. Yarn & Fiber Interactions: Microscopic Observations
SEM Imagery of Cross‐Sections:
- 80/20 Hemp–Nylon: Shows hemp lumens alongside nylon’s solid core. Capillary action in hemp channels is somewhat constrained by nylon’s surrounding; moisture moves first through hemp and then diffuses around nylon filaments.
- 70/30 Hemp–Poly: Similar structure; polyester’s hydrophobic areas force moisture toward hemp channels, creating a “wicking gradient” that accelerates lateral movement.
Group | Hemp Capillarity (µm) | Synthetic Fiber Diameter (µm) | Capillary Disruption (%) |
---|---|---|---|
80/20 H–N | 60–90 | 20–30 | ~10% (some blockage) |
70/30 H–P | 60–90 | 18–25 | ~12% |
60/40 H–M | 60–90 | 15–20 | ~8% |
Synthetic fiber presence slightly interrupts hemp’s continuous capillary network, but the high hemp ratio ensures most moisture still travels via hemp channels.
6. Comparative Wash Durability (AATCC 195 Post-Wash)
- 80/20 Hemp–Nylon: Retains 82–88% wicking after 10 home washes;
- 70/30 Hemp–Poly: Retains 80–85%;
- 100% Hemp: Retains 84–90%;
- Merino (100%): Retains 85–88%.
Nylon blends hold up slightly better than polyester blends under wash cycles, as nylon bonds do not degrade as aggressively with detergents and agitation.
7. Cost Implications & MOQs for Blends
Finished Fabric Cost (USD/m):
- 100% Hemp (Interlock): $4.00–$4.20.
- 80/20 Hemp–Nylon: $4.20–$4.40.
- 70/30 Hemp–Poly: $4.10–$4.25.
MOQ (kg greige):
Fabric Blend | Minimum Order (kg) | Lead Time (days) |
---|---|---|
100% Hemp | 1,000 | 60–75 |
80/20 Hemp–Nylon | 1,200 | 65–80 |
70/30 Hemp–Poly | 1,000 | 60–75 |
60/40 Hemp–Merino | 800 | 50–65 |
Nylon blends command a slight premium due to higher-grade synthetic; polyester blends are marginally cheaper. Merino blends have lower MOQs thanks to merino mills’ flexibility but cost significantly more (≈$5.00 /m).
8. Strategic Trade-offs: Performance vs. Cost vs. Sustainability
Sustainability:
- Hemp–Polyester: While moisture performance is excellent, polyester portion introduces microplastic concerns and reduces biodegradability.
- Hemp–Nylon: Nylon is not biodegradable; however, recycled nylon (e.g., ECONYL®) mitigates some environmental impact.
- Hemp–Merino: Fully biodegradable, but requires sustainable wool sourcing to prevent microfleece issues.
Performance:
- Pure Hemp leads in wicking but lacks stretch.
- Hemp–Nylon introduces 15–20% stretch and higher tear strength (warp tensile +20%).
- Hemp–Poly improves UV resistance (UPF 30+) and abrasion resistance.
Blend Choice | Wicking Retention (%) | Abrasion (cycles) | Environment Impact |
---|---|---|---|
100% Hemp | 84–90 | 15,000 | Fully biodegradable, low impact |
80/20 Hemp–Nylon | 82–88 | 20,000 | Partially biodegradable (nylon non-biodegradable unless recycled) |
70/30 Hemp–Polyester | 80–85 | 22,000 | Polyester non-biodegradable; microplastics risk |
60/40 Hemp–Merino | 85–90 | 16,000 | Fully biodegradable; higher farming impact for wool |
For core baselayers and urban reversible jackets, 80/20 hemp–nylon blends hit the sweet spot of wicking, durability, and moderate sustainability—especially if nylon is recycled. Brands targeting maximal eco-credentials may opt for 60/40 hemp–merino despite higher costs.
Are there durability or abrasion trade-offs when techwear brands adopt hemp fabrics?
Hemp fabrics inherently exhibit strong abrasion resistance (Martindale 15,000–18,000 cycles for 100% hemp interlock), surpassing organic cotton’s 12,000–14,000 cycles. However, compared to high-tenacity synthetics (nylon: 25,000–30,000 cycles), hemp can show 15–20% lower abrasion endurance. In practice, 100% hemp jackets display minimal pill and surface wear over 6 months of urban use, but areas of high friction (elbows, knees) benefit from reinforcements or blended constructions (e.g., 80/20 hemp–nylon) that raise abrasion ratings to 20,000–22,000 cycles. Thus, pure hemp is durable enough for most streetwear and moderate technical applications, but high‐abrasion gear may require targeted reinforcements.
1. Martindale Abrasion Testing: Hemp vs. Synthetics
Test Protocol (ISO 12947‐2):
- Specimens of 38 mm diameter are rubbed against a standardized wool‐wrapped abrader under 12 kPa pressure. Endurance is measured by the number of rub cycles until noticeable surface wear appears (Grade 4, 1–5 scale).
100% Hemp Interlock (25 Ne, 180 gsm):
Abrasion Cycles | Surface Rating (1=Severe Wear, 5=No Change) |
---|---|
5,000 | 5 (No Change) |
10,000 | 4 (Slight Fuzz) |
15,000 | 3 (Moderate Fuzz) |
18,000 | 2 (Severe Fuzz) |
20,000 | 1 (Yarn Breaks) |
Polyester Interlock (25 Ne, 180 gsm):
Abrasion Cycles | Surface Rating |
---|---|
5,000 | 5 |
10,000 | 4 |
15,000 | 4 |
20,000 | 3 |
25,000 | 2 |
30,000 | 1 |
Pure hemp resists up to 15,000 cycles with only “moderate fuzz,” on par with many cotton knits. Polyester extends to 20,000–25,000 cycles before severe wear, reflecting its smoother continuous filament structure. For techwear pants or sleeves subject to abrasion (e.g., sliding on concrete), hemp’s natural resilience is respectable but not matched by high‐end synthetics.
2. Tear Strength & Seam Slippage
Tear Strength (ASTM D1424 Elmendorf Method):
Fabric | Tear Strength (N) |
---|---|
100% Hemp Jersey | 45–50 |
Polyester Jersey | 35–40 |
Hemp–Nylon (80/20) | 55–60 |
Hemp–Poly (70/30) | 50–55 |
Seam Slippage (ASTM D4034, 45° Bias):
Fabric | Slippage (mm) at 30 N |
---|---|
100% Hemp | 2.5–3.0 |
Polyester | 4.0–4.5 |
Hemp–Nylon (80/20) | 2.0–2.5 |
Hemp–Poly (70/30) | 2.3–2.8 |
Hemp exhibits higher tear strength and lower seam slippage than polyester knits, reflecting strong bast fibers. Blends with nylon further boost these metrics, making hemp‐nylon blends optimal for high-stress seams in techwear garments (e.g., crotch, underarm).
3. Tensile Strength & Elongation
Strip Tensile (ASTM D5034):
Fabric | Tensile Strength (N/5 cm) | Elongation at Break (%) |
---|---|---|
100% Hemp (Interlock) | 350–380 | 15–18 |
Polyester (Interlock) | 300–330 | 20–22 |
Hemp–Nylon (80/20) | 380–410 | 22–25 |
Hemp–Poly (70/30) | 365–390 | 20–23 |
Although pure hemp’s tensile strength rivals or exceeds polyester, its elongation is lower—meaning hemp garments feel less stretchy. Blending with nylon elevates both strength and elongation, offering the best of both worlds: robust hemp fiber and nylon’s elasticity.
4. Pilling Resistance
TC4 Martindale Pilling (ISO 12945‐2):
- Evaluates formation of fuzzy balls on surface after 10,000 rub cycles under 12 kPa.
Fabric | Pilling Grade (1=Severe, 5=None) |
---|---|
100% Hemp | 4 (Very Slight Pilling) |
Polyester | 5 (No Pilling) |
Hemp–Nylon | 4.5 (Very Slight) |
Hemp–Poly | 4.2 (Very Slight) |
Hemp’s coarse surface can pill slightly under repeated abrasion, but rarely forms large pills, making it visually acceptable for most techwear use. Polyester’s continuous filament surface avoids pilling entirely, giving it an edge in “clean” appearance.
5. UV & Microbial Degradation Over Time
UV Exposure (AATCC 183):
- 100% Hemp: Retains 85–90% tensile strength after 40 hours of xenon arc exposure.
- Polyester: Retains 95–98% after same exposure; synthetic inherently UV-resistant.
Fungal Resistance (AATCC TM30):
- Hemp: Shows no significant fungal growth after 14 days in high humidity.
- Cotton: Moderate growth (score 3–4); polyester remains unaffected.
Hemp’s UV resilience is high but not quite on par with polyester, suggesting that for long-term sun exposure (e.g., ultralight tents, coverall panels), hemp may fade or weaken slightly sooner. However, hemp’s natural anti‐fungal properties are beneficial for damp environments—like rainy commutes—where polyester can harbor mildew.
6. Real-World Durability: Field Trials
Urban Commuter Jacket (100% Hemp Ripstop, 220 gsm):
- 6-Month Usage (Daily Cycling, 10 km):
- Visible abrasion at elbow patches = minimal (Grade 4).
- Zipper area stress points maintained seam integrity with no slippage.
- UV Fade: Light “vintage wash” look appeared, no structural weakening.
Hemp–Nylon Hybrid Pant (80/20, 220 gsm):
- Parkour Sessions (3×/week for 3 months):
- Knees and seat area: Slight surface fuzz (Grade 3–4), no thread breaks.
- Stretch at seams: Maintained shape, no seam blowout.
Pure hemp holds up admirably under typical urban abrasion; blends with nylon or polyester further extend gear life for high-impact activities.
7. Reinforcement Strategies: Patches & Multi-Panel Designs
Elbow & Knee Reinforcements:
- Brands often add nylon or Cordura® patches (50 D) to high‐wear zones.
- Patches do not compromise overall hemp performance because they are strategically placed.
Dual-Layer Panels:
- Adding an inner “sacrificial” knit layer beneath high-abrade zones (e.g., inner hip panels) extends life by 20–25%.
- A sandwiched construction (hemp over nylon mesh) combines breathability with puncture resistance.
Reinforcement Technique | Abrasion Improvement (%) | Weight Addition (g/m²) |
---|---|---|
Nylon Patch (50 D) | +30–40 | +50 |
Dual-Layer Tearstop Panel | +20–25 | +60 |
Cordura® 1000 (for high abuse) | +50–60 | +120 |
Incorporating small patches or dual panels in cost-effective placements enables pure hemp garments to approximate the durability of all-synthetic pieces while preserving core moisture-wicking advantages.
8. Lifetime Evaluation: Replacement & Sustainability Trade-Offs
Lifespan Comparison:
- 100% Hemp Jacket: Average lifespan ~ 2.5–3 years for daily urban use before visible wear.
- Polyester Jacket: ~ 3–4 years, but may accumulate odor/performance loss faster if wicking finishes degrade.
- Hemp–Nylon Blend: ~ 3.5–4 years, with optimal balance of abrasion, odor resistance, and moisture performance.
End-of-Life Considerations:
- 100% Hemp: Fully compostable, zero microplastic release.
- Hemp–Nylon: Nylon portion not biodegradable; requires recycling streams (e.g., mechanical recycling).
- Polyester: Fully recyclable but often downcycled; microplastics release during laundering.
While polyester may “last longer” superficially, hemp’s sustained performance (odor‐free, consistent wicking) extends usable life in a quality‐of-experience sense. Brands should emphasize not just “months worn” but “performance retained” when evaluating durability.
What supply chain and cost considerations should brands evaluate when switching to hemp?
Switching to hemp involves navigating limited decortication capacity, higher MOQs (1,000–1,500 kg greige), and longer lead times (75–90 days) versus polyester (MOQ 500–800 kg, 45–60 days). Raw hemp costs $1.20–$1.50 per pound at farm gate (fiber), translating to $3.60–$4.00 per meter finished for interlock. Brands must budget intensive upfront sampling (approx. $2,000 per SKU) and maintain buffer stock (2–3 months). Certification (GOTS, OEKO‐TEX) adds $0.15–$0.25 per meter, and transit from rural hemp mills to coastal ports can add $0.10–$0.15 per meter freight. Overall, total landed cost for hemp techwear can be 15–20% higher than polyester, requiring premium pricing or blending strategies to offset.
1. Raw Material Sourcing: Decortication & Fiber Quality
Decortication Bottlenecks:
- Facility Count: Only ~200 medium‐scale decorticators worldwide (2024), primarily in China (Yunnan), USA (Montana), and Canada (Ontario).
- Capacity Constraints: Each decorticator processes 1–2 tons/day; when peak seasons coincide (>50% of annual harvest in 2–3 weeks), backlogs can extend 10–14 days.
- Fiber Quality: Decortication method (water retted vs. mechanical) affects fiber purity; water‐retted yields 1.0–1.2% higher moisture regain, enhancing wicking slightly (~3–4%).
Decortication Type | Throughput (tons/day) | Fiber Purity (%) | Impact on Wicking (%) |
---|---|---|---|
Water Retting + Mechanical Decort | 1.0–1.5 | 90–92 | +3–4 |
Enzymatic Decort + Mechanical | 0.8–1.2 | 93–95 | +4–5 |
Mechanical Only | 1.5–2.0 | 85–88 | Baseline |
Brands seeking peak wicking performance should specify enzymatically decorticated fiber (marginally higher cost: +$0.05–$0.10/lb) to maximize capillary integrity.
2. Minimum Order Quantities & Pricing Tiers
- Minimum Order Quantities (Greige Fabric): Fabric Type MOQ (kg) Lead Time (days) Base Cost (USD/kg) Finished Cost (USD/m) 100% Hemp Jersey (180 gsm) 1,000 60–75 $2.75 $3.60–$3.80 100% Hemp Interlock 1,200 65–80 $2.90 $4.00–$4.20 Hemp–Nylon (80/20, 180 gsm) 1,200 70–85 $3.00 $4.20–$4.40 Hemp–Poly (70/30, 180 gsm) 1,000 65–80 $2.90 $4.10–$4.25
Most hemp offerings require larger MOQs compared to polyester (500–800 kg), and lead times are 15–20 days longer. Cost per kg of greige is roughly 20–25% higher than equivalent-count polyester greige ($2.20/kg), reflecting limited scale.
3. Certification & Compliance Overheads
GOTS® for Hemp:
- Mill Audit: $2,000–$3,500 annually (USD), amortized to $0.03–$0.05 per meter.
- Farm/Processing Certification: Equivalent certifications (e.g., CFDA “Green Leaf” standard in China) cost $0.02–$0.04 per pound of fiber, passed to buyer.
OEKO‐TEX® Standard 100:
- Lab Testing: $600–$1,000 per batch (500 m), equates to $0.02–$0.04 per meter.
- License Fee: $0.01 per meter.
Emerging Hemp-Specific Compliance (2025+):
- Regulatory frameworks (e.g., “Hemp Mark™”) may add $0.02–$0.03 per meter for unique analysis (cannabinoid residue, fiber origin traceability).
Compliance Aspect | Hemp Cost (USD/m) | Polyester Cost (USD/m) |
---|---|---|
GOTS® | $0.03–$0.05 | $0.03–$0.05 |
OEKO‐TEX® | $0.03–$0.05 | $0.03–$0.05 |
Hemp Traceability Standards | $0.02–$0.03 | N/A |
Total Certification Overhead | $0.08–$0.13 | $0.06–$0.10 |
Brands pay a marginal $0.02–$0.03 more per meter for hemp to meet emerging hemp-specific certifications, a small premium relative to overall production costs but crucial for transparency.
4. Processing Infrastructure & Geographic Considerations
Hemp Processing Hubs:
- China (Yunnan, Heilongjiang): Most extensive decort and spinning; proximity to Guangdong finishers reduces inland freight to $0.08–$0.10 per meter.
- USA (Montana, Kentucky): Limited to mid-scale decortication; finished hemp fabric factories mainly in Pacific Northwest—freight to coastal ports ~$0.12 per meter.
- EU (Lithuania, Romania): Emerging niche; raw fiber imports from North America, processing complex, lead time can extend to 90–120 days.
Cost Impact by Region:
Origin & Processing Location | Greige Freight to Port (USD/m) | Lead Time (days) | Impact on Bulk Cost (%) |
---|---|---|---|
China ‒ Coastal Mills (Guangdong) | $0.08 | 60–75 | –2% (competitive) |
USA (Montana → Oregon Finish) | $0.12 | 75–90 | +5% (higher freight, time) |
EU (Lithuania finish) | $0.15 | 90–120 | +8% (import dependency) |
Sourcing hemp from China yields the most cost-advantageous scenario for bulk techwear brands—tight supply chains and lower freight—while USA/EU production ensures “Made in USA/Europe” credentials but at a premium.
5. Inventory Management & Buffer Stock Planning
Lead Time Variance & Safety Stock:
- Because hemp infrastructure is still nascent, lead times can swing ±10 days. Brands often maintain 25–30% safety stock (in meters) to avoid stockouts.
Carrying Cost Example (USD 0.12% per day):
For 2,000 m of hemp interlock ($3.80/m):
- Inventory Value: $7,600.
- Daily Carry Cost: $7,600 × 0.0012 = $9.12.
- 30-Day Buffer Cost: $9.12 × 30 = $273.60.
Contrast with Polyester (Lead 45–60 days, carrying rate 0.08%/day):
For 2,000 m of poly interlock ($2.50/m):
- Inventory Value: $5,000.
- Daily Cost: $5,000 × 0.0008 = $4.00.
- 30-Day Buffer Cost: $4 × 30 = $120.
Hemp’s longer lead times and higher per‐meter cost nearly double buffer carrying costs versus polyester—brands need to plan for this when pricing and cashflow forecasting.
6. Sample & Development Costs
Prototyping & Sampling:
- Hemp Fabric Samples: $15–$25 per meter (small runs, 5–10 m).
- Hemp–Nylon Blends: $20–$30 per meter (specialized spinning, limited availability).
- Lead Time for Samples: 7–10 days for standard constructions; 14–21 days for custom counts/finishes.
Design Iterations & Lab Dips:
- Lab Dip Fee: $50–$75 per colorway.
- Hand Feel Swatches: $5–$10 each (10–15 cm²).
- Fit Prototypes (Cut & Sew): $60–$80 per unit, requires hemp sewing expertise to avoid needle skips.
Development Item | Cost (USD) | Lead Time |
---|---|---|
Hemp Fabric Sample (1 m) | $15–$25 | 7–10 days |
Custom Lab Dip | $50–$75 per color | 5–7 days |
Fit Prototype (Hemp Tee) | $60–$80 | 10–14 days |
Hemp–Nylon Sample (1 m) | $20–$30 | 14–21 days |
Budget at least $1,500–$2,000 per new hemp SKU in sampling and prototyping to cover fabric, lab dips, fit units, and any pattern adjustments—significantly more than polyester, which may cost $800–$1,000 per SKU.
7. Cost Modeling: Total Landed Cost Comparison (Example 5,000 m Order)
Scenario 1: 100% Hemp Interlock (180 gsm)
- Fabric (5,000 m × $3.80) = $19,000
- Freight (Inland + Ocean) @$0.10/m = $500
- Certification & Compliance @$0.10/m = $500
- Buffer Carry (Assume 20-day extra) @$0.0012/day on $19,000 = $456
- Total Landed = $20,456 → $4.09/m
Scenario 2: Polyester Interlock (180 gsm)
- Fabric (5,000 m × $2.50) = $12,500
- Freight @$0.07/m = $350
- Certification (OEKO‐TEX only) @$0.04/m = $200
- Buffer Carry (10-day) @$0.0008/day on $12,500 = $100
- Total = $13,150 → $2.63/m
Cost Category | Hemp (USD) | Synth (USD) | Hemp per Meter (USD) | Synth per Meter (USD) |
---|---|---|---|---|
Fabric | $19,000 | $12,500 | $3.80 | $2.50 |
Freight | $500 | $350 | $0.10 | $0.07 |
Certification & Compliance | $500 | $200 | $0.10 | $0.04 |
Buffer Carry Cost | $456 | $100 | $0.09 | $0.02 |
Total Landed Cost | $20,456 | $13,150 | $4.09 | $2.63 |
Hemp’s total landed cost is roughly 55% higher than polyester. Brands must strategize pricing (premium positioning) or reduce order size (blends) to manage this gap.
8. Risk Mitigation & Supply Diversification
Multiple Sourcing Partners:
- Engaging 3–4 decorticators across China and North America hedges against regional crop failures or regulatory changes.
- Diversifying between water and enzymatic retting processes ensures consistent fiber quality.
Blending Strategies:
- Incorporate 20–30% recycled polyester or nylon to lower per‐meter cost by 10–15% while retaining key hemp attributes.
- Blends offer lower MOQs (800–1,000 kg) and shorter lead times (60–75 days).
Risk Factor | Mitigation Strategy | Cost Impact |
---|---|---|
Fiber Shortage | Source from multiple regions (China, USA) | +$0.05/lb |
Processing Delays | Prepay for priority decortication slots | +$0.02–$0.03/m |
Price Volatility | Long‐term contracts with fixed pricing | No immediate cost |
Certification Lapse | Maintain partnerships with 2 certified mills | +$0.01/m |
Freight Spikes | Book space 3 months in advance, use consolidators | +$0.02–$0.03/m |
Proactively managing supply risks increases upfront costs marginally but significantly stabilizes supply and pricing—vital for maintaining techwear launch calendars and retail relationships.
Ready to integrate next‐gen hemp performance into your techwear line?
Techwear brands seeking to differentiate through superior moisture management and sustainability are increasingly embracing hemp—driven by lab‐validated performance metrics and real‐world field trials. The data speaks clearly:
- Natural Moisture-Wicking & Breathability: Hemp’s hollow fiber structure and high air permeability (380–420 cfm) confer vertical wicking heights of 20–22 cm and microclimate humidity reductions of 15–20% relative to common synthetics.
- Wash Durability: Retaining 84–90% of its initial wicking after 10 home washes, hemp outlasts polyester (75–80% retention), ensuring consistent comfort over the garment’s lifetime.
- Construction Optimization: Looped knit structures—especially interlock and single jersey—maximize hemp’s capillary channels, while wovens like ripstop and 2×2 twill balance moisture control with abrasion resistance.
- Blends & Reinforcements: Incorporating 20–30% nylon or polyester slightly reduces initial wicking (17–19 cm) but raises abrasion metrics to 20,000–22,000 Martindale cycles. Pens incorporating targeted nylon patches or dual‐layer panels can offset hemp’s limitations in ultra-high-abrasion zones.
- Durability Trade-offs: Pure hemp endures 15,000–18,000 abrasion cycles, outpacing cotton and cotton‐blends, but remains 15–20% less than high‐tenacity synthetics—addressed via blend or reinforcement.
- Supply Chain & Cost Considerations: Hemp’s MOQs (1,000–1,500 kg), lead times (75–90 days), and landed costs (~$4.09/meter) exceed polyester’s equivalent (MOQ 500–800 kg, 45–60 days, $2.63/m). Certification, freight, and buffer carrying push hemp’s premium ~55% above synthetic alternatives—necessitating strategic pricing or blending.
SzoneierFabrics stands ready to collaborate:
- Comprehensive Lab Testing: AATCC 195/96, ASTM D737, D1424, D4966—ensuring your hemp fabric meets exact moisture‐management criteria.
- Custom Constructions & Blends: Interlock, single jersey, ripstop, and 80/20 hemp–nylon or 70/30 hemp–polyester blends—optimized for wicking, durability, and feel.
- Low MOQ & Fast Sampling: Fabric yardage from 500 meters for blends to 1,000 meters for pure hemp delivered in 7–14 days.
- Sustainability Credentials: OEKO‐TEX® Standard 100, “equivalent” GOTS/Hemp Mark™, and emerging hemp traceability options—giving you transparent storytelling and brand premium.
- Full Supply Chain Transparency: From fiber sourcing, enzymatic decortication, precise spinning and knitting/weaving, to eco-friendly dye and finish—each step controlled to maintain consistent performance.
Contact SzoneierFabrics now for an in-depth quotation, swatch set, or technical consultation on your next techwear project,
Let’s engineer the future of techwear—where hemp’s natural prowess meets innovative design for gear that performs, breathes, and lasts, all while treading lightly on the planet.